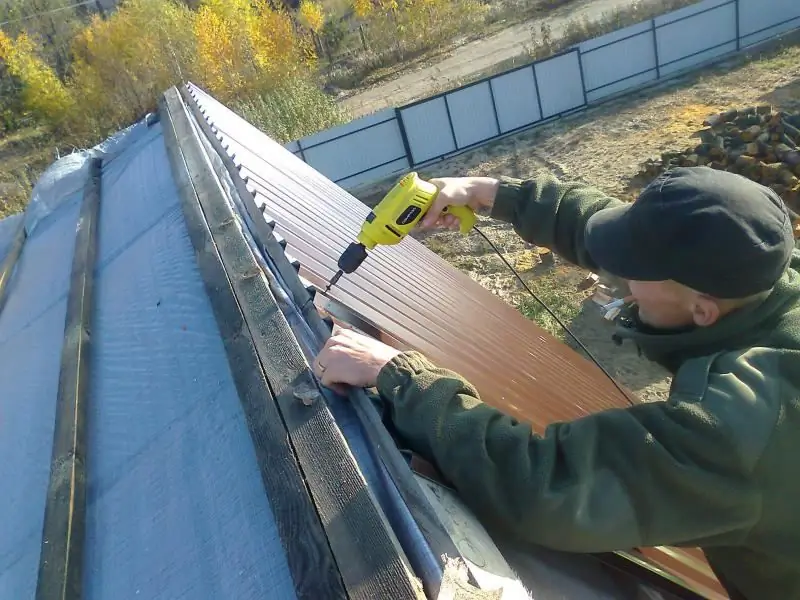
Table of contents:
2025 Author: Bailey Albertson | [email protected]. Last modified: 2025-06-01 07:32
We independently make a reliable roof from corrugated board on a wooden crate
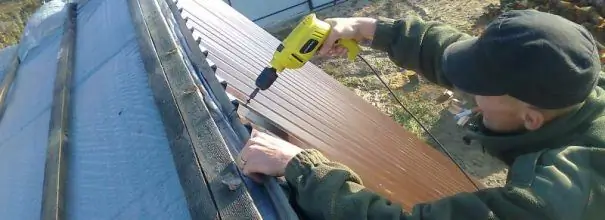
Roofing in a country house is a decisive moment in its construction. Well-designed, it can extend the life cycle of a building up to 50 years or more, and mistakes in manufacturing can negate all efforts and investments. The most reliable and easiest to manufacture are corrugated roofs.
Content
-
1 Roof structure made of corrugated board
- 1.1 Crate
-
1.2 Counter grill
1.2.1 Video: sheathing for corrugated board
-
1.3 Waterproofing
- 1.3.1 Roll waterproofing
- 1.3.2 Roof insulation mastic
- 1.3.3 Foil insulating materials
- 1.3.4 Photo Gallery: Film materials for waterproofing
- 1.3.5 Diffusion materials
- 1.3.6 Vapor barrier materials
-
1.4 Thermal insulation of the roof
1.4.1 Video: Pitched roof insulation
- 1.5 Profiled sheet
-
2 Fastening sheets of corrugated board
2.1 Video: installation of roofing from corrugated board
Corrugated roof structure
The roof structure is based on the rafter system. It is on it that the roofing cake is formed, which performs the following functions:
- Protection of the building from precipitation and wind.
- Conservation of heat in the under-roof space. According to experts, they can be up to 20-25% of that received from the heating system. The costs incurred during roof insulation are quickly compensated by energy savings.
- The possibility of using the insulated under-roof space to organize additional attic-type living space.
To achieve these goals, a roofing cake is created from several layers of various materials.
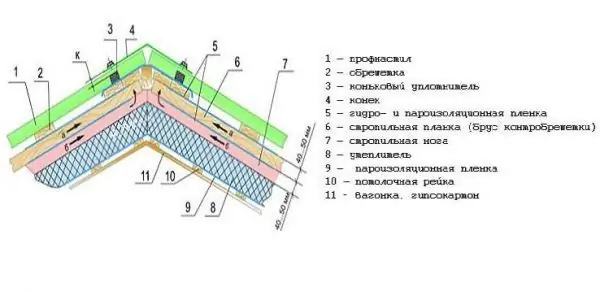
When installing a roofing cake, it is important to ensure that there is a ventilation gap between the waterproofing film and the roofing
Lathing
It serves as a supporting surface for the topcoat. To ensure air circulation in the under-roof space, a counter-lattice is stuffed along the rafter legs, creating a ventilation gap between the rafters and the roof covering.
Most often, the material for the lathing is a board measuring 25x100 mm, edged or unedged. When installing unedged timber, it must first be sanded. You should beware of using a wider board, because when the temperature and humidity in the under-roof space change, it is subject to warping. The result can be a swelling of the topcoat and damage to the adjoining layers of the roofing cake.
Under the profiled sheet flooring, the crate is stuffed with a different pitch of the boards, depending on the slope of the slopes:
- On roofs with an inclination of up to 10 degrees, a gap between the boards of up to 5 cm is allowed.
- On slopes up to 30 degrees, the gap can be up to 45 cm.
- Roof slopes of 45 degrees or more allow the sheathing step to be 60-70 cm.
2-3 upper boards of each slope under the ridge space are installed close to each other
The lathing is stuffed over the waterproofing film, reinforced on the rafters with counter-lattice strips. The distance between the boards is set using special spacers made of wood trim. Fastening the battens to the counter battens is done with two nails at each intersection. This method of fixing increases the strength of the rafter system.
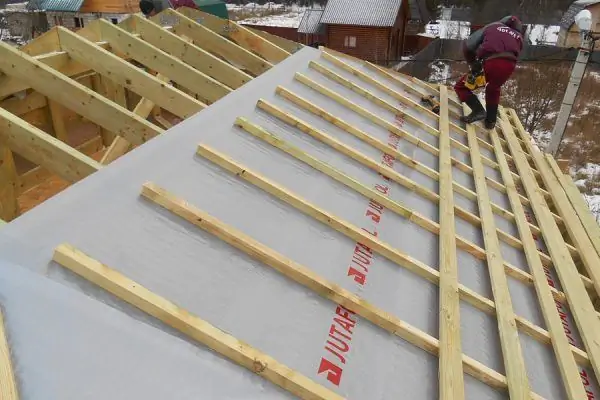
The lathing is mounted on top of the waterproofing and counter-lattice, fixing it at each intersection with two nails
Counter grill
As mentioned above, this roof element creates an air gap between the topcoat of the roof and the waterproofing film. If this condition is not met, condensation remains under the roofing material, saturates wooden parts, contributing to the development of fungal infections and wood decay. In this case, soon after the installation of the roof, urgent repairs may be necessary with a complete replacement of the roof system of the house.
Before installing the counter grill on the rafter, you need to pull the moisture-proof film. Counter-lattice elements are stuffed onto each rafter leg over the foil. For it, bars with a size of 25x50 mm are used, and with a large roof plane - 40x50 mm. There is no need to use large material, this leads to a heavier structure and an increase in financial costs. In addition to creating a ventilation gap, the installation of a counter grill allows workers to move more easily along the roof and evenly, without distortions, pull the moisture-proof film.
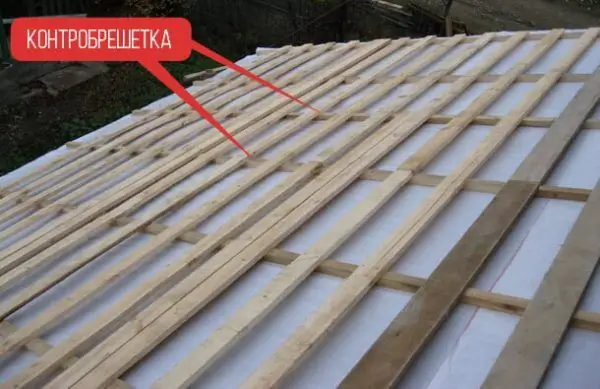
The counter lattice is laid in horizontal rows and is attached to the rafter legs, firmly fixing the waterproofing film
The bars of the counter-lattice are attached to the rafter legs with nails at least 70 mm long with a step of about 20 cm. It is allowed to leave gaps between individual bars, depending on the type of finish coating. The counter lattice can be installed on any insulating materials, including membranes, roofing felt, etc. It is suitable for all types of topcoats, including corrugated board, ondulin, metal tiles, etc.
Video: sheathing for corrugated board
Waterproofing
The purpose of the roof is to protect the internal space of the building from the effects of adverse environmental factors. One of them is water that falls out in the form of precipitation and comes as condensation from the topcoat. This task is solved not only by the selection of high-quality roofing material, but also by the installation of a waterproofing layer in the roofing cake.
For this, various types of materials are used:
- Rolled. These include the well-known roofing material, as well as a number of modern products of this type.
- Coating. These materials are represented by various types of bituminous mastics.
- Film. The most common type of waterproofing materials, especially in individual construction. The attractive side is the low price in comparison with other products of a similar purpose.
- Diffusion. Relatively new and the most expensive material. The difference is the ability to pass moisture in only one direction, which allows the roofing cake to be drained during operation.
Roll waterproofing
On the construction market they are represented by a variety of types:
- roofing felt made from impregnated cardboard;
-
stekloizol - based on fiberglass;
Stekloizol Stekloizol is a modern analogue of roofing material, produced on the basis of fiberglass or fiberglass
- euroruberoid and many others.
The main advantages of rolled insulation include:
- Low cost.
- High reliability.
- Sufficient durability. The service life of such material is up to 15 years. In places of wear, it is not necessary to dismantle it; it is enough to lay several layers of new coating over the old roof.
The disadvantage of roofing material is the relative complexity of installation associated with the use of bitumen mastic. But if you use a euro- or glass-ruberoid, this need disappears, it is enough just to heat the lower surface of the material with a gas burner. The result is a reliable attachment to the roof, completely eliminating the possibility of leaks.
Roof insulation mastic
Mastics are used for insulating flat roofs and flat roofs. Their popularity is due to the following circumstances:
- No shrinkage during roof fabrication.
- Ecological cleanliness. The bitumen-based coating does not emit any harmful substances or unpleasant odors into the atmosphere.
- Resistant to chemically active substances.
-
Absence of seams, resulting in high tightness of the coating.
Bituminous mastic When coated with bitumen mastic, a durable seamless waterproofing layer is formed, which lasts 5-6 years
Along with a lot of advantages, this material has one significant disadvantage - fragility. The maximum service life is five to six years. Then the surface begins to swell and crack.
Film insulating materials
These are the most popular waterproofing products, primarily due to their low cost and ease of installation. The most commonly used polyethylene film with a thickness of 200 microns. It is laid in strips with an overlap of 12-15 centimeters. The joint is additionally glued with tape. On sale there are films with a sticky edge at the joint. They are more convenient to install, but they cost a little more.
We also produce films with an anti-condensation layer on the reverse side. This layer is able to retain moisture on itself, so that it does not get into the insulation.
Photo gallery: film materials for waterproofing
-
Polyethylene film for wind and water protection - To install an inexpensive waterproofing, a conventional polyethylene film is used.
-
Installation of waterproofing film - The film must be laid with a slight sag to compensate for possible linear expansion during operation.
-
Creation of a roofing cake with Ondutis film - Waterproofing membrane "Ondutis" can serve as an independent roofing covering for several months
-
Waterproofing with construction foil - Polyethylene construction films often have a rubberized base and are excellent at retaining moisture
Diffusion materials
It is a new material on the waterproofing market. Its peculiarity is that it allows moisture to pass in only one direction. The installation of such a film on the inside of the roofing cake is carried out to constantly drain it from accidentally trapped moisture.
There are three main types of films with one-sided permeability:
- Pseudo-diffusion. These are materials with limited permeability for use in cold attics and roofs. They are inexpensive.
- Diffusion material of normal permeability. This is a more advanced product used for insulation of attic rooms. It is undesirable to use it in dusty rooms, because the pores in it are easily clogged. This material cannot be used at temperatures below -25 o C, since when the water freezes in the pores, they break.
-
Three-layer superdiffusion membranes can be used in any conditions without losing their qualities.
Diffusion membrane Membrane films allow moisture to pass only in one direction, so that condensation from the roofing will not seep into the insulation layer
Vapor barrier materials
The installation of a vapor barrier when forming a roofing cake is vital. If the waterproofing layers of the roof are designed to protect the house from the penetration of water from the outside, then the vapor barrier protects the insulation from moisture from the inside of the building. Its accumulation inside the insulating layer quickly destroys the wooden structures of the truss system, anticipating a quick overhaul of the roof.
The vapor barrier must be placed below the insulation of the roofing cake, this makes it possible to intercept steam from the room, preventing it from entering the roof. If the roof is not insulated, a vapor barrier is still necessary, otherwise living conditions in the house may be equal to those in a greenhouse.
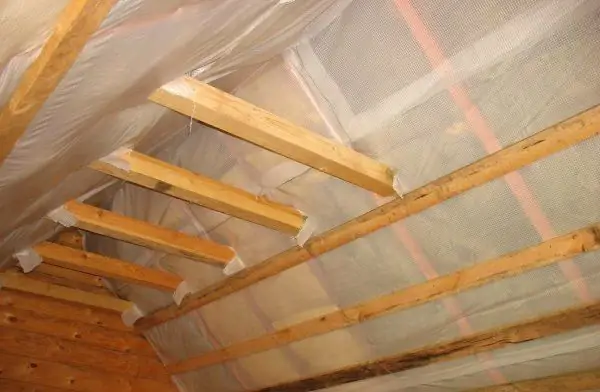
A vapor barrier film protects the roofing cake from moisture coming from inside the room
Most often, various polyethylene-based films are used for this purpose. They can be waterproofing, vapor barrier or antioxidant. The peculiarity of the latter is that one side is covered with a fleecy cloth that actively absorbs water, preventing it from getting on the insulation.
Previously, glassine was used for vapor barrier, but new materials on other bases significantly surpass it.
Depending on the physical and technical parameters, there are three main types of vapor barrier materials:
- Films based on polyethylene. Non-perforated products are used for vapor barrier. With any use of this material, it must be reinforced with a light mesh or fabric. Foil products are used as an insulating material that reflects heat into a building. Therefore, during installation, it is laid with the foil down.
-
Polypropylene films are more durable than previous ones. They are used for both steam and waterproofing. One side is equipped with an antioxidant viscose cellulose fabric coating.
Polypropylene film for vapor barrier Polypropylene films on one side are impregnated with a coating that prevents oxidation
- Diffusion is a new material on the construction market that allows steam to pass through but retains water. Such a film works in a very simple way: letting in steam, it absorbs it into a rough surface. Then the moisture gradually dries out. One-sided diffusion films are available, which need to be oriented in a certain way, and two-sided - they can be installed as you like.
Roof insulation
The need for thermal insulation is associated with large heat losses in the under-roof space of an uninsulated roof. According to experts, it can make up to 30% of the total amount of heat generated by thermal units. Considering the long heating period in most of the country, the losses are quite significant. Therefore, the cost of roof insulation will pay off quickly.
What are the indicators to choose the best insulation:
- Durability - stable operation of the insulation layer during the maximum life of the building.
- Fire safety and resistance to waterlogging.
- Environmental safety - during operation, the insulation should not release hazardous vapors or solid particles into the atmosphere.
- Sufficient density, low specific weight and dimensional stability under the roof.
- Sound insulating properties.
- Effective thickness.
- Resistant to low temperatures.
When choosing an insulating material for a pitched roof, you should pay attention to the following points:
- The thicker the insulation is, the more effective it is.
-
Given the low price of this material, you need to choose products from reliable manufacturers that have proven themselves well on the market. It could be Isover, Knauf or Oops.
Mineral wool KNAUF KNAUF mineral wool provides an optimal combination of sound and heat insulation properties at an affordable price
- The device of the roofing cake must be carried out in accordance with all the rules, including the organization of technological gaps between its layers.
- During the installation process, it is necessary to ensure that there are no gaps between the insulation plates, the joints between individual parts should be overlapped with subsequent layers.
Insulation installation technology is as follows:
- Lay a waterproofing layer.
- Measure and cut the insulation for laying between the rafters. In this case, it must be remembered that it must fit tightly, without gaps in the opening. It is important to arrange a gap between the insulation layer and the waterproofing of at least 20 millimeters.
-
Lay the insulation from bottom to top.
Insulation laying The insulation must be laid tightly between the rafter legs, the joints between the plates must be overlapped with a layer located on top
- When placing insulating materials, sagging should be avoided. Gaps between fragments are undesirable. However, it should be borne in mind that during operation, the insulation layer is prone to an increase in volume.
-
Install vapor barrier film. It should be controlled that its front side is directed into the room. Then moisture from the roofing cake will be removed to the outside.
Installation of vapor barrier The vapor barrier membrane is laid from the side of the room and fixed with a stapler to the rafter beams
- Fasten the vapor barrier film to the beams with a stapler, glue the joints with tape.
- Install the bars on top of the vapor barrier film, which will serve as the basis for the surface finish.
Video: insulation of a pitched roof
Profiled sheet
For the device of the finishing roofing, corrugated board is increasingly used. This is due to its excellent strength characteristics, a large selection of colors and shades, simple installation technology and material affordability.
A more complete list of the advantages of this material can be presented as follows:
- Ecological cleanliness.
- The widest palette of color solutions for the coating, which allows you to choose a harmonious combination with other structures on the site.
- A wide range of protective coatings for all operating conditions.
- Affordable cost.
- The ability to order the material strictly in accordance with the lengths of the slopes in order to make a continuous roof.
The choice of a specific type of profiled sheet depends on the angle of inclination of the slopes. The material must ensure water drainage during summer rains and spring snow melt, as well as withstand snow loads in winter. The value of the vertical overlap of the sheets also depends on the angle of inclination - the smaller the angle, the greater the overlap is created.
For example:
- at an angle of inclination of up to 10 degrees, the overlap should be at least 300 mm;
- on slopes with a slope of 10-15 degrees, the amount of overlap is 200 mm;
- at slopes of 15-30 degrees, an overlap of 170-200 mm is allowed;
- on steeper roofs, a sheet overlap of 100-150 mm is sufficient.
At angles of inclination up to 10 degrees, the joints must be treated with a sealant.
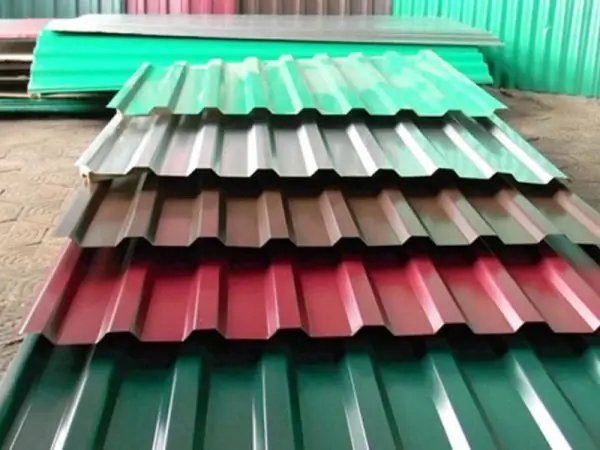
Different grades of corrugated board differ in strength, wave height and material thickness
When choosing a corrugated board for a roof, first of all, you need to pay attention to the marking of products:
- The letter "H" denotes a sheet used for roofs or interfloor floors.
- The designation "HC" indicates the universal nature of the profile. It can be used for roofing and wall decoration, as well as for building site fencing.
- Marking "C2" is used to supply a profiled sheet intended exclusively for wall coverings.
It is important to understand that the strength of the sheet depends on its thickness and profile height. Profiled sheet is produced with a corrugation height from 10 to 114 mm from metal with a thickness of 0.4-1.0 mm.
Fastening sheets of corrugated board
Sheets of corrugated board are attached to the crate with self-tapping roofing screws. They are installed both on the crest of the corrugation and in the depression adjacent to the crate. The lower fastening is made with self-tapping screws up to 30 mm long, the length of the screw for the upper fastening is made up of the profile height plus 30-40 millimeters. Bottom fastening is made in the cavity following the overlap. A washer and an elastic gasket are installed under the hex head of the screw, blocking the flow of moisture into the under-roof space.
The number of attachment points depends on the pitch of the lathing - one screw for each board.
Video: installation of corrugated roofing
The process of creating a roof from corrugated board is simple and straightforward. There are enough materials in the construction markets both in quantity and quality. You need to find the determination in yourself, take it and do it yourself. I wish you success!
Recommended:
Roofing Made Of Roofing Material: Features Of The Device And Operation, Repair, How To Avoid Mistakes During Installation
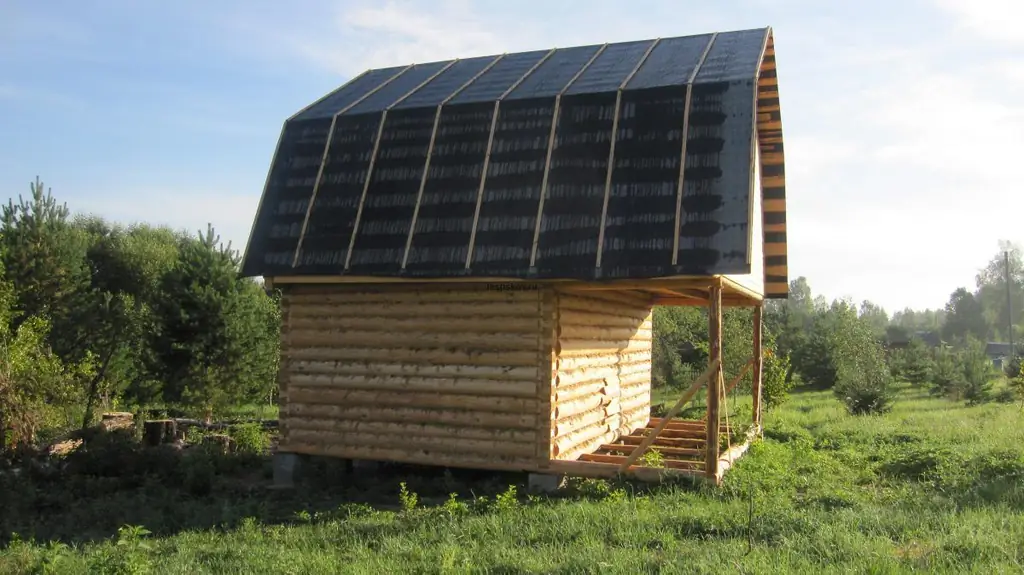
Roofing roofing felt: features, manufacturers and types of material. Installation of soft roofing: calculations, tools, nuances and mistakes. Roof operation
Roofing From A Profiled Sheet, Including The Features Of Its Design And Operation, Repair, As Well As How To Avoid Mistakes During Installation
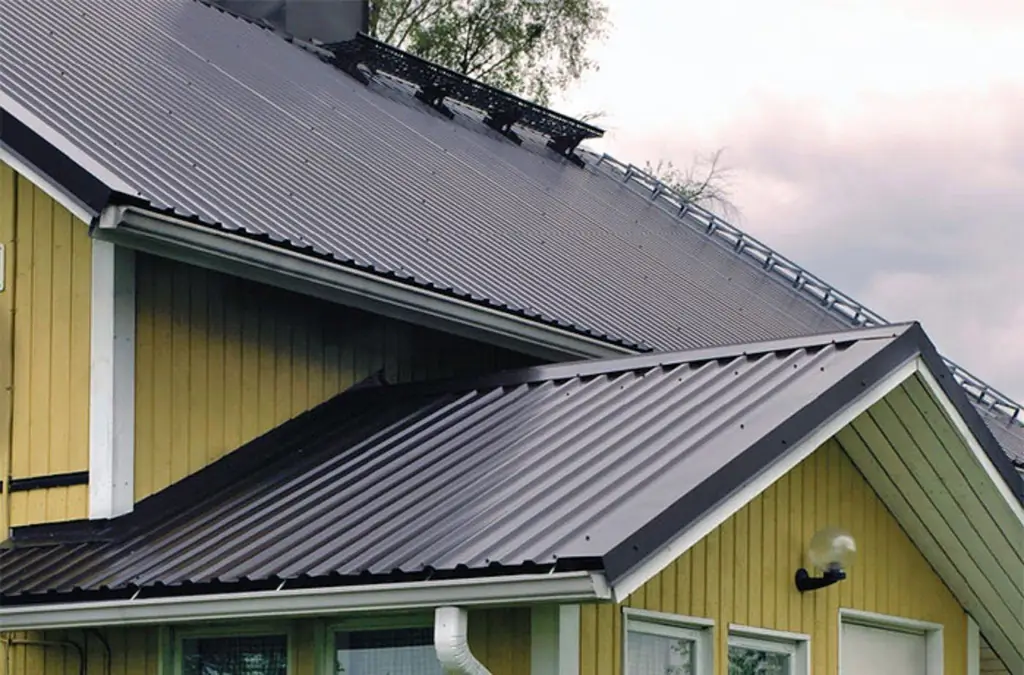
What kind of profiled sheet can be used for the roof. DIY cold and insulated roof device. What mistakes are possible. Features of operation and repair
Roofing Profiled Sheet, Including Its Types With Description, Characteristics And Reviews, As Well As Processing And Use Features
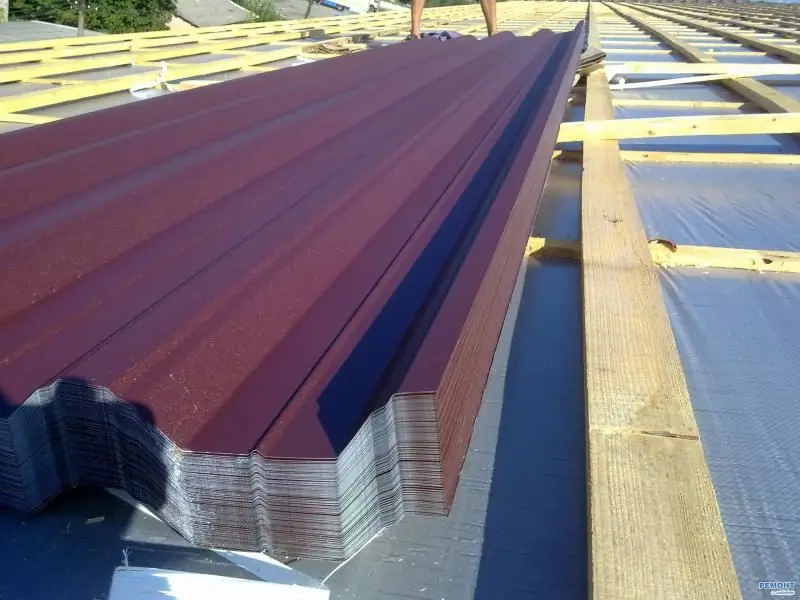
Using a profiled sheet to cover the roof. Classification, features of work and operation of corrugated board. How to cut a profiled sheet into fragments of the desired size
The Slope Of The Roofing From The Profiled Sheet, Including How To Choose The Right Brand Of This Roofing Material, Depending On The Angle Of The Roof
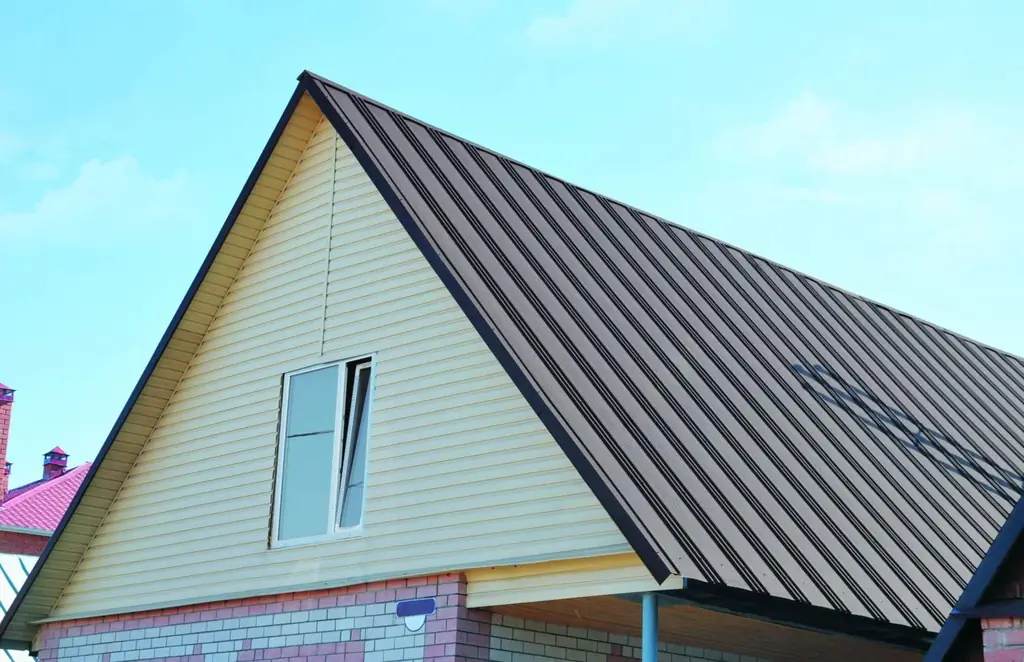
What is the slope of the roof. The angle of inclination of the roof from the profiled sheet: minimum and permissible. The choice of the brand of corrugated board according to the degree of roof slope
Roofing Made Of Flexible Tiles (soft, Bituminous), Characteristics And Reviews, As Well As Features Of The Device And Technology Of Laying The Material
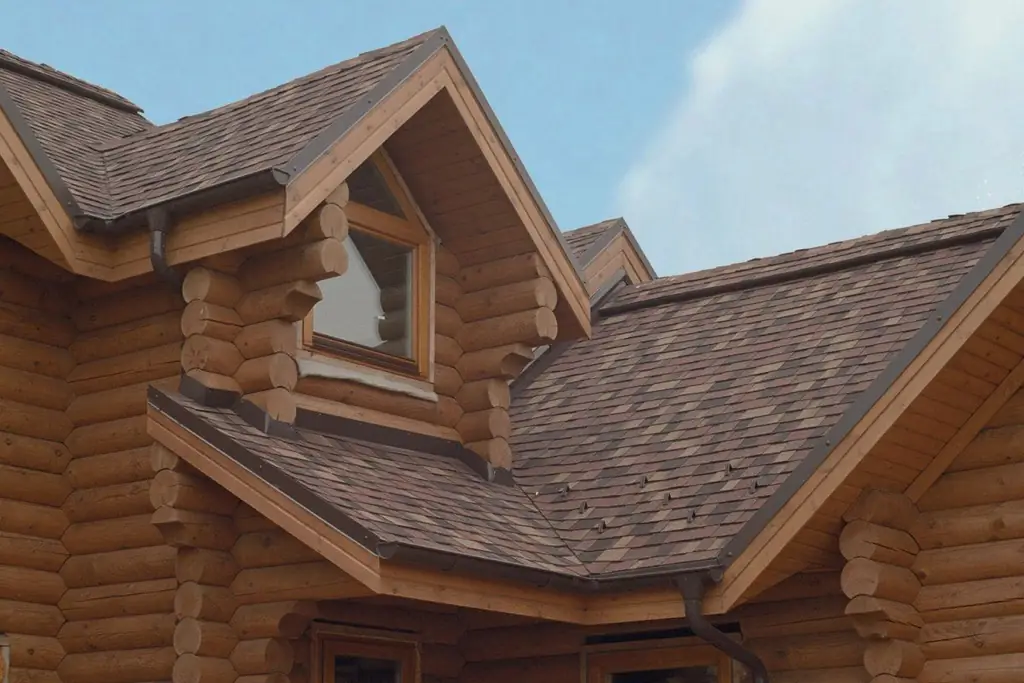
What is a bituminous tile roofing, what are its pros and cons. Features of the technology of arranging a soft roof, recommendations for care and repair