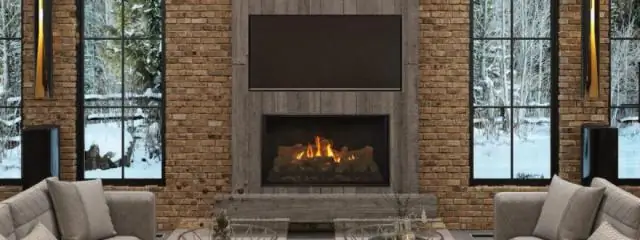
Table of contents:
- Making a furnace out of metal with your own hands
- Pros and cons of metal ovens
- Types, principle of operation and choice of design for self-production
- Possible designs and their features
- Calculation of basic parameters
- Required materials and tools
- Preparatory work: selection of the installation site and laying of the foundation
- DIY step-by-step instructions for making a metal furnace
- Chimney device, its manufacture and installation
- Decor
- Features of operation: cleaning and repairing the stove
2025 Author: Bailey Albertson | [email protected]. Last modified: 2025-06-01 07:32
Making a furnace out of metal with your own hands
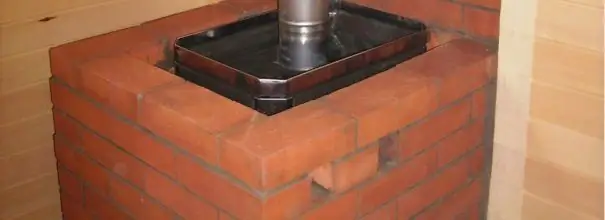
To create a heating unit in your home, it is not at all necessary to build bulky brick structures or buy expensive appliances. For this, you can use the materials and containers at hand. When building a metal furnace with your own hands, skills in working with a welding machine and an angle grinder will come in handy.
Content
-
1 Pros and cons of metal ovens
1.1 Table: advantages and disadvantages of metal furnaces
-
2 Types, principle of operation and choice of design for self-production
- 2.1 From aluminum
- 2.2 Steel
- 2.3 From cast iron
-
3 Possible designs and their features
- 3.1 Closed design
- 3.2 Open type design
- 3.3 Combined oven type
- 4 Calculation of basic parameters
- 5 Required materials and tools
- 6 Preparatory work: selection of the installation site and laying of the foundation
- 7 Step-by-step instructions for making a metal furnace with your own hands
- 8 Chimney device, its manufacture and installation
- 9 Decor
- 10 Features of operation: cleaning and repairing the stove
Pros and cons of metal ovens
The metal stove is a compact, one-piece heating unit. Such a stove can be easily moved, unlike brick options. Its shape can be different. Typically, these structures are made in the form of a cube, parallelepiped or cylinder.
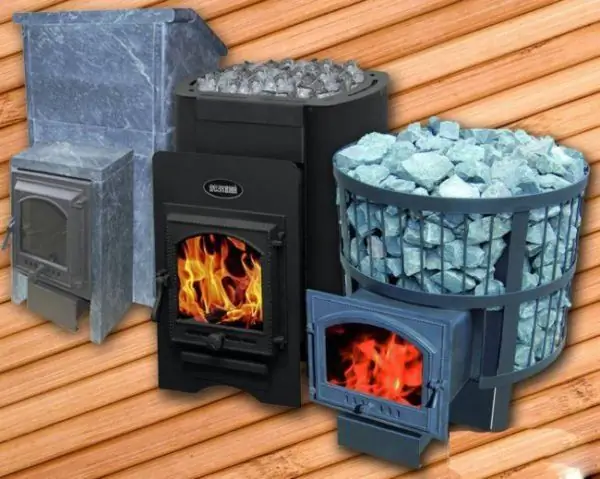
Can be used at home and for economic purposes
The efficiency of a metal stove is low - it is only capable of effectively heating small rooms with an area of 10 to 30 m². In this regard, such heat sources have become popular among summer residents and pet owners. Such ovens are used to heat country houses, utility rooms, workshops, sheds, garages, chicken coops and other rooms with a small area.
Despite the fact that metal stoves are a convenient option and an alternative to capital heating structures, they also have positive and negative qualities.
Table: advantages and disadvantages of metal furnaces
Advantages | disadvantages |
|
|
Types, principle of operation and choice of design for self-production
It should be noted that homemade metal ovens are most often designed with hob surfaces. Therefore, when listing the types of metal furnaces, it is necessary to take into account such designs. There are the following types:
- Heating. The design of these units is intended only for space heating. Such ovens do not perform any other functions.
- Heating stoves with a hob. These designs have a cooking surface. Some structures of this type are equipped with a stove and oven.
- Household and household. Structures used not only in dwellings, but also in outbuildings, utility rooms, garages. Such ovens are often installed to heat rooms in which pets and birds are kept.
By their design, metal furnaces are classified into chamber, channel and bell-type:
- Chamber constructions. In such units, flue gases enter a special compartment, in which they completely burn out under the influence of the natural circulation of gas flows. In household structures, the combustion area is connected to the afterburner, forming a common module called the crucible. For this process to be effective, a vaulted furnace is required. A striking example of this is the classic construction of the Russian stove.
- Channel constructions. In this furnace, the flue gases burn almost completely, after which they move between the partitions through special channels, in which they gradually cool down. During movement, hot streams give off heat to the walls of the structure. The afterburning of gases in a furnace of this type does not occur until the temperature in the furnace channel rises to 400 ° C. The efficiency of this type of oven does not exceed 60%.
- Bell structures. The frame of this unit resembles a hood. Hot streams are directed under the upper part of the furnace (bell) and are retained there, completely burning out and heating the entire body. Then the gases are lowered. To warm up this oven, it is enough to increase the temperature in a small area of the bell. This feature increases the efficiency of the furnace up to 75%.
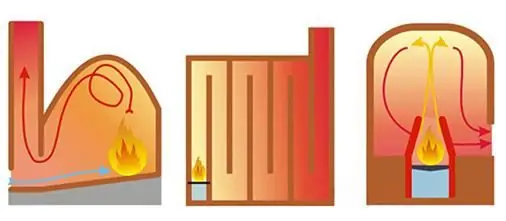
Arrows indicate hot streams
For the manufacture of furnaces, steel, cast iron and aluminum are most often used.
From aluminum
This option is often used due to the availability of material, namely aluminum cans. By its design, this container is suitable for creating a heating unit. It is only necessary to make a hole at its base to install the chimney. However, the melting point of aluminum is 660 ° C.
This parameter makes the material unstable to strong heat. This is due to the fact that high efficiency is achieved as a result of the afterburning of exhaust flue gases. During this process, the temperature is around 400 ° C.
Given these temperature ranges, aluminum is not the best material for making a furnace. The walls of the unit will quickly burn out, and the structure of the can will soon be deformed.
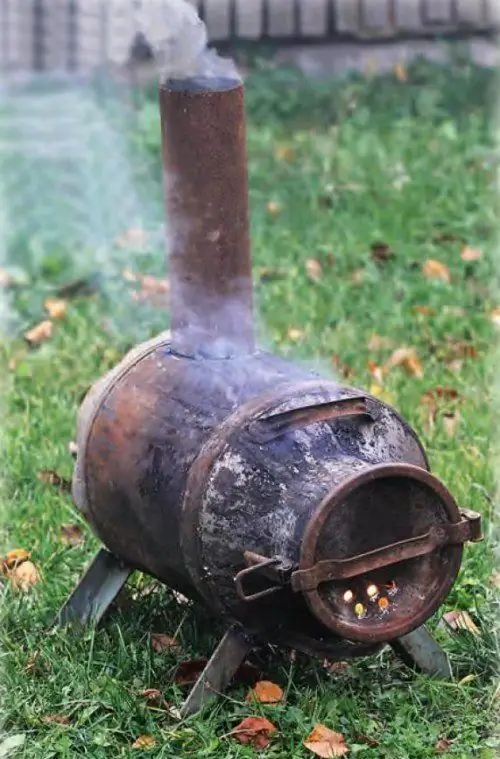
Material burns out quickly
Of steel
The melting temperature of steel is in the range from 1450 to 1520 ° C, therefore, this material, in comparison with the previous one, is more suitable for the manufacture of such structures.
This is due to the fact that each metal, regardless of its type, burns out under the influence of high temperatures. Therefore, the use of a material of lesser thickness is impractical. The thin walls of the oven, subject to constant use, will burn out in 3-4 months.
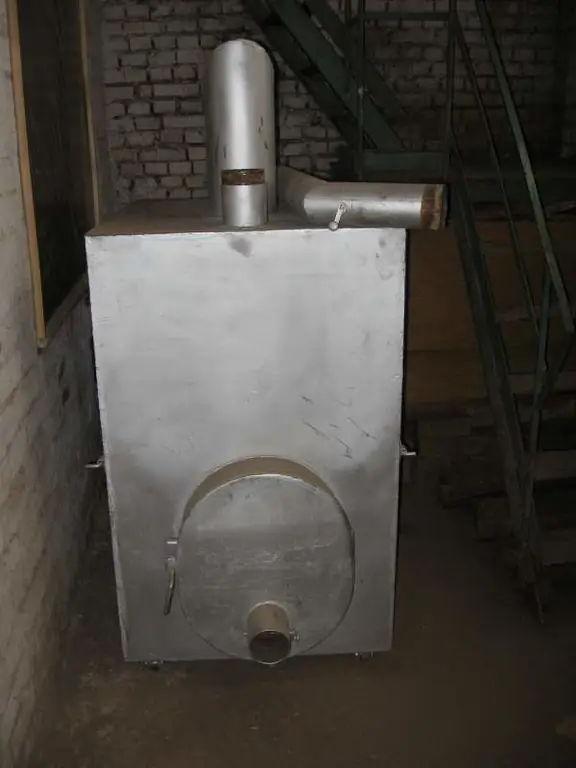
Reliable material
To increase the resistance of the material to high temperatures and extend the life of the heating structure, it can be hardened. For this, the steel sheets are red-hot.
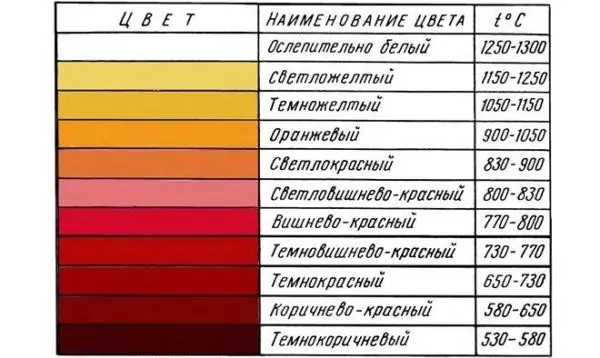
Effective method
It is necessary to ensure that black or blue spots do not appear on the metal. This will indicate that the hardening is not correct. You should also take into account the temperature of the hearth, in which the coals should not be heated to white.
The heating scale must be used to set the combustion temperature.
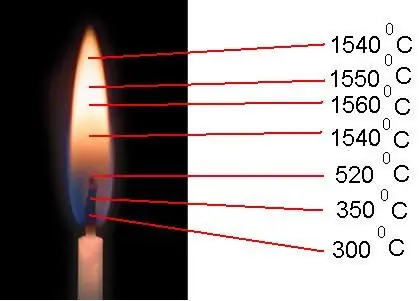
Helps not to spoil the metal workpiece
In the process of hardening the metal, you will need to place it in engine oil and warm water. The cooled steel sheets under the influence of high temperatures can deform, acquiring a wavy surface. To correct this defect, the steel sheet is leveled with a hammer. The metal hardening process can be carried out several times.
To check the quality of steel hardening, you need to use a file, the working part of which is carried out along the edge of the steel sheet. If the file sticks to the metal, this indicates insufficient hardening.
If there is no way to harden the metal, you can use refractory steel. Depending on the alloys it contains, the required melting point reaches 2500 ° C.
This makes it possible to use material with a thickness ranging from 1.5 to 3 mm. A furnace made of refractory steel with a specified wall thickness can last up to 30 years. The entire structure will be smaller than a furnace of similar dimensions made of conventional steel, and the efficiency is much higher. A vivid example is the Slobozhanka oven.
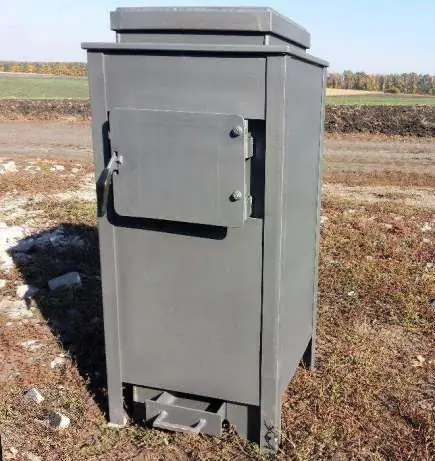
Hardened steel version
Cast iron
The melting point of cast iron is 1450 degrees. This material is often used for the manufacture of radiators in apartments and houses. It combines the properties of metal and brick. This makes cast iron a very heavy and brittle material.
Cast iron has low thermal conductivity - it retains heat well inside the furnace. In addition, the metal heats up quickly, and after the end of the furnace continues to give off heat for 3-4 hours.
To make a stove, it is necessary to use cast iron with a thickness of 6 to 25 mm. If the walls of the furnace are less than 6 mm, the structure will be very fragile. If they are more than 25 mm, then at the very first fire, the furnace body may crack. Since the entire structure will be heavy, it requires the installation of a capital base. For this, a slab foundation is made.
Stoves made of this material are effective for heating small rooms, the area of which does not exceed 60 m².
Cast iron is not suitable for self-production of such a furnace, since in the conditions of home workshops it is difficult to process.
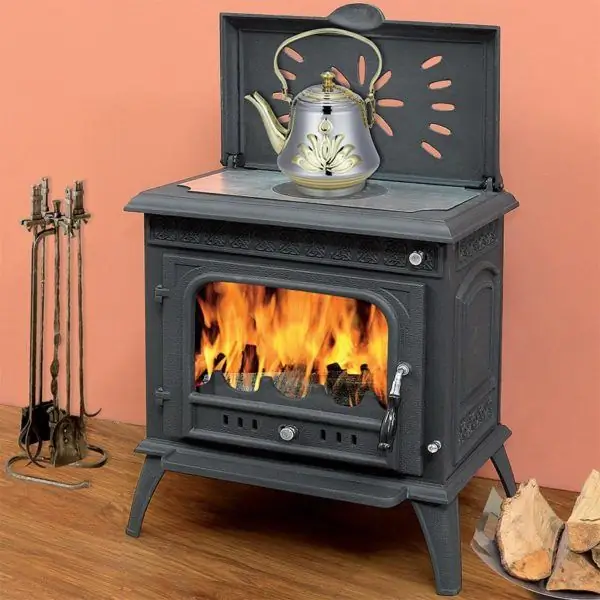
The material is difficult to process in a home workshop
Possible designs and their features
Metal furnaces are manufactured in closed, open and combined designs.
Closed design
Such an oven usually includes three compartments:
- lower, in which there is a combustion chamber with a blower;
- medium, which includes a heater and a steam outlet;
- upper, representing a tank for heating water.
Furnaces of this type are lined with refractory bricks inside and outside. This increases the heat capacity of the unit. To speed up the heating process, the tank and the steam outlet are closed with a special shutter. It takes 60 to 100 minutes to warm up a room with a volume of 10-12 m³.
Open type design
Unlike the previous type, stones are stacked on a metal grate located above the combustion chamber. There is no overlap between the firebox and the stones. As in the first case, these stoves are designed for use in small saunas and steam rooms. To increase the heat capacity, a galvanized sheet cover is used to cover the stones.
Combined type of ovens
A distinctive feature of the design of this type of furnace is the presence of an enlarged combustion chamber equipped with double valves and grate bars. The presence of two pairs of such elements in the design contributes to the efficient operation of the blower and the heater. In the upper part of the unit, stones are placed in its neck. These elements are laid around the chimney.
Calculation of basic parameters
A closed-type metal stove was chosen for manufacturing.
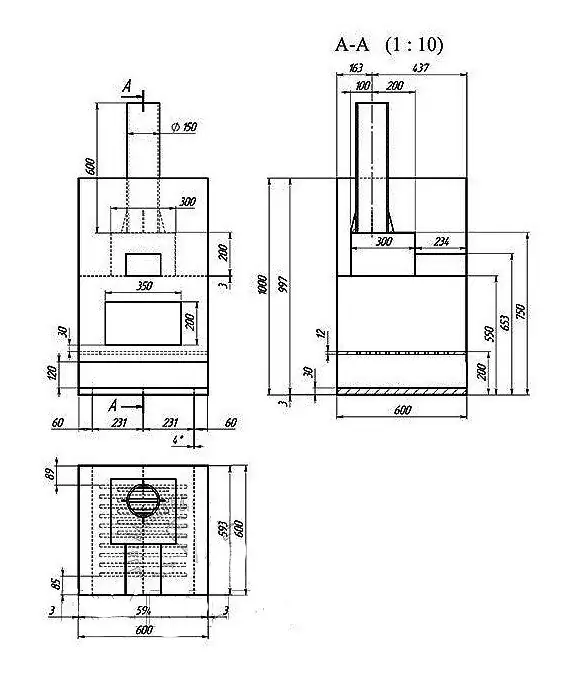
Optimal dimensions
Its base will be square, 600x600 mm in size. The height of the structure will be 1350 mm. The height of the combustion chamber is 653 mm, the chimney is 600 mm. The chimney requires a 150 mm pipe.
To calculate the volume of the combustion chamber, it is necessary to use the formula for finding the volume of the cube: V = h³, where h is the height, length and width of the figure under study. Substitute the values 0.6 ∙ 0.6 ∙ 0.35 = 0.126 m³.
To calculate the approximate heat transfer of this stove, it is necessary to multiply the volume of the heated room by the value - 21. Suppose that the room has dimensions: length - 3 m, width - 2.5 m, height - 2.3 m. For example, it will look like this: 2 ∙ 2.5 ∙ 2.3 = 11.5 m³ is the volume of the room. Now we calculate the required heat transfer of the furnace for a room of the specified size: 11.5 ∙ 21 = 241.5 kcal / h.
Required materials and tools
In the manufacture and installation of a metal furnace, the following tools are required:
- Shovel and bayonet shovel.
- A hammer.
- Pick.
- Tanks for water, concrete mortar and masonry mixture.
- Concrete mixer.
- Building level.
- Yardstick.
- Large square.
- Plumb line.
- Welding machine.
- Angle grinder.
- File.
- Cord.
You will also need the following materials:
- Concrete mix of M 300 or M 400 brands.
- Reinforcing bars for the manufacture of a reinforcing grid for the foundation.
- Waterproofing material - roofing felt or thick polyethylene.
- Masonry mix or clay.
- Asbestos cord.
- Stones (dunite, jadeite, quartzite, nephrite, talcochlorite, chromite)
- To manufacture a furnace structure from steel sheets, you will need:
- 1 sheet 3 mm thick, 60x60 cm in size;
- 4 sheets, 3 mm each - 100x60 cm;
- 1 sheet for the grate - 60x60 cm, 12 mm thick;
- 1 sheet for the partition of the combustion chamber - 60x60 cm, 3 mm thick;
- pipe with a section of 150 mm, with a wall thickness of 8 mm;
- 4 corners 10 cm long, with 5 cm wide margins.
Preparatory work: selection of the installation site and laying of the foundation
Cut parts from steel sheets must be checked for burrs and sharp metal protrusions, as they will interfere during welding. You should also pay attention to the dimensions of the cut elements.
When choosing a place for installing the oven, it should be borne in mind that these units are best installed in the corner of the room, away from walk-through doors and windows. If such a stove is intended for a bath or steam room, then it can be installed behind a small partition. This additionally protects against accidental contact with the hot surfaces of the oven.
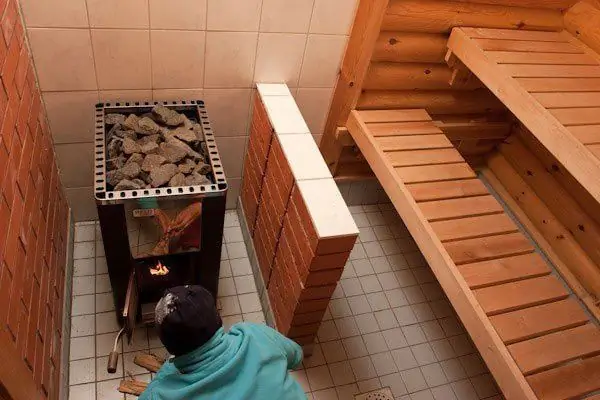
Option for a bath
It is best to erect the foundation for the stove together with the building under construction. However, if the heating structure is planned to be installed indoors, it is necessary to disassemble the floor to the very foundation. In this case, logs can be sawed only after the base has been erected to their level.
Over time, the building shrinks, and otherwise, the base of the furnace will crack, and the unit will warp.
To lay the foundation for a brick lined oven, you must perform the following steps:
- Make a marking of the future dimensions of the furnace. It is more convenient to take notes on the wall.
- Disassemble the flooring. You need to get to the very ground. Do not cut the wooden logs at this stage.
- In accordance with the markings on the wall, dig a pit 50 cm deep and 75 cm wide. If there is a large amount of sand in the ground, the pit walls may crumble. To avoid this, it is necessary to cover them with roofing material or polyethylene.
- Thoroughly compact and level the bottom of the pit.
- Pour medium gravel inside to form a layer with a thickness of 250 mm.
- Lay waterproofing on top of it - roofing material.
-
Then fill in a layer of sand equal to 150 mm. It must be tamped. It should be noted that wet sand is better compressed.
Base scheme for a brick lined metal furnace Concrete thickness can be replaced by brickwork
- Make formwork for liquid concrete from boards or OSB boards. If it is made of boards, then concrete can be poured out through the cracks or earth can be poured inside. To prevent this, the inner surface of the formwork can be covered with polyethylene.
-
Now you need to make a metal frame that will strengthen the concrete base. This requires reinforcing rods with a thickness of 8 to 10 mm. Of these, it is required to make a volumetric structure consisting of two gratings connected at a distance of 200 mm parallel to each other. The width of the cells should be no more than 150x150 mm. Rebar intersections can be reinforced with welding, wire or plastic straps.
Foundation reinforcement The metal structure should be below the upper level of the future foundation
- Install the finished metal frame inside the formwork. It should be noted that this structure must be placed at a height of 50 mm above the waterproofing. To do this, you can drive in wooden stakes or pieces of reinforcement perpendicular to the base. Attach a metal frame to them. You can use halves of bricks for this, which will create the desired height for placement.
- Pour concrete mixture. For this, the M 300 or M 400 brand is suitable. It should be noted that all the elements of the reinforcing cage are hidden under a layer of concrete. In the process of pouring the foundation, air bubbles are formed, which must be removed by bayonetting or using a deep vibrator.
- Cover the filled mixture with polyethylene. This is necessary for uniform solidification of the foundation. If this is not done, moisture will evaporate from the top layer of concrete. This can cause the hardened base to crack and lose its strength. After 8-10 days, the foundation will harden.
- Clean the cured base from dust and debris.
- Cover with waterproofing material. For this, roofing material or thick polyethylene is suitable.
-
From above, in a continuous layer, make a masonry of refractory red bricks. When the level of the masonry reaches the logs, they must be sawed so that the wooden ends lie on the concrete base.
Prepared base for the installation of a metal furnace and brickwork Roofing material will be laid on top of solid brickwork
DIY step-by-step instructions for making a metal furnace
A metal furnace can be made not only from steel sheets, but also using scrap materials. If everything is clear with steel structures, then an old bath can be used as a cast-iron frame. Below is a variant of making a stove-heater from steel sheets.
Stove making
- Cut parallel strips 8 mm wide in steel sheet 12 mm thick. This structural element will play the role of grates.
-
Connect the steel sheets by welding according to the diagram.
Diagram of the main elements of a metal stove-heater Optimal parameters indicated
- Weld on a pipe with a diameter of 150 mm.
- Weld a 350x200 mm steel door to the finished furnace body, which will close the combustion chamber.
- Weld a 150x100 mm door to the blower hole.
-
Use an angle grinder to remove burrs and sharp fragments from the surface of the furnace body.
Grinding the metal surface of the furnace The surface becomes matte
- Weld steel corners to each corner of the furnace bottom, with a width of 50 mm fields. The whole structure will stand on these elements.
- Install the structure on the prepared base.
-
Now the oven must be bricked. To do this, the building material must be soaked in water for 30 minutes. After that, make a markup for masonry. During masonry, the casing of the oven can be stained with mortar. Therefore, it is advisable to cover the metal structure with plastic wrap. It should be noted that the brick structure must be erected at a distance of at least 10 cm from the wall, and the surfaces of the adjoining walls must be covered with sheet metal or refractory tiles. This is necessary for fire safety purposes.
Soaking bricks in water Promotes better adhesion
- Laying begins from the corner of the marking. Lay the bricks flat. The seams between them must be the same, no more than 5 mm.
-
A reinforcing mesh must be laid between the first and second row. For this, it is cut into strips and laid. This element will strengthen the brick structure.
Reinforcement of rows of brickwork The mesh will strengthen the structure
-
In the third row of masonry, it is necessary to leave two gaps for holes. This will help normal air circulation.
Creation of air exchange in the oven As a result, the heat transfer of the furnace will increase.
- Lay out the next rows with a dressing.
-
The lining of the combustion chamber must be laid out with fireclay bricks. This material can withstand high temperatures without changing its structure.
Furnace lining Fireclay bricks are used
-
During masonry, blower doors and latches are installed in the lower and upper rows. These elements are designed to regulate draft, shut off and direct hot streams.
Installation of blower doors These elements will help regulate air flow
-
A heating shield can be provided in the design of the brick lining of the stove. The diagram shows the stages of building rows.
Ordering the heating plate The design will help regulate heat depending on the season
Chimney device, its manufacture and installation
The order of the chimney has its own characteristics. At the junction of the chimney with the roof, there is a masonry extension. From the outside, this protrusion protects the structure from atmospheric precipitation, from the inside, it reduces the temperature of the outgoing stream. The diagram shows the order of the chimney for a metal stove-heater.
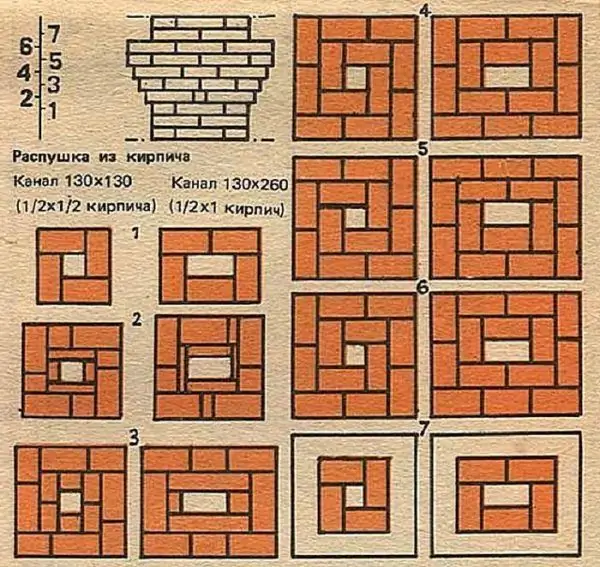
The fluff makes it possible not to use insulation
Decor
You can decorate the oven in various ways:
- Plastering.
- Finishing with facing bricks.
- Tiles.
- Various types of tiles (terracotta, majolica, clinker).
- Natural and artificial stone.
- Marble.
- Metal.
Finishing the furnace with metal is the simplest and most effective way. For this, sheet steel or rolled aluminum is used. Furnace end surfaces coated with these materials create an additional insulating layer.
For coloring the metal, silicone paints of various shades are used.
Features of operation: cleaning and repairing the stove
Operation of a brick-lined stove must comply with the following rules:
- Before each use of the heating unit, check the presence of draft. For this, the metal latch is pushed back. The absence of draft or its movement in the opposite direction will indicate a clogged grate or the entire chimney channel.
- In order to minimize the amount of carbon deposits formed when burning firewood, it is necessary to use wood of certain species. For this, aspen, oak, birch and beech firewood are suitable.
- It is best to use softwood shavings for kindling, as this material contains resins that ignite quickly. For this purpose, it is convenient to use pine and spruce cones.
- With the constant use of a metal heater, it is necessary to take care of cleaning the chimney from soot every heating season. If the stove is used several times a month, this procedure is performed once every 2-3 years.
- Effective combustion of firewood occurs only when the combustion chamber is loaded by 1/3.
- If cracks appear in the brickwork, they are sealed with special clay blue rocks or special mixtures for laying furnaces. The oven can be heated only after the clay has dried.
Having studied the nuances of making a metal stove, you will not only be able to make a high-quality heating unit yourself, but also successfully use it for heating household and utility rooms.
Recommended:
Facing And Decorating The Stove In The House With Your Own Hands (including Ceramic Tiles), Instructions With Photos And Videos
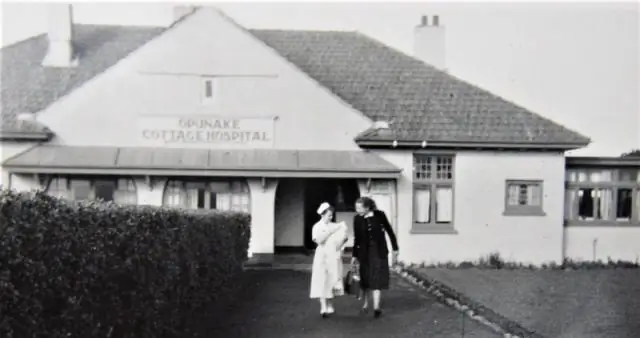
Do-it-yourself cladding and finishing of the stove: what is it for, what types are used, step-by-step instructions, decor. Tips for choosing tools and materials
How To Clear A Blockage In A Bathroom: Ways To Clean A Bath Drain, A Siphon, A Mixer, A Pipe With A Cable And Other Means + Photo And Video
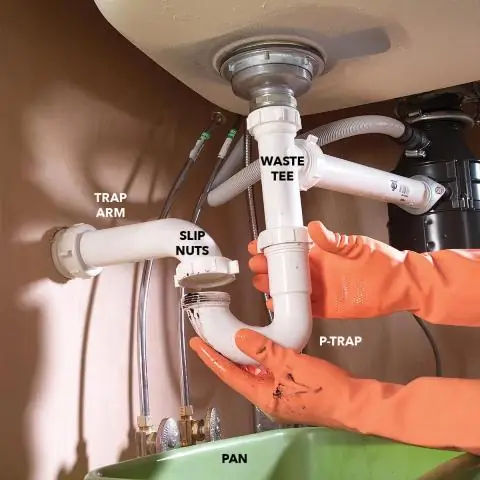
Reasons for blockage in the bathroom and its prevention. How to clean the drain and pipes: chemistry and mechanical cleaning. How to disassemble a siphon, mixer. Photo and video
How To Choose And Build A Foundation For A Bath With Your Own Hands - 4x6, 3x4 And Other Sizes, Tips, Instructions, Photos And Videos
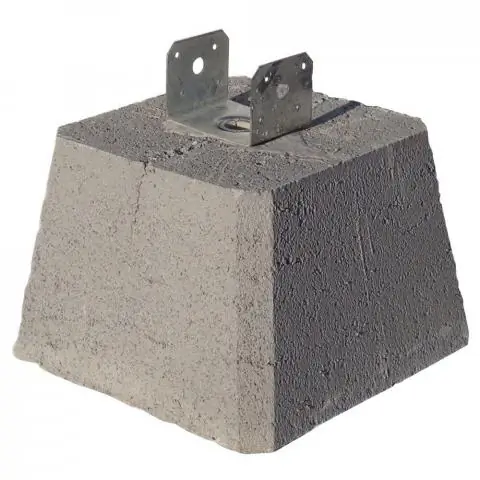
How to make a foundation for a bath with your own hands. Types and features of foundations. The choice of materials and technology, installation rules and step-by-step instructions
How To Clean A Stove With Your Own Hands - Repair, Cleaning A Brick Russian, Bath, Round Stove From Soot Without Disassembling Why It Does Not Heat Well, Reasons, Cleaning Wells, G
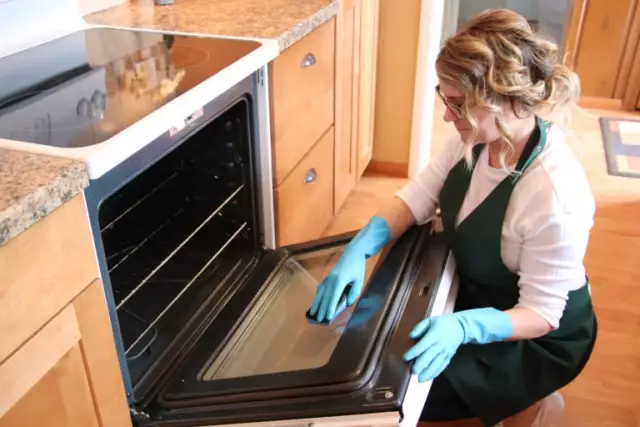
How to repair and clean the oven with your own hands. Types of repair, when and why you need it. List of necessary tools and nuances to consider
Coffee Turka: How To Choose The Right One, Which Is Better, Copper Or Brass, Electric Or For A Stove And Other Options + Reviews, Photos, Videos
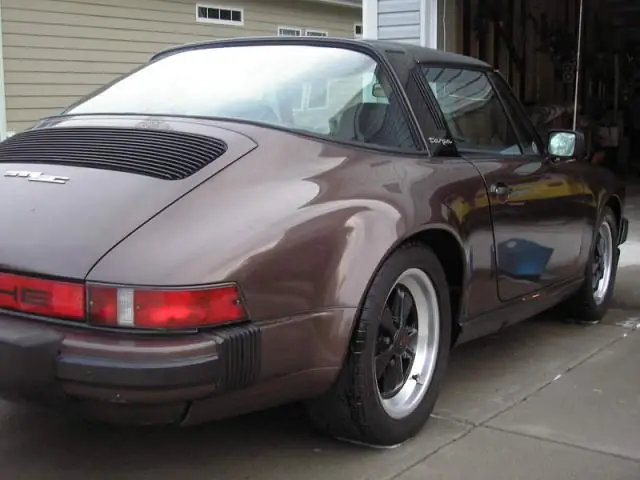
Coffee in the morning is an undeniable classic. And to make it great, you need to choose the right Turk. Our article will help you decide