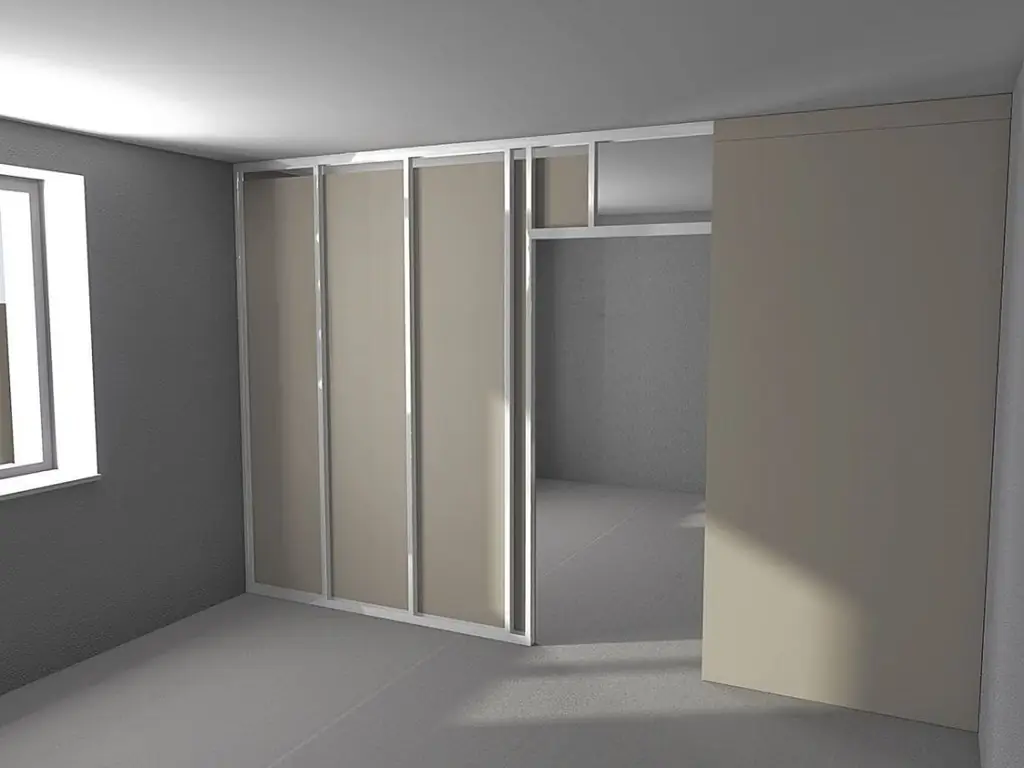
Table of contents:
2025 Author: Bailey Albertson | [email protected]. Last modified: 2025-06-01 07:32
DIY plasterboard partition
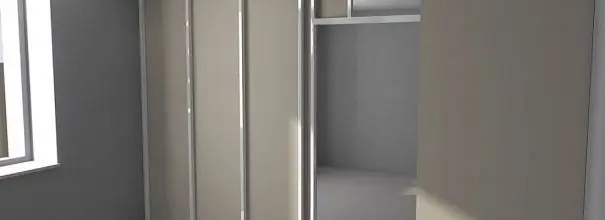
Usually, the question of dividing living space into zones arises with an increase in the number of family members. Growing children require separate square meters. Elderly parents, and they are sometimes like children, also want to have their own territory. Easily and simply, at no extra cost, the technology of erecting partitions made of plasterboard, a material that is absolutely environmentally friendly, sound-absorbing and inexpensive, will solve these problems.
Content
-
1 In which rooms are plasterboard partitions used?
1.1 Photo gallery: the use of drywall for the construction of partitions
- 2 Design features of a plasterboard partition, pros and cons
-
3 Tools required for the manufacture of partitions from gypsum board
3.1 Table: Consumption of materials with a distance between the post profiles of 0.6 m
-
4 Making a drywall partition with your own hands
-
4.1 Layout and layout
4.1.1 Video: how to mark the partition from the gypsum board
- 4.2 Installation of battens
- 4.3 Sheathing of the frame with thermal and sound insulation
-
4.4 Putty and finishing of the partition
- 4.4.1 Video: plasterboard putty
- 4.4.2 Video: do-it-yourself drywall partition
-
- 5 Reviews
In which rooms are plasterboard partitions used?
It is no exaggeration to say that walls, ceilings and partitions made of gypsum boards are used today in all branches of civil construction. The advanced technology brought to us from Western Europe is used not only in the residential sector, but also in production areas.
In 2014, at the legislative level, norms and rules for the construction of gypsum plasterboard structures were developed and enshrined in a document called SP 163.1325800.2014 “Structures using gypsum plasterboard and gypsum fiber sheets. Design and installation rules”
Private developers have long appreciated the benefits of dry construction. The use of finished factory products, sometimes called "dry plaster", allows you to bypass the most unpleasant aspects of housing construction - an abundance of construction waste, corrosive dust, dirt, heavy fumes from cement mixtures. With the correct use of technology, gypsum plasterboards are a versatile material. It can be used almost anywhere, even in office equipment with high humidity levels.
Correct waterproofing and a competently laid layer of ceramic tiles on top of a moisture-resistant sheet (GKVL) allows you to arrange partitions in kitchens, toilets and bathrooms.
Photo gallery: the use of drywall for the construction of partitions
-
Plasterboard partition in the living room -
An elegant partition made of light gypsum plasterboard divides the living room space into recreation areas
-
Drywall partition in the bedroom - The combination of a partition with stylized shelves fits seamlessly into the interior
-
Drywall partition in the toilet - Distinguishing between toilet and bathroom in the bathroom improves the level of comfort
-
Plasterboard partition in the children's room - Divide the children's room into several functional zones will allow the original partition from the gypsum board
Features of the construction of a plasterboard partition, pros and cons
The plasterboard partition consists of a metal frame sheathed in one or two (and sometimes three) layers with gypsum board sheets. The surface layer is putty with gypsum mortar and covered with paint or pasted over with wallpaper.
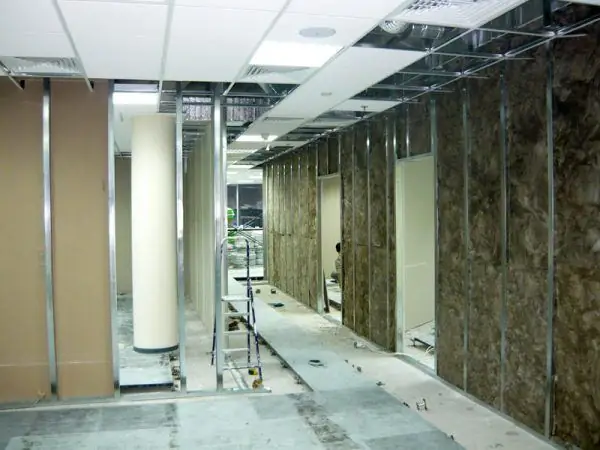
Doorways are arranged in the corridor partitions to divide the space into isolated rooms
The classical structure of the wall assumes a solid base, to which a raster of metal profiles of a given size is rigidly attached. Horizontal guide profiles (PN) are laid along the floor and ceiling, between which a vertical plane is formed with the help of racks. To increase strength, additional transverse braces are mounted between the posts.
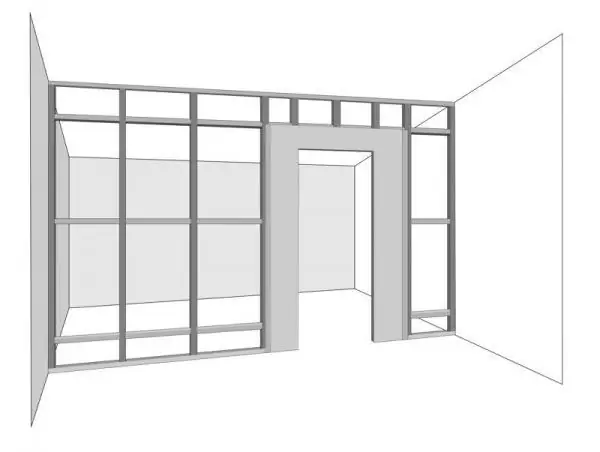
Cross members increase structural rigidity
Further, the surface of the partition is sheathed with drywall sheets. Since the standard size of the gypsum plasterboard is 120 cm, the distance between the vertical profiles is kept in multiples: 0.6, 0.4 or 0.3 m. load. Moreover, according to the standard, the distance between the screws is taken to be no more than 25 cm.
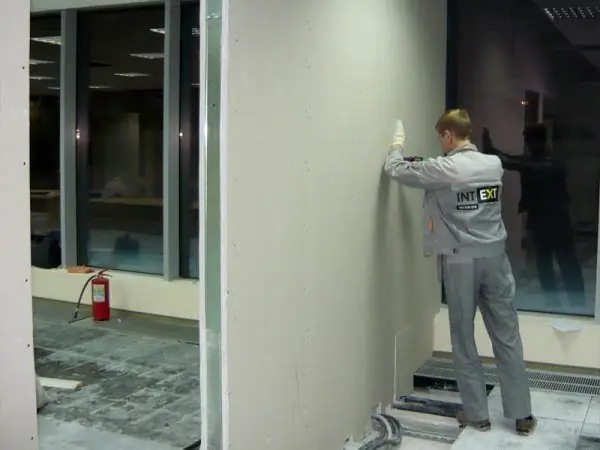
If two layers of gypsum board are mounted in the first layer, the distance between the screws is allowed up to 70 cm
After covering both sides of the frame with plasterboard, the joints of sheets and screws are putty. The gypsum solution is prepared in such a way that the finishing time does not exceed 20 minutes, since the gypsum tends to harden quickly. A reinforcing tape (usually self-adhesive), similar to a serpentine, is preliminarily laid in vertical joints. Transverse seams are reinforced with fiberglass strips or perforated paper bandage.
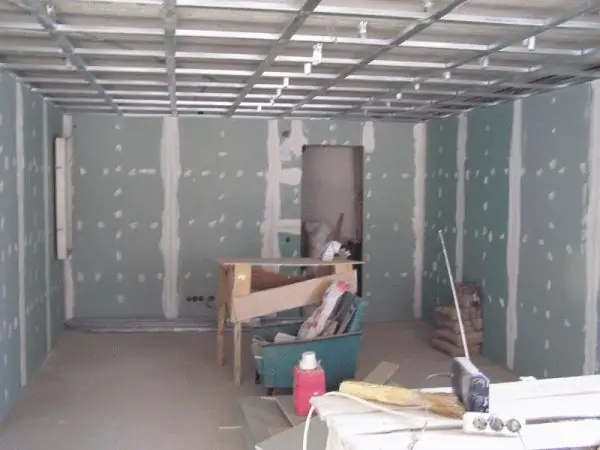
Three times coating with a plaster solution allows you to completely level the surface of the partition
Since the gypsum shrinks by 8-10% during drying, the operation is repeated twice, in between the seams are sanded with an emery bar. This is necessary to completely align the plane of the partition. The finish is completed with a finishing coat consisting of a fine dispersion paste.
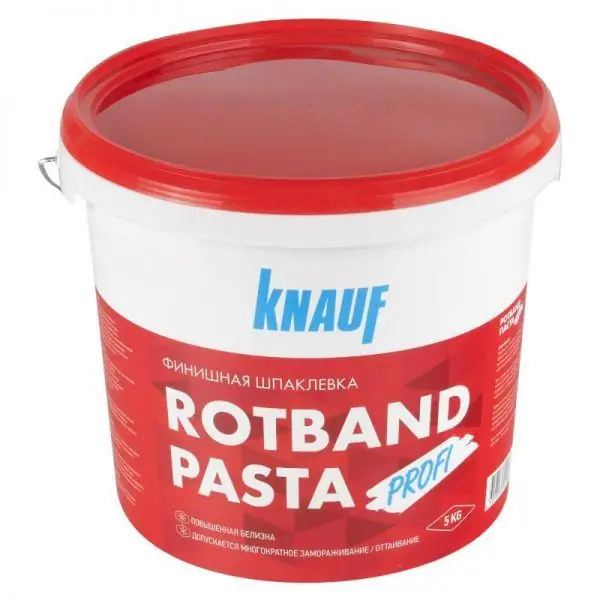
The finishing paste contains plasticizers that make the surface even and smooth
In fact, the installation process takes less time than finishing work. Each layer of putty must be completely dry, therefore, a certain time must be kept between the application of layers.
The pluses of drywall systems include:
- The speed of construction. The area of one plasterboard sheet is 3 m 2 (1.2 x 2.5 m). An experienced craftsman installs it in 4-5 minutes, hence the high speed of building the partition.
- Safety. The material is gypsum pressed between two sheets of cardboard. This is one of the most environmentally friendly types of panels.
- Fire resistance. The stoves do not burn and do not support combustion. With a thickness of 12.5 mm, the sheet can withstand fire for 20 minutes. This means that the partition will stop the spread of the fire for at least 40 minutes.
- Low weight of the structure (the weight of one standard sheet is 25 kg). Thanks to this, the pressure on the support is very gentle, which is especially important in buildings with limited load on load-bearing floors.
- Relatively high levels of sound insulation. Even without the use of anti-noise inlays (in the form of mineral wool or polystyrene), the permeability of sound through the partition is within the standard values.
- The internal space of the structure carries the payload. Electrical cables and water pipes are placed between the sheets. If necessary, sewer channels and other equipment are installed inside the partition.
-
The flexibility of the material allows you to give the partition a variety of architectural forms. Decor elements such as arches, columns and other curved surfaces are often used.
Installation of drywall arch The construction of an arch over the doorway is available even to a novice master
- Repairability. Any local damage is easily repaired. To restore the integrity of the structure, it is sufficient to replace only the place of failure (without disassembling the structure as a whole).
The disadvantages of the GCR partitions include two factors:
-
Low resistance to mechanical stress. There is an opinion among the people that it is impossible to "hammer a nail" into a wall or partition made of gypsum board. Although this is not entirely true. Fasteners with spacers have been developed specifically for drywall and other porous materials. With their help, shelves can be attached to the partition, pictures can be hung, etc. In addition, the problem is solved using embedded wooden blocks or plywood strips.
Drywall dowel The special design of the dowel provides reliable fastening to the plasterboard partition
- Water swelling. It really is. But almost all panel materials are at risk, including MDF, laminated chipboard and plywood. Interesting fact: drywall absorbs up to 15% of water (relative to its own weight) without loss of performance.
In general, an objective analysis shows that plasterboard systems have more advantages than disadvantages. That is why this material is so widespread in modern construction and interior decoration.
Tools required for the manufacture of a plasterboard partition
For the matter to argue, it is advisable to prepare all materials and tools in advance. A basic set for mounting a partition looks like this:
- a screwdriver or light drill with a screw tightening depth gauge;
-
painting knife, planer for grinding the ends of the gypsum board;
Plane for gypsum board A perforated plate at the base of the planer cuts off irregularities from the end of the GKL sheet
-
scissors for metal (for cutting profiles);
Tin scissors Compact sheet metal shears allow you to cut profiles exactly to the specified size
- saw with a narrow blade and a fine tooth;
- measuring tools: construction tape, hydraulic level (or laser level), plumb;
- construction thread (better - beating with blue);
-
a set of spatulas (trowel and narrow spatula up to 15 cm);
Drywall trowel For surface treatment of partitions, only metal spatulas are used.
- a container for diluting gypsum putty;
- puncher;
-
gun for applying sealant;
Sealant gun A tube filled with acrylic sealant is inserted into the pistol clip
-
grinding block;
Sanding block Leveling and grinding of the putty is carried out using sandpaper and a bar
- paint roller for paint (or wallpaper glue).
If the partition is installed in a room with wooden floors and ceilings, then a hammer drill is not needed. It is needed to install guide profiles only in concrete or brick buildings.
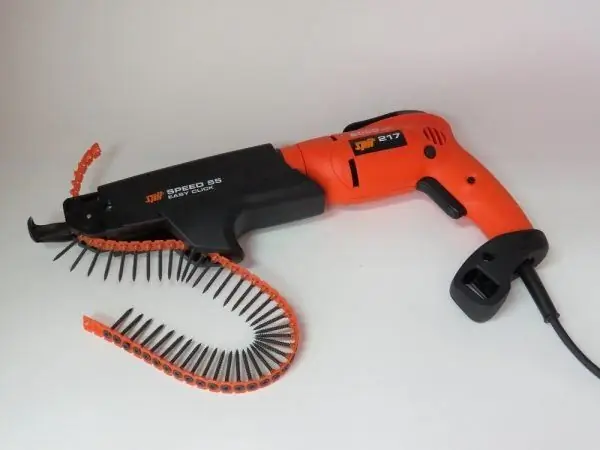
There are expensive models of professional screwdrivers with automatic screw feed
The calculation of materials for the construction of a gypsum board partition is easiest to perform according to publicly available tables. The websites of many specialized companies (for example, KNAUF) provide detailed information on the consumption of components down to each screw. As an example, we will give the calculation of the material for 1 m 2 of the C-111 partition (single metal frame plus one layer of drywall on both sides).
Table: Consumption of materials with a distance between the post profiles of 0.6 m
Name | Quantity per 1 sq. m | Calculated materials | Total number | |
one | KNAUF-list (GKL, GKLV, GKLO) | 2 m 2 | x | 2 m 2 |
2 | Knauf profile PN 50/40 (75 / 40,100 / 40) | 1.3 lin. m | x | 1.3 running meters |
3 | Knauf profile PS 50/50 (75 / 50,100 / 50) | 2 running. m | x | 2 running meters |
4 | Self-tapping screw TN 25 | 34 pcs. | x | 34 pcs. |
5 | Putty "KNAUF-Fugen" (for sealing joints) | 0.9 kg | x | 0.9 kg |
6 | Reinforcing tape | 2.2 lin. m | x | 2.2 running meters |
7 | Dowel K 6/35 | 1.6 pcs. | x | 2 pcs. |
8 | Sealing tape | 1.2 lin. m | x | 1.2 running meters |
nine | Primer "KNAUF-Tiefengrund" | 0.2 l | x | 0.2 l |
ten | Mineral wool slabs | 1 m 2 | x | 1 m 2 |
eleven | Knauf-profile PU | according to customer needs | x |
Making a drywall partition with your own hands
First of all, it should be noted that for the successful installation of the partition, it is desirable to have ready-made working drawings. As you develop your plan, you need to consider factors such as:
- electrification, location of switches and sockets, hidden cabling;
- optimal wall thickness, the presence of door or "window" openings in it;
- the possibility of laying water supply and drainage if the partition is planned in an adjacent room with a kitchen or dining room;
- design load, installation of decorative and functional elements. If, in the future, shelves or other suspended furniture are conceived on the surface of the partition, the places of attachments and, accordingly, the laying of amplifiers made of plywood and wooden blocks are determined in advance.
It is worth emphasizing the importance of a preliminary understanding of the functional purpose of the structure. At the design stage, it is advisable to take into account all the possibilities, because redoing a finished partition is much more difficult (but not impossible) and more expensive. All ideas should be given time to mature and "settle".
Layout and markup
When the plan is approved, they begin to build the partition. The place is freed from furniture and foreign objects on the walls. For marking, use the surfaces of the floor, ceiling and adjacent walls. With the help of a tape measure and skipping, the contours of the structure are marked. In order for the partition to fit well into the existing room, the binding is made to the walls and corners. It is important to observe the parallelism of lines and right angles, otherwise skews of the geometry of space are inevitable. Incorrect angles are especially painful in small rooms, so you need to measure them carefully.
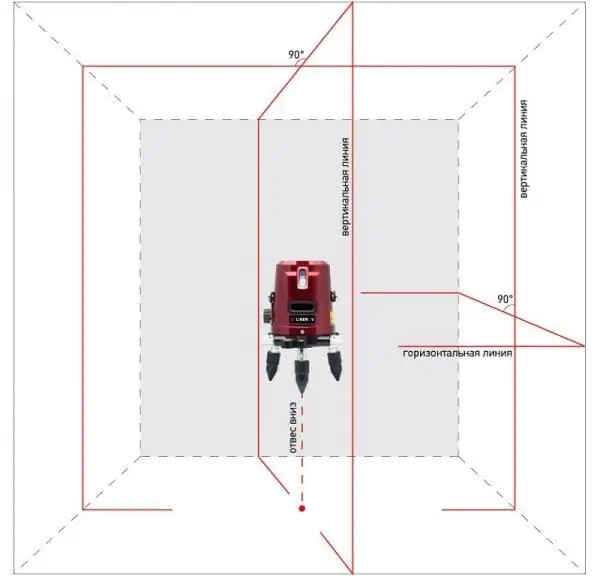
The laser level is ideal for marking the vertical and horizontal axes of the partition
Video: how to mark a partition from a gypsum board
Professional installers draw lines on the floor of the "clean", ie the final size of the wall. The location of the edge of the guide profile is determined by adding 12.5 mm (thickness of the drywall sheet).
Installation of battens
The frame is laid by installing guide profiles on the floor and ceiling, fastening rack profiles. In terms of the volume of work, the installation of the crate is 30%. It includes complete assembly and fixation of the metal structure.
In practice, the order of work on the assembly of the crate is as follows:
-
The guide profile is attached to the floor of the room. Fixation is done with dowel-nails using a puncher and a hammer. As a rule, they use fasteners measuring 6/35 mm (the first number is the diameter of the dowel-nail, the second is its working length). The lower part of all profiles is glued with a damper tape, which compensates for small deformations and protects the metal from corrosion, especially on a concrete base.
Damper tape In addition to the insulating function, the tape acts as a seal
-
On the walls, "root" racks are installed vertically. The length of the rack profile is made 3-5 mm less than the actual height of the room. The dowel-nails are driven in at a distance of at least 0.5 m, starting from the extreme points. On many guide profiles, perforations are made every half a meter, and they are used for fastening.
Mount the racks Wall studs rigidly fix the structure to the wall
-
The upper rail is mounted on the ceiling in a similar way. The result is a closed perimeter of the future partition. During work, you need to use stable ladders or goats. If the ceiling is concrete, it is recommended to use protective goggles when drilling holes, as stone chips are poured directly into the eyes.
Ceiling guide profile The position of the ceiling rail must be aligned with the floor profile vertically
- In accordance with the drawing, the locations of the racks are marked. As already noted, the maximum distance between the profiles is 0.6 m. But in order to increase the rigidity, you can place the racks every 40 or 30 cm. The meaning of this arrangement is that the sheets, which are subsequently sheathed with the structure, are joined on the profiles.
-
All racks are fixed in position with special flat head screws.
Cutter for fixing plasterboard profiles Professional installers use a cutter that pierces the profiles and fixes them in the desired position
If horizontal elements are planned in the partition, for example, a doorway, the upper crossbar from the guide profile is installed in the appropriate place. The workpiece is cut 10 cm longer, then folded 5 cm from each edge and screwed to the racks. Often, wooden bars are inserted into the pillars of the doorway for reinforcement along the entire height of the future door. The size of the bar is selected according to the width of the profile and fixed with self-tapping screws through the end of the rack.
This completes the installation of the frame. Next, they go to the sheathing of the partition with GKL sheets.
Frame cladding with thermal and sound insulation
Covering the frame with plasterboard in terms of time and labor costs is 40-45%, depending on the number of layers and the presence of additional structures. Straight sections are sewn up very quickly, but you need to carefully fit the sheets to each other and follow certain rules:
- the gap between plates with a straight edge is maintained in the range of 5-7 mm; joints of gypsum plasterboard sheets with semicircular, round or folded edges are made without gaps;
-
the horizontal joints should not coincide, the sheets are staggered (offset by half or a third of the sheet width);
Sheathing of the GKL partition Offset of sheets is a prerequisite for the correct sheathing of the frame
- vertical seams are located on racks and parallel to each other;
- self-tapping screws are immersed in the thickness of the sheet no deeper than 1 mm (ideally, the cardboard is crushed) and the distance between them is up to 25 cm with a single-layer sheathing;
- sheets on different sides of the partition are displaced in a horizontal projection (this increases the rigidity of the structure);
-
L-shaped plates are mounted around the openings; cutting of a rectangular configuration is unacceptable;
Doorway trim The upper part of the doorway is sheathed with L-shaped sheets
-
sound insulating mats are laid with a gap of at least 3-4 mm, the material cannot be creased.
Insulation of the partition Sound absorbing mats are cut to size equal to the distance between the post profiles
Drywall is cut with a sharp painting knife. A deep (up to plaster) incision is made along the line on one side (usually the front). Then the sheet is broken and cut from the other side, freeing the cut from the cardboard.
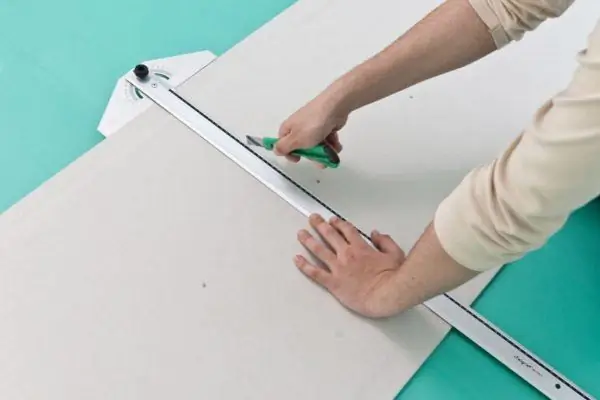
Marks are placed along the edges of the sheet and the desired size is cut along the ruler
Small parts are cut out with a thin hacksaw (it is possible for metal). To do this, the sheet is pierced through, and then the hole is expanded to the desired size.
The seats for switches and sockets are selected with a crown worn on the drill. The standard size for the installation of electrical appliances is 75 mm.
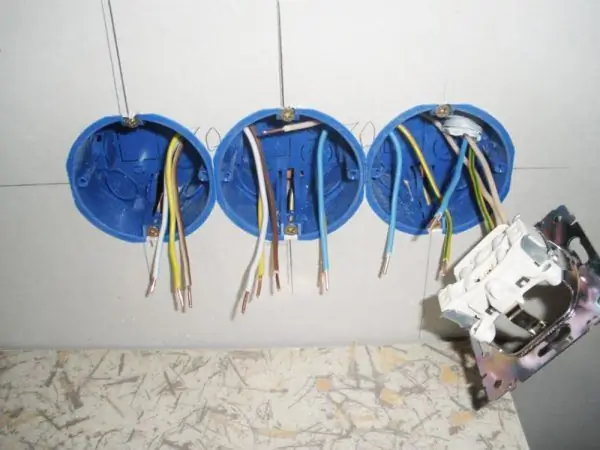
For the equipment of the sockets, special installation boxes are used.
If the edge is torn or irregular in shape, it is leveled with a special plane (or the back of the knife).
In practice, it is customary to remove the factory bevel (tapered or rounded) in those places where the sheet is in contact with the walls. In the future, this makes it easier to putty the surface.
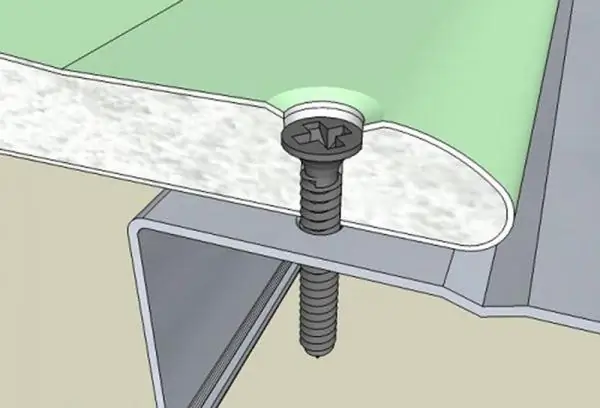
The narrowing of the end face on the sheet can be rounded or elongated.
Insulation and sound insulation are installed after one side is completely sewn up. Mineral wool is cut in such a way that the mat completely fills the gap between the posts, including the U-shaped cavity of the profile itself.
When arranging arches or other rounded planes, two options for bending the sheet are possible:
- Cutting longitudinal lines on the opposite side of the bend. The cutting step is 50 mm, this is enough for the bending radius to be 50 cm or more.
-
GCR wetting with water. So that water is evenly absorbed into the gypsum, the cardboard is perforated with a special roller with metal needles. After giving the sheet the desired shape, it is left to dry and, already finished, is mounted on the frame. Often in such a situation you cannot do without an assistant. To maintain the shape of the custom part, one fitter holds it in position while the other fixes the sheet to the profiles.
GKL sheet bending Longitudinal cutting of drywall allows you to bend it in different directions
Curved surfaces are fixed with a step of 10-15 cm over the entire area of contact with the profiles. Small distortions are subsequently leveled with putty.
From personal practice, I would like to give one useful advice. If communication lines are planned inside the partition, do not rush and sew up the frame completely. First, the gypsum boards completely cover one side. After that, cables are laid or drain pipes are installed, attaching them to the profiles (in the holes of the racks). It is advisable to conduct testing before finally revealing a metal structure. Electrical lines are “ringed” with a tester, and pressure pipes are tested under pressure (especially if they have connections or tees). If everything is working properly, you can sheathe the raster from the other side. In this case, the ends of the wires are twisted into a roll and tied up next to the places of the terminals. This is especially true if the inner cavity is filled with mineral wool (for insulation and sound insulation).
Putty and finishing of the partition
A simple calculation shows that 25-30% remains for leveling and filling the partition. But this operation can take most of the work in time. This is due to the fact that the technology involves drying each layer (at least 12 hours). And since there are at least three of these layers, it is clear that the process takes 36-48 hours. In addition, a novice drywall plaster needs to know that, in addition to tools and materials, certain skills are required for putty. Rarely does anyone immediately manage to bring the plane of the partition "to zero". The only assistant is patience and diligence with a sanding bar in hand.
After each application of the gypsum plaster, the dried surface is cleaned with sandpaper. The main goal in this case is to give the plane uniformity and smoothness. The bumps are grinded off, and the depressions are again filled with plaster mortar. The width of the putty along the vertical joints is at least 40 cm, on the horizontal joints 15-20 cm are permissible.
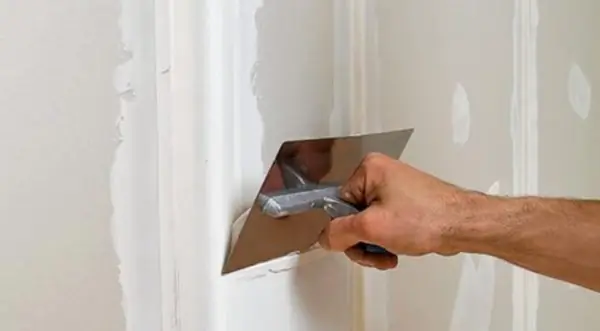
The width of the trowel for leveling the partition is 35 cm
Before the first application of the gypsum, a mesh bandage is glued to the vertical slots. Transverse joints are glued with fiberglass.

The use of a mesh bandage eliminates the formation of cracks on the partition
The final stage of preparing the surface of the partition for painting is the application of the finishing paste. There are two types of this coating - in bags with dry mix and ready mix in buckets. The second option is preferable, albeit more expensive.
Putty is applied in a thin layer and evenly fill all the recesses. After a little training, any person can handle the task. You can check the quality of the putty using the rule. A general construction error of 1 mm per 1 linear meter is considered permissible.
In general, the algorithm for plastering a plasterboard partition is as follows:
- The solution of plaster putty is mixed. The ratio of water to dry gypsum is 1: 1 by volume. Quite simply - half a bucket of water accounts for half a bucket of gypsum. First, water is poured into the container, then (with stirring) putty is poured until the consistency of thick sour cream is obtained.
-
The surface of the partition is treated with a deep penetration primer. This will remove construction dust from the wall and increase the adhesion of the putty mixture. Drying time is at least 4-6 hours.
Primer The primer can be used either neat or diluted with water
-
The factory edges of the drywall are glued with a serpyanka. The carved joints are made with fiberglass.
Fiberglass tape Fiberglass tape is glued onto a damp filler
- The first layer of putty is applied. First, the seams and joints are aligned, then the screws are putty.
- After the gypsum has dried, the surface is cleaned with emery, and the main emphasis is on removing excess putty.
- A second layer of putty is applied. The main goal is to fill in the remaining cavities and dents in the wall with plaster. The mixture consumption is halved.
- The dried second layer, if necessary, is again passed through with a sanding stone.
- A third, final layer is applied. This time, use a finishing paste that does not shrink when dry. Some craftsmen prefer to cover with a finishing layer not only the seams of the sheets, but also the entire surface of the partition. Sometimes this is justified - after such treatment, water-based paint lays well on the wall.
From personal experience, I'll give you a little hint. The most common mistake of a novice plasterer is trying to make an even but short stroke with a diluted compound. It is very difficult to level a large area in this way. You should try to pull the seam as far as possible, at least 1-1.5 meters in one "stroke" of the spatula. The chances of success will increase many times over.
Video: plasterboard putty
The last thing, which, unfortunately, is often forgotten when finishing, is sealing the perimeter of the partition with a sealant. They mainly use acrylic, which is used to fill small (up to 3 mm) gaps between the sheets of gypsum board and the load-bearing walls (ceiling) with a pistol. The sealing eliminates microscopic air currents and prevents the penetration of sound waves. The sealant is applied in a thin stream, then rubbed with a brush soaked in water to a continuous strip. The operation must be done 24 hours before painting, but after final drying and sanding of the putty.
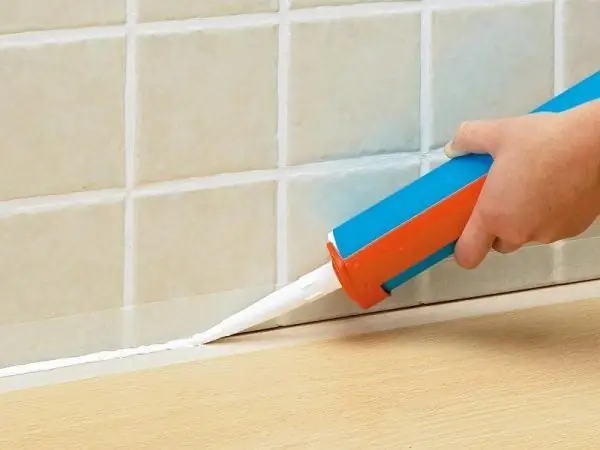
Acrylic sealant is applied with a construction gun
Video: do-it-yourself plasterboard partition
Reviews
The construction of a drywall partition is a fascinating and interesting business. In a matter of days, the planned redevelopment is embodied in reality. Nevertheless, one should not deviate from the technological rules during installation. The parameters and assembly conditions stipulated in the rules were not composed for fun. They reflect the properties and performance of the material. Compliance with the installation standards is guaranteed to ensure a long term of use and the functional quality of the plasterboard partition.
Recommended:
Do-it-yourself Bath From Blocks - Expanded Clay Concrete, Gas Silicate And Others - The Pros And Cons Of The Material, Step-by-step Instructions With Photos, Videos And Project Dra
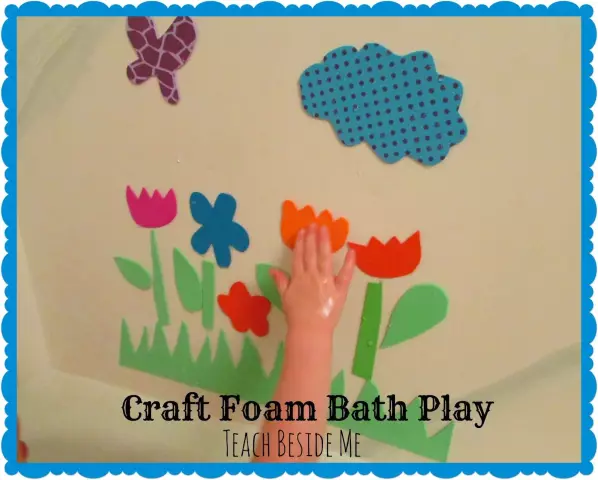
How to build a bath from expanded clay concrete blocks. The choice of materials and construction of the bath. Step-by-step instructions for the installation and decoration of a concrete block bath
Interior Sliding Partitions For Zoning The Space Of A Room: Design And Material Features, Their Pros And Cons, As Well As Installation Instructions, Photos
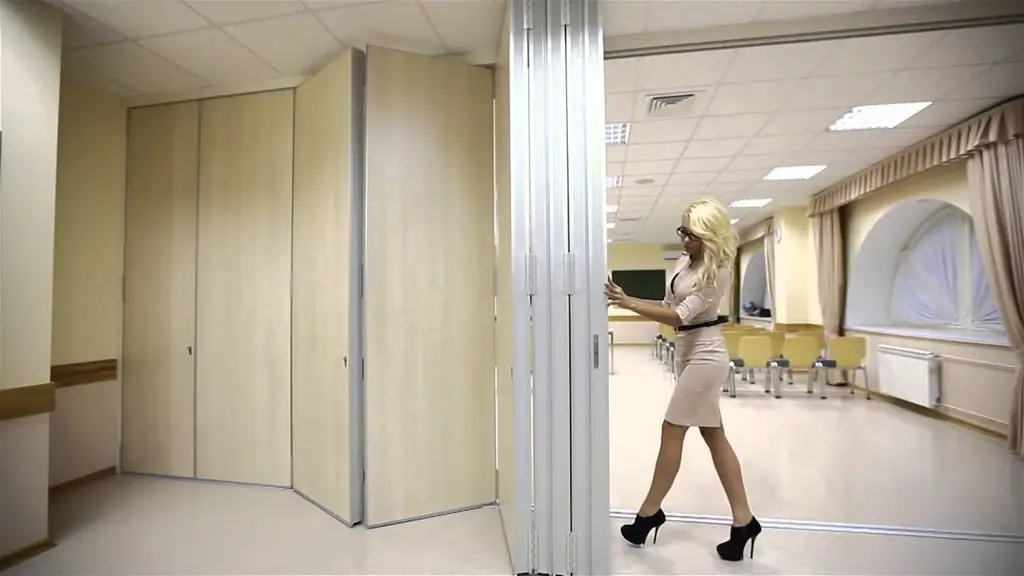
The device and purpose of interior sliding partitions. Varieties of partitions by design. Independent production and installation
Screens-partitions For Zoning Space In The Room: Varieties And Design Features, Manufacturing And Installation By Hand
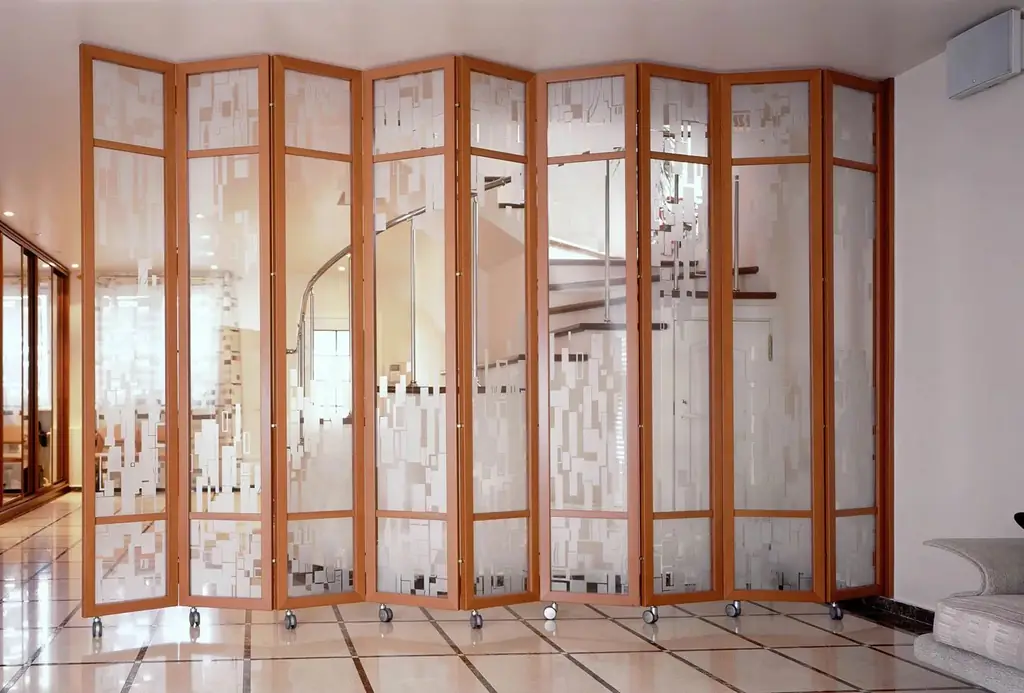
What is a partition-screen. What are the types of screens, their features, advantages and disadvantages. How to make a partition screen yourself
Rack-partitions For Zoning Space In A Room: Varieties And Design Features, Installation Stages, Photo
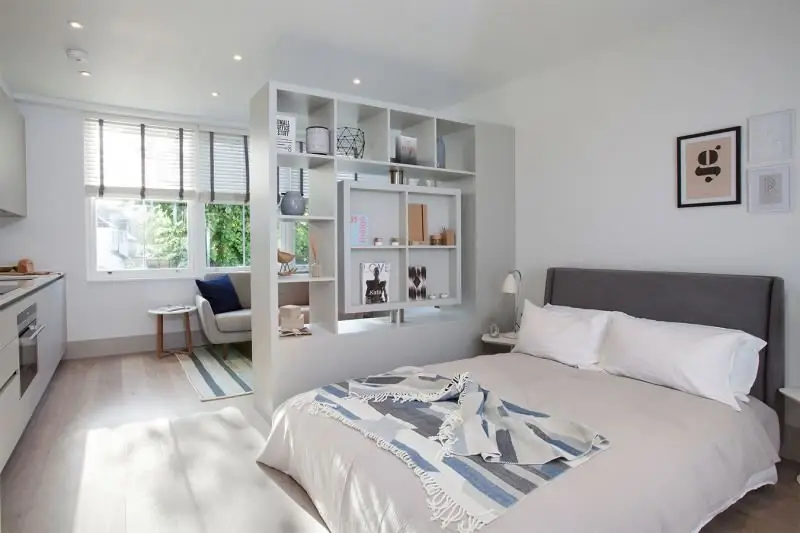
Rack-partition: advantages and disadvantages, varieties. DIY selection and installation of multifunctional furniture
Decorative Partitions For Zoning Space In A Room: Varieties And Design Features, Their Installation With Instructions
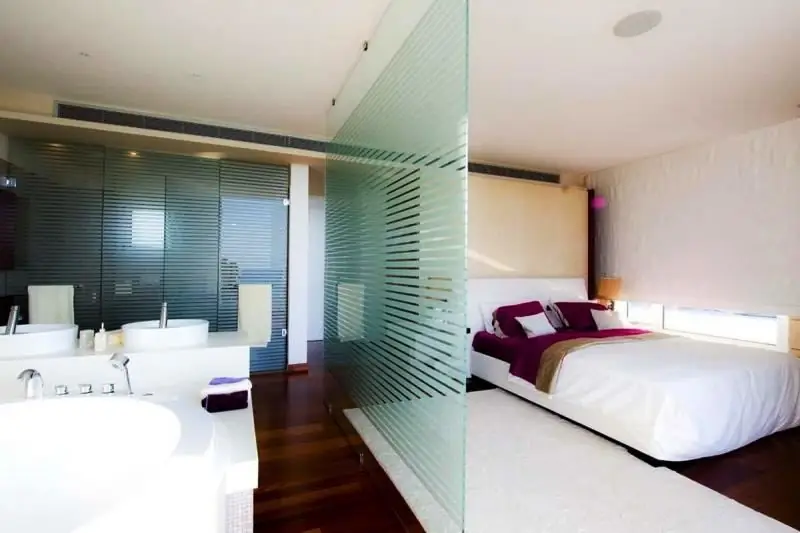
How convenient it is to zone a room with minimal costs. What materials are suitable for partitions and how to use them. We make a design partition ourselves