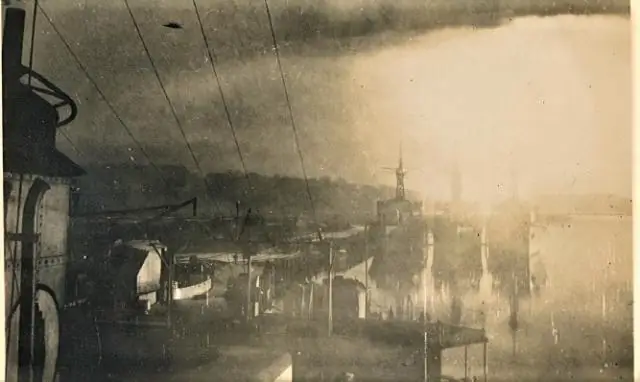
Table of contents:
2025 Author: Bailey Albertson | [email protected]. Last modified: 2025-06-01 07:32
DIY sliding gates
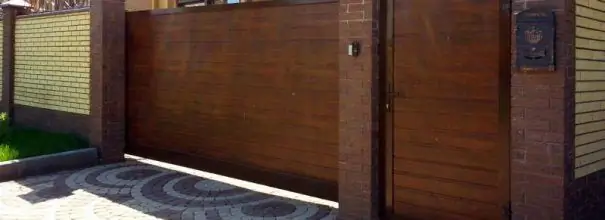
Sliding gates are very popular at the present time, although in the recent past, few could afford to install such a structure on the site, due to the high cost of accessories and mechanisms. Now their cost is much lower and the availability is higher, and also a person with welding skills can make them with his own hands. The absence of upper and lower guides in sliding gates gives an advantage to the passage of vehicles of almost any size.
Content
- 1 Sliding gates - principle of operation and design
- 2 Design drawing and diagram
-
3 Selection and calculation of materials with fittings
3.1 Required tool
-
4 Instructions for the manufacture and installation of sliding gates with your own hands
- 4.1 We connect the frame to the frame
- 4.2 Painting
- 4.3 Sheathing
- 4.4 Foundation
- 4.5 Installation
- 4.6 Automatic door opening
- 4.7 Table: dependence of motor power on door weight
- 4.8 Ready-made sliding gates with automation:
- 4.9 Video: do-it-yourself sliding gates
Sliding gates - principle of operation and design
The principle of gate operation: the leaf moves on two roller trolleys mounted on a concrete channel. The upper rollers are used to protect against falling and skewing. In the closed state, to relieve the load from the roller supports, an end roller is installed on the guide, which drives into the lower catcher when the gate is closed. The upper catcher is installed for more reliable fixation of the gate in the closed state. The full size of the gate is 150% of the width of the opening, that is, if the opening is 4 m, then the total width of the gate leaf will be 6 m and, accordingly, the space for rollback should be at least 6 m. Perhaps this is the main drawback of this type of gate and if not enough places it is worth considering other options.
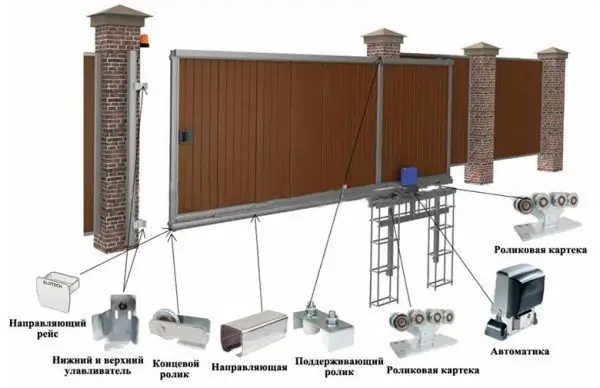
Sliding gate scheme with basic elements
Drawing and schematic design
Before making a gate, it is necessary to decide on the dimensions of the future gate, make a drawing indicating these dimensions. The gate consists of a load-bearing frame and a lathing (inner frame). The frame is usually made of a rectangular profile pipe 60 * 30 mm and 2 mm thick, and you can also use pipes 60 * 40 mm or 50 * 50 mm if the required size is not available. For the inner frame, a 40 * 20 or 30 * 20 profile pipe is suitable, depending on which one is available.
An example of a connection diagram for gate parts:
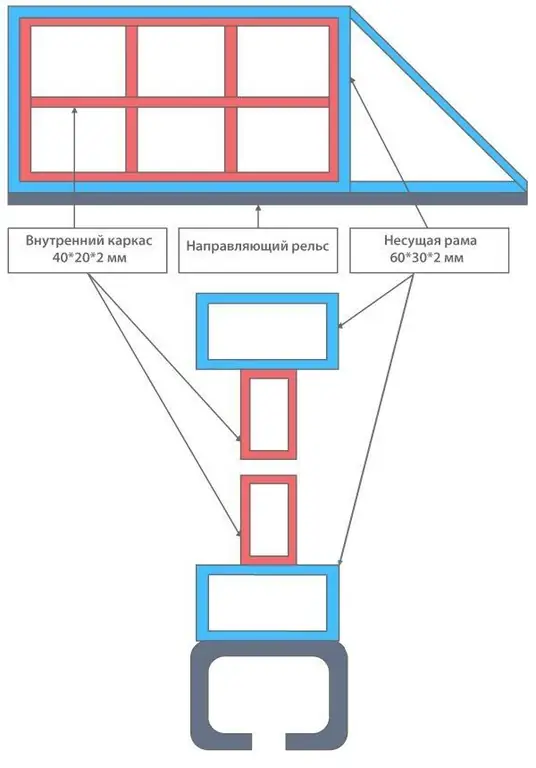
Parts connection diagram
Selection and calculation of materials with fittings
Take the drawing above for example. For the frame we will use profiled rectangular pipes 60 * 30 2 mm thick. We calculate the total length of the pipe for the frame based on the dimensions in the drawing 4200 * 2 + 1800 + 1865 = 12065 mm, the length of the hypotenuse of the triangular part is calculated by the formula c = √b 2 + a 2 √1800 2 +1865 2 = 2591 mm, 12065 + 2591 = 14656 mm. The total is 14.66 m in meters, this is what concerns the frame.
For the inner frame, take a 40 * 20 pipe and now calculate the total length 4200 * 3 + 1865 * 4 = 2060 mm or 20.6 m. All dimensions are taken with a small cape.
Fittings are difficult and unprofitable to make on their own and are usually bought in stores of the corresponding profile. When choosing accessories, you need to know the approximate weight of the future structure for the correct selection of rollers that can withstand this weight without problems.
Almost any material can be used for internal lining of the gate, but most often a profile sheet is used for this purpose, popularly called it "corrugated board". Decking can be ordered in any size and color, it is quite lightweight and has an anti-corrosion coating. For the gate in our example, you need a sheet with dimensions of 7.833 m 2. For fastening the corrugated board, self-tapping screws with a drill or rivets will be needed. For the mortgage, you need to purchase a section of a channel with a width of 16-20 cm and a length equal to half of the gate opening, in our case at least 2 meters. The reinforcement for the foundation frame should be taken with a diameter of 12-16 mm and a length of 15. For mixing concrete for the foundation, you will need cement, sand and crushed stone in a ratio of 1: 2.1: 3.9. For the foundation of the gate from the example you need 0.5m 3 of concrete.
Required tool
- Welding machine, preferably semi-automatic.
- Grinder with cutting and grinding discs.
- Screwdriver or riveter.
- Hammer, tape measure, white marker.
- Concrete mixer, bayonet and shovel.
- Protection for eyes and hands.
DIY instructions for the manufacture and installation of sliding gates
First, you need to cut the pipes according to the dimensions given in the drawing using a grinder. Be sure to use protective equipment.
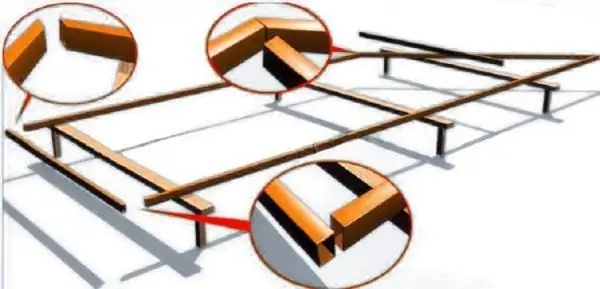
Cutting and sizing pipes
When finished cutting, place the pipes on a horizontal surface or supports, as in the picture above, to form a frame according to the drawing. After making sure that the layout is correct, we weld all the corners of the frame at several points, then completely weld the joints. Now you need to grind the weld seams. The inner surface of the frame, where the frame will be attached, must first be primed with an anti-corrosion primer, since later when the frame rises, access will be impossible.
Using the same method, we weld the frame and also clean and prime it only from the outside.
We connect the frame to the frame
First, let's decide how the gate leaf will be sewn up - only from the front or from both sides. If only from the front, the frame should be welded flush with the front side of the frame, when from two, then in the middle. Let's take the option on both sides. We measure the distance and make marks inside the frame where the frame should be. Inside the frame, lying horizontally, we lay the finished frame in the middle of the frame, adjusting it according to the marks with substrates from pieces of a wooden bar. Adjusted, checked, now you need to connect the frame to the frame with welding points around the perimeter with a step of about 45-60 cm, so that the frame and frame do not move. We boil in 1 cm sections crosswise until the step between them is 15-16 cm, and only then we boil the joints completely. Now we weld the guide rails from the hardware kit to the bottom of the frame. We will weld in the same wayas well as frame to frame.
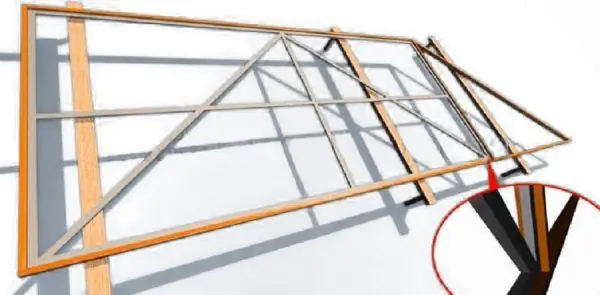
Welding the frame to the frame
Painting
Next, you need to prepare the frame for painting. First, we clean all the welds with a grinder to an acceptable look. We degrease the entire frame and prime it with an anti-corrosion primer. After the primer layer has dried, you can start painting. For painting it is better to use alkyd enamels, but acrylic paints are also quite suitable. You can paint with a spray gun, brush or small roller. Painting is done in 2 layers, applying the next layer after the previous one has dried.
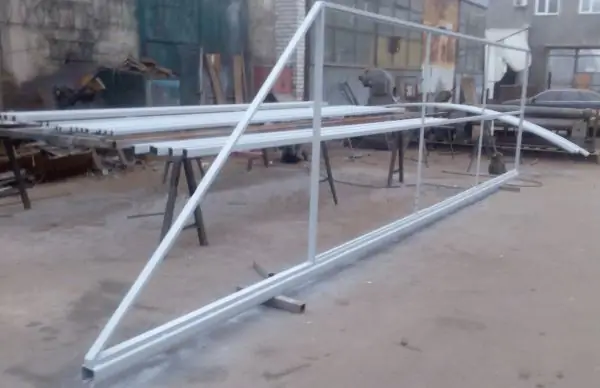
Finished frame painting
Sheathing
You can start sewing the door leaf. The cut-to-size profile sheet is fastened with self-tapping screws with a drill or rivets. First, we fix the sheet in the corners, and then we fasten it along the perimeter and along the inner frame in 15-20 cm increments.
Foundation
You can start pouring the foundation. We dig a hole at least half the length of the gate opening, in our case at least 2 m, 0.5 m wide and 0.7-1 m deep. We start preparing the mortgage - there is nothing complicated here. This is what the finished mortgage looks like:
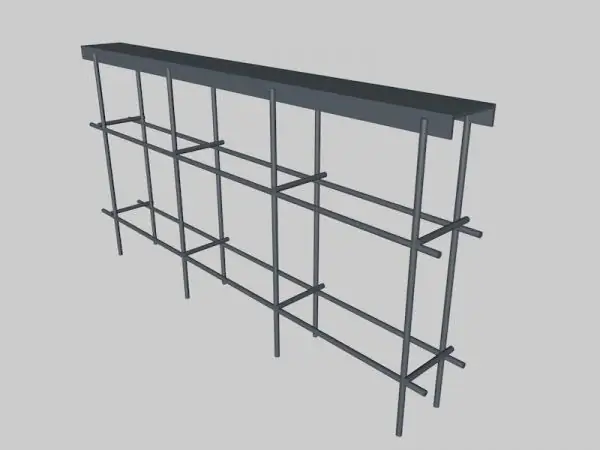
Embeddable channel with reinforcing frame
We place the mortgage in the pit and check with the level that the channel is in the horizontal plane and in the same level with the yard area, so we will provide an even base for the carriages. We mix the concrete with a concrete mixer in the proportion: 1 part of cement, 2.1 sand, 3.9 crushed stone. The resulting concrete grade is M250. We fill the hole completely, not forgetting to often pierce the concrete with a piece of reinforcement or a wooden lath for better penetration and filling of voids. The foundation should stand for at least 10 days, and the full period of drying and curing with concrete is 28 days. The next day and in the next 3-4 days, it is necessary to water the foundation with water to avoid cracking of the concrete.
Mounting
The foundation is ready - you can start installation. Place 2 carriages on the mortgage at the maximum distance from each other. We expose the gate on carriages, inserting them into the guide rail. Now you need to adjust the carriages. The one closest to the opening is placed so that the gate, when fully opened, does not reach the carriage with its edge of 15-20 cm. Another carriage is placed so that when the gate is fully closed, its edge does not reach the carriage 5 cm. We check the installation with a level and tack it with welding. When we have checked that the whole structure is correct, we weld the joint of the carriage and the mortgage completely.
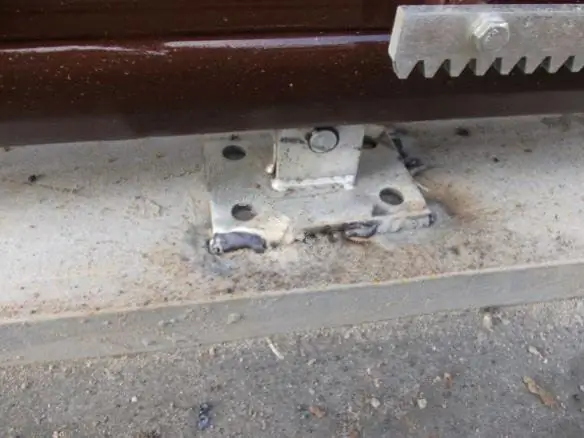
Tack welding of carriages on a channel with installed gates
The next steps are to fasten the remaining parts. The upper protective rollers are attached to the mortgage in the post, if it is provided, when there is no mortgage, you must first fix the metal plate on the anchor bolts, it will act as a mortgage. The top rollers are usually welded to the insert.
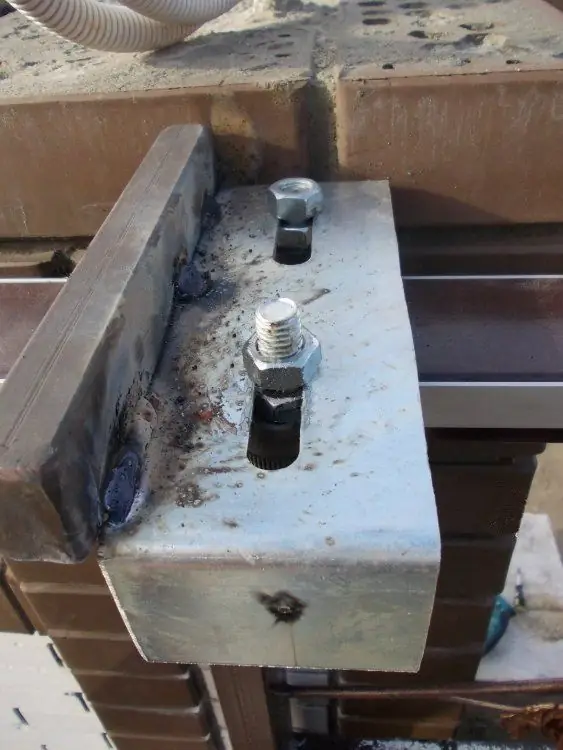
Upper roller mounting option
You can weld a piece of pipe 30 * 20 on top of a 60 * 30 pipe and weld the upper rollers to it. In this way, we will get a more reliable mount.
On the opposite pillar, we attach to the embedded a section of a profile pipe 30 * 20 with a length equal to the height of the gate leaf, and directly to the pipe, the upper and lower catchers. We attach the lower catcher 5 mm higher than the end roller is located, so that when hitting the catcher, the gate rises, thus partially removing the load from the carriages.
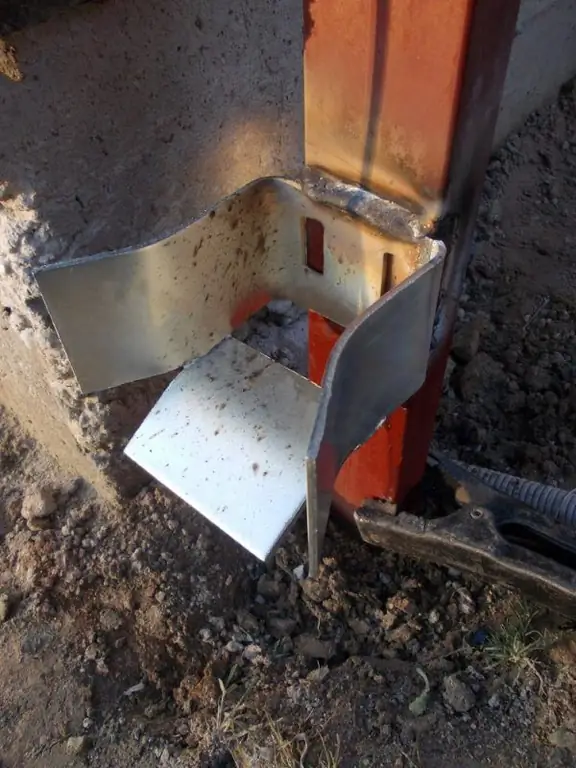
Lower catcher fastener
The upper catcher is attached to the pipe 5-7 cm below the top of the gate to protect it from vibrations in the wind.
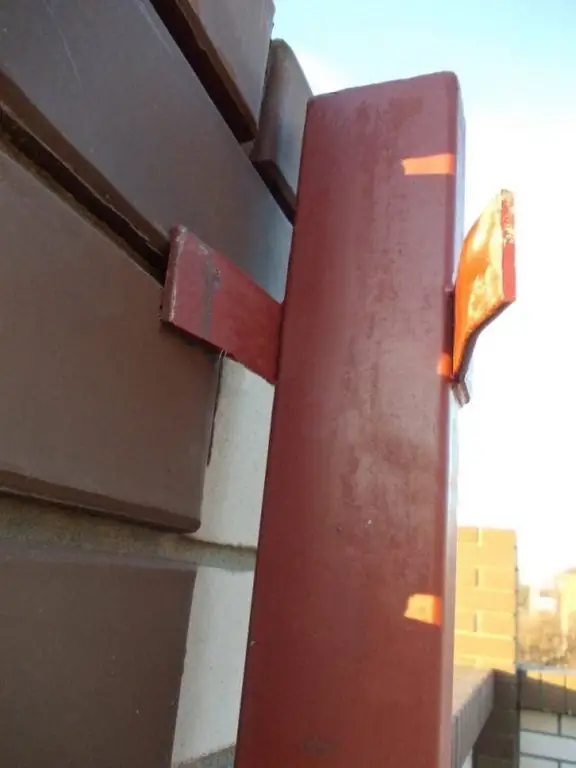
Mount the top catcher
Next, we clamp the end roller in the guide with bolts, you can even weld it for better reliability, since the nuts are released over time.
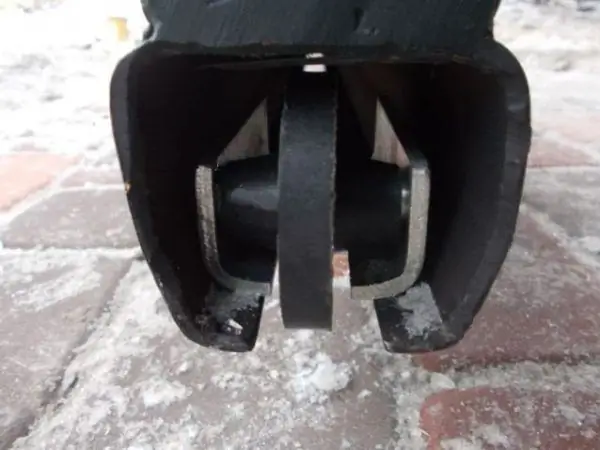
Installing the end roller in the rail
The guide is closed on one and the other side with rubber plugs that come with the fittings.
Automatic gate opening
For ease of use, you can make an automatic drive for opening the gate, nowadays the market offers a large selection of such drives, and it is not difficult to choose something for yourself with a good balance of price and quality. It is best to entrust the installation of the drive to a specialist in this matter, although you can figure it out yourself, since the drive comes with detailed instructions for connecting the motor itself, sensors and mounting the gear rack.
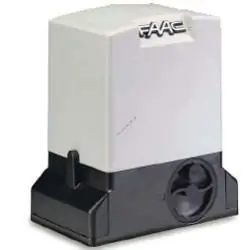
Automatic gate drive
The power of the purchased drive, depending on the weight of the sliding gate, can be viewed in the table:
Table: dependence of motor power on door weight
Gate weight | Engine power |
250-300 kg. | 200-250 W |
500-600 kg. | 350-400 watts. |
800-1000 kg. | 500-600 watts. |
But it is still better to buy a drive with a power reserve.
Ready-made sliding gates with automation:
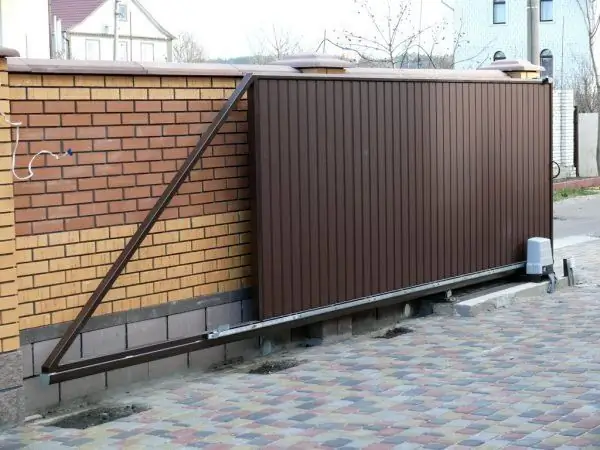
Ready-made sliding gates with automatic drive
Video: do-it-yourself sliding gates
It is no secret that sliding gates designed and assembled on their own will be much cheaper than those ordered from a company for the production and installation of such gates. We control the quality of workmanship ourselves, so that everything can be adjusted down to millimeters, thereby making a quality product for our own use.
Recommended:
How To Build A Wooden Porch With Your Own Hands: In Stages, Photos And Videos
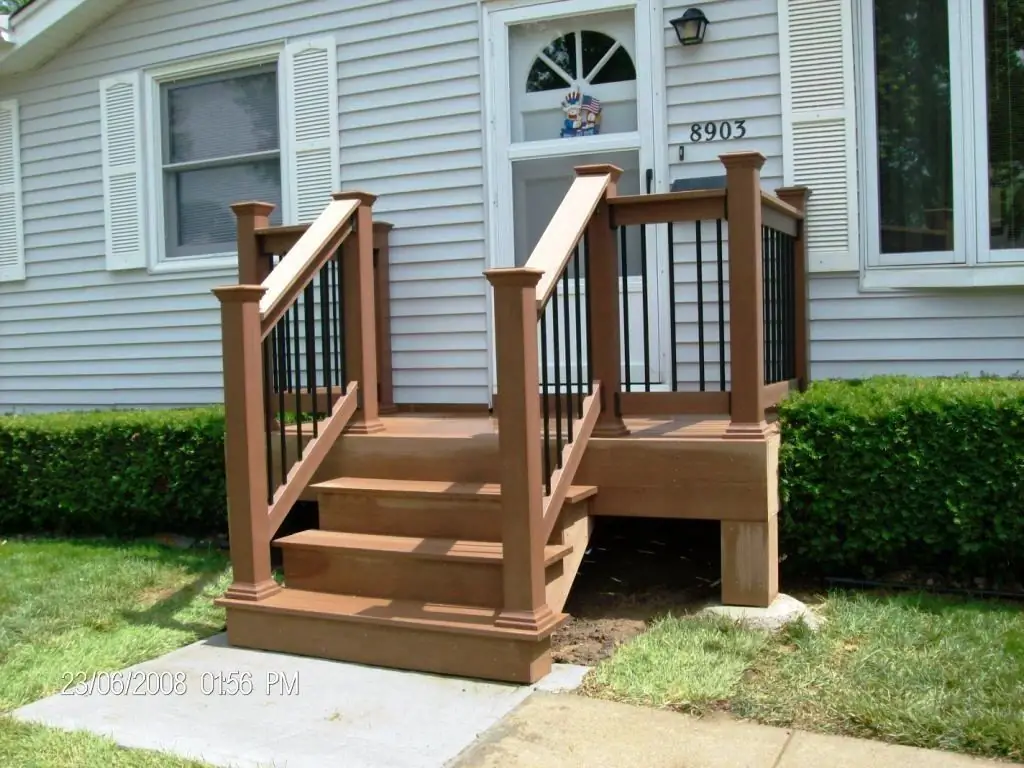
Detailed description of the construction of a wooden porch. Materials used, work procedure step by step
How To Make A Veranda With Your Own Hands To The House - Instructions, Projects, Drawings, Photos And Videos
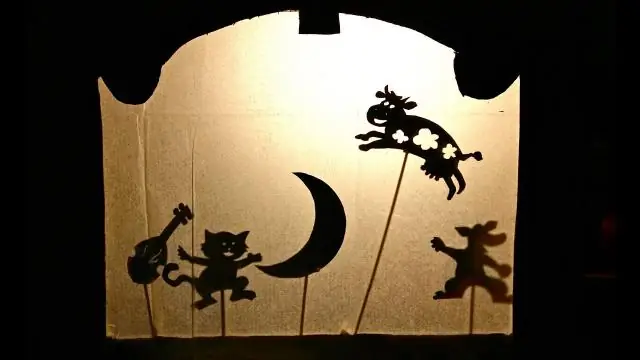
The article describes how to build a veranda close to the house with your own hands
How To Choose And Build A Foundation For A Bath With Your Own Hands - 4x6, 3x4 And Other Sizes, Tips, Instructions, Photos And Videos
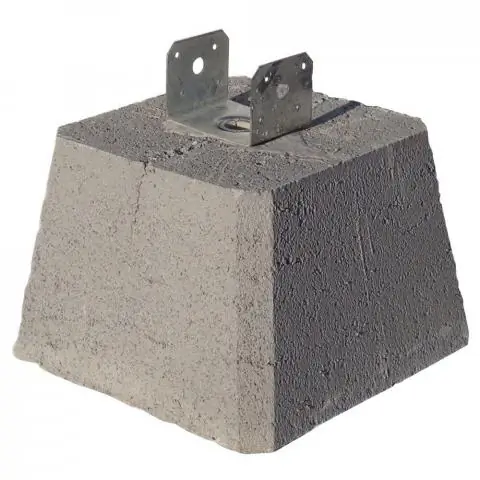
How to make a foundation for a bath with your own hands. Types and features of foundations. The choice of materials and technology, installation rules and step-by-step instructions
How To Build A Warm Chicken Coop For The Winter With Your Own Hands - Instructions With Photos And Videos
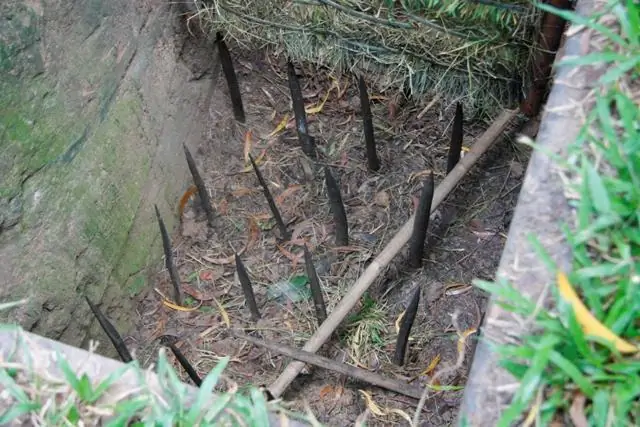
The need to insulate the chicken coop. What material can be used. How to make a winter poultry house yourself: step by step instructions. Treatment and care
How To Make A Birdhouse Out Of Wood With Your Own Hands: Options With Drawings And Diagrams + Photos And Videos
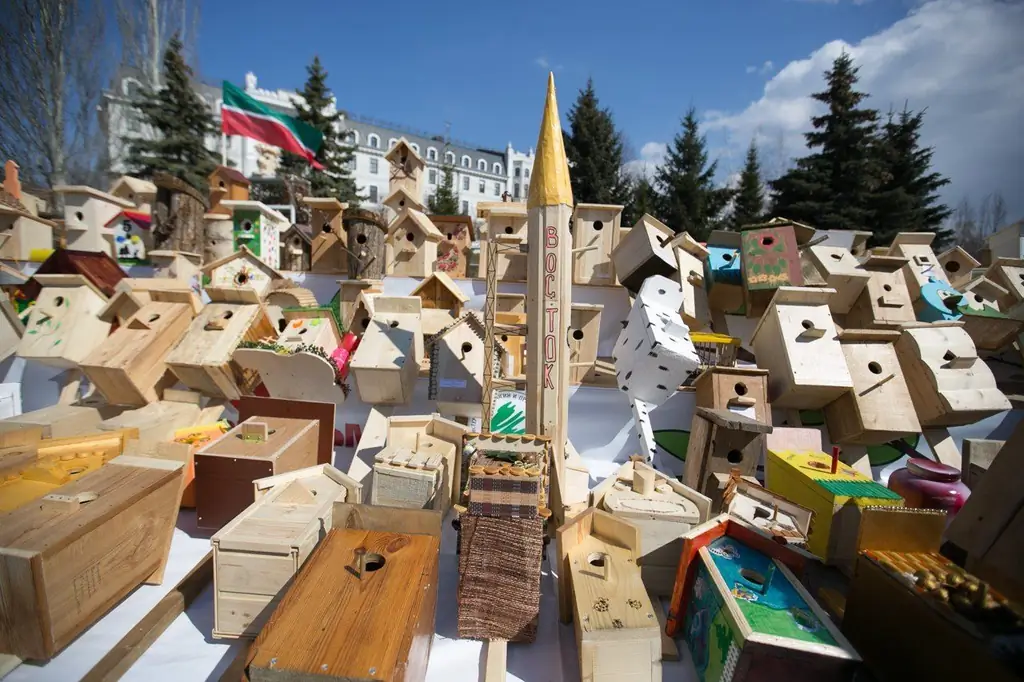
How to make a wooden birdhouse with your own hands. The right tree, the necessary materials and tools, drawings, step-by-step manufacturing instructions. Video