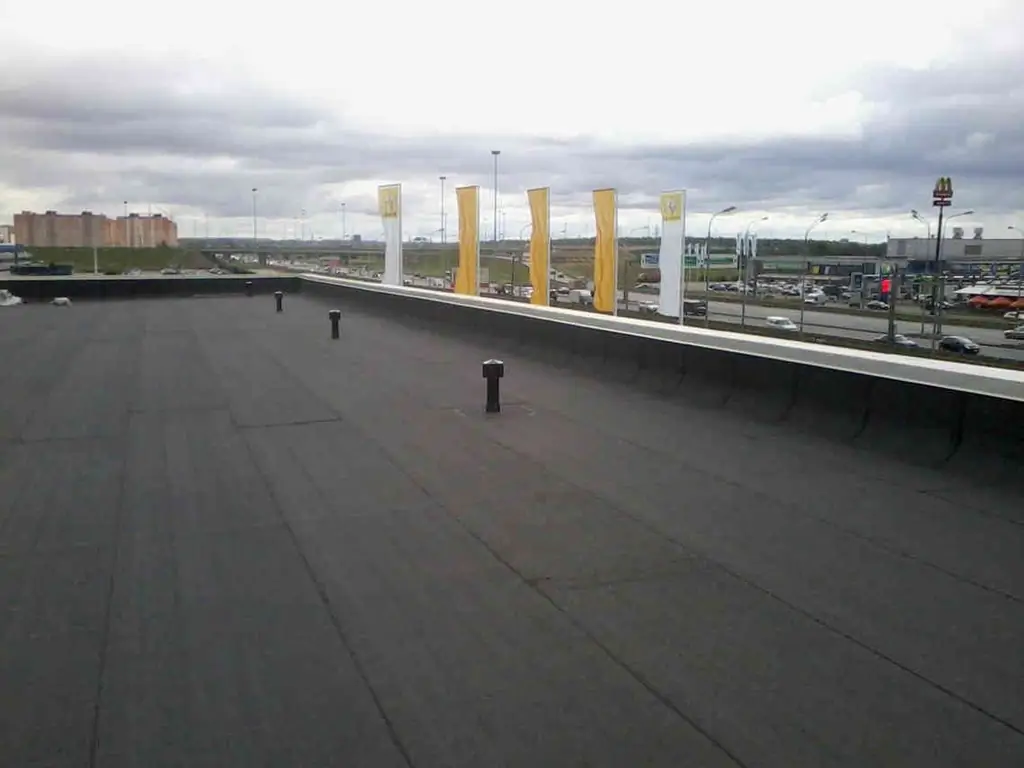
Table of contents:
2025 Author: Bailey Albertson | [email protected]. Last modified: 2025-06-01 07:32
Features and characteristics of the welded roof
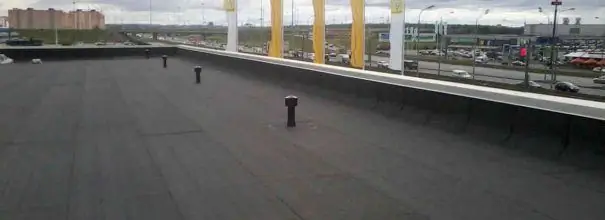
Most often, a weld roof is used to cover flat roofs and surfaces with small slopes. To create it, a roll material based on a canvas impregnated with polymer bitumen components is used. The weld-on roof is installed both on residential buildings and in warehouses, hangars, industrial facilities and other structures.
Content
-
1 Welded roof: features and characteristics
-
1.1 Materials for welded roofing
- 1.1.1 Base of the welded roof
- 1.1.2 Binders
- 1.1.3 Spreads
-
-
2 Tools for overlaid roof
2.1 Video: tools needed to create a weld roof
- 3 The device of the overlaid roof
-
4 Features of the installation of the welded roof
- 4.1 Errors during the installation of the welded roof
- 4.2 Video: installation of a welded roof
-
5 Features of the operation of the welded roof
- 5.1 Video: soft roof problems
- 5.2 Service life of the overlaid roof
-
6 Repair of overlaid roof
- 6.1 Local damage
- 6.2 Bulges
- 6.3 Cracking
- 6.4 Separation of the waterproofing layer from the base
- 6.5 Delamination at junction points
Weldable roof: features and characteristics
A few decades ago, only roofing material was used to create a welded roof - a material based on cardboard impregnated with bitumen. It regularly performed its functions until the bituminous layer lost its properties. After that, the coating had to be changed. Since then, the technologies for the production of roofing materials have become more perfect, as a result of which new types of roll roofing with a multilayer structure have appeared:
- Bottom layer. This is a polyethylene film, which, in addition to the protective function, plays the role of an indicator that allows you to determine the optimal heating temperature during installation.
- Working layer. The working surface is made of bitumen or bitumen-polymer compositions, as well as just bitumen.
- The foundation. Reinforcing fabric acts as the base of the roll. Nowadays, cardboard is no longer used; it has been replaced by polyester, fiberglass or fiberglass.
- Second working layer. To cover the base, the same polymer compositions or bitumen are used.
- External powder. Basalt chips are usually used.
This structure provides high strength, durability and good waterproofing characteristics of the roof covering. But they appear only in the case when the technology of installation of the overlaid roof is observed.
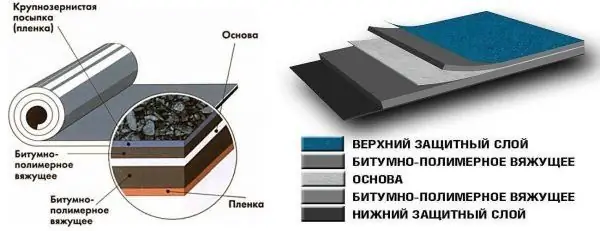
The multilayer structure of the overlaid roof ensures its high strength and durability, subject to the installation technology
The weldable roof has a number of advantages that make it well-deserved popularity:
- light weight - the material is easy to load, bring and deliver to the roof;
- the presence of a layer of mastic on the inside, which greatly simplifies installation;
- reliability - during the period of operation, such a coating does not require special care;
- high strength;
- good hydro and sound insulation characteristics;
- resistance to temperature changes;
- environmental friendliness - during operation, such a roof does not emit harmful substances;
- affordable cost.
Materials for overlaid roofing
When creating a roll roof, different materials are used for the base, dressing and binding components. In order to understand what a particular roof covering is made of, you need to look at its markings:
-
The first letter indicates the type of base:
- "T" - fiberglass;
- "X" - fiberglass;
- "E" stands for polyester.
-
The second letter indicates the type of outer coating:
- "K" - coarse-grained mineral dressing;
- "M" - fine-grained dressing;
- "P" - polymer film.
-
The third letter characterizes the bottom cover:
- "M" - fine-grained sand;
- "P" - polymer film;
- "C" - suspension;
-
"F" - foil.
Weldable roof marking The marking of the overlaid roof consists of three letters, each of which indicates the type of a certain layer in the coating structure
The base of the welded roof
Unlike the paper backing that was used in the past, modern materials do not rot and do not allow mold to develop. There are several options for creating a base, which differ in strength and price:
- Fiberglass. The fiberglass material is not very strong, its quality will depend on the type of impregnation. The elasticity of the fiberglass is low, so it must be carefully transported and laid. If the material is bent during installation, it may burst. It is not recommended to use such a coating for the roofs of residential premises, since it has a short service life.
- Fiberglass. It consists of more ordered glass filaments, which provides it with greater strength compared to fiberglass. But the elasticity of this material is also not very high.
-
Polyester. This is the strongest and most reliable base, but it also has a high cost. Polymer fibers, which make up polyester, are arranged in a chaotic manner and provide high shown strength, wear resistance and elasticity.
Technoelast EPP One of the strongest and most reliable roll coatings is the "Technoelast EPP" deposited material, consisting of polyester, wrapped on both sides in a polymer film.
Binders
Bituminous impregnation is used as a binder, which can be of several types:
- Oxidized bitumen. This is the cheapest material that does not have very high characteristics, therefore, such roll coatings are used only to create the lower layer of the roof. They are not suitable for regions with frequent temperature changes and require additional protection against UV radiation.
- Polymerized bitumen. It can be used at air temperatures down to -25 o C. Isotactic and atactic polypropylene increase the tensile strength and density of the material, but this also increases the melting point. The APP supplement is cheaper than the PPI, but its characteristics are very slightly inferior. Styrobutadiene styrene is used for coatings on complex roofs located in harsh weather conditions. Such materials have high ductility, they are often called rubber bitumen.
Sprinkles
Special dressing is used to strengthen the top layer. They help to resist solar radiation, atmospheric precipitation, increase the hardness of the coating and its service life.
The dressing can be of different fractions:
- dusty - used for the bottom layer of the roofing cake, does not allow the sheet in a roll to stick together;
- fine-grained;
- middle fraction;
- coarse-grained;
- scaly.
Foil or plastic foil can be used instead of mineral dressing.
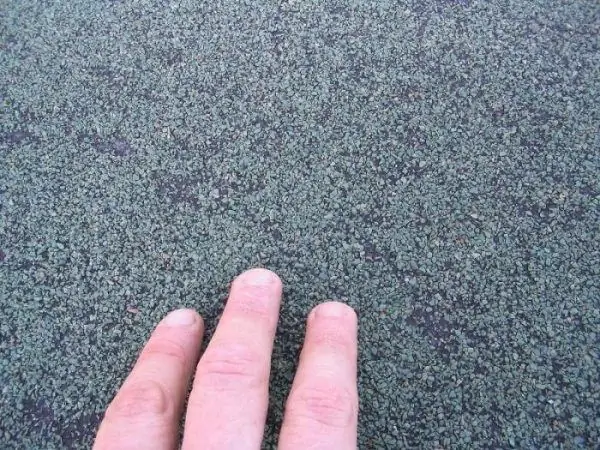
In order to make the top layer more durable and resistant to the external environment, it is sprinkled with mineral chips
To create a welded roof, the material is laid in 2-5 layers, the roll width is usually from 400 to 1050 cm, and the length is from 7 to 20 meters
Hardfaced roofing tool
The installation of the weld-on roof, although not particularly difficult, will require a certain set of tools to complete it:
-
gas-air injection burner, which is connected to a gas cylinder through a reducer;
Gas-air injection burner The gas-air injection burner is connected to the cylinder through a reducer
- hose with a diameter of 9 mm and a length of 10-15 m for connecting the burner to the cylinder;
- knife;
- stick for rolling out the material;
-
roller for rolling the rolled material;
Roller for rolling up roll material After heating the bottom layer, the material is pressed to the roof and rolled with a roller
- spatula for smoothing out beads;
- an ax for removing old roll coating;
- broom, broom or industrial vacuum cleaner to clean the surface before laying the material;
- brush for applying primer;
- overalls - shoes with thick soles, gloves, overalls.
Video: tools needed to create a weld roof
The device of the overlaid roof
The roofing cake of the overlaid structure is a coating that reliably protects the roof from the negative effects of external factors throughout the entire period of its use. Roll materials are used for roofs with a slope of 1 to 12 degrees.
The composition of the roofing cake for roll materials is no different from what is done for piece soft coatings:
- vapor barrier - this layer consists of a film or weld-on material and is attached with an overlap of strips and sealing of seams;
-
thermal insulation - plate heaters are usually used, which are glued together with hot bitumen;
Insulation of a flat roof Insulation can be glued with bitumen mastic or fastened with disc-shaped dowel nails
- cement-sand screed - it is performed over a layer of thermal insulation, its thickness is usually 5 mm. If the coverage area is large, then the screed is made with 6x6 m squares, separated by expansion joints;
-
waterproofing - laid in several layers with an overlap of 150 mm with high-quality sealing of the joints.
Diagram of the device of the overlaid roof The base for the welded roof can be a profiled sheet, a concrete slab or a wooden floor
When creating a roofing cake, not a single layer can be excluded. For example, if there is no vapor barrier, then the thermal insulation material will begin to get wet, which will lead to a deterioration in its qualities. The absence of a cement screed will increase the stress on the thermal insulation, and it will also quickly lose its performance.
Features of installation of a welded roof
If you decide to independently mount the welded roof, then you will not be able to do the job well alone. In order to do everything quickly and in compliance with the technology, it is best to work three together. In extreme cases, you can get by with one assistant.
The first person uses a gas burner to heat the bottom layer on the roll material. After that, the second person rolls out the material on the roof surface, and the third person immediately after him carries out the leveling of the coating using a stitching roller. Only by following this sequence of actions can you create a high-quality coating that will protect the roof from the negative effects of external factors for a long period of time.
Features and sequence of mounting the deposited material:
- The base for laying the deposited material must be dried and pre-coated with a primer.
- Before heating the material, it must be unwound and tried on. A construction knife is used for cutting to size.
-
Using a gas burner, heat the edge of the roll and fix it in the desired place, then roll the roll.
Heating the roll with a gas burner When laying roofing material, it is necessary to simultaneously warm up both the roll and the base
- Gradually unrolling the roll, warm up its inner side and apply it to the roof surface. The burner flame must be directed both at the roof surface and at the bottom of the roll in order to simultaneously melt both surfaces.
- Smooth the surface well and roll it in with a roller.
-
Check the quality of work and, if necessary, correct errors.
The device of the overlaid roof After laying the heated surface, it is rolled with a roller, then the coating will stick to the base evenly and without bubbles
In order not to spoil the quality and appearance of the overlaid roof, you cannot walk on it immediately after installation, you must give time for it to cool down
For better performance of work, you need to take a soft roller and roll out the strip from the middle to the edges. The strips are laid with an overlap to ensure the tightness of the coating. On the sides, the overlap should be 8-10 cm, and at the ends of the strips - 12-15 cm. On roll materials with coarse-grained dressing, the edges are specially underfilled for a width of 7-10 cm.
Errors during the installation of the welded roof
If you do not have the skills to perform similar work, then it is better to turn to professionals. If you have a desire and a certain skill, all the work can be done with your own hands, you just need to strictly adhere to the developed technologies.
The most common mistakes that are made during self-assembly of a welded roof:
- wrong choice of material. The roof covering must be selected taking into account the operating conditions and weather conditions in the region where the building is located;
- installation on a completely flat roof. It is recommended that the slope is at least 1 degree - this will not allow water to accumulate on the roof, and it will not seep into the coating;
- the presence of pits and depressions. The surface should not only have a minimum slope, it should also be flat;
- moisture content of the base is more than 4%. In such conditions, the material will not adhere well;
- fusing on a surface not treated with a primer. These compounds provide a high-quality primer for the surface and provide better material adhesion;
-
non-compliance with overlap. It should be both laterally and at the ends, and the transverse overlaps of adjacent strips should be displaced by at least 0.5 m;
Overlaps when laying a weld roof When laying a weld-on roof, the transverse overlaps of adjacent strips should be offset relative to each other by at least half a meter
- laying of one layer of the overlaid roof. The overlaid roof must have at least two layers, and for the first one is taken with ordinary material, and for the second, a coating with protective dressing is used;
- insufficient heating. It must be carried out until the indicator pattern located on the inner side of the strip begins to deform;
-
incorrect design of junctions. Vertical inlets on pipes, chimneys or walls must be at least 15-20 cm high;
Junction device At the junctions, it is necessary to arrange vertical overlaps, which can then be closed with an additional layer of material
- incorrect device of the drainage system, which does not allow water to quickly go off the surface.
If you do not make the described mistakes, you will be able to create a high-quality welded roof on your own, which will last at least 10-15 years.
Video: installation of a welded roof
Features of the operation of the overlaid roof
The operation of the weld-on roof provides for scheduled and unscheduled inspections so that the condition of the coating can be assessed.
- During the spring inspection, the presence and size of blisters, the tightness of the coating in its horizontal sections and at the junctions are assessed.
- In the summer, they find out the presence of cracks, bubbles and cavities. It is necessary to constantly remove emerging plants so that their roots do not destroy the coating material.
- Periodically, it is necessary to clean the surface from leaves, dirt and debris, since water will stagnate in these places. To do the work, use a broom or a wooden shovel so as not to damage the coating material. The gutter system is checked periodically to ensure that the water can drain properly.
- In winter, the roof must be cleaned of snow and ice. Fusion roof is mainly used on roofs with a slight slope, from which the snow cannot naturally fall. During such work, wooden or plastic shovels are also used, everything is done carefully so as not to damage the welded roof.
- After strong wind, rain or hail, it is advisable to carry out unscheduled inspections. This will allow you to identify damage immediately after they appear, so that you can fix everything in time. During the inspection, you should pay attention to the condition of the dressing, as this layer is destroyed over time.
Video: soft roof problems
Service life of the overlaid roof
The service life of the overlaid roof is significantly influenced by both the quality of the materials used and the technology of their installation, which must not be violated.
- If glassine, roofing felt or bikrost are used, then the service life of the overlaid roof is about 10 years.
- The use of linocrome, bikroelast or bipole can increase it to 10-15 years.
- When materials such as uniflex and ecoflex are used, the roof lasts 15-25 years.
- The use of Uniflex together with a vapor barrier increases the service life up to 25-30 years.
Repair of welded roof
Although the hardfaced roof has high performance characteristics, over time, situations arise when such a coating needs to be repaired.
During the inspections, damage can be identified that requires repair:
- cracks and ruptures of the upper layer;
- the presence of vegetation and signs of rotting of the middle layer;
- delamination of the material.
It is advisable to carry out repairs when the damage area does not exceed 40% of the entire coating, otherwise the roof must be completely changed
Local damage
Small cuts and cracks are repaired with patches.
- The surface is cleaned of debris, dusting is removed and dried.
- Bitumen is heated.
-
Install, press in and iron the patch well. The patch should cover the damage by 10-15 cm on all sides.
Local damage to the surfaced roof Local damage to the overlaid roof is eliminated by installing patches
Swelling
Bubbles form during a temperature drop when air enters the insulation layer and swells. Bubbles can also appear from the fact that the material was laid on a damp base.
To eliminate them, the following operations are performed:
- The place of the bulge is cut crosswise.
- The surface is dried, well coated with mastic and the exfoliated material is sealed.
-
A patch is installed on top.
Blister repair The swelling is cut, dried, greased with bitumen and sealed, and a patch is installed on top
Cracking
Roofing usually cracks due to the action of sunlight, as a result of which the protective dressing disappears. To carry out the repair, the surface is first cleaned of dirt, dried and a layer of mastic is applied. When it hardens, apply a second layer and immediately apply coarse dressing. You can also install a patch with a coarse-grained coating, it should overlap the damaged area by 10-15 cm. If the damaged area is large, then the entire coating will have to be replaced.
Separation of the waterproofing layer from the base
Tear-off of the web most often occurs if the base was not well cleaned of dirt and dust during installation, and also if a primer was not used during installation. The exfoliated area is cleaned of dirt and dust, dried and glued again with bitumen mastic.
Delamination at the junction
Peeling of the coating mainly occurs in those places where the welded roof is adjacent to vertical elements or a wall.
- The vertical surface is cleaned of dirt, dried and coated with a primer.
- If the wall is uneven, then it is leveled with plaster.
- Mastic is applied to the surface of the wall.
-
Roofing material is fused.
Delamination at the junction The wall is cleaned, leveled, primed and covered with mastic, then the coating is fused and fastened with dowel-nails for insurance
It is recommended to additionally use mechanical fasteners for strengthening.
Do-it-yourself installation of a welded roof is within the power of any home craftsman. To ensure good sealing in difficult places, you can not lubricate the surface with bitumen, but pour it. This solution will be more effective than even three layers of roll materials. The reliability and durability of the overlaid roof will depend on compliance with the technology of its installation, so if you are unsure of your abilities, it is better to entrust the work to professionals.
Recommended:
Membrane Roof, Including The Features Of Its Design, Operation And Repair, As Well As How To Avoid Mistakes During Installation
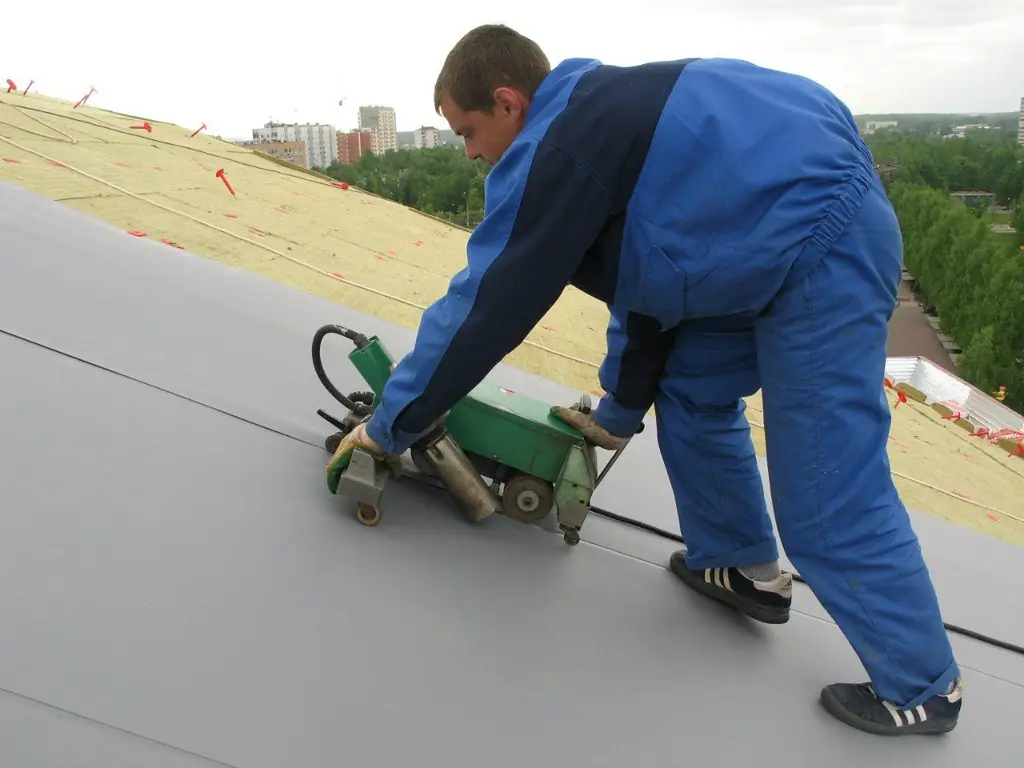
Technical characteristics, advantages and disadvantages of membrane roofing. Features of installation. Rules for the operation, maintenance and repair of a membrane roof
Roofing From A Profiled Sheet, Including The Features Of Its Design And Operation, Repair, As Well As How To Avoid Mistakes During Installation
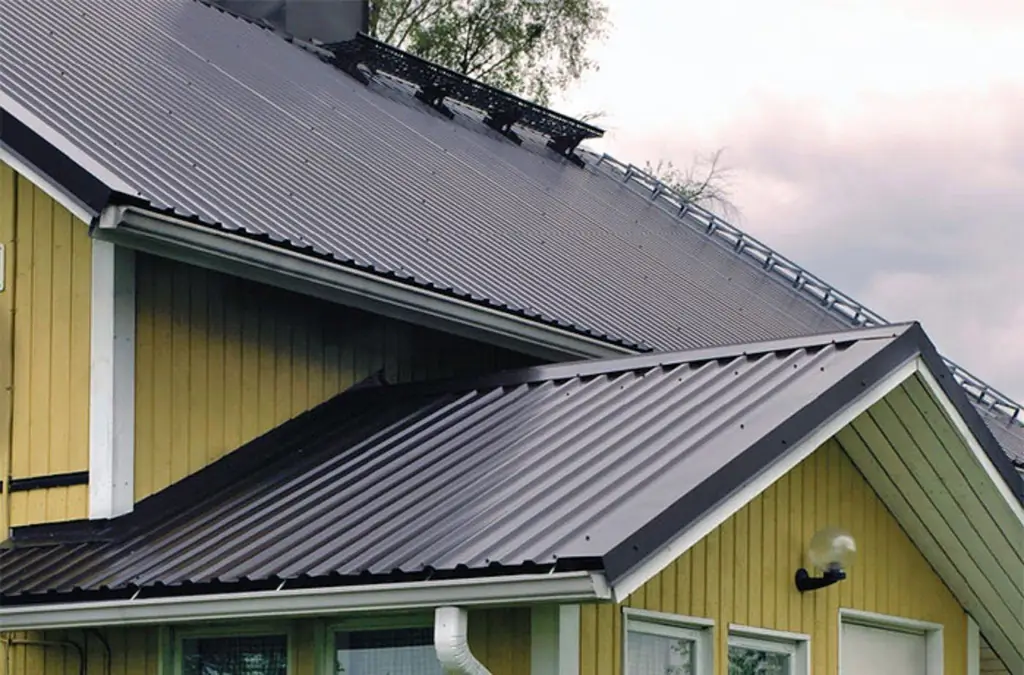
What kind of profiled sheet can be used for the roof. DIY cold and insulated roof device. What mistakes are possible. Features of operation and repair
Polycarbonate Roofing, Including The Features Of Its Construction, Operation And Repair, As Well As How To Avoid Mistakes During Installation
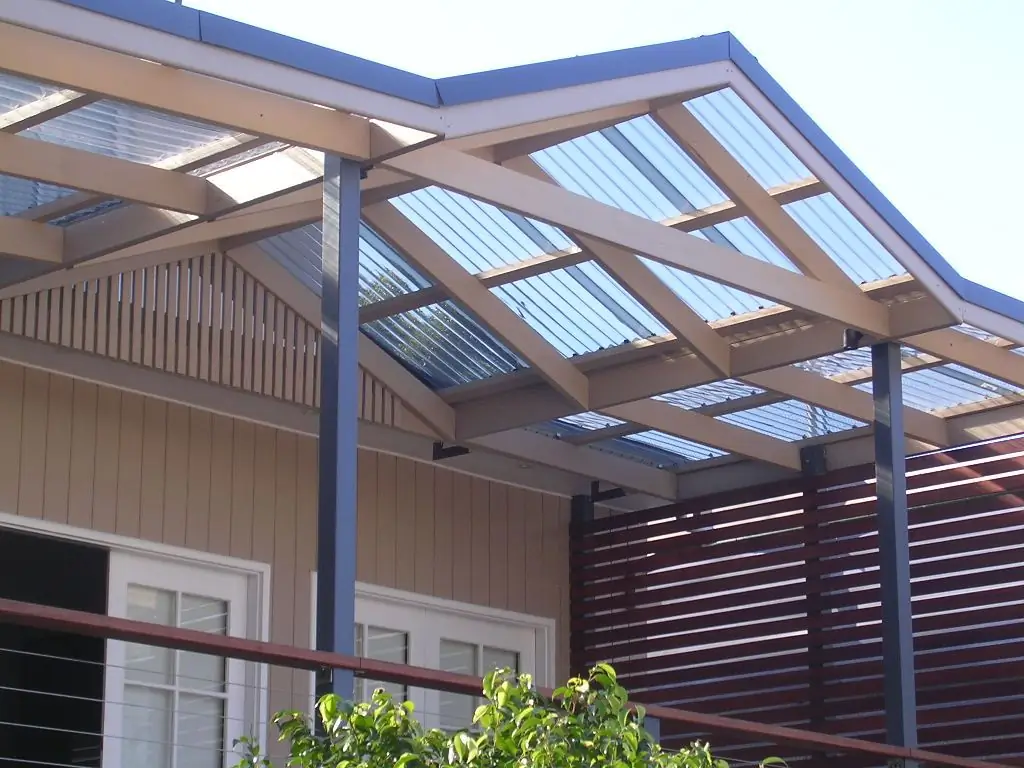
Characteristics of polycarbonate as a roofing material. How to make a polycarbonate roof with your own hands. Features of operation and repair. Photo and video
Roll Roofing, Including The Features Of Its Construction, Operation And Repair, As Well As How To Avoid Mistakes During Installation
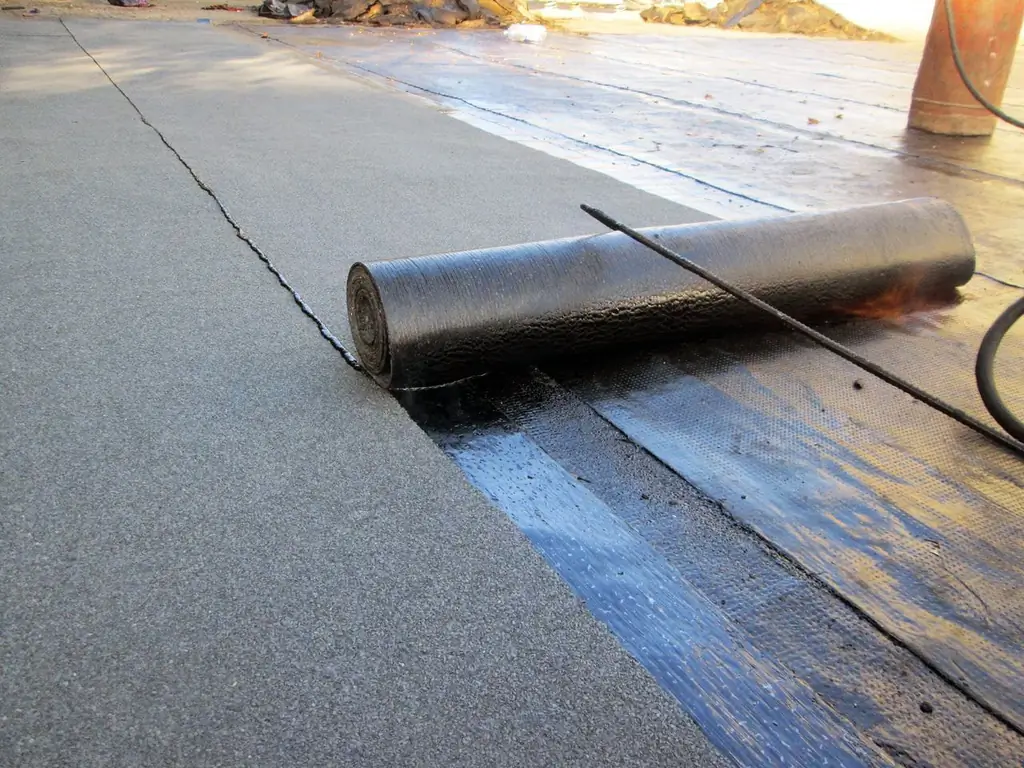
The difference between roll roofing and modern and Soviet counterparts. Can I use roll roofing on a pitched roof? How to install it and when to repair it
Seam Roofing, Including The Features Of Its Construction, Operation And Repair, As Well As How To Avoid Mistakes During Installation
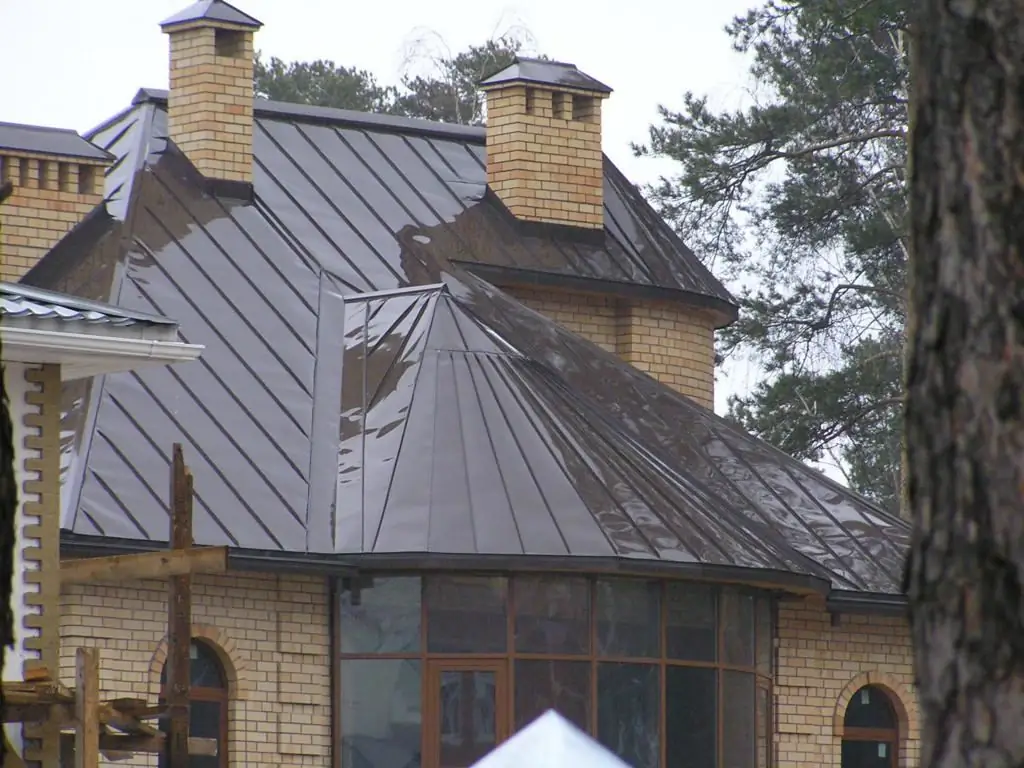
Features of the design and characteristics of the folded roof. Required tools and installation sequence. Repair and operation of seam roofing