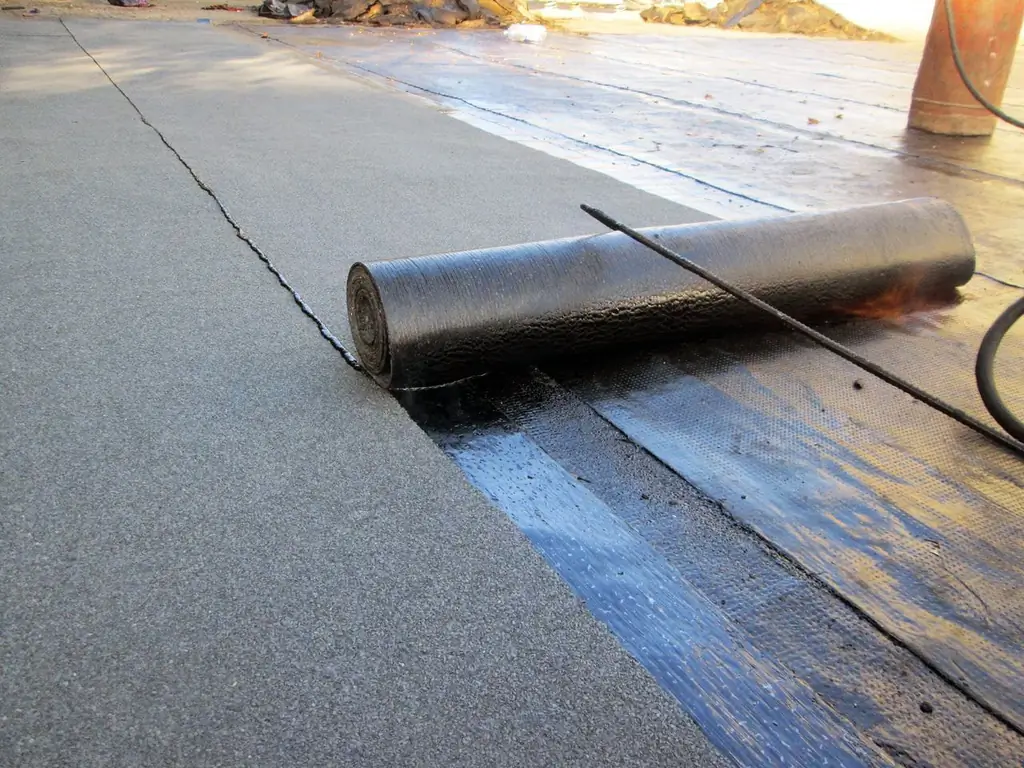
Table of contents:
2025 Author: Bailey Albertson | [email protected]. Last modified: 2025-06-01 07:32
Roll roofing: its advantages and features of use
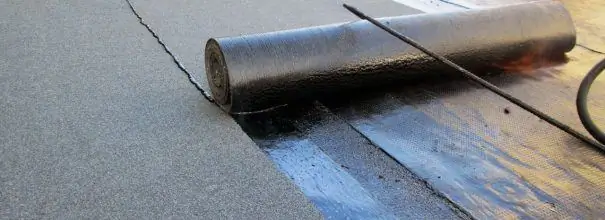
Roll roofing materials are a demanded product in the construction market, but most ordinary people are not familiar with them. After all, the main area of use for rolls is flat roofs, which are found in residential high-rise buildings, office buildings or small outbuildings. However, materials suitable for pitched roofs have recently appeared. With knowledge of a roll roof, you can organize roof repairs in OSBB, build a stylish modern summer cottage with a flat roof, or save money on arranging a gable.
Content
- 1 What is roll roofing and what are its features
-
2 Roll roofing device
-
2.1 What are roll roofing materials?
- 2.1.1 Types of euroruberoid by type of base
- 2.1.2 Table: markings of roofing material
- 2.1.3 Types of euroruberoid for polymer impregnation
- 2.1.4 Types of euroruberoid by decorative layer
-
-
3 Range of roofing roll materials
- 3.1 Table: examples and properties of polymer-bitumen coatings
- 3.2 Table: Examples and properties of bituminous coatings
- 3.3 Table: examples and properties of polymer coatings
-
4 Features of installation of a roll roof
- 4.1 Roll roofing tool
- 4.2 Installation errors
-
5 Installation instructions for roll roofing
-
5.1 Weldable roof
5.1.1 Video: hot installation of roll roofing
- 5.2 Cold installation of roll roofing
-
5.3 Installation of self-adhesive roofing on pitched roof
5.3.1 Video: installation of a roll roof on a pitched roof
-
5.4 How to mount roll roofing near vertical elements
5.4.1 Video: Application of roll roofing on vertical surfaces
-
-
6 Features of operation of roll roofing
6.1 Service life of roll roofing materials
- 7 Repair of roll roofing
What is roll roofing and what are its features
The name "roll roofing" is used due to the fact that the outer finishing layer of the roofing cake is soft and rolls up into a roll (like wallpaper). In the lower layers of such a roof, a semi-permeable membrane, moisture-proof film and insulation, for example, mineral wool, are used, so often - but not always - all elements of the roofing cake can be rolled up.
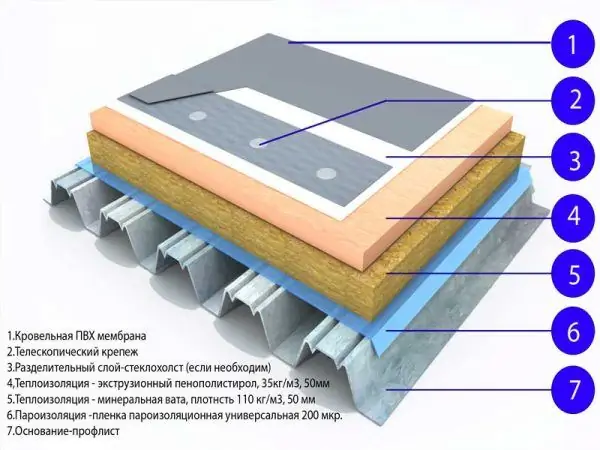
Even if insulation is used for thermal insulation in blocks, the roof still remains roll
From the features of the finish, the advantages of the roll roof follow:
- ease of installation - it is much easier to roll out a roll on a flat surface than to lay tiles and profiled sheets;
- the possibility of transportation even in a passenger car (for comparison: metal tiles cannot be brought even on the roof because of the large area of the sheets, and traditional tiles will be too heavy for a small car);
- the absence of gaps between fragments of material, in which water could accumulate - the stripes literally fuse together, forming a monolithic canvas;
- effective use of material - if the roof is of the correct shape, there are practically no scraps left;
- low load on the foundation and floors, due to the low weight of the roofing material and the absence of a complex rafter system;
- safety in repair and cleaning - it is easier to stay on a rough roof with a slight slope than on a metal tile;
- good sound insulation - thanks to the layer of insulation and the structure of the finishing material itself, the rain is not audible at all;
- heat resistance - up to 110 ° C (therefore, modern soft roofing does not melt on a hot day);
- decorative look - thanks to various mineral dressing, the roll roof looks more interesting and attractive.
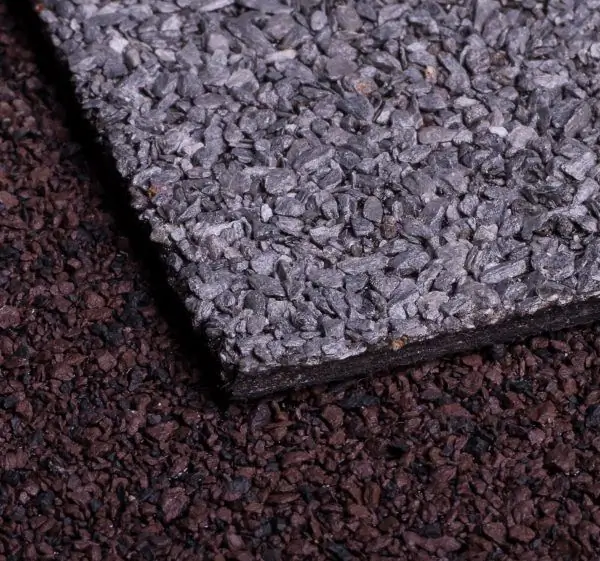
If you do not like the gray roll-up roof, you can choose the color option
But there are also disadvantages:
- when installing a weld-on roll roof, special gas burners are used, which can be dangerous if handled carelessly;
- roll materials cannot be mounted in winter, since in the cold they become fragile and roll out poorly;
- the service life of the most expensive roll roofing is 2-3 times lower than that of metal sheets (metal tiles, corrugated board).
To eliminate the shortcomings, manufacturers add modifiers to the source and cover it with armor sprinkles.
Roll roofing device
Rolled roofing, or euroruberoid (recently they began to call all types of new roll coatings based on roofing felt) consists of a base: fiberglass, fiberglass, occasionally building cardboard, two layers of polymer impregnation: bitumen with modifiers and finishing dressing: granite crumbs, slate, quartz, gabrodiabase. Thanks to this structure, it turns out to be a good waterproofing agent, dampens noise, prevents heat loss through the roof (of course, to a lesser extent than insulation).
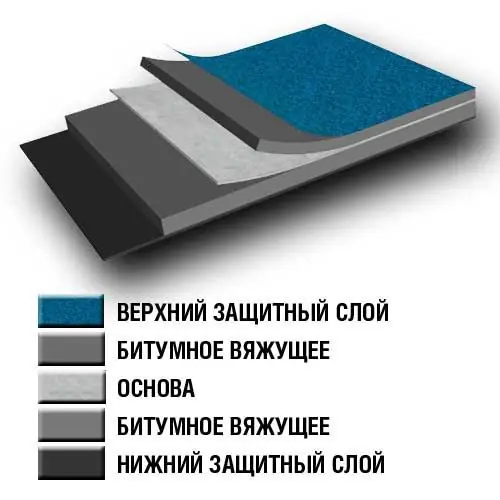
Most roofing roll materials are arranged according to the same principle, mainly only the proportions of the components differ
Roll roofing materials of this type are suitable for arranging lightweight roofs of industrial buildings and warehouses, repairing other types of roofs, as well as finishing pitched roofs. Indeed, in composition, they do not differ from the already familiar soft tiles, only thanks to the roll format they are even easier to install. And the imposition of euroruberoid on the ridge in several layers will save the junction of the slopes from leaking better than with any other type of roof. This property is especially beneficial when finishing multi-gable, hip and other types of pitched roofs with a large number of joints.
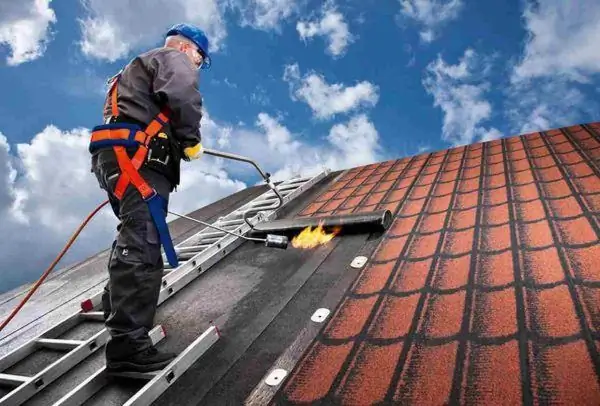
Today it is already possible to purchase a roll roofing for pitched roofs with imitation of a tile pattern
What are roll roofing materials?
Modern rolled roofing material is a composite made of synthetic canvas impregnated with modified bitumen and covered with mineral chips. The properties of various types of roll roofs differ due to the use of different elements.
Types of euroruberoid by type of base
So, as a basis, you can use:
-
fiberglass is a non-woven building material in which tangled fibers are clearly visible. Fiberglass canvas is often used to reinforce putty in interior decoration, so many people know that it tears and breaks easily. But this material is safe, resistant to the influence of water and living organisms. When combined with fiberglass, bitumen and mica chips, it forms a good roll roof. Materials based on fiberglass are the cheapest and are recommended for utility and technical buildings;
Fiberglass Glass fiber is characterized by a porous structure
-
fiberglass is a more structured analogue of fiberglass. Its threads form a tight weave, so the material is more durable. Roll-up roofing based on fiberglass is durable and reliable, but almost inelastic. If the rafter system sags in the roof or the configuration of the base changes for other reasons, the fiberglass can peel off in one piece. In such a situation, the fiberglass will break, such a defect can be quickly repaired;
Fiberglass The way of weaving threads in fiberglass gives it reliability and characteristic texture.
-
polyester is used in the form of a non-woven fabric (like fiberglass). In addition to high strength, this fabric provides elasticity to the roll roof, so it easily follows the shape of the base. Polyester-based roofing has an increased service life, but it also costs significantly more than analogues;
Polyester Despite the absence of intertwined threads, the structure of the polyester fabric is dense and uniform
-
cardboard is the traditional, but least reliable base option. It is mainly used in the production of economy class roll roofing materials.
Roofing cardboard Roofing board is slightly denser and thicker than packing board
Baseless roll roofing materials are also produced. Their lack of a reinforcing fabric is compensated by a greater thickness of material and the addition of crushed rubber. Such varieties are even more elastic than those described above, but they have less tensile strength.
Marking will help you distinguish between roll materials with different types of substrates. "E" indicates polyester (polyester), "T" - for fiberglass, "X" - for fiberglass. Letter marking also denotes the type of external and internal surface of the roll roof.
Table: roofing material markings
E | TO | P | |||
Type of base used | Top surface of material | Lower surface of material | |||
E | Polyester base | P | Film | P | Film |
T | Frame fiberglass | M | Fine-grained dressing (sand) | M | Fine-grained dressing (sand) |
X | Fiberglass | TO | Coarse-grained dressing (stone chips) | IN | Ventilated layer |
WITH | Self-adhesive layer |
Types of euroruberoid for polymer impregnation
Roll roofing materials also differ in the type of modifying additives. In the USSR, ordinary bitumen was used, but due to its low resistance to solar heat and ultraviolet light, the roof quickly "aged" and deteriorated. To avoid premature loss of properties, add to bitumen:
- artificial rubber (styrene-butadiene-styrene or SBS) - provides the elasticity of the material even at low temperatures, so the roof is not covered with microcracks while it is being cleaned of snow;
- atactic polypropylene - guarantees the heat resistance of the roll coating, so it can be used in regions with hot climates.
The amount of additives ranges from 5-25%, the more modifiers in the material, the better are the properties they add.
Types of euroruberoid on the decorative layer
The protective top layer of a roll roof can be made in the form:
-
coarse-grained dressing with a fraction of 0.6-12 mm (the size of the particles in appearance is defined as fine gravel, individual pebbles are clearly visible at arm's length). In high-quality material, the stones are sunk into bitumen half the height;
Euroruberoid texture with coarse dressing Coarse dressing forms a thick, rough protective layer
-
fine-grained dressing with a particle size like river sand. Since the grains are applied by spraying, even a good roll roof may have small bald spots;
Euroruberoid texture with fine-grained dressing Small grains of dressing require careful handling of the material
-
dusty dusting (visually noticeable color change due to a thin layer of talcum powder). This material is suitable only for the lining layer, in the upper one it will not last long even in the garage;
Euroruberoid texture with dusty dressing Roll roofing with dust-like dusting is the same on both sides of the canvas
-
flaked mica slate dressing. When crushed, all mica schists are divided not into grains of sand, but into flakes. Depending on the size and thickness of the flakes, the material can be used in both the outer and inner layers. With a small thickness, such a dressing reliably protects bitumen from damage, but mica is more fragile than gravel;
Mica Slate Plates Euroruberoid with scaly dusting should be unrolled carefully, as these thin plates are very easy to break
-
a film that easily fuses with other roll roofing materials, therefore it is suitable for the lowest layer of the roofing cake.
Roll roofing with film coating Film-coated roll roofing provides such good water resistance that it is often applied to roofs without waterproofing
When buying, keep in mind that material with coarse dusting is more heat-resistant - up to +80 ° C for two hours and durable (up to 32 kgf), but also the most expensive. Fine-grained dressing is worse adhered to the bitumen layer, but is only slightly inferior in thermal stability (+70 ° C) and tear resistance (26 kgf). Materials with dusty dressing and films are softer, but also more plastic. They should be used in the lower layers, on complex roofs with a large number of fractures, as well as where vertical roof elements meet.
Range of roofing roll materials
When buying building materials, it is often not possible to get acquainted with detailed information about their structure. Therefore, it is worth figuring out which materials belong to which type.
Table: examples and properties of polymer-bitumen coatings
Trademark | Properties | Using |
"Monoflex", "Evrotor", "Ekoflex", "Euroflam" | Fusion roll material on polyester base with modified bitumen (SBS elastomer added). Elastic, mechanically resistant, hygienic and fireproof. Frost resistance -50 ° C, temperature resistance +100 ° C. There are a wide variety of colors. Installation possible at -25 ° C. Serves 10 years. | Roof waterproofing, roof finishing for multi-storey buildings. |
"Isoplast", "Stekloizol" | Euroruberoid with a base of fiberglass, fiberglass or polyester. Protected from below with a polymer film, from above - by fine ("Isoplast-P") or large ("Isoplast K") sprinkling or slate film. It is highly flexible, tolerates heat up to +120 ° C, prevents the growth of moss and plants. Installation possible at -20 ° C. Service life - 20 years. | Thin - for waterproofing and intermediate layers (marking with EPP, HPP, EPM), thick with dusting (4.5-5 mm) - for the outer layer (EKP marker). |
"Luberit" | Fused euroruberoid with a base made of fiberglass, fiberglass or polyester. The outer layer is a dressing with a large ("Luberit K") or dust-like fraction ("Luberit P" - one-sided, "Luberit G" - two-sided). Withstands from + 80-130 ° C to -30 ° C. | Material with marker K - for the top layer, P - for the lower and middle layer, G - only waterproofing. |
Copperflex (Cooperflex) and Aluflex | Roofing rolls with a copper or aluminum top layer. It darkens noticeably over time. Service life - up to 35 years. | External finishing of a multi-layer roll roof. |
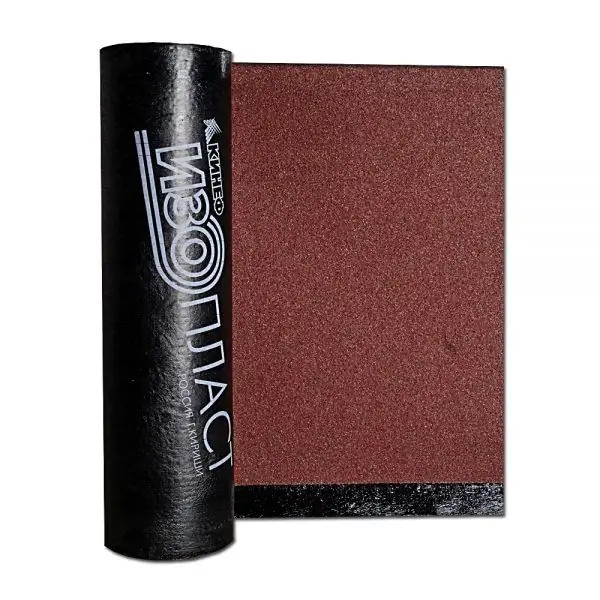
The brand name is easy to find on the back of the roll
Polymer-bitumen materials also include "Dneproflex", "Filizol", "Dnepromast", "Bikrost", "Uniflex". In terms of properties, they almost do not differ from those described above. Flexible shingles can be attributed to the same class. It is produced not in rolls, but in structure and properties it is similar to Isoplast with a fiberglass base.
Table: examples and properties of bituminous coatings
Material | Properties | Using |
Metalloizol | Bituminous material with a foil base 0.05-0.2 mm thick. More durable than counterparts with a cardboard base. Waterproofing is worse than polymer materials. The roll width is small - 20-46 cm. It quickly breaks down. | Soft roof of non-critical buildings |
Glassine | Bituminous roll material with a cardboard base. Thinner and less stable than roofing felt. | Roll roofing underlay. |
Roofing material | Traditional roll material based on cardboard and impregnated with bitumen without modifiers. The outer layer is coarse-grained sand or scaly mica, the lower layer is dust-like or fine-grained. Service life up to 7 years. Suitable only for temperate climates. | RKK - finishing of the roof of individual and auxiliary buildings, RPC - lining. |
Hydroizol | Bituminous material with an asbestos-cellulose base. Possesses increased rot resistance, waterproofs well. Installation - on hot mastic. | GI-K - for roof waterproofing. |
Tol | An analogue of roofing material, tar-impregnated cardboard. Roofing varieties have fine or coarse-grained dressing. It is mounted on hot tar mastic or roofing nails. Serves 5-7 years. | Waterproofing, upper layers of the roof of ancillary buildings. |
Mastic | Liquid waterproofing material based on bitumen or tar. Requires high or medium heat, depending on the composition. Hot mastics are prepared just before installation. | Rollless roofing, waterproofing, gluing roll materials together, repair. |
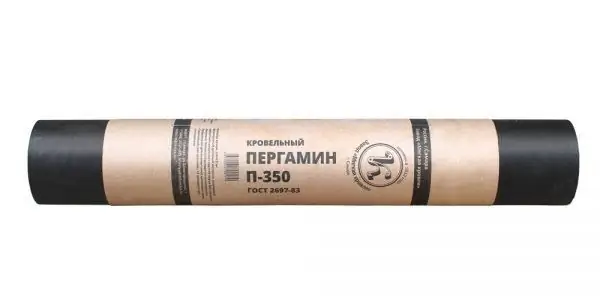
Inexpensive roll materials are usually supplied with paper labels
Practice shows that bituminous coatings are not able to compete on equal terms with polymer-bituminous ones. But there are also better materials - polymer. There is absolutely no bitumen in them, only petroleum resins and rubber. Such materials are mounted either on cold mastic or using an adhesive layer.
Table: examples and properties of polymer coatings
Trademark | Properties | Using |
"Kromel" | Elastomeric material with or without backing. It is mounted on cold mastic, an adhesive layer or mechanical fasteners. Requires a base of reinforced concrete slabs or screed. The Kromel-1RA variety is suitable for areas with aggressive climates. Resists high temperatures, UV rays, has fire-fighting properties. Lasts longer for bitumen-polymer materials. | "Kromel-1R" - all layers of the roofing cake, "Kromel-1RA" - the outer layer. |
"Polikrov" | Elastomer with fiberglass or virgin rubber backing. It is mounted only on cold mastic "Polikrov-L". The combination of these materials combines the properties of roll and bulk waterproofing: it provides a uniform layer without seams and allows vapors to escape, reliably protects the base. It lasts a long time, because only the outer protective layer ages over time. Requires a planned renovation of the varnish coating every 7-10 years to fully restore its properties. | AR-150, AR-130, R-130 are suitable for roofing in any type of building |
"Krovlelon" | Elastomer based on chlorosulfonated polyethylene (CSPE). It is resistant to ultraviolet and ozone, does not burn, it is mounted in the cold, and ensures complete moisture resistance of the roofing cake. Heat resistance 150 ° C. Service life - 20 years or more. It is more expensive than analogs. | Roofing cake in moderate to difficult climates |
Elastomeric roofing materials also include "Gidrobutil", "Roof", "Ogneizol", "Krosil", "Telkrov", "Polychrome", "Rukril". Their properties and field of application are similar to those of the trademarks described above.
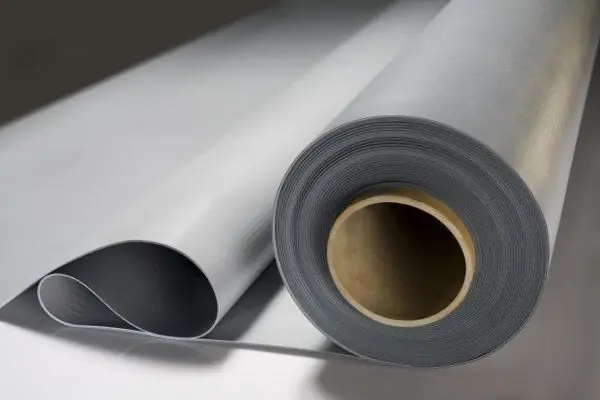
Roofing elastomers are difficult to distinguish from conventional films, so read the label carefully
When buying a roofing membrane, pay attention to the markings that indicate the chemical composition of the elastomer: BK - butyl rubber, EPDM - ethylene-propylene rubber, HSPE - chlorosulfonated polyethylene. Among them, materials with the EPDM marker are the most cold-resistant, and CSPE are the most durable.
Features of installation of a roll roof
If you decide to equip the roll roof yourself, the first step should be to choose the installation method. Depending on the type of base, the strips of euroruberoid are interconnected by fusing the polymer substrate or by bonding bitumen mastic. The first method is more reliable, but only suitable for roofs with a non-combustible base. In apartment buildings, euroruberoid is applied directly to a reinforced concrete slab, so a gas burner is used for installation.
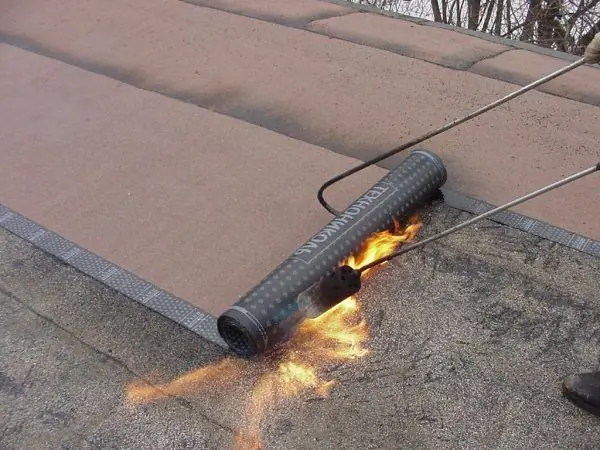
If you act carelessly, during installation, not only the base overheats, but also the edge of the already laid strip
But if the base is wooden (as in most summer cottages and outbuildings), it is better to use cold mastic, which provides setting without heating to a dangerous temperature. It is enough to warm up cold mastic to 150-160 ° C, while hot mastic requires 220 ° C and the addition of filler powders.
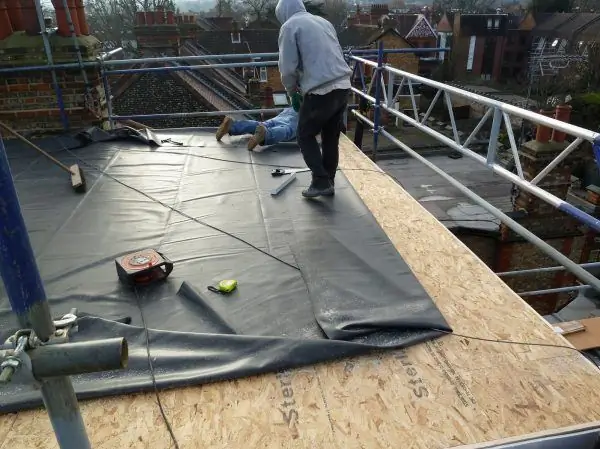
On irresponsible buildings, wooden flooring can become the basis for a roll roof
For structures with a high probability of ignition or low heat resistance, an euroruberoid on an adhesive basis is recommended. It is enough to remove the protective film from it and lay it on the base, the materials will seize due to the heat from the sun (which is why it is better to work on a hot summer day). But since with this method, micro gaps remain at the joints even during overlapping, the lower layers should be additionally sealed with mastic. Self-adhesive materials are not only the easiest to install, but also have the longest service life.
Roll roofing tool
Depending on the chosen installation method, buy or rent the necessary tools:
- gas burner (when installing a welded roof);
- talcum powder;
- a sharp knife for cutting euroruberoid;
- tape measure;
- nails and a manual or pneumatic hammer (for securing the first lining layer on the OSB base);
- a camping burner or stove for heating mastic;
- a roller for sealing seams (only needed when installing a self-adhesive Euro-roofing material);
- a mop or a wide roller for pressing the material to the base (similar to a roller or soft spatula, which are needed when gluing wallpaper).
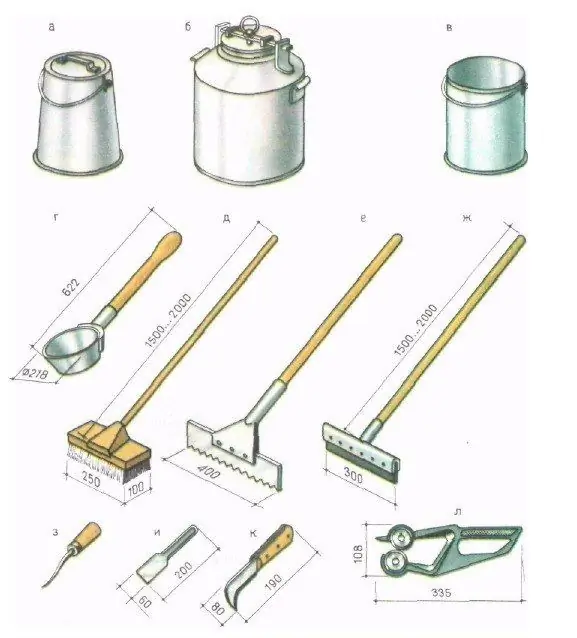
Traditional tools were used for the installation of the welded roof 50-60 years ago
Tools in the picture:
- a - a tank for heating mastic;
- b - thermos for hot mastic;
- c - a bucket for mastic (needed for transferring small portions during application);
- g - bucket for applying mastic (pouring directly from the bucket is undesirable);
- d - brush for preparation of the base;
- e - stroke to distribute the mastic;
- g - paddle with a rubber insert;
- h - awl for removing air from the blisters;
- and - a spatula;
- k - knife;
- l - Roller shears for easy cutting of materials with a solid base.
Ideally, you should have three types of materials: marked "P" - lining, "K" - roofing for the top layer and "E" - elastic for bypassing pipes and protrusions on the roof. They may differ in the way of installation, pay attention to this when choosing a tool.
Installation errors
If you have little experience in handling euroruberoid, these tips will help prevent annoying mistakes.
-
A common cause of problems is an insufficient number of roll roofing layers. For a roof with a slope of over 15%, 2 layers are required, at 5-14% - 3 layers, and at 0-4% - at least 4 layers. That is, the smaller the slope of the roof, the higher the likelihood of water stagnation and the greater the need for reliable waterproofing. In addition, under mechanical loads (eg hail) the impact force into a flat roof is also greater.
Correct roll roofing cake on a concrete base Before starting the installation of the roll roof on the roof, the correct pie must be arranged
- The main secret of installing a weld-on roll roofing is careful handling of the gas burner. The material must be heated so that it melts and adheres firmly, but does not start to smoke or burn. It is necessary to underheat - and the roof will peel off over time, if it is overheated - the material will quickly "age" and you will have to make a patch. Therefore, either invite the masters, or before a responsible mission, practice at a less significant object - a shed or garage.
- The use of a roll coating in the lower layers without sprinkling is not an attempt to save money, but a technology requirement. Otherwise, the thickness of the lower melted film will not be enough to fill the pores between the stones, which is why the layers will not adhere well to each other. Therefore, even if you have scraps from the previous roof, the sprinkled fragments cannot be used in the lower layers of the roll roof.
- When rolling out a roll, pay attention to the presence of talc, many manufacturers use it so that the layers of euroruberoid do not stick together during storage and transportation. During installation, it should be removed with a vacuum cleaner, a broom or a brush, otherwise talcum powder will not allow creating a monolithic layer on the surface of the roofing surface
- Laying roofing material directly on top of the insulation is permissible only for hangars, where the weight of the structure is especially important. This cannot be done in a residential building, this reduces the service life of the heat insulator. In a cottage with a flat roof, the insulation should be protected and a screed should be made over it, which will become the basis for the Euro-roofing material. On a house with a pitched roof, the OSB structure should be sheathed or moisture-resistant plywood (preparation is similar to installing soft tiles).
-
The joints of the material in different layers should in no case coincide. That is, it is better to lay the canvases on a flat roof according to the scheme: along, along with an offset relative to the first layer, along with an offset relative to the second layer, etc. This rule should be followed, even if it increases the consumption of material. You need to start from the lowest place, determining it by level.
Layout scheme for welded roll roofing Layer joints must not match
- The correct choice of the direction of laying the bales on the pitched roof affects the durability of the coating. On a roof with a slope of 15-25 °, all layers should be perpendicular to the ridge, at less than 15 ° - parallel. The mismatch of the joints is provided by offsets.
- The size of the overlap is determined by the type of roof according to the rule: the greater the slope, the less overlap. On a roof with a slope of more than 5 °, the canvases of the inner layers are superimposed by 7-8 cm, and the outer ones by 10-15 cm. On a flat roof, the overlap is stable - 10 cm.
- It is forbidden to arrange layers perpendicular to each other by the rules for installing roll roofing materials.
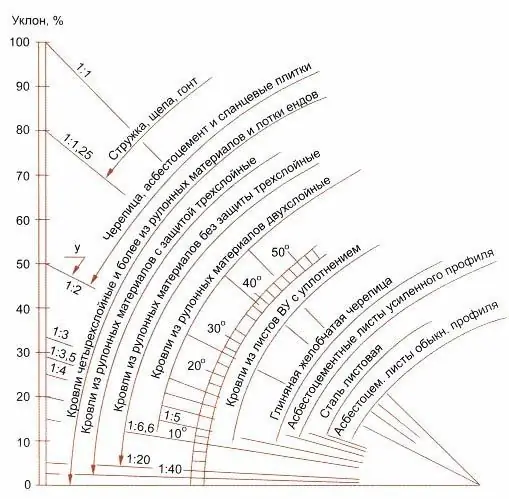
Roll roofing materials can only be used on roofs with a certain slope.
Installation instructions for roll roofing
Installation should be started after thorough preparation of the base. It should be even (without grooves and mounds), solid (crate is not allowed as for rigid materials) and strong (not to bend under load). In pitched roofs, the base is usually OSB or plywood boards, in hangars - profiled metal, in multi-storey buildings - reinforced concrete slabs.
Before laying, you also need to equip the base waterproofing. In garages and other small buildings, it may not be done, but in more critical buildings it is mandatory, as it helps to increase the resistance of the roof to water penetration. Reinforced concrete products are usually insulated with mastic by spraying or simply with a brush. When dry, it creates a dense monolithic film similar to rubber. For other types of substrates, a non-woven membrane or polymer film is more suitable.
The last stage of preparation is checking the material. Roll out the roll you plan to work with and make sure it is intact, in accordance with the color and markings.
Surfacing roof
The deposited roll roofing is laid as follows:
-
If you have not completely waterproofed the base, you should at least treat the joints with a special sealant. Those who want to save money can use the "old-fashioned" method. Cut strips 15 cm wide from the roll and glue them in the direction of the material laying with a distance of the width of the roll. This is a waterproofing of the seams, in the future, the rolled roof should be rolled out so that the orientation strip falls exactly on the joint of the canvases. You need to glue with bituminous mastic.
Waterproofing joints It is much easier to apply the sealant with a brush than to glue the strip roofing
-
Select the lowest point on the roof and start from there. Heat the edge of the roll with a burner, orient it correctly and press it to the base. Roll out the roll and make sure it is not skewed. After that, roll up the material and start securing.
Unrolling the roll during preparation If the size of the roof allows, you can roll out several rolls for getting used to
-
Heat the ends and the bottom of the blade with a burner. If everything is done correctly, a roll of molten bitumen 2 cm in size should form in front of it and on the sides. It is better to work with three people: the first one heats the canvas, the second rolls it out with a hook, the third rolls the roll with a roller while the bitumen is hot. Especially carefully it is necessary to warm up and roll the edges of the roll. The movement of the roller should be from the middle to the edges and at an angle to expel any air bubbles.
Rolling with a roller of a roll of welded roof Sometimes one person does the heating and rolling, but it is better to separate these responsibilities.
-
Check the quality of the work after unrolling the roof over the entire length of the roof. If swelling or peeling appears at the seams, you need to heat up the material and roll it again. Lay the next layer with an overlap of 10 cm in length and 15 cm in the end to reliably cover all seams.
Hot rolling the second layer Please note - the seams are immediately insulated with molten bitumen
-
Proceed as described above until you reach the parapet. Here you need to cut out a fragment of a suitable length and attach it to the parapet with nails, staples or other mechanical means. After that, the material must be heated and rolled.
We weld the roof to the vertical Make sure that the material laid on the wall is placed strictly vertically
-
In the same way, lay another 2-3 layers of rolled roofing, not forgetting about the displacement of the seams. With the top, be especially careful not to damage or smoke the decorative dressing.
Rolling out the second layer of the overlaid roof Watch the overlap carefully - it should be even
Video: hot installation of roll roofing
Cold installation of roll roofing
The technology of laying a non-melted roof has some peculiarities.
-
First, roll out the rolls and leave them unfolded to get used to. If there is no time, just roll out the roll and roll it again.
Unrolled rolls The pre-straightened material fits better on a flat horizontal surface, creases appear on it less often
-
Roll out the first roll to the middle and make sure its position and dimensions are correct. After checking, roll it in the opposite direction to make two interconnected rolls.
Rolling in two rollers The method of rolling "from the center to the sides" is used for the installation of euroruberoid both cold and hot
-
Apply mastic to the future location of the canvas and roll out the roll roofing. Up to 1.5 m 2 of surface can be processed in one step. After rolling, apply a roller to the surface.
Roller A roller for rolling in euroruberoid can be made independently
The rest of the action does not differ from the hot method.
Laying a roof with a self-adhesive base on a pitched roof
If the installation of a roll roof is carried out on a pitched roof, proceed as follows:
-
First, calculate the slope of the roof and determine the orientation of the canvases. Recall that up to 15% of the roll is rolled along the ridge, after 15% - across.
We calculate the angle of inclination of the roof A simple diagram will help you quickly determine the exact angle of your slope
-
Spread the first panel at the bottom of the roof so that the bypass to the cornice overhang is 13-15 cm. Cover it and roll the material with a roller so that the adhesive base is firmly pressed against the OSB.
First layer on OSB The construction stapler will help to quickly fix the euroruberoid on the OSB
-
Place the next layer higher with an overlap of 10 cm. Repeat the operation until you reach the ridge. The overlap on it should be from 25 cm.
Rolling rolls over the ridge With a large length and width of the roof, the rolls can be built up with butt ends
-
Process the second ramp using the same technology. Fix the overhangs on the eaves with clamping strips.
Edge rail Euroruberoid is recommended to be pressed with aluminum edge strips
If the roof is steeper, the first roll is rolled down from the ridge (taking into account 25 cm for the overlap) and all subsequent layers are placed vertically. Different slopes are processed in turn; it is not worth overlapping the entire roof.
Video: installation of a roll roof on a pitched roof
How to mount roll roofing near vertical elements
Since these places are the most difficult, especially for beginners, it is worth dwelling on them in more detail. If you do not pay due attention to the abutments to the vertical surfaces, water will begin to flow under them and not only the rolled roof will collapse, but also the base itself.
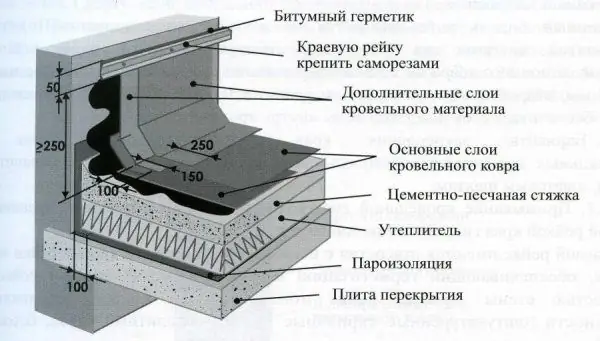
Joints of rolled roofing to vertical surfaces require special attention
We recommend that you proceed as follows:
-
Cut a piece of material of such a width to ensure a vertical rise of 25 cm. Fix it mechanically on top (with staples, nails, screws), and glue the rest to the base, trying not to round the corner too much.
Sawing a roll If you need to process a parapet, and not a protruding pipe, it is easier to saw off a piece of a roll of the required width
-
Make the second fragment wider, it should overlap the vertical by 35 cm. Attach it and roll the upper part (5 cm) into a roller and attach it to the vertical wall of the chimney or at the top of the parapet through the clamping bar. Glue the rest to the base on top of the first layer.
Apron installation When fixing roofing material on the parapet, keep in mind that on top of it you will still need to tightly fasten the apron
-
Seal all seams with mastic or warm up and roll the material.
Sealing seams at the junction of the rolled roof There should be no visible gap, seal carefully
For each layer of the main roll roofing, there should be two layers of connecting patches at the points of abutment to the vertical elements of the roof.
Video: applying roll roofing to vertical surfaces
Features of the operation of roll roofing
To increase the service life of a roll roof, it is recommended to adhere to a number of rules:
- after complete installation, no debris should remain on the roof. The remains of building materials are gradually sunk into the soft roof and destroy it;
- do not walk on the finished roll roof on hot days. This cannot critically damage modern material, but you can break the protective coating and it will become uneven. If you find a "bald spot", you need to restore the dressing with small stones and cold mastic;
- in autumn, during the period of leaf fall, you should monitor the condition of the drain funnels, otherwise the accumulation of wet leaves will reduce the service life of this unit. The rule only applies to houses with flat roofs;
- do not clean snow and ice with metal tools. Even with careful handling, they will inevitably damage the top layer of the roof. In addition, some of the snow should remain on the roof, it serves as additional protection for the roofing material. Cleaning is carried out only when the amount of precipitation exceeds the permissible load;
- the heating cable in the gutters will help to increase the service life of the roll roof, since the main damage due to cleaning from ice or stagnant water occurs precisely in these places. Heating will prevent the formation of ice and prevent destruction. But if not, it should be cleaned here regularly and with the utmost care.
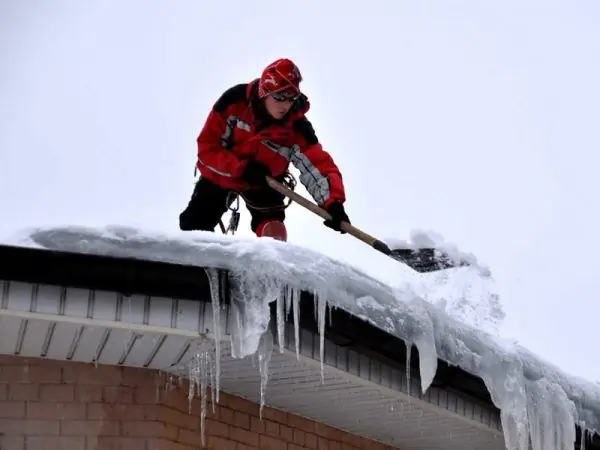
When cleaning the roof, use a plastic shovel and a safety rope
Service life of roll roofing materials
Roll roofing - economy class material. Considering this, one should not expect the same service life from it as from polymer sand tiles. The best representatives of roll materials are able to last up to 30 years without the need for repairs (unless extraordinary circumstances occur). Correct installation is also very important - if it is done by specialists in compliance with all the rules, even an inexpensive roll roof will last 10 years. It is believed that the lifespan of a glass-ruberoid is 12-15 years, while a polyester-based roll roof “lives” for 20-25 years. In the area of housing and communal services, the planned repairs of rolled roofing begin 26-27 years after installation.
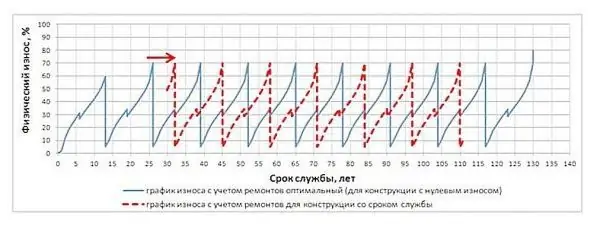
The approximate degree of wear of the roll roofing depends on the time and the repairs
It is important to understand that statistics and calculations of the operating period do not take into account the possibility of fire, storms with abnormally strong winds and similar disasters. Even from materials with increased weather resistance and thermal stability, one should not expect miracles.
Since the climatic conditions in our country are far from ideal, the need for a major overhaul of a roll roof may arise within 10-15 years after its installation. Therefore, the condition of the roof should be assessed from time to time. Examine the surface for:
- softening the mastic at the joints;
- the appearance of blisters, which can indicate the separation of the roof or the separation of all layers from the base;
- breaks or cracks in the top layer of the coating;
- vegetation (lichens, blades of grass), which can tell about decay of the middle layers of the roof.
You can learn more about routine seasonal inspections of rolled roofs from the Operation and Repair Manual for housing and communal services workers. If inspections and scheduled repairs are carried out regularly, a complete replacement of the roofing cake will not take 50 years or more.
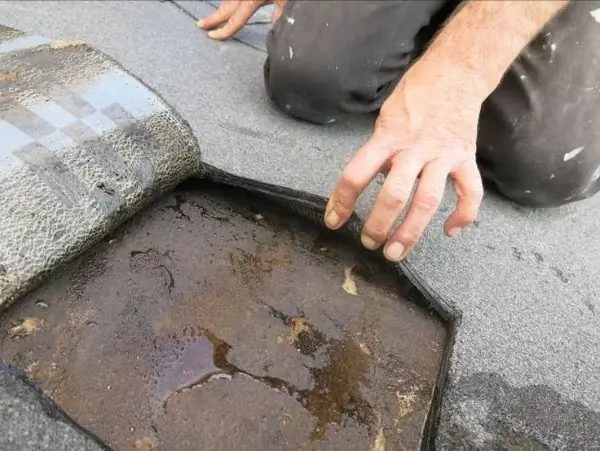
Even a small crack on the upper layer of a roll roof leads to wetting and destruction of the lower layers, so sometimes you have to open the roofing pie to assess the situation
Everything here is like in medicine - the sooner you find the disorder, the easier it will be to fix it. In any case, you will have to remove the layer of roofing material to the level of the intact layer (in difficult cases - to the membrane or even the base), if necessary, replace the insulation and restore all layers of the soft coating, carefully melting the roof joint and patch. The operations are the same as for editing, only smaller scale.
Roll roof repair
Depending on the globality of the problems, there are:
- planned repair of a rolled roof (damage takes up to 40% of the roof);
- overhaul of the rolled roof (more than 40% of the roof is damaged).
Bulges and small cracks are treated with patches. It is necessary to completely cut out the damaged fragment of the roof, clean and dry the base. After that, a patch is glued to the mastic, exactly overlapping the cut out fragment. It must be additionally secured with nails or a bar. At the end, the repair site is covered with a larger finishing patch, it is enough to glue it with mastic.
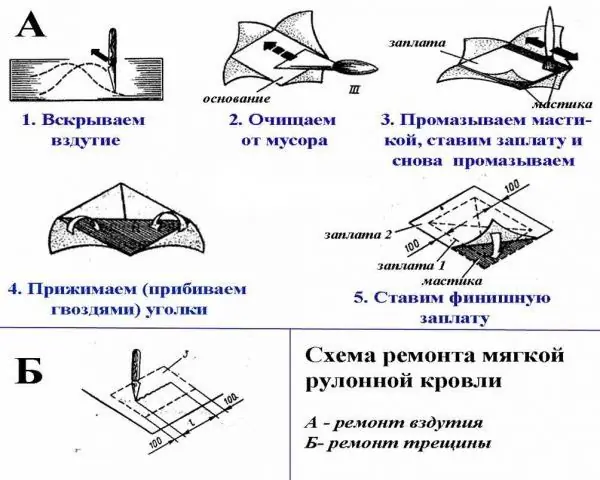
The patching method is suitable even for beginner craftsmen
This technique allows you to effectively repair the roof with a minimum of tools and materials. But if the crack is long, you will have to spend more effort and remove the whole strip. It is better to burn such an area with a burner in order to further dry the base and provide better adhesion. When working with a large layer, the procedure is the same as when laying a new roll cover. If you need to ensure a consistent appearance, you will have to lift the edge of an adjacent whole sheet in order to hide the mounting tape of a new roll under it. The photo shows that on one side of the roll, the sprinkling does not reach the edge, this tape should be placed under the adjacent strip.
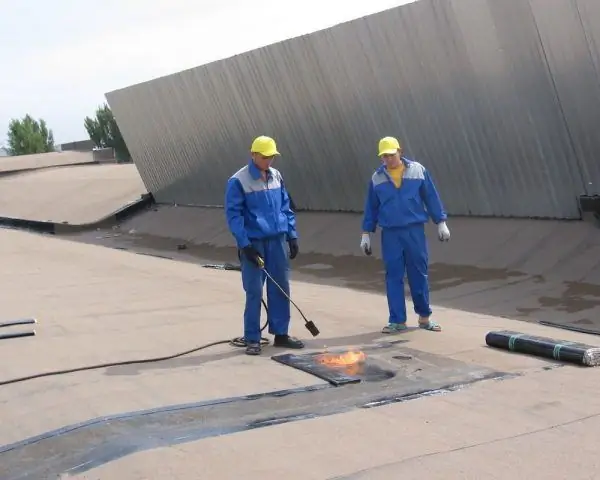
If the damage is on the same canvas, it is more advisable to replace it completely, rather than making patches
It may seem that the maintenance of a roll roof is costly, but in fact, the planned repair of a roof with any other coating (except for shingles) will be much more difficult and expensive. Therefore, in this aspect, the roll roof is not inferior to traditional roofing materials.
Recommended:
The Welded Roof, Including The Features Of Its Construction, Operation And Repair, As Well As How To Avoid Mistakes During Installation
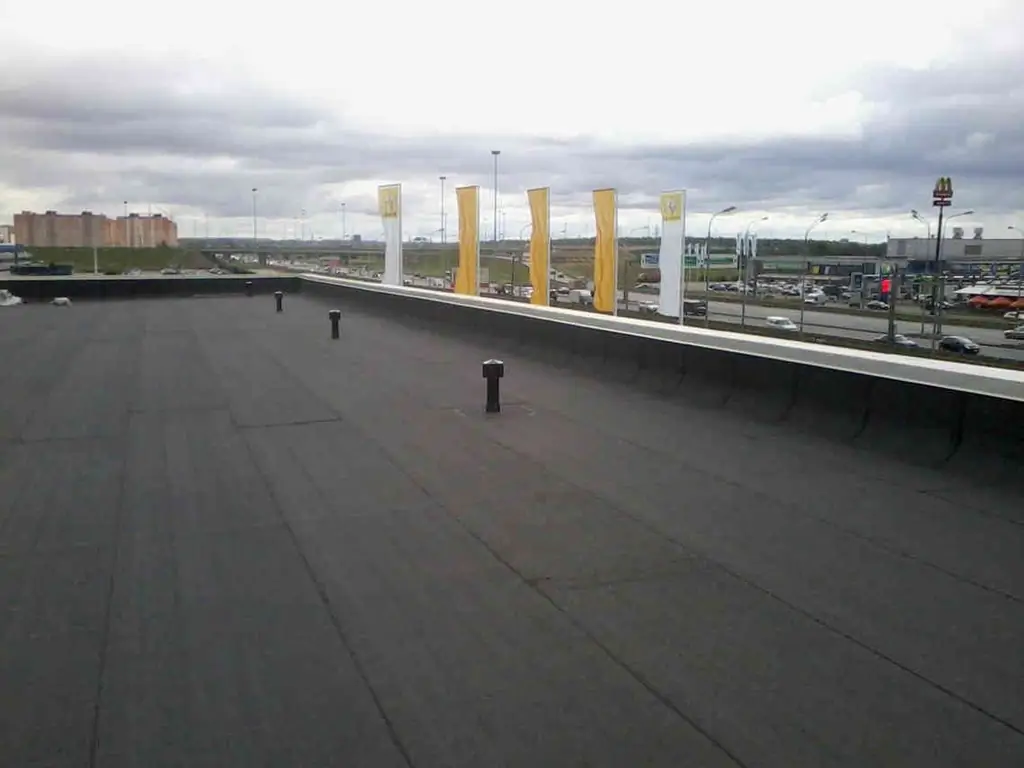
The main features and characteristics of the overlaid roof. Materials and tools required for the job. Installation, operation and repair of the overlaid roof
Roofing From A Profiled Sheet, Including The Features Of Its Design And Operation, Repair, As Well As How To Avoid Mistakes During Installation
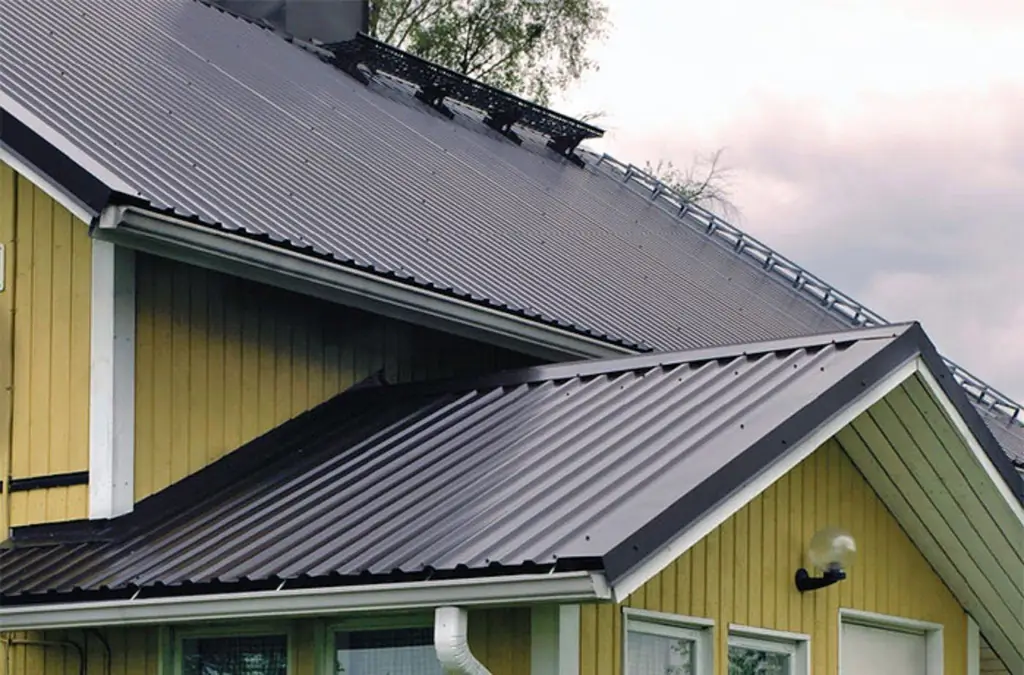
What kind of profiled sheet can be used for the roof. DIY cold and insulated roof device. What mistakes are possible. Features of operation and repair
Polycarbonate Roofing, Including The Features Of Its Construction, Operation And Repair, As Well As How To Avoid Mistakes During Installation
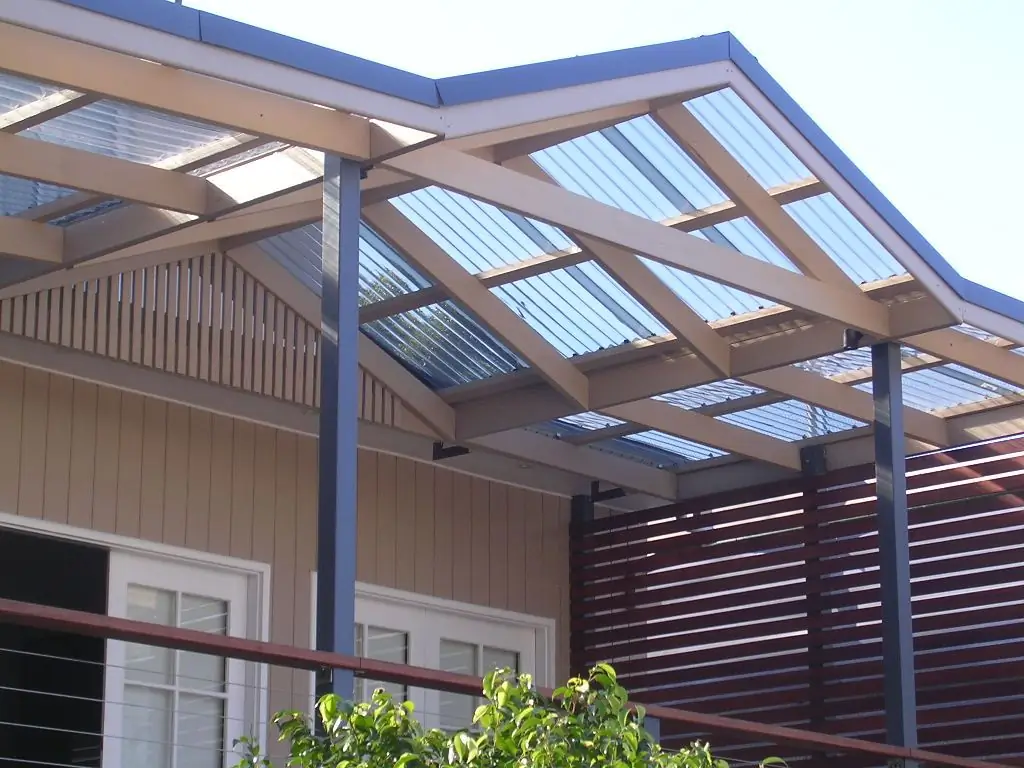
Characteristics of polycarbonate as a roofing material. How to make a polycarbonate roof with your own hands. Features of operation and repair. Photo and video
Roofing Made Of Corrugated Board, Including The Features Of Its Design And Operation, Repair, As Well As How To Avoid Mistakes During Installation
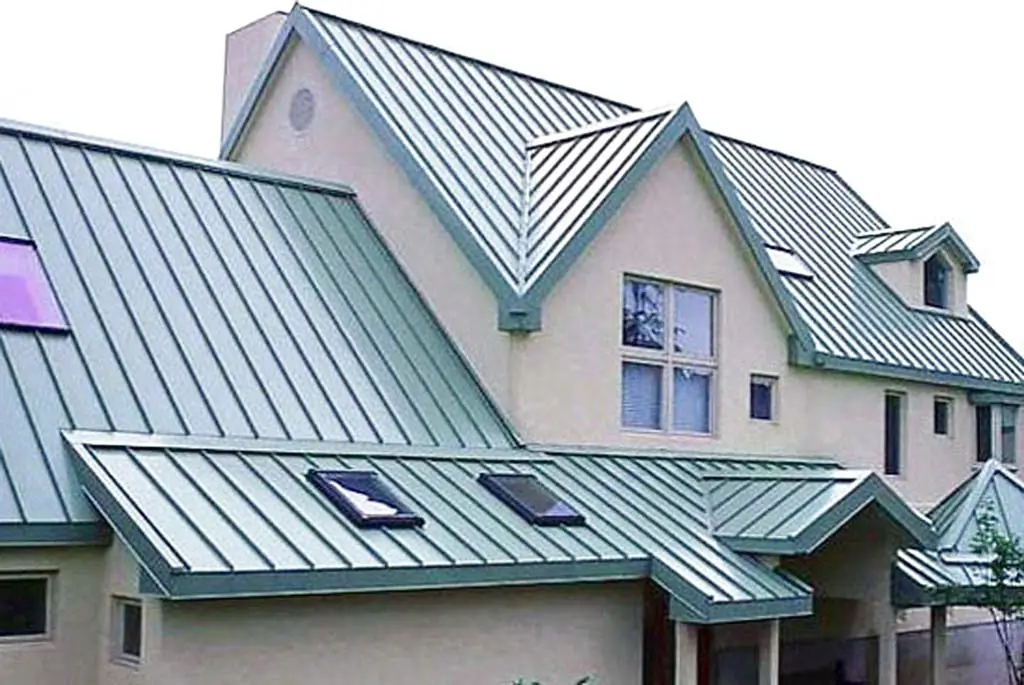
Features and characteristics of corrugated roofing. Types of roofing sheeting. Calculation of the amount of material for the roof. Features of installation and operation
Seam Roofing, Including The Features Of Its Construction, Operation And Repair, As Well As How To Avoid Mistakes During Installation
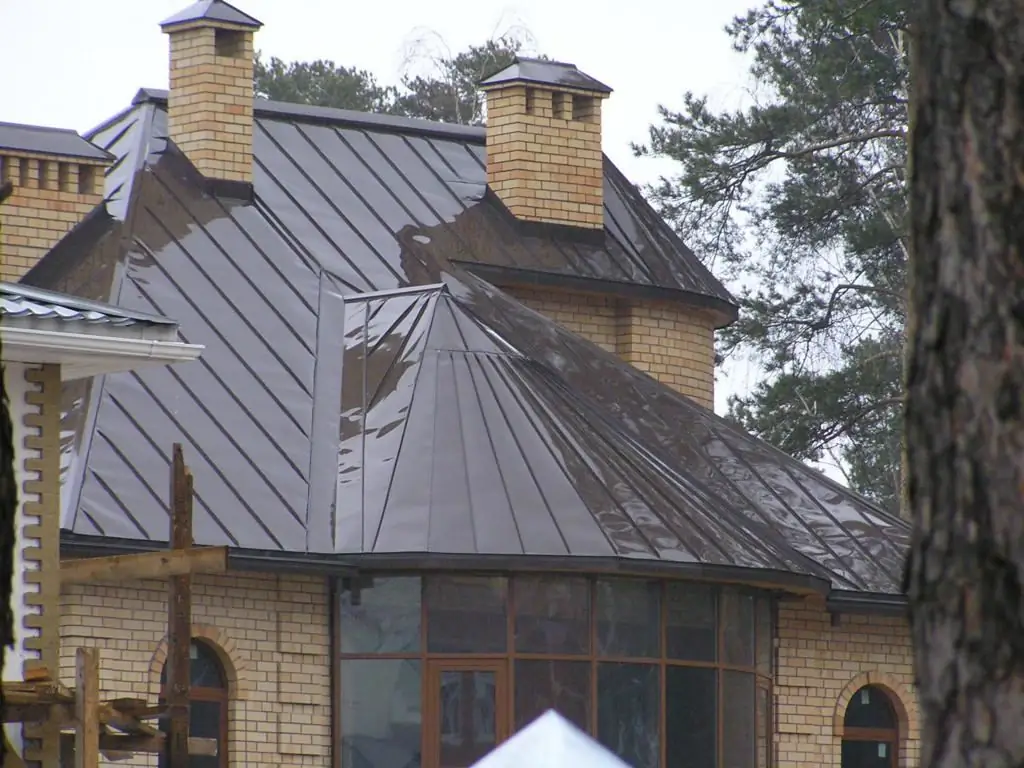
Features of the design and characteristics of the folded roof. Required tools and installation sequence. Repair and operation of seam roofing