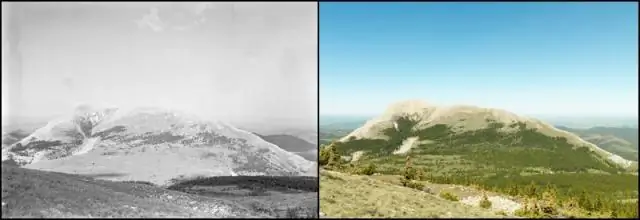
Table of contents:
- How to make a greenhouse according to Meathlider with your own hands
- What is it, description of the structure, difference from conventional greenhouses
- Greenhouse according to Mietlider: calculations and project drawings
- Choice of material, advice when buying
- Calculation of the required amount of material, required tools
- Do-it-yourself step-by-step instructions for building a Mitlider greenhouse
- Tips for finishing
2025 Author: Bailey Albertson | [email protected]. Last modified: 2025-06-01 07:32
How to make a greenhouse according to Meathlider with your own hands
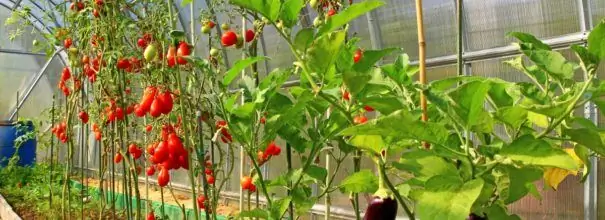
One of the main criteria for proper growth and productivity of agricultural crops is effective ventilation of the greenhouse. In agricultural practice, different types of greenhouses are used, however, to create a favorable microclimate, it is better to use a greenhouse of a special design, like the Mitlider greenhouse. Given the simplicity of this structure, it is quite possible to build it yourself.
Content
- 1 What is it, a description of the design, the difference from conventional greenhouses
- 2 Greenhouse according to Mietlider: calculations and project drawings
-
3 Choice of material, advice when buying
- 3.1 Cellular polycarbonate
- 3.2 Table: pros and cons of cellular polycarbonate
- 3.3 Timber frame
- 3.4 Table: pros and cons of wood
- 3.5 Frame made of polypropylene or polyvinyl chloride
- 3.6 Table: pros and cons of greenhouses, the frame of which is made of polypropylene or polyvinyl chloride pipes
- 3.7 Metal frame
- 3.8 Table: Advantages and Disadvantages of Mitlider Greenhouses with a Metal Frame
-
4 Calculation of the required amount of material, required tools
- 4.1 Calculation of the foundation
- 4.2 Calculation of cellular polycarbonate
- 4.3 Design of reinforcement
- 4.4 Timber calculation
- 4.5 Required tools
- 5 Step-by-step instructions for building a Mitlider greenhouse with your own hands
-
6 Tips for finishing
6.1 Video: we build our own greenhouse
What is it, description of the structure, difference from conventional greenhouses
The greenhouse according to Meathlider is a cubic or arched greenhouse. Thanks to the special design of the roof slopes and the location of the ventilation windows, a high-quality air exchange takes place inside such a structure.
The American doctor of agricultural sciences Jacob Meatlider proposed to make a gable roof in such a greenhouse, with a ventilation hole, in which each inclined plane is located at a different height.
These design features distinguish the Meatlider greenhouse from simple greenhouses. Ordinary greenhouses are ventilated with open doors. In this case, some of the warm air stagnates under the ceiling, creating an unfavorable atmosphere. In the Mitlider design, warm streams freely exit through the ventilation in the roof, being replaced by fresh air masses.
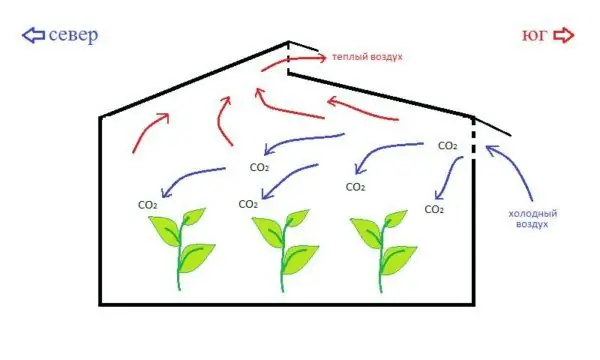
Simple yet effective design
Mitlider's greenhouses in the form of arches have become very popular. The design of this form is much easier to manufacture, and it is more convenient to maintain it. Thanks to the rounded shape of the ceiling, warm air currents are better removed, leaving room for fresh air.
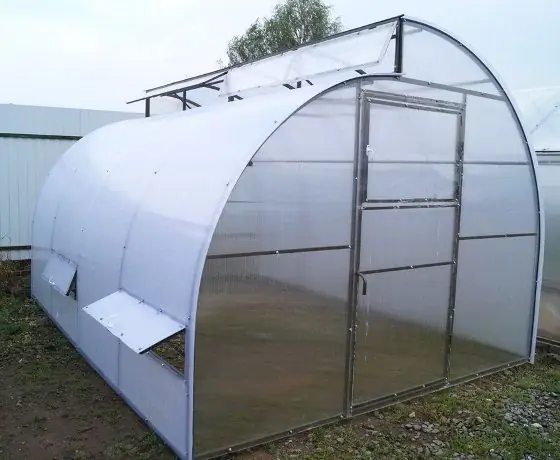
Arched structure
Greenhouse according to Mietlider: calculations and project drawings
Before carrying out all construction activities, it is necessary to choose the right place for the construction of this structure. The area for the Meatlider greenhouse should be well lit by the sun. For building, it is preferable to choose land with a flat surface. The site needs to be cleared of debris, stones and roots.
If the greenhouse is to be built on a slope, then care must be taken to create terraces. The walls of such steps must be reinforced in order to avoid slipping of soil masses.
The standard dimensions of this greenhouse are 6 m in width, 12 m in length, and 2.5 to 2.7 m in height. These parameters determine the classic version of the structure, but are not limiting. This makes it possible to build a greenhouse in accordance with the size of the site. The optimal material for covering it is cellular polycarbonate.
Any construction, even as simple as a greenhouse, requires drawing up drawings and diagrams.
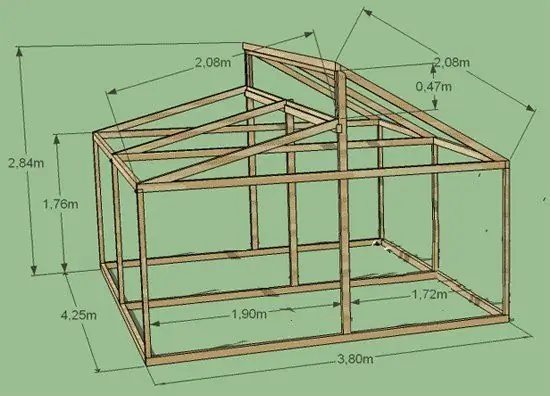
Optimal parameters
Choice of material, advice when buying
The durability of the structure and the properties of the microclimate inside it depend on the correctly selected material. Since the light-penetrating cover is placed on all sides of the Meatlider greenhouse, it is extremely important to select a quality material for this.
Cellular polycarbonate
The most popular and effective coating for greenhouses and greenhouses is cellular polycarbonate.
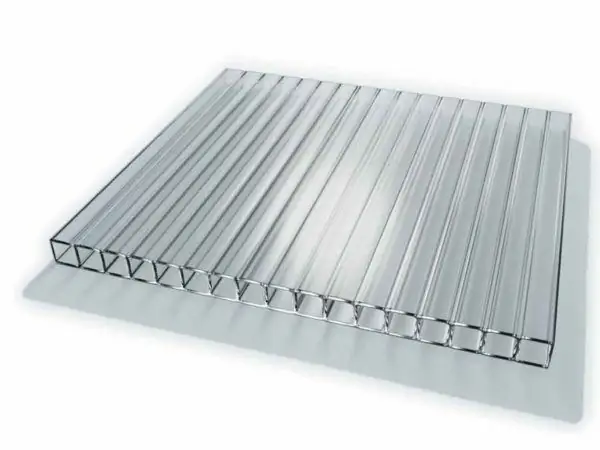
Transparent option
When choosing cellular polycarbonate used for structures of this kind, you need to pay attention to the following points:
- Thickness of sheets and their light transmission. For the Mitlider greenhouse, polycarbonate with a thickness of 6 to 8 mm should be used. These material parameters are most suitable for creating a favorable microclimate inside the greenhouse. A sufficient amount of sunlight necessary for the normal life of plants penetrates through such sheets. In the cold months of the year, walls made of material with such parameters prevent the rapid cooling of the air inside the greenhouse. For regions with cold climates, it is necessary to use material with a thickness of 8 to 10 mm. Cellular polycarbonate 4 mm thick is not used for such greenhouses and greenhouses, since its thermal insulation properties do not meet the requirements of growing. Thin sheets are more suitable for decoration and finishing work. The light transmission of this material is almost as good as glass, which is only 10% lower.
- Resistant to moisture, sunlight and temperature extremes. When purchasing a coating, you need to inquire about its chemical composition and characteristics. Preference should be given to more expensive polycarbonate, since a cheap material after a while can fade in the sun, cloudy from water or crack after the first winter. To avoid these unpleasant moments, a protective film layer is applied to the material. In any case, you will have to buy a high-quality and, accordingly, expensive coating.
- Flexibility. This criterion is especially important in the manufacture of arch-type structures.
- Thermal insulation qualities. If you choose high quality material, then there is no need to use additional insulating layers.
- Manufacturer. Today, the following companies are well-known manufacturers of cellular polycarbonate:
- Polygal is an Israeli manufacturing company that pioneered this type of product;
- Palram is a joint German and Israeli company;
- Brett Nartin is an English firm;
- Polygal Vostok is a Russian-Israeli manufacturer.
Despite the effectiveness and popularity of cellular polycarbonate, this material has advantages and disadvantages.
Table: pros and cons of cellular polycarbonate
Benefits | disadvantages |
|
|
For the frame, wood is used, as well as pipes made of metal, polypropylene or polyvinyl chloride. Each material is widely used for the construction of such greenhouses, however, their individual characteristics differ significantly.
Wood frame
Due to the high humidity inside the greenhouse, the wooden frame will quickly become unusable. Mold and fungal formations will appear on all elements and details of such a structure. In this regard, before using the material for the construction of greenhouses and greenhouses, it must be treated with special antiseptic impregnations, mastics and biocides. An important condition for such substances is the absence of toxic compounds that will poison the soil and crops. Therefore, the wooden frame of greenhouses is treated with oil-based preservatives.
An important role is played by the type of wood, which is more resistant to the specific environment of the greenhouse. For this purpose, it is necessary to use bars of oak, hornbeam, beech, spruce, pine.
Also, during the acquisition, you need to inspect the bars in order to detect traces of woodworm insects.
Bars should not contain many knots, cracks and wood chips.
Table: pros and cons of wood
pros | Minuses |
|
|
Frame made of polypropylene or polyvinyl chloride
These materials are plastic alloys. Polyvinyl chloride (PVC) or polypropylene (PP) pipes are used for the manufacture of water supply and sewer channels. This material is used in mechanical engineering, electrical engineering, construction. Due to their properties, such pipes are used in the construction of greenhouses and greenhouses.
The main criterion for choosing such pipes is their stiffness and wall thickness. Too thin pipes will not hold their shape well.
Table: pros and cons of greenhouses, the frame of which is made of polypropylene or polyvinyl chloride pipes
Benefits | disadvantages |
|
The low weight of the greenhouse is not only a positive, but also a negative quality, since strong wind currents can deform or overturn it |
Metal carcass
The designs of greenhouses according to the Mitlider from metal tubes have become very popular. This material allows you to make structures of any shape.
Table: advantages and disadvantages of greenhouses according to Mitlider with a metal frame
Benefits | disadvantages |
|
|
Calculation of the required amount of material, required tools
To exclude unnecessary costs or troubles with a lack of materials, it is necessary to make a calculation by their quantity. For the construction of a greenhouse according to Mitlider, a project with a frame made of wood with a polycarbonate coating was chosen. The structure will be located on a concrete foundation (strip or pile). The greenhouse will be manufactured with dimensions: height - 2.7 m, width - 3 m, length - 6 m.
Foundation calculation
To lay the foundation, you will need concrete of the M 200 brand, sand, reinforcement and roofing material.
Sand poured into the trench and poured concrete will have the shape of an elongated parallelepiped. To calculate the volumes of these materials, you need to remember the school geometry course and use the formula for finding the volume of a cube, which looks like this: V = h³, where h is the width, height and length of the figure.
For convenience, calculations will be made separately for each side of the perimeter, and the results will be added
The sand will be poured into a 200 mm wide trench with a 100 mm layer height. These figures need to be converted to meters. Let's substitute the values: 0.2 ∙ 6.0 ∙ 0.1 = 0.12 m³ sand is required for one side of the foundation 6 m long. Since there are two of these sides, then: 0.12 ∙ 2 = 0.24 m³.
Now you need to calculate the volume of sand on two sides with a length of 3 m. To do this, subtract the width of two-perpendicular belts (0.2 m each) from three meters: 3.0-0.4 = 2.6 m. Calculate the volume of sand for these sides: 0.2 ∙ 2.6 ∙ 0.1 = 0.052 m³. Since there are two of these sides: 0.052 ∙ 2 = 0.104 m³.
Add up the volumes of the sides: 0.24 + 0.104 = 0.344 m³ material will be required to create a sand cushion of a concrete base.
The same formula is used to calculate the volume of concrete mix. The width of the foundation tape will be 0.2 m, height 0.3 m. As in the first case, calculations will be made separately for each side of the perimeter. We make a calculation: 0.2 ∙ 0.3 ∙ 6.0 = 0.36 m³. We multiply this value: 0.36 ∙ 2 = 0.72 m³, concrete is required for both sides of the foundation 6 m long.
We make the calculation on two sides of the base, the length of which is 3 m. Substitute the values: 0.2 ∙ 0.3 ∙ 2.6 = 0.156 m³. We multiply this figure by two: 0.156 ∙ 2 = 0.312 m³.
Now it is necessary to add up the results of calculations on all sides of the perimeter of the concrete base: 0.72 + 0.312 = 1.032 m³, concrete mix will be required to fill the strip foundation of the Mitlider greenhouse.
Calculation of cellular polycarbonate
To determine the total number of polycarbonate sheets, it is necessary to make calculations for each side of the greenhouse. For calculations, you need a formula for calculating the area of a rectangle, which looks like this: S = a ∙ b, where a is the height of the figure, b is its length.
Let's make a calculation for two sides, each 6 m long. Substitute the values: 6.0 ∙ 2.2 = 13.2 m². Since the structure has two similar sides: 13.2 ∙ 2 = 26.4 m².
Calculation for two sides with a length of 3 m: 3 ∙ 2.2 = 6.6 m². Multiply by half: 6.6 ∙ 2 = 14.52 m².
Let's carry out calculations for the roof. First, we calculate the roof section with parameters 1.87x6.0 m. Substitute the values: 1.87 ∙ 6.0 = 11.22 m². Now for the second roof section: 1.55 ∙ 6.0 = 9.3 m².
Having calculated the areas of all sides of the structure, it is necessary to add the obtained values: 26.4 + 14.52 + 11.22 + 9.3 = 61.44 m².
Sheets of cellular polycarbonate must be purchased with a margin, since this material will be required for finishing the sides of the roof, vents and doors.
Reinforcement calculation
To strengthen the strip base, it is reinforced with metal rods. For this, reinforcement with a thickness of 0.8 cm is used. A volumetric frame is made from it, in which the rods are fixed with connecting elements made of a similar material. The size of one such part is 15x20x15x20 cm or 70 cm in total length. These elements are located in the frame at a distance of 30 cm from each other.
With these values, it is easy to calculate the total amount of material. Since each side of the perimeter will be reinforced with four horizontal rods, then: (6 ∙ 4) + (3 ∙ 4) = 24 + 12 = 36 m.
Now you need to find out how many connecting elements are required for the entire perimeter: 36: 0.3 = 120 pieces. To find out the total length of all elements, you need: 120 ∙ 0.7 = 84 m.
The total length of all reinforcement for strengthening the foundation: 36 + 84 = 120 m.
Timber calculation
The design of the greenhouse according to Mitlider provides for the presence of vents (transoms) located at the junction of the roof slopes, as well as on the sides. In a structure 6 m long, a solid transom or several separate vents are usually made. This length of the greenhouse allows you to make 4 vents 150 cm long, 30 cm high. The sides of the greenhouse are equipped with two or three vents with these parameters.
To make the frame of the greenhouse, you will need wood of the following sizes:
- For the manufacture of vertical racks - bars, section 100x150 mm, length 220 cm, in the amount of 18 pieces.
- For the supporting frame (roof) - bars with a similar section, 270 cm long, in the amount of 4 pieces.
- To make a rafter system, you will need material with a cross section of 55x80 mm: 5 bars 200 cm long and 5 more pieces 140 cm each.
- For the manufacture of the lower strapping, bars with a section of 100x150 mm are required: 2 6 m long and 2-3 m long.
- For the upper strapping, bars are needed with the same length, but with a section of 100x100 mm.
- For the manufacture of vents, bars with a section of 60x60 mm are required:
- 14 pieces 150 cm each;
- 14 - 30 cm each.
-
For the manufacture of doors, bars with the same section:
- 4 pieces 200 cm long;
- 4 - 75 cm each.
Required tools
During the construction of the Mitlider greenhouse, you will need the following tools:
- Bayonet and shovel.
- Concrete mixer.
- Water tanks.
- Concrete pouring sleeve.
- Hacksaw.
- A hammer.
- Screwdriver.
- Yardstick.
- Plumb line.
- Building level.
- Large square.
- Sander or sandpaper.
- Molar brush.
- Bulgarian.
- Perforator.
- Jigsaw and fine-toothed saw.
- Sharp construction knife.
- Cord with stakes.
- Pencil or marker.
Do-it-yourself step-by-step instructions for building a Mitlider greenhouse
After making calculations and purchasing all the necessary materials, you can start building a greenhouse along the Mitlider:
-
Make markings on the prepared plot of land. To do this, you need to pull the cord, which is fixed to the stakes. In order for the shape of the future foundation to have a strictly outlined (rectangular) shape, it is necessary to check the markings. To do this, a cord is pulled diagonally from the corners of the perimeter. If the intersection is in the middle of the rectangle, then the markup has been done correctly.
Foundation markings A stretched cord will not let you go wrong
- Around the perimeter of the marking, dig a trench 20 cm deep and 20 cm wide. Its bottom must be tamped, and the walls must be leveled.
-
Pour sand inside the trench so that a layer 10 cm thick is formed. Tamp it. It should be noted that wet sand is better compressed.
Greenhouse foundation trench The walls and the bottom must form a 90-degree right angle
- On top of the sand cushion, lay a waterproofing layer around the entire perimeter. For this, roofing material or thick polyethylene, folded in several layers, is used. Waterproofing should cover not only the top of the sand layer, but also the walls of the trench.
-
Make formwork from boards, plywood sheets or OSB boards. The height of its side should be at least 25-30 cm. To prevent the formwork structure from falling apart under the pressure of uncured concrete, it must be strengthened. To do this, use various spacers and stops.
Formwork for the foundation Stops will hold the structure
-
To strengthen the strip base, it must be reinforced. To do this, make a volumetric frame from reinforcing rods 0.8 cm thick. The intersections can be secured by welding or twisted with wire. The connecting elements are made of the same material. Therefore, you will need a grinder to cut them. They look like a rectangle, the dimensions of which are 15x20 cm. These parts must be located at a distance of 30 cm from each other inside the entire perimeter of the reinforcing frame. It should be noted that the metal structure should not touch the waterproofing layer. Therefore, it is installed on bars or fragments of bricks, 3-5 cm high.
Reinforcing frame of the foundation Will strengthen the base
-
The concrete base can now be poured. To do this, you need to use a mixture of the M 200 brand. To make it easier for yourself when pouring, you need to use a special sleeve, through which the mixture will go directly into the formwork. The incoming concrete mixture must be raked off with a shovel. Thus, air bubbles are removed from the liquid foundation, and the concrete is evenly laid inside the trench. The mixture must completely cover the metal structure. The height of the strip base is 30 cm. Its upper part will rise 20 cm above the ground level. It should be noted that the filling must be carried out immediately along the entire perimeter. Layer-by-layer filling of the mixture is allowed.
Strip foundation The best option for this type of structure
- When the concrete base is poured into the formwork, it must be covered with a waterproofing material. Such a layer will prevent the rapid evaporation of moisture, and protect it from drying out in the sun. It should be noted that the first two days, every 10-12 hours, you need to open the waterproofing for 20-30 minutes. This will ensure uniform hardening of the concrete mixture. After 4-6 days, the foundation will completely solidify.
-
When the strip base becomes solid, it is necessary to remove the formwork. Clean the upper surface of the base from debris, dust and protruding particles.
Hardened strip foundation The base is ready for the construction of the frame
- Lay a layer of roofing material on top of the concrete tape. It will protect the wooden frame from moisture.
-
From beams with a section of 100x150 mm, make a rectangular frame of the lower strapping. The joints of the material should be made in a half-tree method. Fasten the bars with nails.
Bottom rail of a wooden structure Half-tree connection
- Install the bottom trim on the foundation.
-
Drill holes in the corners of the lower trim to install the anchor bolts. Such holes must be made every 120-150 cm. The bolts will hold the entire structure.
Securing the bottom harness to the foundation Anchor bolt used
-
Install the corner posts of the frame (timber 100x150 mm). To keep them upright, it is necessary to use pins and slopes.
Installation of corner posts The head will hold the rack
-
Install the rest of the racks. The distance between them should be 75 cm. Wood joints must be reinforced with metal corners.
Connecting timber frame elements Used metal corner
-
Make the upper harness from beams with a section of 100x100 mm. To do this, in a bar, every 75 cm, make grooves for complete cutting. The result will be a part that must be installed on the upper ends of the vertical posts.
Methods for installing ordinary frame racks The type of connection of the posts affects the height of the structure
-
Install 4 roof supports.
Installation of roof supports The structure will serve as a frame for the vents
-
Make and install vents and doors from bars with a cross section of 60x60.
Manufacturing of vents The optimal size of the vents
-
Install the rafter system using bars with a section of 55x80 mm, lengths 200 and 140 cm. Use metal plates and corners as connecting elements.
Installing the rafter system The step between the rafters must be the same
- Using a jigsaw and a fine-toothed file, cut the polycarbonate sheets to the required length.
-
Using an electric drill, prepare holes in these sheets, for further screwing them to the wooden frame. To fix this material, you must use self-tapping screws with a rubber gasket. During installation, the polycarbonate sheets must not be strongly clamped with self-tapping screws. Having a cellular structure, this material is easily damaged. When installing this coating, it is important not to confuse the inner and outer surfaces of the material, since only one side of it is covered with a protective film.
Self-tapping screws for working with polycarbonate The gasket will protect the material and create a waterproofing layer
-
After installing polycarbonate, it is necessary to check the entire structure in order to eliminate cracks and gaps in the coating.
Ready greenhouse according to Mitlider Polycarbonate coated
Tips for finishing
Since a microclimate favorable for growing is organized inside the Mitlider greenhouse, it is necessary to effectively use every centimeter of the inner space. The growing surface can be placed on more than just the floor.
Wood or plastic can be used to make racks or shelves to grow any kind of crop.
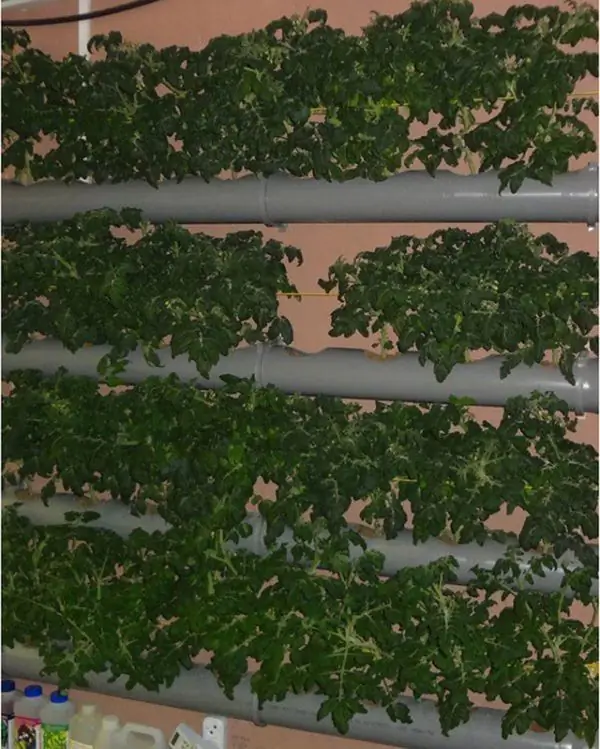
Used PVC pipes
Large diameter PVC pipes are a convenient alternative to such structures. This material is cut lengthwise. The result is a gutter, into which you can pour soil and grow useful herbs.
PVC pipes can be used in a vertical position if you cut round holes at a short distance from each other, and plant, for example, strawberries inside.
Watering of such a bed will be carried out through a tube with small holes of a smaller diameter inserted into the middle of the main pipe. The space between the pipes is covered with earth. Such a bed will not take up much space.
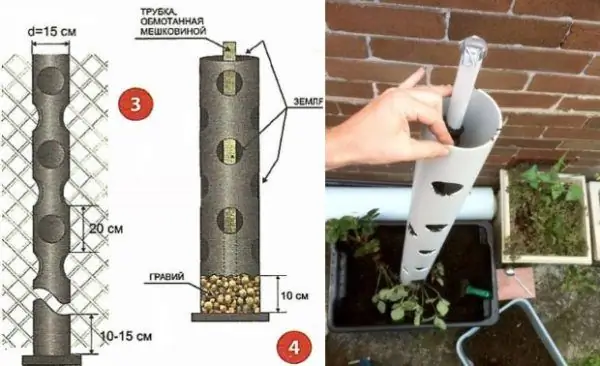
Convenient and efficient
In this greenhouse, you can stretch the cords vertically to provide direction for the growth of tomatoes, cucumbers, beans or other vegetables.
Video: we build our own greenhouse
Having built a Mitlider greenhouse with your own hands, you will organize high-quality ventilation and a favorable microclimate for grown garden crops. The reward for your efforts will be a bountiful harvest.
Recommended:
How To Build A Wooden Porch With Your Own Hands: In Stages, Photos And Videos
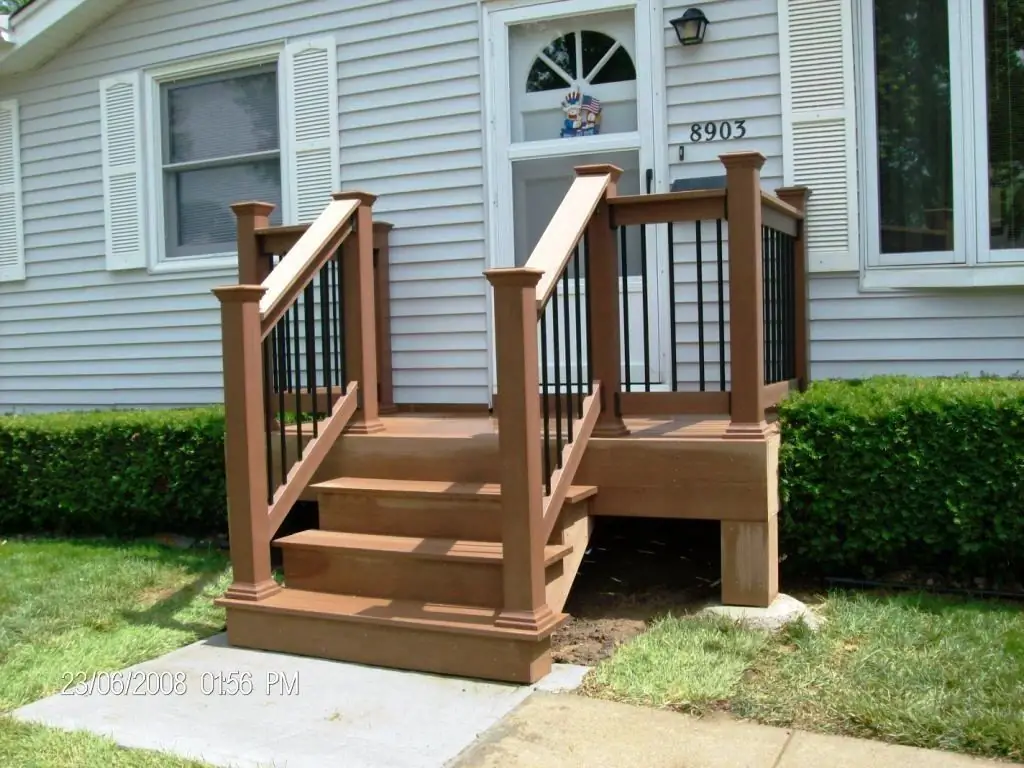
Detailed description of the construction of a wooden porch. Materials used, work procedure step by step
How To Make A Veranda With Your Own Hands To The House - Instructions, Projects, Drawings, Photos And Videos
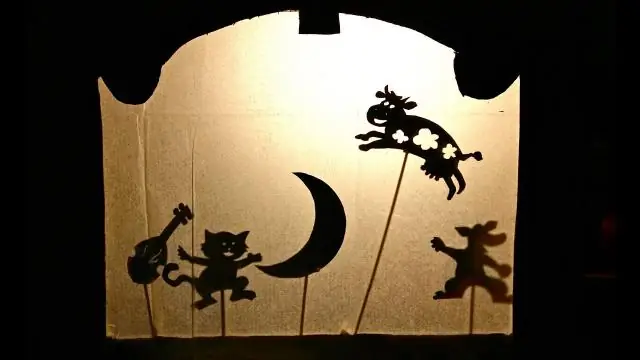
The article describes how to build a veranda close to the house with your own hands
How To Choose And Build A Foundation For A Bath With Your Own Hands - 4x6, 3x4 And Other Sizes, Tips, Instructions, Photos And Videos
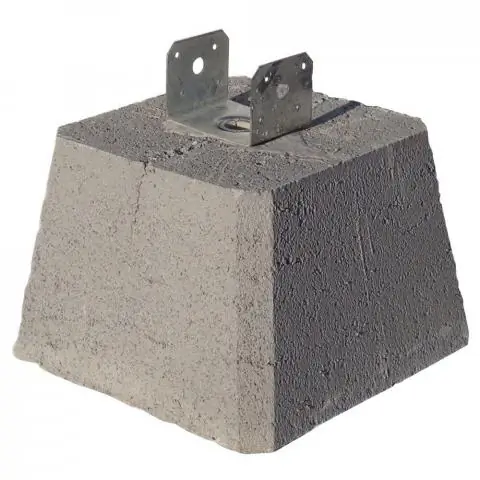
How to make a foundation for a bath with your own hands. Types and features of foundations. The choice of materials and technology, installation rules and step-by-step instructions
How To Build A Warm Chicken Coop For The Winter With Your Own Hands - Instructions With Photos And Videos
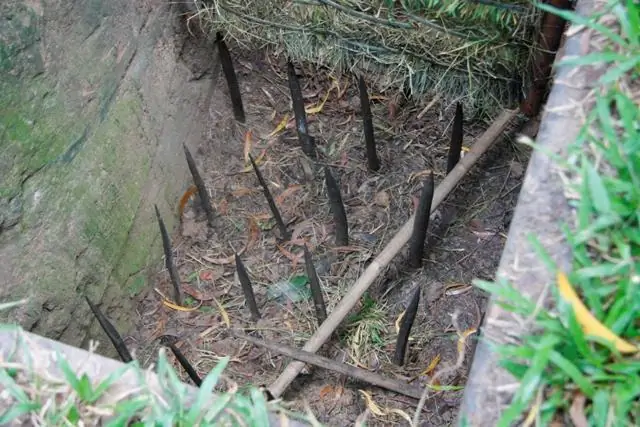
The need to insulate the chicken coop. What material can be used. How to make a winter poultry house yourself: step by step instructions. Treatment and care
Making Interior Doors With Your Own Hands, As Well As How To Choose Material And Make Calculations
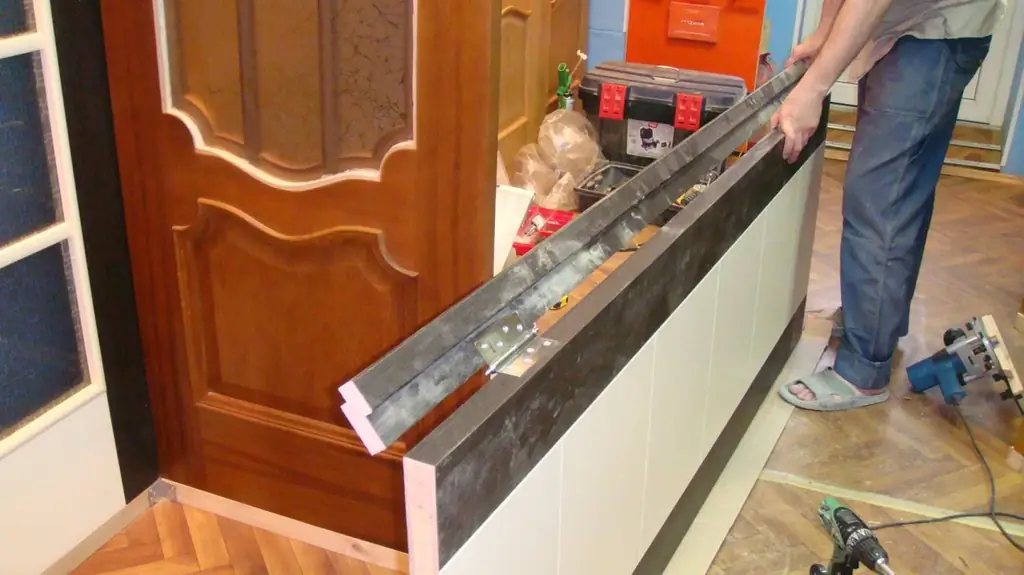
Tools and materials for the manufacture of interior doors. Manufacturing technologies for interior doors. Varieties of internal wooden doors