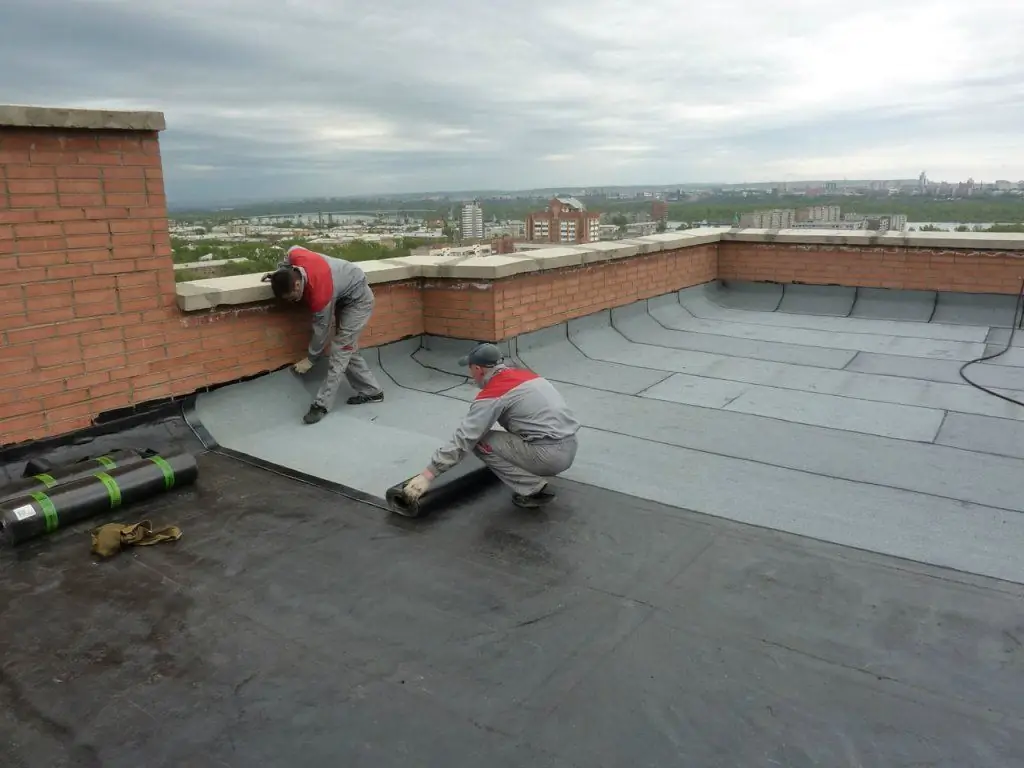
Table of contents:
2025 Author: Bailey Albertson | [email protected]. Last modified: 2025-06-01 07:32
How to calculate the need for materials and install a welded roof

Roofing a house is one of the construction stages that protects the interior from the vicissitudes of the weather. Its correct design determines the durability of the building and the comfortable living conditions in it. Before erecting a roof, you need to correctly calculate and purchase all the necessary materials. And knowing the basic mistakes that inexperienced builders often make will help to avoid leaks during the entire declared service life of roofing materials.
Content
-
1 How the welded roof works
- 1.1 Photo gallery: deposited flat and low-slope roofs
- 1.2 What does the welded roof consist of?
-
2 Calculation of the need for materials for roofing
2.1 Calculation of the need for bottled gas
-
3 Stages and technology of installation of the welded roof
- 3.1 Tools for installing the weld-on roof
-
3.2 Overlay roofing with expanded polystyrene
3.2.1 Video: flat roof insulation - installation of expanded polystyrene boards
- 3.3 Laying the overlaid roof on a wooden base
- 3.4 Construction of multilayer weldable roofs
- 3.5 Video: do-it-yourself surfacing
-
4 Thermal insulation of the overlaid roof
- 4.1 Materials for insulating flat roofs
- 4.2 Composition of the roofing pie of the insulated roof
- 4.3 Arrangement of abutments on the overlaid roof
- 4.4 Video: soft roof with insulation
- 5 Errors during the installation of the welded roof
How is a welded roofing structure
Fusion materials remain one of the most popular coatings for shallow pitched roofs. The reason for this is the relatively low cost and simplicity of such a roof. The quality of modern bitumen-polymer roll products makes it possible to reasonably count on the durability and tightness of the roof during its entire service life.
Fusion roofs are most often installed on flat roofs of industrial and residential buildings. In private housing construction, they are also used on pitched structures with an angle of inclination up to 15 degrees. All materials used in the composition of welded roofs are made from high-strength components and have increased resistance to various natural phenomena. The topcoats have a multi-layer structure and can easily withstand the effects of strong winds, heavy rainfall and hail:
- the basis of the roofing material is made of reinforced fiberglass, fiberglass or high-strength polyester;
- working layers consist of bitumen, to which polymer binders are added to increase the elasticity and durability of the coating;
- the outer surface of the products used as finishing for the construction of a multi-layer roof is covered with coarse-grained dressing, which provides additional protection against ultraviolet rays and mechanical damage.

Modern deposited materials have a multi-layer structure, consisting of a strong base, bitumen-polymer binder and protective coatings on both sides
Significant disadvantages of welded roofs include the difficulty of detecting leaks. Water can penetrate under the cover very far from where it seeps into the room.
Soft roofs require constant monitoring and timely elimination of detected minor damages. At the same time, special attention is paid to the junctions and drains. The frequency of the audit is at least twice a season, as well as after each potentially dangerous weather anomaly.
Photo gallery: weldable flat and low-slope roofs
-
Fusion roofing with imitation of tiles - The deposited material can be laid on roofs with a fairly large slope
-
Flat roof made of weldable materials -
A flat deposited roof made of modern materials, subject to the laying technology, has served for several decades
-
Roofing material - Modern roll roofing materials are made on the basis of reinforced glass fabric or polymer materials.
-
Damage to the overlaid roof - Violation of the installation technology can lead to the formation of a leak at the junction of the canvas
What does the welded roof consist of?
Regardless of the material of the roof base, during its installation, a roofing carpet is formed, consisting of the following layers (from bottom to top):
- Vapor barrier - most often made of polyethylene film with a thickness of about 200 microns. The canvases are laid with an overlap of about 12-15 cm, the joints are glued with construction tape. At the junctions, the film is brought onto the mating plane to a height of 10-12 cm. At present, special membranes with one-sided permeability are increasingly used.
- Forming screed - created to ensure the slope of the roof towards the roof outlets. The screed is usually made only on concrete roofing slabs and expanded clay concrete is used for this. It has heat-saving properties and low weight. Filling is done on the lighthouses. Drying time should be at least a day, ideally seven days. The total curing time of the concrete is 28 days.
- Thermal insulation - is laid from slabs of mineral or basalt wool in two layers. The joints of the lower layer must be completely covered by the upper plates in order to prevent through channels for the penetration of cold air. The purpose of the heat-insulating layer is to exclude the effect of ambient temperature drops on the microclimate inside the building.
- Waterproofing - protects the insulating layer from moisture penetration from the side of the roofing.
-
The top coating of the roof is a roll deposited material that can be laid in several layers. For the lower layer, ordinary sheets are used, the uppermost roll should have a coarse-grained protective backing on the outside. The joints of the canvases of different layers must be shifted so that they do not overlap.
Fusion Roof Roofing Pie To form a slope and additional protection of insulation material on flat roofs, a screed is made of expanded clay concrete
The peculiarity of using the deposited materials is that they can be used on the old coating during repair. This saves labor and material resources for dismantling and disposal of old material.
To improve the adhesion of the roll material, the surface to be covered must be prepared. Special preparation consists of applying a primer / primer to a previously cleaned and dried substrate.
Calculation of the need for materials for roofing
The basis for calculating the need for materials is the data on the total area of the roof or each slope separately. In this case, you need to calculate all the elements of the roofing pie in turn. The best way is to draw up technological maps. It consists in the fact that on the sweep of the covered surface on a scale, layered layouts of all the materials used are applied.
Consider specific calculations using the example of a rectangular flat roof measuring 10x8 m with parapets around the perimeter.
- Calculation of the need for a vapor barrier. A polyethylene film is used in a roll of 20 m long and 2.05 m wide with a thickness of 1.2 mm. To determine the size of the sweep of the roofing space, we add the size of the influx to the parapet to the dimensions of the roof - 15 cm on each side. Thus, the roof map will have a length of 10 + 2 ∙ 0.15 = 10.3 m and a width of 8 + 2 ∙ 0.15 = 8.3 m. If the film is laid along the short side (8.3 m), then from one roll will turn out two full canvases and there will be 20 - 2 ∙ 8.3 = 3.4 m. They will cover a surface with a width of 2 ∙ (2.05 - 0.1) = 3.9 m (0.1 is the size of the overlap of the canvases) … Two rolls will cover 2 ∙ 3.9 = 7.8 m, leaving two pieces of 2.05 x 3.4 m, which will not be enough for the remaining surface. Therefore, a third roll is required, which will completely cover the remainder with a width of 10.3 - 7.8 = 2.5 m,for which you have to cut off two strips from it and lay them with a large overlap.
- Determination of the need for adhesive tape for processing joints. As a result of the layout of the canvases, five longitudinal glues are formed, for the connection of which 8.3 x 5 = 41.5 m of adhesive tape will be needed. In addition, fastening the film to the parapets will require another 2 x (8.3 + 10.3) = 37.2 m. The total consumption of adhesive tape for laying the vapor barrier will be: 41.5 + 37.2 = 78.7 m.
-
Calculation of the volume of concrete for the screed. Usually its thickness h is 12-15 cm. Taking into account the value of 15 cm, we obtain: V = L ∙ B ∙ h = 10 ∙ 8 ∙ 0.15 = 12 m 3.
Screed volume calculation The required volume of concrete for a screed is determined by multiplying its length, height and width
- Calculation of the amount of damper tape. Before pouring along the perimeter of the parapet, it is necessary to glue a damper tape designed to compensate for the thermal expansion of the screed in the hot season. Its required size will be 2 ∙ (10 + 8) = 32 m.
-
Determination of the need for insulation. We use basalt wool for thermal insulation. It is available in the following sizes:
- length - 800, 1000 and 1200 mm;
- width - 600 mm;
- thickness 50 and 100 mm.
Obviously, a material with a length of 800 or 1000 mm should be chosen, so that a whole number of plates are laid on one side. Plates 1000 mm long (i.e. 1 m) are laid along the long side, then 10 pieces will be needed per row. The number of such rows will be 8 / 0.6 = 13.3 ≈ 14 pcs. Thus, for a complete roof covering, 10 x 14 = 140 slabs of 1000 x 600 mm are required. When installing a layer of insulation of 100 mm, you can take 140 slabs of the corresponding thickness or 280 slabs with a thickness of 50 mm, which must be laid in rows with overlapping joints.
Insulation of a flat roof Roof insulation can be carried out with one layer of slabs 10 cm thick or with two layers of thinner material with overlapping joints
- The calculation of the need for waterproofing on top of the insulation is done in the same way as for the vapor barrier layer. Most often, the required amount of vapor and waterproofing coating is the same.
- Calculation of the need for a topcoat. It should be borne in mind that the size of the longitudinal overlap between the canvases should be 6 cm - this is incorporated in the design of the material. Transverse joints are made with an overlap of 10 cm. Otherwise, the calculations are carried out in the same way.
Calculation of the need for bottled gas
Let's make a reservation right away that the use of blowtorches running on hydrocarbon fuels does not make it possible to make a high-quality installation of the finish coating, since it is not possible to obtain sufficient heating and melting of the bitumen layer over the entire glued surface. Therefore, natural gas burners are used to carry out this work. The fuel consumption is determined by the burner power. The consumption rate can fluctuate within 0.8-1.2 l / m 2, therefore, with a roof area of 80 m 2, the gas demand will be about 80 liters. Considering that in the process of work it is more convenient to use 50-liter cylinders, you need to have two such containers at the beginning of the installation of the finish coating.

A two-nozzle torch quickly heats up the material during fusion and consumes about 1 liter of gas per square meter of surface
Stages and technology of installation of a welded roof
The use of fire during the installation of the roof imposes stringent safety requirements

The use of deposited materials is allowed only on reliable non-combustible bases.
Many materials used in such work are combustible, and some are fusible. Therefore, before performing the work, a fire-retardant layer is created in the form of a cement-sand screed or non-combustible substrates are used.
Tool for mounting the welded roof
The set of tools for the installation of a welded roof includes the following items:
-
Gas burner with cylinder and pressure reducer.
Laying roofing material with a gas burner To lay the roofing material by fusion, it is necessary to heat the lower surface of the sheet with a gas burner and press it tightly to the base
- Roller for rolling the edges of the weld material.
-
Putty knife. It is used to control the quality of joints. If no sag appears at the junction of the canvases, you need to check the quality of the joint with a spatula and, if necessary, reheat this place. An indicator of a high-quality seam is the formation of a bead about 2 cm wide.
Putty knife The quality of the blade joints is checked with a spatula
- Construction knife for cutting canvases.
- Brushes for cleaning surfaces from debris and dust and applying primer.
-
Industrial vacuum cleaner for fine cleaning before priming. When installing the roof of a private house, a household unit is sufficient.
A vacuum cleaner Before applying the primer, the roof surface must be thoroughly vacuum cleaned
Overlay roofing with expanded polystyrene
Expanded polystyrene is one of the most effective and durable insulation materials. Therefore, the choice in favor of using it can be explained quite easily. But the main obstacle to this can be its instability to high temperatures - it melts easily. The only way to use expanded polystyrene is to provide it with reliable protection from the effects of flame. This protection can be implemented in several ways:
- Arrange a cement-sand screed up to 10 cm thick. In this case, all the necessary slopes must be made towards the water flow from the roof.
- Cover the insulation with asbestos plates. For this purpose, flat slate can also be used.
- To make a bedding of expanded clay up to 7-10 cm thick, on top of which to arrange a cement-sand screed. In addition to protection from flame (expanded clay is a granules of sintered clay), such a layer is also a reliable thermal insulation. This will reduce the thickness of the main insulating layer.
A roofing cake of this design will reliably protect the house from all the vicissitudes of the weather.

To protect the expanded polystyrene from the effects of open fire during melting, expanded clay is poured over it and a screed is arranged
Video: flat roof insulation - installation of expanded polystyrene plates
Laying the welded roof on a wooden base
Wood and secondary products from it (plywood, chipboard, OSB and others), with all their advantages, have a significant drawback - they are flammable. Nevertheless, they are quite suitable for the construction of a welded roof. To do this, you need to attend to the implementation of preventive measures:
- Fire protection treatment with special fire retardants.
- A protective coating device in the form of a non-combustible substrate over a wooden floor. These can be flat asbestos-containing materials or soft, thick glass cloth backing.
Hardfacing timber roofs are usually installed on auxiliary structures, and a protective layer in the form of a screed on them is usually impossible due to its heavy weight.

Roofing material can be fused over wood after it has been treated with fire retardants
Construction of multilayer weldable roofs
The welded roofs are made using roll materials, which are based on:
- Fiberglass is a woven material made from glass threads. Possesses high strength, biologically stable. The disadvantages include insufficient strength in places of displacement of the topcoat. When the base is skewed, it can form cracks.
- Glass cloth - also made of glass, but non-woven. The web in the cover is quite flexible and elastic, but does not show sufficient tensile strength.
- Polyester is a web of polyester fibers. A very strong, flexible and biologically stable base for roofing roll materials.
To give these materials waterproofing properties, they are coated on both sides with polymer-bitumen compositions. There are two types of deposited coatings:
-
For the outer layer. The lower surface of such material is covered with a protective fusible film, and the upper surface is sprinkled with marble or granite chips. It protects the surface from UV radiation and mechanical damage. It is impossible to lay the material intended for the device for the inner layers as a topcoat, since it does not have the necessary strength and protective characteristics.
Outer layer of a double layer roof For the device of the upper layer of the overlaid roof, it is imperative to use a material with mineral dressing
-
For inner layers. The difference is that the film on the outside is fusible. When installing the top cover, it melts together with the bottom surface of the top cover. It is important to avoid overlapping joints of the top and bottom layers.
Material for the inner layers of the overlaid roof On the front surface of the material for the inner layers (substrate) there is a low-melting film
Adjacency rules for the top and bottom layers are the same.
Video: do-it-yourself weld roof
Insulation of the welded roof
The insulated roof of the house saves up to 25% of the heat in the building itself - this is a considerable savings on heating, so the costs incurred quickly pay off.
As for the insulation of a flat or low-slope roof, then the need for this may not arise. With such roofs, the attic usually serves as a purely technical room, therefore, high-quality insulation of the ceiling may be quite enough to ensure normal thermal conditions in the house. But in any case, insulation must be performed.
Roof insulation can be done in two ways:
- Installation of thermal insulation material during construction during the installation of the roof. This method is more convenient and technologically advanced. In this case, you can better equip the drainage system and ventilation of the building.
- Insulation of the roof from the inside. This work can also be done on the old house.
Materials for insulating flat roofs
Various materials can be used to insulate a flat roof:
-
Basalt-based mineral wool (Technoruf grade 45 or 60 produced by Technonikol). They are unique in that they can be applied without a protective screed.
Basalt wool slab insulation Fireproof basalt material allows you to reliably insulate the roof, and the device of a protective screed on them is optional
-
Polyurethane foam. Excellent material for roof insulation, has no seams or joints, non-flammable. It is applied by spraying.
Thermal insulation of a flat roof with polyurethane foam Polyurethane foam is applied by spraying, so it allows you to arrange perfect thermal insulation without joints
-
Foam concrete. This is a relatively new insulation, which is not inferior in strength to classical counterparts, and in its structure is a foamy material.
Roof insulation with foam concrete Foam concrete is one of the most modern materials that can be used to insulate roofs of any configuration
Composition of the roofing cake of the insulated roof
You need to create a reliable base for roof insulation. Most often, concrete slabs or profiled sheets are used for it. The operation to form a roofing cake is performed in the following order:
-
Installation of a vapor barrier film. Previously, a thick plastic wrap was used for this. But membranes with one-way permeability are more reliable. They remove moisture from the thickness of the insulation and do not let it pass in the opposite direction. If there is no such layer, moisture will gradually be absorbed into the porous material, which, from this, collapses into lumps and ceases to perform its functions.
Flat roof vapor barrier Membranes with one-sided permeability are currently used as a vapor barrier film.
-
Laying insulation boards. This element is best formed from several layers with overlapping joints. The plates are fixed to the base with telescopic dowels or with bitumen. The use of the first option is more appropriate on a metal base, it can also be used on concrete, but it is more expensive and more time consuming. Bitumen sticking is a more complicated and expensive operation. If a two-layer installation is used, the bitumen can be applied before the second layer is installed.
Laying insulation on disc dowels To fasten the insulation to metal or concrete surfaces, it is more convenient to use dish-shaped dowel-nails
- Laying of waterproofing from PVC foil or geotextile. The moisture-proof coating is laid directly on the insulation.
- Installation of the topcoat.
Arrangement of abutments on the welded roof
The device of abutments is, perhaps, the most important operation in the construction of a welded roof. Even a minor mistake here can lead to sad consequences, especially since it is a very difficult task to detect a leak in such roofs.
-
Adjacent to a perpendicular surface. It is made when the main canvases are installed at the intersection with the parapet. Surface preparation is carried out simultaneously with the main site and, after cleaning and repairing the damage, it ends with a primer to a height of 15-20 cm. Roofing in the abutment area is made with a solid sheet with an approach to the entire prepared vertical plane. Along the perimeter of the parapet, the edges of the canvases are fixed with a metal tape using dowels.
Direct flat parapet connection The connection is made with solid sheets, which are fastened at the top with a metal tape
-
The connection can also be arranged in a more reliable way - using a sealing metal strip. It is placed between two layers of the main covering on the parapet (wall of rectangular pipes). This joint forms a reliable and tight connection.
Junction device on a two-layer roof For a more reliable abutment device, a sealing metal strip is installed between the two layers of coating
-
The connection to the round pipe is carried out using special factory-made caps. The upper diameter of the cap is equal to the pipe diameter and is fixed with a clamp. The base is made in the form of a plane and is melted with the main coating during the installation process. Caps are produced according to the dimensions of the main standard pipes used in construction.
Roof adjoining to round shapes A hood of the appropriate size is used to securely connect to round ventilation and chimney outlets
- The connection to the weir is performed using special inserts in the roofing pie. At this point, a funnel is made, into which a water collector with a clogging mesh is inserted. Fixation and sealing is carried out using bituminous sealants.
Video: soft roof with insulation
Errors during the installation of the welded roof
In the process of installing roofing, performers often make mistakes that can be decisive for the quality of the roof. Typical among them are the following:
- The presence of traces of work shoes on the surface of the coating. This happens when the roofer unwinds the roll in front of him. Moving over hot material, it breaks the composite coating. Therefore, hot bitumen sticks to shoes. In addition, with this installation method, it is impossible to control the softening of the bitumen. In particular, a picture in the form of snowflakes is applied to the films produced by TechnoNIKOL. When, when heated, they begin to deform, the surface becomes suitable for gluing.
- When installing a two-layer roof, the canvases are glued only in parallel, but not crosswise. As a result of the intersection of the joints of the upper and lower layers, leaks are formed. When laying in parallel, make sure that the joints do not overlap. This is also a ready-made leak.
-
Incorrect surface spreading. To ensure slopes towards the drainage funnels, it is necessary to use beacons installed before applying the screed. In the absence of a slope towards the drain on the roof, “reservoirs” are formed, leading to rapid deterioration of the roofing.
No roof slope If the slope of the roof is done incorrectly, water accumulations will form on the surface, which will gradually destroy the coating.
- The use of an unsuitable tool for quality control of joints. To do this, only use a spatula. If a knife blade is used, undercuts are inevitable, which later turn into leaks.
- Incorrect execution of transverse joints between the canvases. It is necessary to weld the bottom layer onto the top one, provided with a dressing. To perform this operation with high quality, you need to warm up the canvas from above and carefully roll this place with a roller until the dressing is immersed in the bitumen. Only then can the top layer be heated and glued. The overlap must be at least 10 cm.
Considering the above, it can be summarized that the roof fusion should be carried out by experienced personnel with the appropriate qualifications and experience.
Execution of works on the installation of a welded roof requires certain knowledge and skills. And although the installation technology is extremely simple, there are a number of features that must be taken into account during installation. Therefore, if a decision is made to carry out the work on your own, you need to participate in overlapping at least one roof and gain some experience. In addition, the presence of at least one experienced specialist is desirable during the installation of the roof. I wish you success!
Recommended:
Repair Of The Overlaid Roof, Including A Description Of The Technology And Main Stages
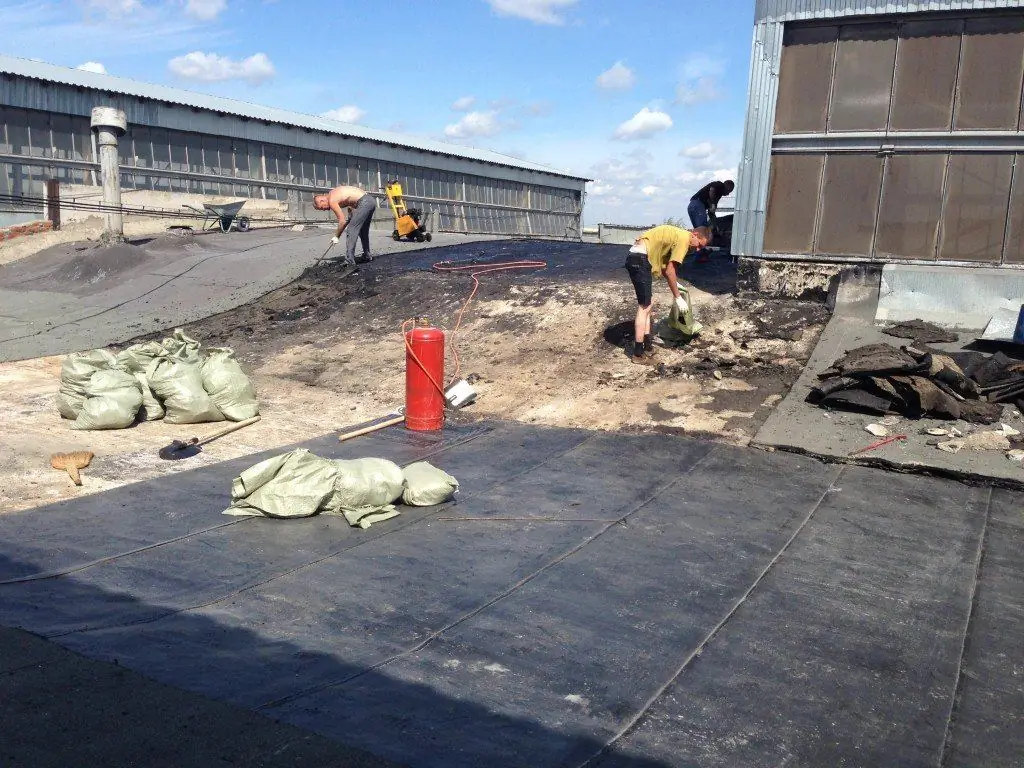
What defects arise during the operation of the deposited roof, the reasons for their occurrence and how to eliminate them. Repair of a roof made of deposited materials
How To Correctly Calculate The Consumption Of Self-tapping Screws For 1m2 Of Profiled Sheet For The Roof, Fastening Scheme

How to fix the roofing profiled sheet - with screws or rivets? Features of mounting corrugated board on self-tapping screws. Consumption of fasteners per 1 m²
Lathing For Monterrey Metal Tiles, Including A Diagram And Installation, As Well As How To Correctly Calculate The Amount Of Material

Sheathing device for metal tiles "Monterrey", the recommended dimensions and the scheme for calculating the required amount of sawn timber. Installation procedure
Lathing For A Soft Roof, What Needs To Be Taken Into Account During Installation And How To Correctly Calculate The Amount Of Material
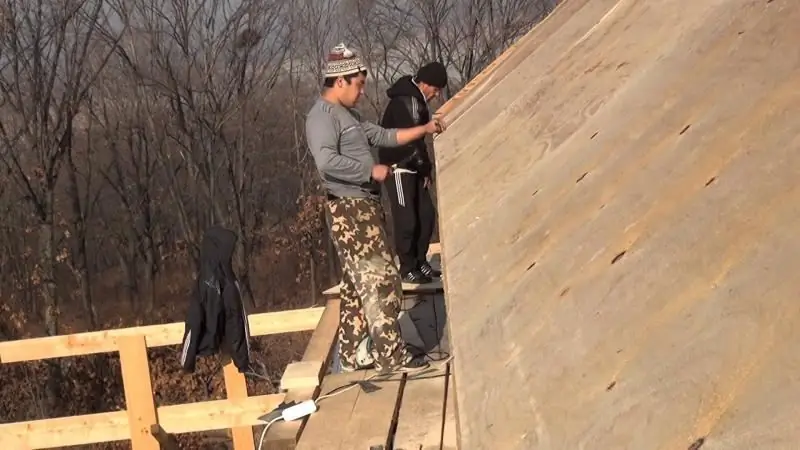
Types of sheathing for a soft roof. List of materials and their calculation. Solid lathing along the sparse. Installation of battens and counter battens for soft roofs
Snow Holders On A Roof Made Of Corrugated Board, Including An Overview Of The Varieties, As Well As How To Correctly Calculate And Install
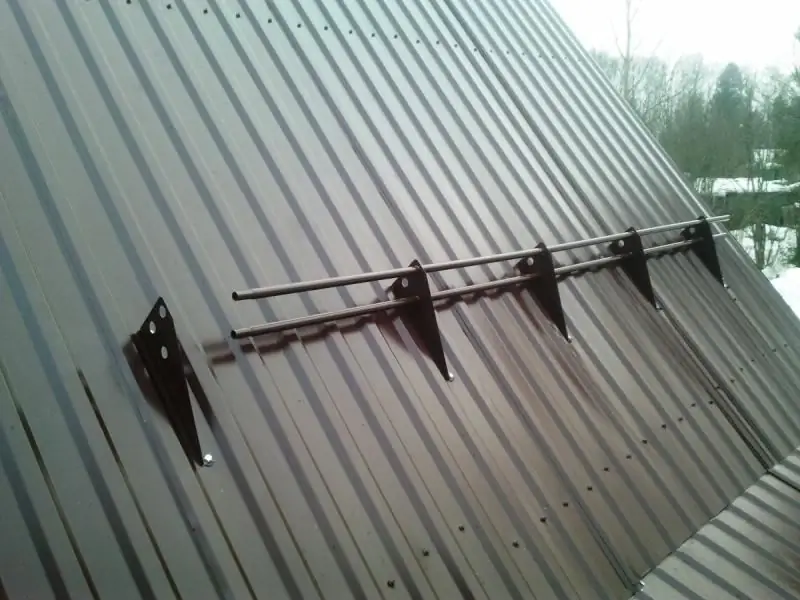
Do you need snow holders for a roof made of corrugated board. Types of barriers. Correct installation of snow guards and calculation of their number