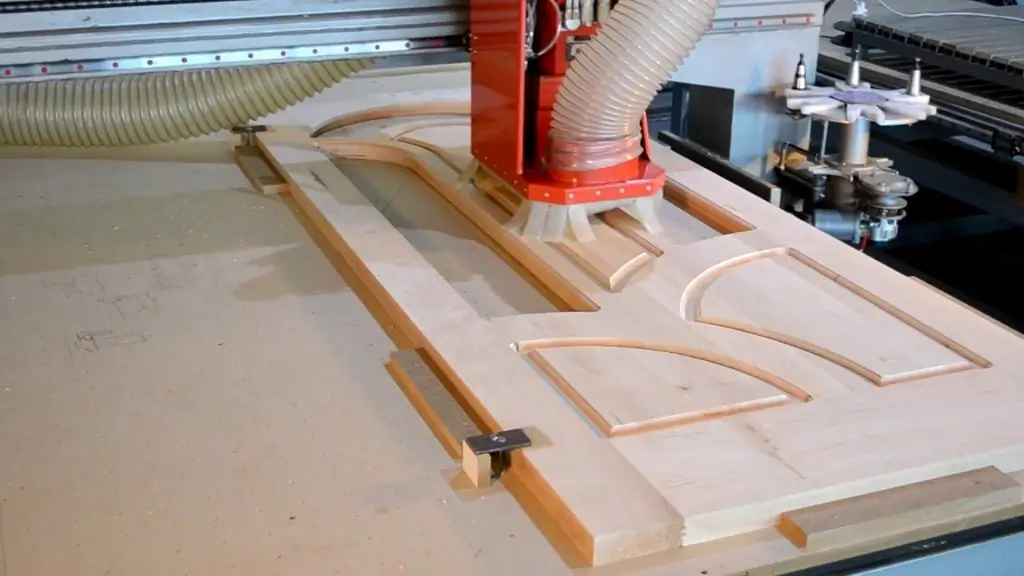
Table of contents:
2025 Author: Bailey Albertson | [email protected]. Last modified: 2025-06-01 07:32
Production of interior doors
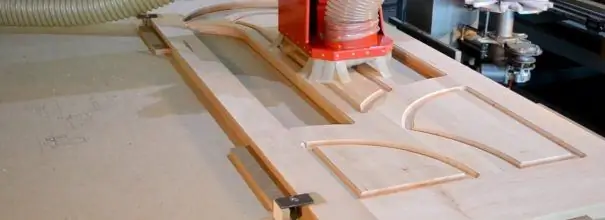
Interior doors are a necessary part of residential, industrial and office premises. When choosing door leaves and additional elements, you need to know how and according to what rules they are made, as well as understand the advantages and disadvantages of the materials used in the production of doors. Modern manufacturers use high-tech equipment that allows them to produce a large number of high quality products with various types of coatings and with modern designs.
Content
-
1 Manufacturing technology of interior doors
1.1 Video: making doors from solid wood
- 2 Rules and regulations for the production of interior doors
-
3 Current GOSTs for the production of interior doors
3.1 Table: ratio of the dimensions of the opening to the dimensions of the door leaf
- 4 Material for the manufacture of interior doors
-
5 Equipment for the production of interior doors
5.1 Video: production of interior doors
Manufacturing technology of interior doors
Doors serve to separate various functional parts of the room and provide sound insulation, protection from extraneous odors and excess moisture. The manufacturing methods for door leaves and additional elements depend on the materials used in the production. The most popular doors are made of solid wood or prefabricated on a wooden frame. Glass inserts make the canvas partially permeable to light and visually expand the space of rooms or corridors.
The most complex and multi-tier technological process takes place in the manufacture of doors using wooden elements. The fact is that timber that has not gone through the full cycle of preliminary drying and processing is prone to warping and cracking. To avoid losses in the quality of the final product, it is necessary to pay great attention to the preliminary preparation of wood using certain technological methods. The process of manufacturing interior doors includes the following steps:
-
Pine timber (round timber) is cut into blanks using band saws with automatic log feed.
Sawing round timber Logs are sawn into workpieces of the required thickness
-
The blanks are processed with high temperature and steam in drying chambers to avoid uneven drying and warping of wood. At the end of the drying process, a mandatory moisture control is performed.
Drying chambers for wood Drying of lumber is carried out under the influence of steam and high temperature
-
The dried workpieces are cut into bars of a technological section and defective fragments (chips, knots, cracked and rotten areas) are removed from them, which can affect the quality of the door frame and door leaf.
Cutting and troubleshooting of blanks Defective areas are cut out of the workpiece cut into a bar
-
Then the workpieces are spliced using spikes, glue and a vertical press into a shield, from which, after drying and trimming, a door leaf is obtained.
Gluing blanks into a shield Using a vertical press, a panel blank of a door leaf is obtained
- After grinding, the sheet is covered with three-layer veneer or MDF-panels with one veneer layer and placed in a gluing press.
-
At the next stage, shaped decorative elements, panels or openings for glazing are cut out with a milling and engraving machine, and after assembly, the door leaves are covered with three layers of varnish with intermediate and final grinding.
Door assembly Panel elements or glazing are mounted during final assembly
- After final drying, the products are packed, if necessary, supplied with fittings and sent to the consumer.
The technological sequence of manufacturing doors may be different and it depends on the material, equipment and product design. For example, for expensive doors made of solid valuable wood species, the use of veneer is not typical and they are made using complex CNC machines, and in budget doors, corrugated cardboard inserts and cheap lamination film are often used.
It is important to note that in the factory, the hardware is usually not installed on doors with symmetrical decor, since during installation at the consumer's site, the product can open both to the left and to the right, respectively, the hinges and handles are installed by installers locally
Video: making doors from solid wood
Rules and regulations for the production of interior doors
Door blocks are manufactured on equipment that is located in significant production areas. Certain requirements are imposed on these premises as to industrial facilities, which include timber warehouses, dryers, a processing shop, a paint and varnish section and a finished product warehouse. Each production site is equipped according to the rules and regulations, in accordance with the technical conditions for a specific task. The main requirements for production facilities for the manufacture of doors are the following criteria:
- availability of free access roads;
- buildings should be provided with stable temperature, humidity, natural and artificial lighting;
- electricity, heating, ventilation, water supply and sewerage must be equipped;
- premises must be equipped with fire alarms, fire extinguishing equipment and emergency exits;
- at workplaces, it is necessary to ensure safe working conditions;
- paint and varnish areas should be isolated from the rest of the premises and equipped with forced ventilation.
The personnel are obliged to undergo professional training and education in labor protection, fire and electrical safety, as well as to undergo unscheduled, repeated and initial instructions at the workplace.
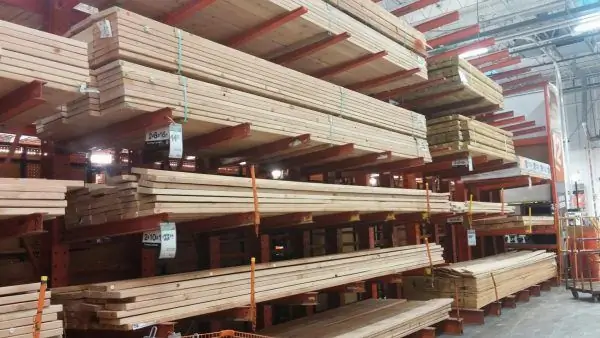
The production area must be equipped in accordance with standards
The main standard for the production process is the technological documentation, which is based on the Technical specifications for the production of TU 5361-001-58037723-2015 "INTERIOR DOORS, PARTITIONS AND RUNNING PRODUCTS TO THEM." This document sets out the requirements for the design of interior doors, the quality of the material and coating of the front surface, as well as environmental requirements. The regulations specify the order of acceptance of finished products, certification and installation of the warranty period.
It is important for the buyer to have a certificate, a warranty period and the compliance of the door, frame and additional elements with the requirements of technical conditions, since this confirms the quality of the product and allows you to count on a long service life
Current GOSTs for the production of interior doors
The technical characteristics of the doors are determined by standards that set the general technical conditions or methods for determining the physical parameters and dimensions of the finished product. Many manufacturers create products in non-standard sizes, but with strict adherence to quality requirements. The consumer may be interested in the list of regulatory standards used by manufacturers of interior doors, namely:
- General requirements for wooden doors with a list of regulatory documents are established by GOST 6629-88, and requirements for wood products are set out in GOST 475-78.
- Design options for interior doors, their types and sizes are specified in GOST 24698-81.
- Requirements for completions, fasteners and hinges are assigned by GOST 538-88.
- Methods for determining sound insulation, heat transfer resistance and air permeability are regulated by GOST 26602.
- Determination of the flatness of the door leaf is carried out according to the ST SEV 4181-83 standard.
- The reliability test procedure is set out in ST SEV 3285-81.
- Resistance to shock loading is performed according to the method specified in ST SEV 4180-83.
The accompanying documents for the finished product must contain a symbol for the door leaves, for example, U05195 VERSAL pat. 1014 dec / oro door leaf D3 91x 230 L, which means the following door parameters:
- article - U05195;
- the trade name of a particular collection is VERSAL;
- type of finish / color - pat. 1014 dec / oro;
- product name - canvas;
- product model - D3;
- width and height of the canvas - 91x230;
- opening type, left - L.
Before ordering doors, it is necessary to carefully measure the doorways in order to select the required frame size, door leaf and the required number of additional elements. For interior doors, there are standard dimensions of openings with the corresponding designation according to SNiP and this approach facilitates the selection of the door frame according to the table.
Table: ratio of the dimensions of the opening to the dimensions of the door leaf
Designation according to SNiP | Opening height range, mm | Opening width range, mm | Blade size, mm |
21-7 | 2050-2100 | 670-720 | 2000x600 |
21-8 | 2050-2100 | 770-820 | 2000x700 |
21-9 | 2050-2100 | 870-920 | 2000x800 |
21-10 | 2050-2100 | 970-1020 | 2000x900 |
21-13 | 2050-2100 | 1300-1320 | 2000x600 (2 pcs.) |
The existing regulatory documents guarantee a high level of product quality, standardization in size and compliance with environmental requirements, in addition, the consumer can determine the conformity of the product properties declared by the manufacturer to the quality and price level
Material for the manufacture of interior doors
In the production of interior doors and partitions, modern materials are used that are environmentally friendly, durable, lightweight and have a long service life. These include metal-plastic and glass doors, the frame for which is an aluminum profile, and the filler is plastic panels or tempered triplex glass with a matte finish. But traditional doors with a timber frame and inserts of glass, MDF panels and panels occupy the main niche in the market. In the manufacture of such products, the following materials are used:
- Pine timber cleaned from defects with a moisture content of not more than 8%, spliced into a thorn using glue pressing.
- High density particle board.
- Natural veneer made of various types of wood, 0.6 mm thick.
-
Laminating film imitating precious wood species.
Laminating film Laminating film gives doors a natural wood grain
- MDF panels of various thicknesses are used for cladding door leaves and creating panel elements.
- Frosted glass, triplex or tempered, used for light-diffusing and decorative inserts in the door leaf.
-
Corrugated cardboard is used in budget options, as soundproof inserts in the canvas between the frame beams.
Corrugated board Corrugated cardboard is used for insulation and sound insulation of inexpensive door leaves
- Wax and waterproof coatings, tinting compounds and varnishes.
- Glue of the type "Kleiberit 303.2", MERITIN Glue D3 and others, is used for industrial gluing of fragments of sheets, door frames and additional elements.
The production of inexpensive doors is based on the use of chipboard, laminated film, corrugated cardboard and MDF, while more expensive products use solid wood with milled elements, panels and tempered glass inserts.
Six years of experience in operating veneered paneled doors by the author of the article shows their significant reliability. But in rooms with high humidity, I would like to recommend various types of laminated doors with an additional waterproof coating. After four years of service in the bathroom on the internal veneer, despite the treatment with liquid wax twice a year, whitish streaks and drips from exposure to steam and condensate appeared. There was a need for cosmetic repairs, so it was necessary to sand the plane of the door leaf, degrease it with a solvent, cover it with a tinting compound and waterproof varnish in two layers. To a lesser extent, the same problem appeared in the laundry room, and as for the rest of the doors, minor damage to the veneer and scratches were removed by gluing and processing with hard,tinted wax of various shades. After such minor repairs, the canvases, boxes and accessories acquire their original appearance and serve for more than six years. Under the conditions of summer cottage use, wooden doors covered with waterproof varnish serve for more than eight years. At the same time, warping and drying out does not occur in conditions of temperature drops and changes in humidity. But it should be noted that the best option for summer cottage construction are metal-plastic doors and boxes that do not change properties and retain their geometry under changeable weather conditions. At the same time, warping and drying out does not occur in conditions of temperature drops and changes in humidity. But it should be noted that the best option for summer cottage construction are metal-plastic doors and boxes that do not change properties and retain their geometry under changeable weather conditions. At the same time, warping and drying out does not occur in conditions of temperature drops and changes in humidity. But it should be noted that the best option for summer cottage construction are metal-plastic doors and boxes that do not change properties and retain their geometry under changeable weather conditions.
Equipment for the production of interior doors
The most expensive production of interior doors, in terms of the amount of equipment required, is the manufacture of wood products. Manufactured products from metal-plastic and glass require a large number of components and a small number of machines for cutting frames and processing glass sheets. Processing of lumber is more saturated with machines, presses and other equipment. Consider the equipment that is used for the production of wooden doors:
-
Sawmills and band saws used for cutting round timber.
Band sawmill The sawmill allows you to get lumber of the required thickness from the round timber
-
Steam chambers for drying lumber.
Drying chambers Industrial drying chambers allow you to bring lumber to the required moisture level and avoid warping of blanks
- Equipment for the production of veneer.
-
Tenoning machine for frame and door leaf.
Tenoning machine The machine is designed for cutting thorns on wooden blanks
-
End, thermal vacuum and pneumatic presses for gluing door leaf elements.
Press for gluing door elements Using a pneumatic press, the door leaf is glued
- Circular saws and panel saws for cutting workpieces to size.
-
Copy-milling machines with programmed control for decorating door leaves.
Milling engraving machines Shaped and paneled elements are produced using milling machines
- Grinding machines for intermediate and finishing of products.
- Paint and varnish equipment.
The list of the production park can be expanded due to the use of various technological and design solutions in the production of interior doors and component parts, which has a positive effect on the consumer properties of the final product.
Video: production of interior doors
youtube.com/watch?v=Z-vE_LnHJnw
We examined some types of interior doors, production technology, as well as regulatory documents and requirements governing products of this type. For the correct choice of doors, it is necessary to know the properties of the coating and the material from which they are made. High-quality equipment and adherence to production technology ensures resistance to external influences and a long service life of products. A wide range of design solutions allows you to give the living space an individual look and unique style.
Recommended:
Interior Laminated Doors And Their Varieties With A Description And Characteristics, Advantages And Disadvantages, As Well As Use And Compatibility In The Interior
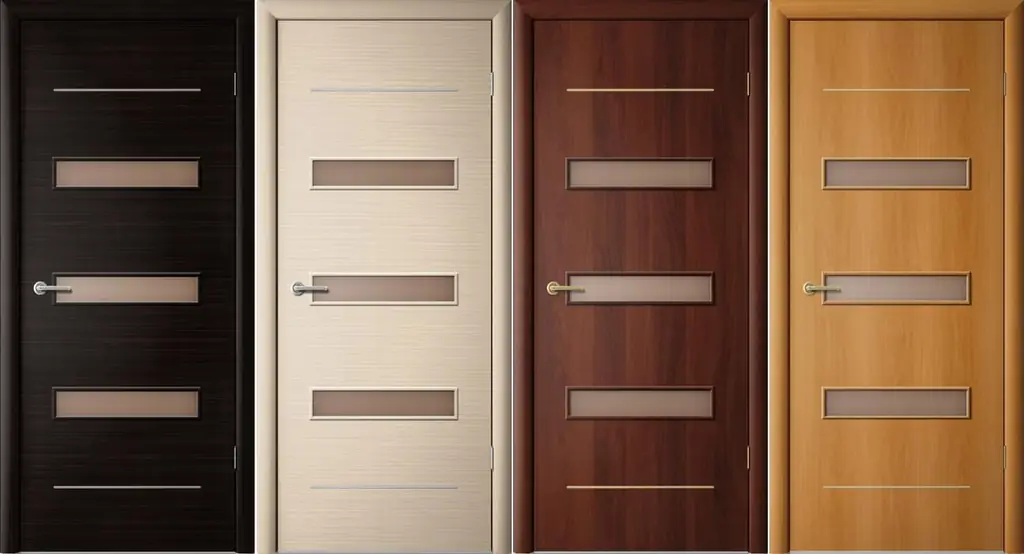
What are laminated doors: varieties and their characteristics. How to choose and install doors. Tips for the operation and repair of laminated doors
MDF Doors: Entrance And Interior Doors, Their Varieties With A Description And Characteristics, Advantages And Disadvantages, As Well As Installation And Operation Features
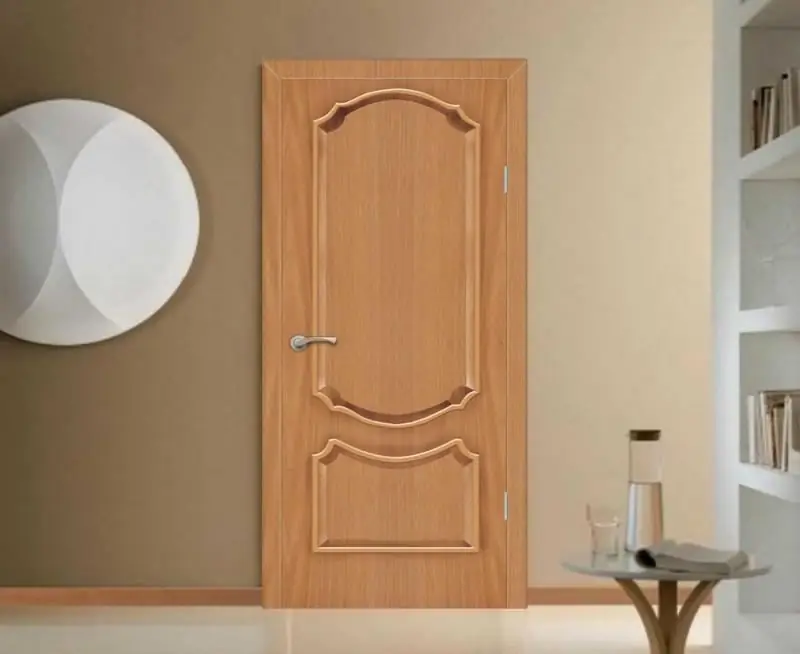
Doors from MDF: features, characteristics, varieties. Making and installing MDF doors with your own hands. Door restoration. Reviews, photos, videos
Types Of Interior Doors With A Description And Characteristics, Depending On The Material Of Production And Design Features
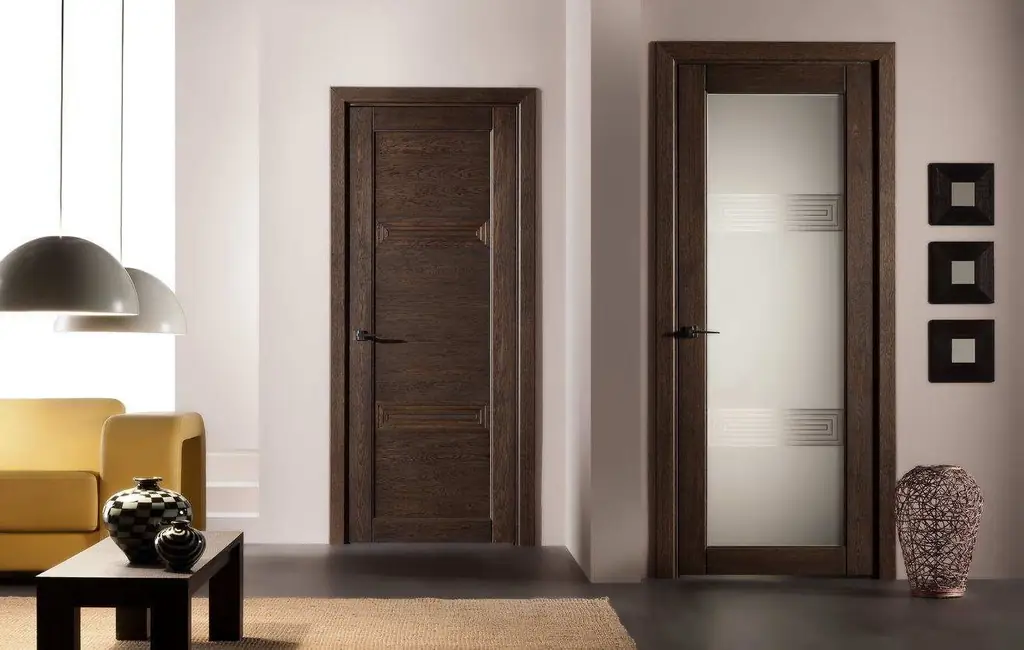
How interior doors are arranged and what materials they are made of. Characteristics and features of different models of interior doors
Moving A Gas Pipe In The Kitchen: Features, Rules, Requirements And Recommendations
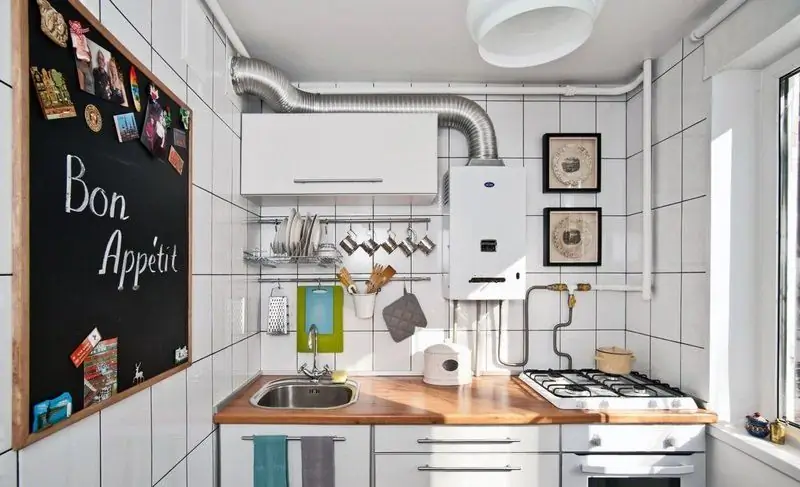
Norms and rules for the location of gas pipes in the apartment. Procedure for transferring pipes. Obtaining a permit, work technology, leak testing
How To Wean A Cat From Dry Food: Basic Weaning Rules And Common Mistakes, Advice From Owners And Veterinarians
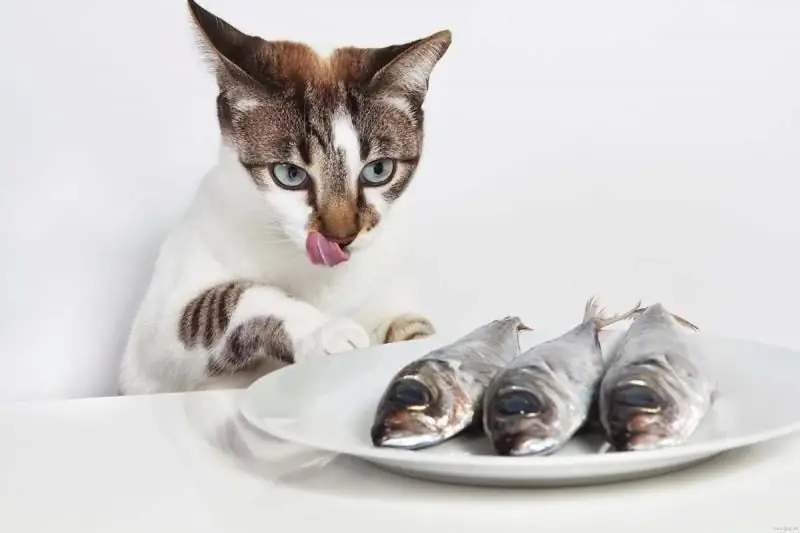
When is it necessary to transfer a cat from dry food to natural food. Possible difficulties. Stages of translation. The main mistakes when changing the diet. Reviews