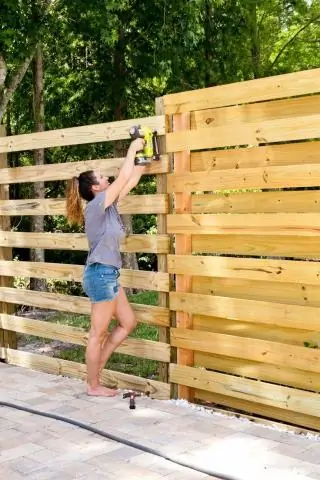
Table of contents:
2025 Author: Bailey Albertson | [email protected]. Last modified: 2025-06-01 07:32
DIY concrete fence
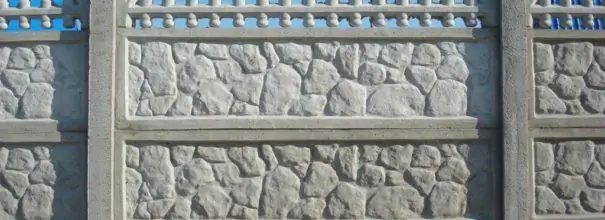
Even with the current huge selection of materials, a decorative concrete fence is one of the most demanded and popular types of modern fences. It will not only provide reliable protection to the site, but also become its aesthetic decoration. It is also captivating that such a fence will last a very long time without losing its quality characteristics, and you can cope with its manufacture with your own hands.
Content
-
1 Advantages of concrete fences, features and disadvantages
- 1.1 Types of concrete fences
- 1.2 Photo gallery
-
2 DIY concrete fences
- 2.1 Calculation of the number of concrete sections
- 2.2 Tools for the job
- 2.3 Mortars for the construction of a concrete fence
- 2.4 Step-by-step process of pouring concrete mixture into the finished form
- 2.5 Video: How to make a concrete fence
-
2.6 Installing concrete fence supports
- 2.6.1 Mounting on solid poles
- 2.6.2 Installation of the fence on the type-setting posts: step by step instructions
-
3 Painting and decorating a concrete fence
- 3.1 Which paint is suitable
- 3.2 Colors
- 3.3 Paint application technology
- 3.4 Painting video
Advantages of concrete fences, features and disadvantages
Before installing a concrete fence, you should familiarize yourself with its advantages and disadvantages. The advantages of a concrete fence are quite significant:
- Long service life (up to 50 years).
- Wear resistance.
- All kinds of texture and color options.
- Simple installation.
- Fire safety and frost resistance.
- Versatility - can be used for all types and sizes of sites.
- Shielding of noise.
- Impermeability.
There are also disadvantages:
- A concrete fence needs regular maintenance - treatment and prevention of damage.
- The dimensions of the structure are limited due to design features.
- Great weight.
- Poor shock resistance.
- A foundation is required to install monolithic panels.
- Not cheap price.
- Concrete box effect.
Types of concrete fences
- Monolithic. These are heavy reinforced concrete panels, for the installation of which a crane is used. They need a powerful foundation - tape or columnar. This is the most durable fence option, which is most often used in industry - for fencing warehouses, workshops and enterprises.
- Typesetting. Due to the small size and weight of the sections, such fences are very popular in the private sector. The sections are inserted into the grooves of the support posts, so two or three people can easily cope with the installation. The fence can be made both deaf and openwork, or combined from different types of sections.
- Double-sided. They look the same - both from the outside and from the inside.
- One-sided. A cheaper option with a pattern or texture on only one side.
If we talk about factory products, the most popular are concrete fences (or eurofences), which are assembled from blocks or horizontal sections. Their width, as a rule, is 2 meters, and their height is from 0.3 to 0.5 meters. Blocks weigh from 25 to 70 kilograms. Such structures are easy to transport and cost less than their monolithic counterparts. The composition of the eurofence is cement (grade 500), fine gravel, sand, reinforcement (steel reinforcement and polypropylene fiber) and superplasticizer. It can be of any color and faced with the desired material - marble, granite or ceramics.
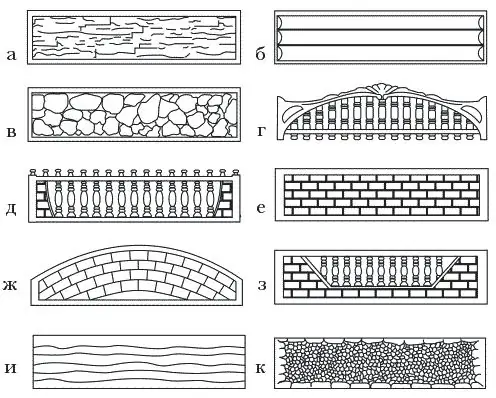
There are many different types of fences
They also produce cinder block slabs that are resistant to frost. Expanded clay or pebbles are added to the concrete mix for these slabs.
Photo gallery
-
Fence with decorative elements - Combined fence
-
Concrete wattle - Fence imitating wattle fence
-
Pebble texture - Imitation pebbles
-
Imitation of texture - Imitation of stone texture
-
High fence with decorative elements -
High fence with decorative elements
-
Combined fence - Low combined fence
DIY concrete fences
Calculating the number of concrete sections
The manufacture of a concrete fence begins with the calculation of the number of slabs that are required to fence the site along its entire perimeter. To do this, you need to mark the territory. Pegs are hammered in the corners of the perimeter of the site, between which the cord is pulled. This will be the line of the future fence. It is important to mark the places where the installation of the slabs will not be possible in order to move the fence forward or backward.
The standard size of the Euro plate is 2 m wide and 0.5 m high. However, taking into account the tolerances and all kinds of gaps, it is customary to take a length of 2.06 m as a basis.
The recommended fence height is 2 meters. In this case, the site will be hidden from prying eyes. When calculating, it is necessary to take into account the support pillars, the cross section of which is 15x15 cm. Thus, when installing 10 slabs with a length of 2.06 m, the fence length will be 20.75 m, taking into account the first and last support pillars.
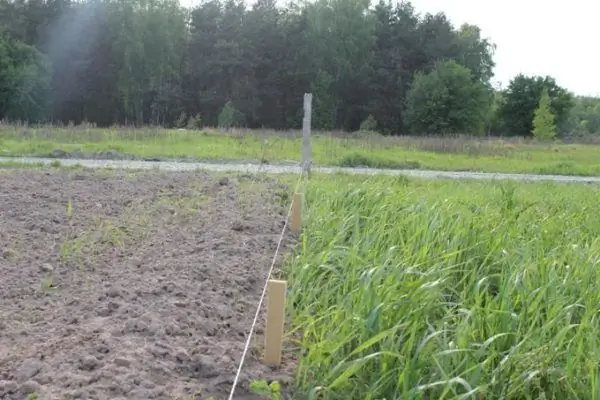
Territory marking
Tools for work
- Concrete mixer or other container for the mixture.
- A trowel, a shovel, a pointed rod.
- Form for sections.
- Armature (wire).
- Level.
- Materials for the mix.
- Vibrating table.
- Composition for lubricating molds.
The process of making and installing a concrete fence is not too time-consuming, but it will take time and several pairs of working hands. If you decide to cast the plates with your own hands, then the first step is to decide on the proportion of the future solution, its composition and shape of the product. The quality of the components is also important: for example, the use of untreated sand instead of prepared sand can contribute to the deformation of the slabs under the influence of the external environment after a few years.
Mortars for building a concrete fence
Main ingredients for the mix:
- Cement (grade not lower than 400).
- Purified river sand, size 1.3-3.5 mm.
- Gravel, washed crushed stone.
- Water.
Standard mortar for concrete blocks
- Crushed stone or expanded clay - 1 part.
- Sand - 3 parts.
- Cement - 1 part.
- Plasticizer - according to the instructions.
- Water (until the mixture becomes thick sour cream in consistency).
Foundation mortar
- Crushed stone - 2 parts.
- Cement - 1 part.
- Sand - 2 parts.
- Water (to optimum density).
For ease of pouring concrete, you can use ready-made forms. They are:
- Polypropylene.
- Rubber.
- Plastic.
- ABS.
- Fiberglass.
Step-by-step process of pouring concrete mixture into the finished form
Step 1. Before pouring the panels into the mold, you need to prepare the reinforcing frame. For it, reinforcement or metal wire with a diameter of 4 to 6 mm is used. The material is laid with a mesh, with a step of 10 by 10 cm, and welded.
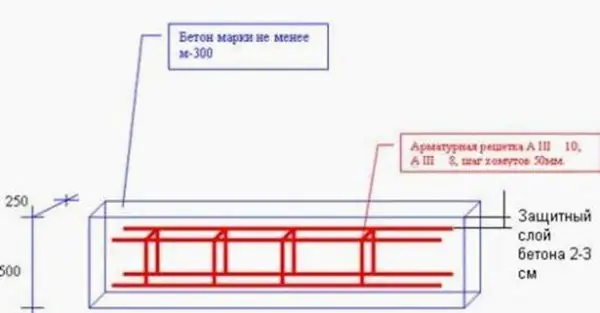
Rebar laying scheme
Step 2. Preparation of the composition. It is best to mix the solution in a concrete mixer, but if it is not there, then any bulky plastic container or an old bath will do. All components are poured into it, and then water is gradually added. In this case, the density of the solution is regulated. The mixture is thoroughly mixed until smooth (no more than 10 minutes), and poured into a prepared mold previously installed on a wooden board or an old door. The base is leveled.
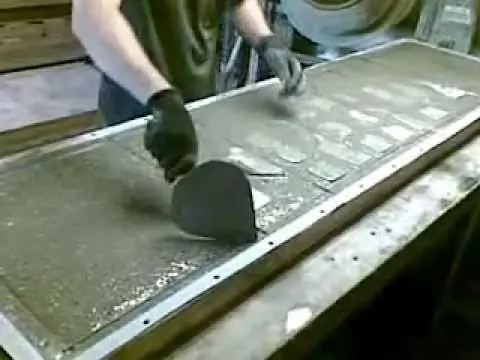
Filling the mold with concrete
Step 3. The mold must be lubricated with a composition of diesel fuel and used engine oil.
Step 4. Pour half of the solution into the mold and wait for a while. Next, we lay the reinforcing mesh and distribute the rest of the mixture from above.
Step 5. We knock on the wooden board with a hammer so that the concrete, having compacted, releases cement milk onto the surface. This simulates vibrocompression, during which the concrete completely fills the mold. You should also pierce the grout with a pointed rod to release air.
Step 6. Smooth the surface with a spatula and cover the form with a film until the mixture finally hardens. The process takes one to three days. Concrete takes longer to mature - up to 30 days. Only after their expiration can the panels be installed. Finishing work - priming and painting, is performed 6 months after the panels are manufactured.
Video: How to make a concrete fence
Installation of supports for a concrete fence
The service life of the fence directly depends on the correctly installed supports. They take on the entire load, therefore, the higher the concrete fence, the more powerful its supports should be. Fencing posts can be stacked or solid. But in both versions, grooves are provided for installing concrete sections.
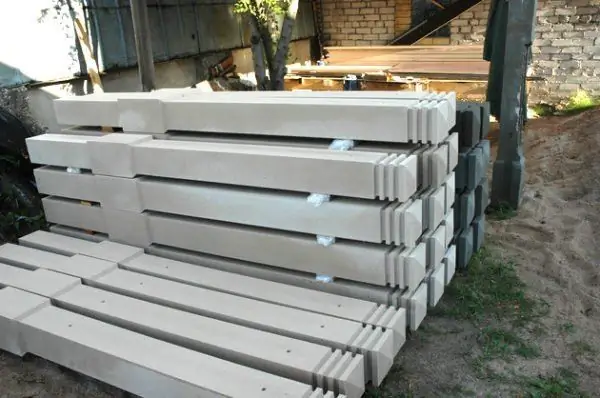
Ready-made concrete fence posts
Mounting on solid posts
There are two ways to mount on monolithic posts.
The first is that all the pillars are concreted in the marked places at once, and after the concrete has hardened, the slabs are installed in the grooves (through the top). The downside is that it is difficult to implement without special devices, and also that this method does not tolerate errors in the markup. It will be impossible to eliminate the error without a complete rework.
The second method is more convenient. Only the first pillar is concreted, and the second is not rigidly fixed. Next, all the plates are put on the pillars, and then the second pillar is tightly put on them and fixed with broken bricks. The structure is leveled and installation is continued further. The pillar is poured with cement after all the plates have been installed.
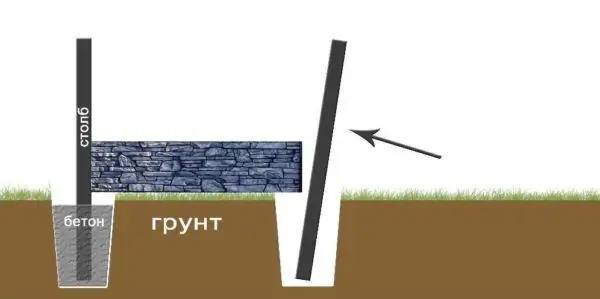
Floating pole mounting technology
Step 1. Markup. The strength of the fence depends on the accuracy of the installation - if the pillars are located too close, then the panel will not enter the grooves, and if it is too far, then the section will fall out. Therefore, it is important to drive the pegs in correctly.
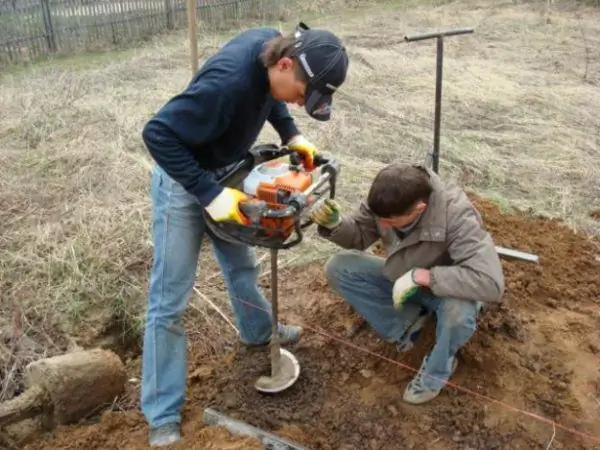
Well drilling for supports
Step 2. Drilling wells under the pillars for a third of the pillar length.
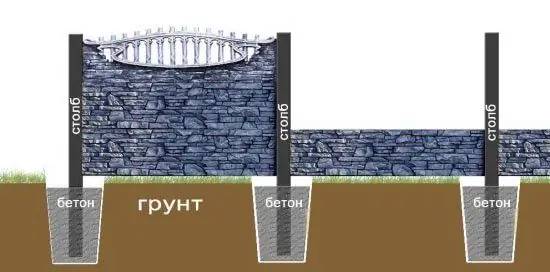
Pole installation scheme
Step 3. Installation of the support post. It is installed in a pit and covered with rubble 15 cm. After that, its verticality is checked by the level, and the pillar is poured with concrete. The extreme supports are installed and a string is pulled between them. The rest of the pillars are already equal to it.
Step 4. Installation of sections in the grooves of the posts. Fastening them with a solution to each other. Some masters do not advise to completely close up the cracks, since the pillars can “play” in winter and they need compensation gaps.
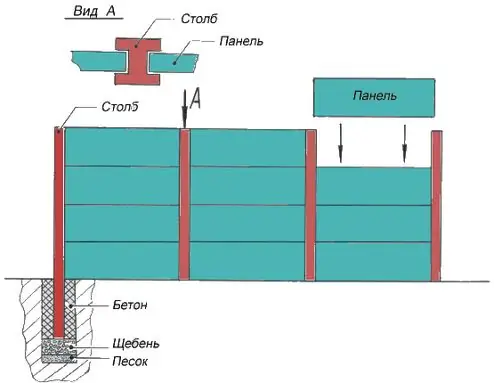
Fence installation scheme on solid pillars
Installation of a fence on type-setting posts: step by step instructions
Stacked posts are hollow blocks assembled around a steel pipe or cast onto a reinforcing cage. The cavities of the blocks are usually filled with concrete.
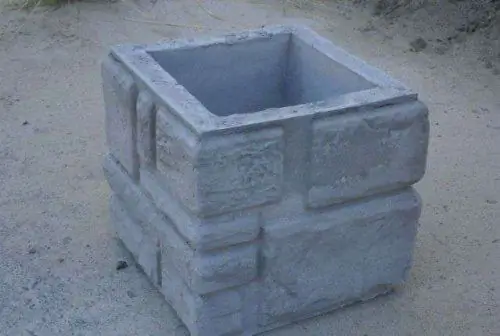
Hollow post block
This technology is good in that it does not require a foundation for the entire fence - it is needed only for the posts.
Step 1. Prepare holes 1 or 1, 2 m deep and 20 cm wide.
Step 2. Backfilling of rubble to the bottom of the pit.
Step 3. Installing the pipe or reinforcement so that it protrudes 40 cm from the ground, and then concreting it.
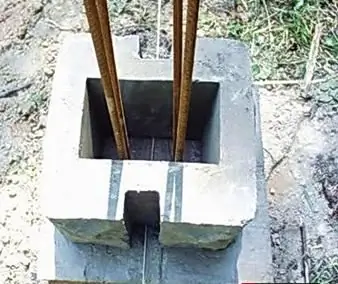
Arrangement of fittings
Step 4. After preparation of the foundation, the column is assembled. The first block is put on each post along the entire length of the fence. The block is positioned so that the metal core is in the middle.
Step 5. The first row of panels is put into the recesses of the posts and poured with concrete. The concrete should be liquid, and the ratio of sand to cement is 1 to 4, or even 1 to 5.
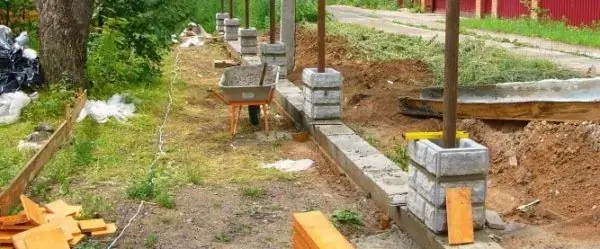
Blocks are put on reinforcement and concreted
Step 6. Next, the second row is installed, until the height of the fence reaches 1.5 m. After that, soil is poured to the lower section of the fence. It is not necessary to deeply bury it in the ground - otherwise, in frost, the ground will begin to break the fence.
Step 7. Installation of blocks continues until the installation of the upper decorative panel.
Step 8. Installing the caps on the poles.
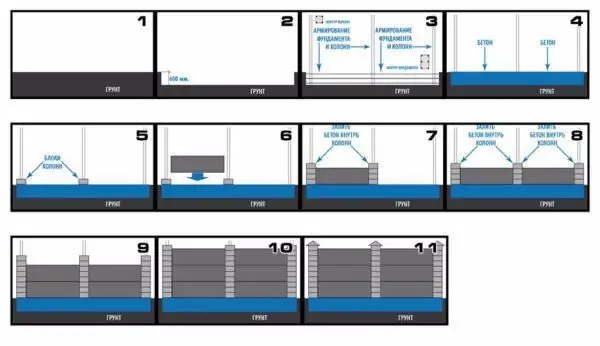
Fence installation diagram
Painting and decorating a concrete fence
In order for a concrete fence to serve as long as possible, it must be properly looked after. There are several reasons for this.
- Technical. Painting is needed in order to protect the concrete from external influences and to extend the life of the fence.
- Psychological. By itself, concrete is inconspicuous, and the color will make it brighter and more pleasing to the eye.
- Decorative. In order for the fence to be in harmony with the color of the room, an appropriate shade is selected.
What paint is suitable
Increased demands are placed on paint for concrete fencing. She must be:
- moisture resistant;
- frost-resistant;
- resistant to temperature extremes and sunlight.
These requirements are fully met by any type of facade paint - both matte and glossy. If the fence is located on the sunny side, then it is better to choose matte paint, because glossy paint will glare strongly. It is preferable that the paint is water-based. For example, acrylic, acrylate, silicone or latex. The main thing is that it has a low level of vapor permeability and a sufficient content of acrylates.
When calculating the amount of paint, it must be borne in mind that the more embossed the surface of the fence, the more material will be needed. On average, 1 m² will require about 300 ml of paint.
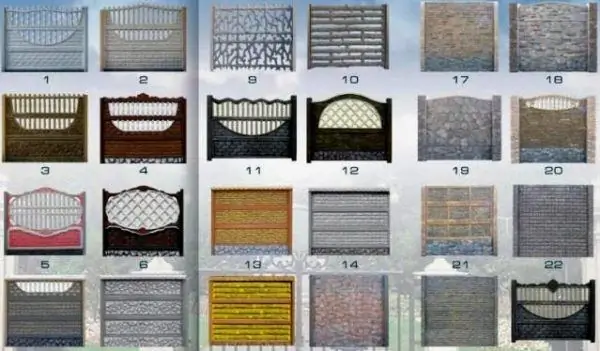
Various decor of concrete fences
Color solutions
Most preferred from an environmental point of view are colors such as brown, green, gray, blue or beige. These natural shades will harmonize and set off flowering plants and green spaces. Do not make the fence too colorful and multicolored - a combination of two or three shades is enough. Textured elements are highlighted using white, gray or dark colors.
With paint, you can simulate any surface - for example, sandstone or wood. To paint like sandstone, you must first apply a light brown paint, and then a dark brown one (with a foam sponge).
Paint application technology
It is not recommended to paint a new fence right away, as it should shrink. Six months later, you can start finishing work. The painting principle is the same for both new and old concrete fences. First, preparatory activities are carried out. They include:
- Cleaning the surface of the fence from dust and dirt;
- Surface primer and crack bridging.
Priming must be carried out before painting the fence - it will ensure better adhesion of the paint to the concrete surface and get rid of dust and dirt.
- It is better to paint a porous concrete fence with a spray gun or other professional equipment.
- If the old fence was restored, you need to wait until the filler materials are completely dry. Irregularities are cleaned off with a mesh or sandpaper.
- The fence is painted in two layers.
- The primer dries for a day, so you cannot immediately paint the primed surface.
- The second coat of paint is applied after 24 hours.
- Do not paint at high humidity and low temperatures (below +5 ° C).
Painting video
Having studied the process of making a concrete fence, you can try to make it yourself. As a result, you will appreciate the cost savings and great satisfaction with the work done. A hand-made fence is a unique product that will last for many years.
Recommended:
How To Make A Bar Stool With Your Own Hands From Wood, Metal And Other Materials + Drawings, Photos And Videos
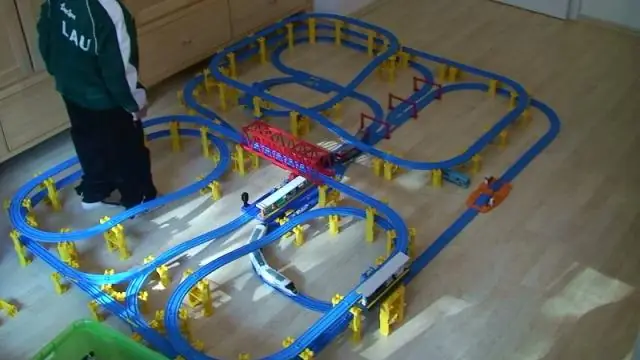
Bar stools manufacturing options. Required tools, materials used. Step-by-step description of the manufacturing process with a photo
How To Properly Lay Linoleum On A Wooden, Concrete Floor, On Plywood With Your Own Hands In An Apartment, In A Room + Installation Video
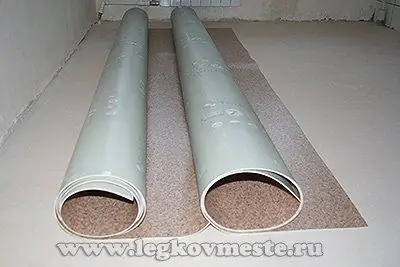
Laying linoleum on the floor in an apartment with your own hands. How to properly lay material on different types of floors, without moving furniture, and cut it to the walls
How To Make A Kite With Your Own Hands At Home: Options With Drawings And Sizes + Photos And Videos
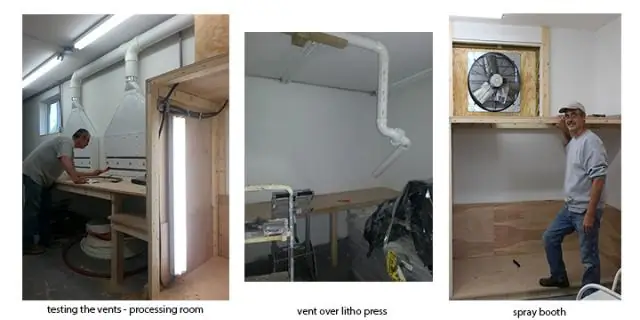
DIY kite: the necessary materials, diagrams, drawings, manufacturing steps. How to make a kite of different shapes. Secrets of a Successful Launch
How To Install Fence Posts With Your Own Hands, Including Without Concreting, At The Correct Distance And Depth - Instructions With Photos And Videos
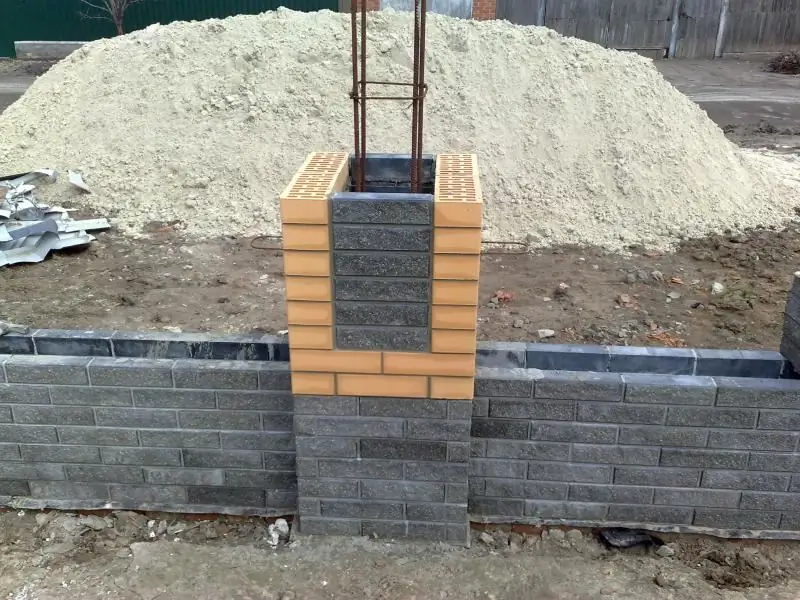
How to install fence posts: installation methods, use of suitable materials
How To Make A Slime At Home With Your Own Hands - Without Sodium Tetraborate And Glue, From Hand Cream, Shaving Foam And Other Ingredients, Recipes With Photos And Videos
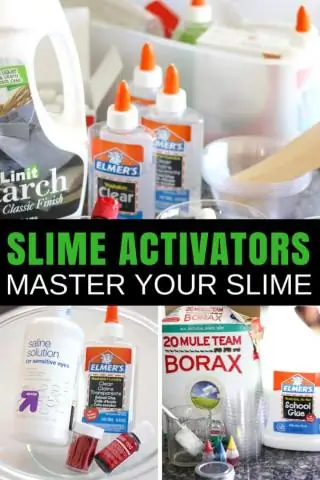
Is it possible to make a slime at home. Types of slimes and recipes for their manufacture, depending on the desired properties. Toy care features