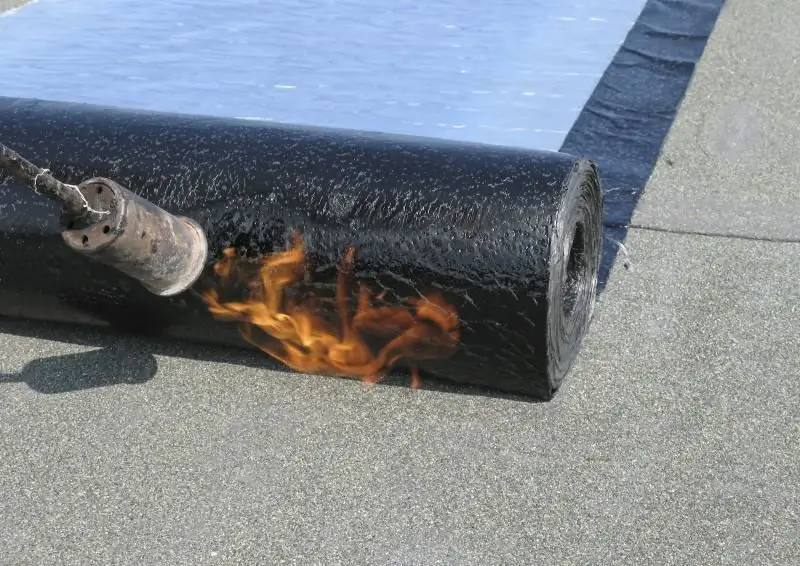
Table of contents:
2025 Author: Bailey Albertson | [email protected]. Last modified: 2025-06-01 07:32
How to choose a roll roofing material and make a roof with your own hands
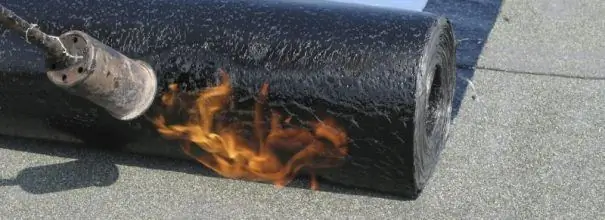
Roofing is a crucial moment in the construction of a country house. The comfort of living in it or the possibility of using the building for its intended purpose depends on the quality of this operation. Roofing mistakes are fraught with significant financial losses.
Content
-
1 Roll roofing materials - what is it
- 1.1 Photo gallery: roll roofs
- 1.2 What are the types of roll roofing materials
- 2 On the advantages and disadvantages of roll materials
-
3 Characteristics of some materials
- 3.1 Materials based on bitumen and bitumen-polymer mixtures
- 3.2 "Filisol"
- 3.3 Technoelast
- 3.4 Self-adhesive roll roofing materials
-
4 How to choose roll roofing material
4.1 Video: choosing roll roofing material
-
5 Roof device
5.1 Video: installation of a soft roll roof
-
6 Dismantling the roof
6.1 Video: how to remove old layers of roofing material from the roof
Roll roofing materials - what is it
When building a country house, one of the main tasks is to create a beautiful and durable roof. You can make the roof aesthetically attractive by using roll roofing materials. As practice shows, they are the easiest to use, and a properly arranged roof can work up to 25 years. The repair of such a roof is also simplified, in which it is not necessary to dismantle the old coating, but it is enough to install patches in the places of leaks.
Roll roofing materials are widely used for roofs with a slope angle of 10-30 degrees. Such a coating is convenient for both pitched roofs and complex-shaped roofs. The roll cover perfectly takes root both on small country houses and on presentable cottages.
Photo gallery: roll roofs
-
Pitched roof made of rolled materials - Modern roll materials look beautiful and reliably protect the roof from leaks
-
Roll roofing made of profiled material - Some weld materials look like shingles
-
Flat roll roof - Before laying roll materials, the roof must be insulated
-
Roof made of bitumen-polymer materials -
Roll materials based on fiberglass can be used in most climatic zones of our country, except for the coldest
What are the types of roll roofing materials
Roll-shaped soft roofing materials are widely represented in the building materials market, and their range continues to expand. Moreover, they have a variety of technical characteristics.
According to the method of application, roll coatings can be conditionally divided into the following categories:
- Soft coatings in the form of rolls, which are glued to the base during installation using polymer or bituminous mastics.
- Materials with a self-adhesive surface on the back. To install them, it is enough to remove the protective film from the surface and press it against the prepared base.
-
Products melted onto the roof with gas burners.
Fused roll materials Gas-fired roll roofing materials are often used to cover flat and pitched roofs
The quality indicators of roll roofing materials are regulated by GOST 30547-97, which stipulates all the technical characteristics of these products.
Classification by type of base is as follows:
- By the type of panel used in the production - with a base or baseless.
- By the types of bases used, which can be asbestos, fiberglass, cardboard and polymer.
- According to the types of external coating, roll materials are divided into polymer, bituminous or polymer-bitumen.
- According to the composition of the protective coating, they can be foil-coated, with a film coating or with a powder.
The very first representatives of the class of roll coatings are roofing material and rubemast. They have long been used for roofing and are still relevant to this day. The reasons for their popularity are their low cost and quite acceptable durability.
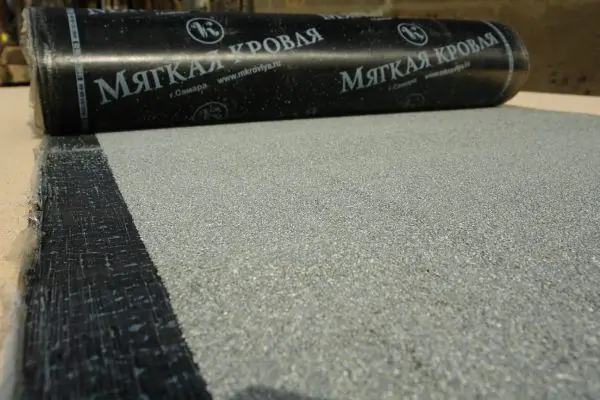
Rubemast is an improved version of roofing material and has a service life of up to 15 years due to the use of special additives and plasticizers
On the advantages and disadvantages of roll materials
To fully assess the possibility of using roll materials for roofing, you need to consider the main positive properties of this class of coatings:
- Low weight. Roll materials can be easily delivered to the installation site even without the use of lifting mechanisms. Installation requires little effort when unrolling the rolls.
- Wide range of uses. The material can be used on roofs with any slope of the slopes, in hard-to-reach places and in areas with a complex configuration with adjustment to the installation site.
- Lack of noise during operation in any type of precipitation.
- High tightness rates. Correctly laid roll material is a monolithic coating that does not allow water to pass through under any operating conditions.
-
Simple installation. Laying a floor does not require special knowledge, and the necessary skills are developed very quickly.
Laying roll roofing on bituminous mastic Some coatings do not even require gas burner skills
- UV resistant. The material with bulk protection does not deteriorate under the influence of sunlight.
- Simple repair of the coating, associated with the possibility of sealing leaks without dismantling the old coating using local patches.
- Environmental friendliness of the material. Rolled coatings do not emit harmful substances into the surrounding space.
The negative sides include:
- The difficulty of obtaining high tightness. When installing a roof covering, it is necessary to strictly comply with all the requirements of the technological process, avoiding the formation of air bubbles and loose material adjoining at the joints.
- The use of hot work when installing the roof. On some types of bases (wood, plywood, board made of combustible materials), heating with open fire is prohibited. Building hair dryers can be used.
-
Difficulty in determining the places of roof leaks - the defect may be far from the place of its manifestation. It is determined only visually.
Roll roof defect Over time, the roll material may come off, in such places it is necessary to put patches
Characteristics of some materials
Among all the abundance of roll materials on the market, several groups can be distinguished.
Materials based on bitumen and bitumen-polymer mixtures
These are, as a rule, weldable products, which are based on glass fabrics or non-woven glass cloth. When using elastic polyester bases, a material with a relative elongation of 16-30% of the original size is obtained. These products include:
- isoelast;
- isoplast;
- bikroplast;
- bikroelast;
- dneproflex;
- filisol and many others.
The breaking force for such materials when stretched is 30-60 kg. The limiting parameter for Russian conditions can be fragility at temperatures from 25 degrees below zero.
One of the best materials for roof waterproofing is the Technoelast coating developed by the Russian company TechnoNIKOL. Its characteristic feature is the high hydrophobicity of the coating at the joints of the canvases. For this, the technology of diffusion welding was developed. When used, scattered canvases turn into a continuous coating. In the production of technoelast, not only polymer-bitumen compositions are used, but also artificial rubber, which allows obtaining higher strength characteristics.
This material can be used in most climatic zones. It also has enhanced waterproofing properties due to the use of front and back polymeric films. Its thickness can be up to four millimeters. The mass of a square meter of material is 4.9 kg. The breaking force is 60 kg in length and 40 kg in width.
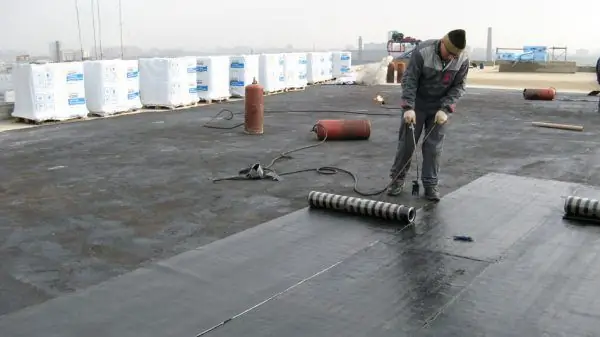
Technoelast, like many other roll roofing materials, is applied by fusion
Filisol
This is the contribution of Russian manufacturers to a wide range of roll roofing materials. Considering the conditions of their operation in harsh climatic conditions, it uses SBS-type thermoplastic elastomer, which made it possible to obtain a competitive material, one of the best in the modern line of similar products.
Filisole is based on fiberglass or polyester fabric coated on both sides with a polymer-bitumen binder with thermoplastic elastomer.
This material is characterized by the following features:
- Versatility. The combination of a high-strength base and an elastic binder makes it possible to use both a thermal method (fusion) and mechanical fastening of strips during installation. This allows the material to be used when constructing roofs on which the use of open fire is prohibited.
- Cost-effective for fusion mounting. A special mastic layer with high elasticity and adhesion rates can significantly save energy when installing such a coating.
-
Reduction of labor intensity when laying mechanically. The high strength base allows the coating to be used in one layer.
Roll coating "Filisol" Filisol was developed specifically for harsh operating conditions, so it can be used at temperatures from 50 degrees below zero
Technoelast
It is a unique roofing material for creating a breathable roof. Often, swellings are observed on a new coating, formed when moisture evaporates under it. The cause may be moisture from the screed or insulation layer. Elimination of such defects is carried out by opening the bubbles and applying a patch to the damaged areas.
This situation can be avoided by using rolled roofing material "Technoelast". In terms of the device and the components used, it differs little from standard products, but the lower plane is arranged in an original way. The adhesive is applied continuously on its surface, but there are streaks with sprinkling along the canvas. When glued to the base, such material adheres to the sticky layer, and the loose areas are channels for moisture escape.
Fastening of rolled technoelast is performed mechanically.
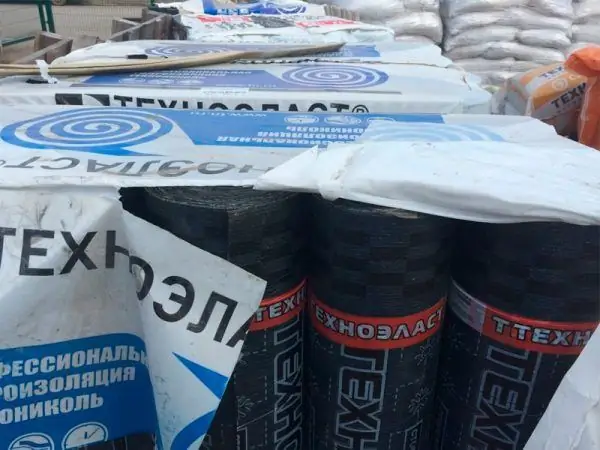
Roll material "Technoelast" allows you to make a roof without air bubbles
Self-adhesive roll roofing materials
Self-adhesive materials differ from ordinary polymer-bitumen sheet by the presence of a sticky layer on the bottom surface. Structurally, the fabric consists of a polyester base with a reinforcing fiberglass mesh. On both sides, it is covered with a polymer-bitumen composition with the addition of thermoplastic components. Then an adhesive is applied and covered with a protective film.
When installing, it is enough to remove it and lay the material on the base of the roof, rolling it with an elastic roller. This flameless technology allows the coating to be used on fire-hazardous (wooden) substrates.
Rolls can be laid at temperatures up to +5 o C, but in the range of 5-15 o C, its surface must be heated with a construction hairdryer with an air stream temperature of about 400 degrees.
The operating temperature range is -50 to +60 o C.
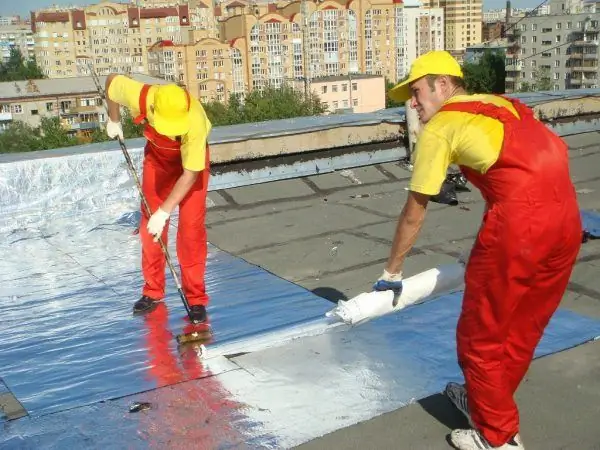
Self-adhesive materials can be used on any roofs, including fire hazardous
How to choose roll roofing material
When deciding which material to use for the roof, the following circumstances must be considered:
- The architectural design of the roofing system. The choice of roofing material depends on the angle of inclination of the slopes, the complexity of the shape and geometry. It is necessary to take into account the attractiveness of the coverage and its compliance with other objects on the site.
- What matters is the magnitude of the load on the building's rafter system, and, consequently, its final pressure on the foundation.
- Requirements for the durability of the structure. The decisive factor in this case is the type of structure. For example, the roofing requirements for a residential building are somewhat different than for a summer kitchen.
Regardless of the emergence of new roofing materials, roll coatings are still very popular. This is primarily due to their lower price.
Video: choosing roll roofing material
Roof device
For roofing, various roll materials with sprinkling are used - glass and ordinary roofing material, roofing felt, tar-bituminous products, as well as non-covering materials such as waterproofing or glassine.
Roof manufacturing technology is divided into two main stages - preparatory and main.
Preparatory operations include the following:
-
Cleaning the surface from debris and dirt.
Roof surface preparation Before laying roll materials, the roof surface must be cleaned of debris and remnants of the old coating
- Rewinding rolls of topcoat with simultaneous cleaning of loose powder.
- Preparation of mastic.
- Preparation of the necessary tools.
There are cold and hot mastics. The first of them are obtained by mixing dewatered bitumen with fillers from fluff lime, asbestos fibers and others. Diesel oil is used as a solvent. The binder is also dewatered bitumen or pitch, the fillers are the same.
The main technological processes include:
-
Laying vapor barrier and insulation. In this case, drain funnels are installed.
Insulation of a flat roof Roof insulation can be done with mineral wool, polymer or sprayed materials
- Application of paint vapor barrier - hot or cold, layer thickness 2 mm. The glued vapor barrier is arranged over a layer of hot mastic by gluing sheets of glassine.
-
Screed device made of cement-sand mortar or cast sandy asphalt concrete.
Flat roof screed On the laid heat-insulating plates, a screed with a concrete mixture with the obligatory laying of a reinforcing mesh is performed
- At the junctions of the screed to vertical surfaces (sides, pipes), an interface with a radius of up to 50 mm is performed to ensure high-quality adhesion of the topcoat.
-
The screed surface is primed with bitumen diluted in a 2: 1 ratio. It needs to be done a few hours after its filling.
Screed priming with bitumen The priming is performed a few hours after the concrete screed has set.
-
Gluing sheets of roll coating. It is produced by applying mastic and rolling out the coating sheets. They need to be pressed to the base and rolled in with a roller. For overlay application, gas burners are used.
Installation of roll roofing Fusion of the topcoat from roll materials is carried out using gas burners
Roofing works are carried out at a temperature not lower than -20 o C. In this case, the supporting surface must be warmed up to +5 o C. This is an energy-intensive operation, therefore, in practice, roofing works are carried out only in the warm season.
The mastic is supplied to the place of work heated to a temperature of about 180 o (for hot) and 70 o for cold. When working on pitched roofs, the roll material is rolled along the slope from bottom to top with an overlap between the individual sheets of at least 10 cm.
Video: device of a soft roll roof
Dismantling the roof
In order to build a reliable new roof, in some cases it is necessary to dismantle the old coating.
In this case, certain conditions must be observed:
- Suitable outside temperature. It is preferable to carry out work at a temperature not higher than 20 o C. Under these conditions, the roofing materials will not soften excessively and will be removed without destruction.
- To complete the work, you will need tools - a chasing cutter and roofing axes.
- The work should be performed by well-trained people, as it requires a lot of effort.
Dismantling is carried out in the following order:
- With a layer thickness of up to three centimeters, the roof is cut into squares up to half a meter in size. For this, a wall chaser is used. The parts are separated from the base of the roof with roofing axes, using them as wedges and levers.
- With a thicker roofing cover, it is cut down with axes. A roofing ax is a common tool on which a wooden handle is replaced by a metal one made of a steel pipe with a diameter of about 40 millimeters. It is welded to the ax on the butt and serves as a lever when undermining the chopped parts.
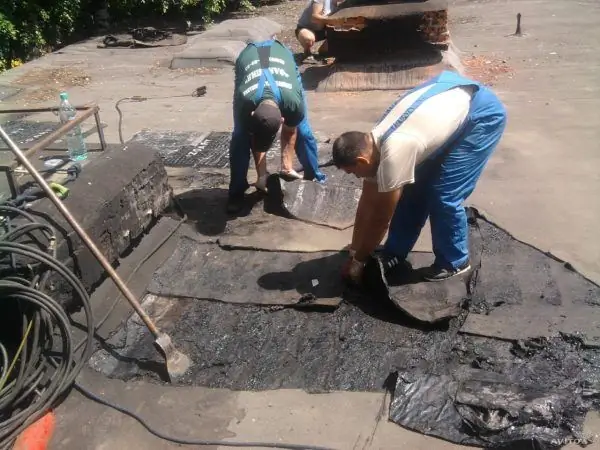
A roofing ax is used to remove the old coating.
The old roofing material removed from the roof is stored in containers for further disposal.
Video: how to remove old layers of roofing material from the roof
The quality of the house covering ensures its long-term operation and comfortable living in it. The choice of a soft roll roof is reasonable from the economic point of view, but requires special attention to the quality of performance. Therefore, do-it-yourself work is best done with the participation of an experienced master.
Recommended:
Types Of Roofing Materials With A Description And Characteristics And Reviews, Including Roll, As Well As Features Of Their Operation

Types of roofing materials: sheet, soft and tile roofs. Technical characteristics and features of operation of various types of coatings
Roofing Profiled Sheet, Including Its Types With Description, Characteristics And Reviews, As Well As Processing And Use Features
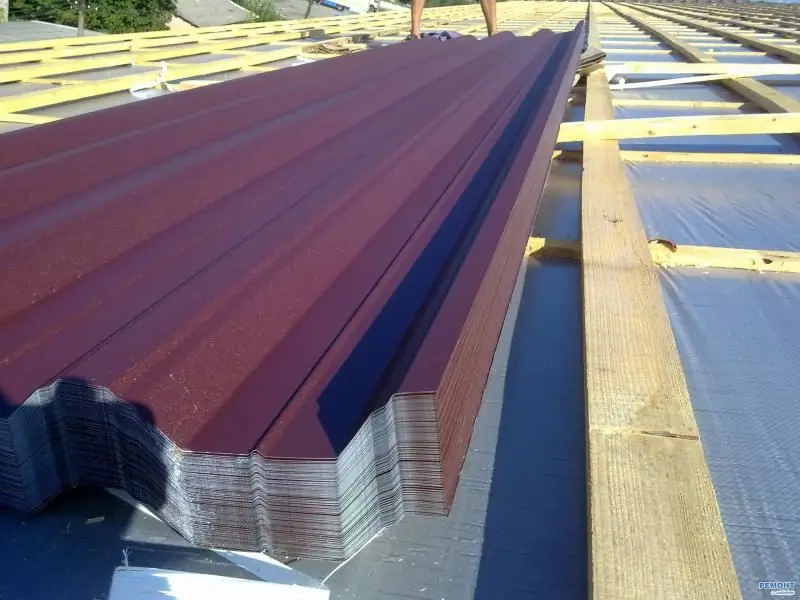
Using a profiled sheet to cover the roof. Classification, features of work and operation of corrugated board. How to cut a profiled sheet into fragments of the desired size
Types Of Roofs With Descriptions, Characteristics And Reviews, As Well As Features Of Installation And Operation
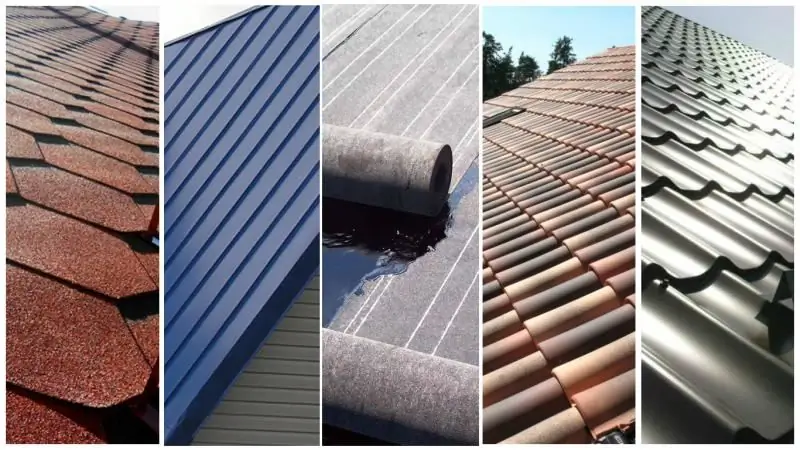
A variety of roofing materials used in private and multi-storey buildings. Description, characteristics, installation and operation of different types of roofing
Roofing Sheeting, Including Types And Brands With Descriptions, Characteristics And Reviews
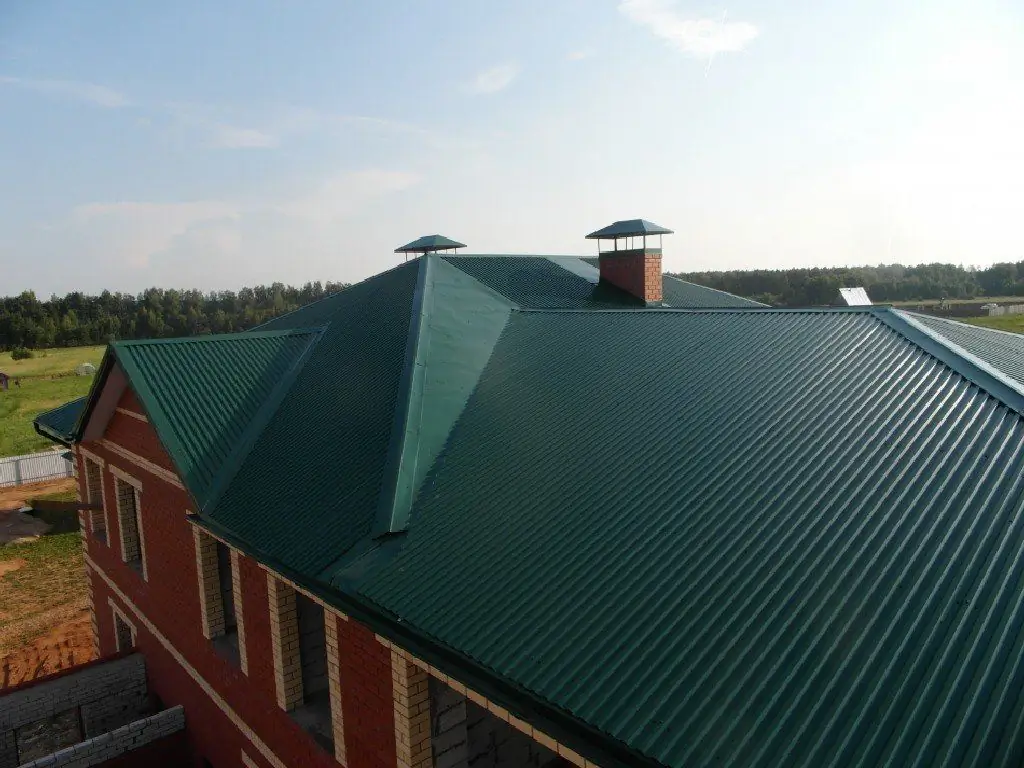
What kind of corrugated board is considered roofing. Features of different brands. Types and advantages of corrugated board. How to choose it and calculate the required amount. Reviews
Roof Vapor Barrier And Its Types With Description And Characteristics, Features Of Materials And Installation
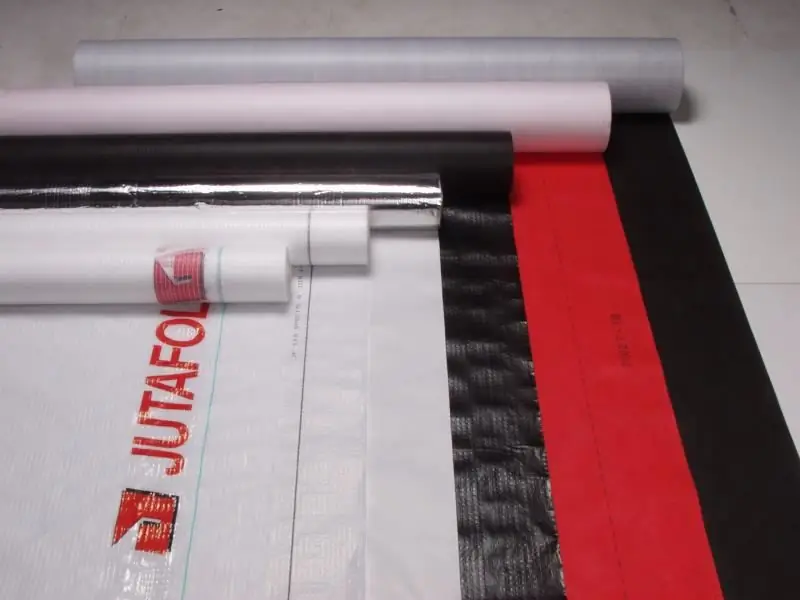
Roof vapor barrier, its types, description and characteristics. Features of materials for roof vapor barrier. Installation methods for each of the materials