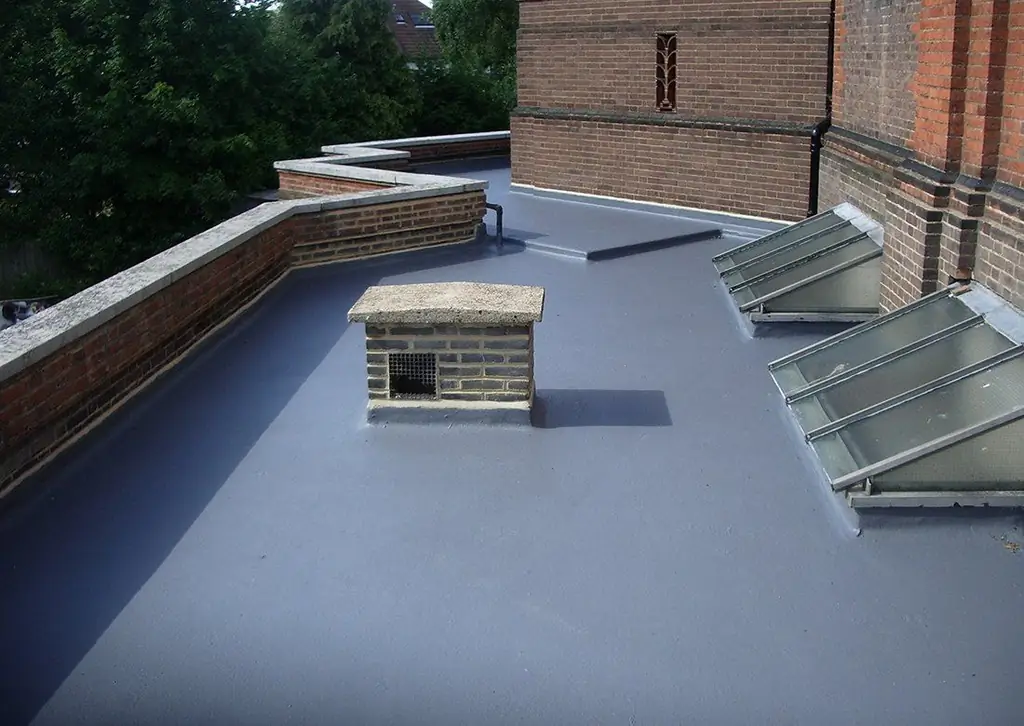
Table of contents:
2025 Author: Bailey Albertson | [email protected]. Last modified: 2025-01-23 12:41
The device of a liquid bulk roof: the main elements, features of installation and operation
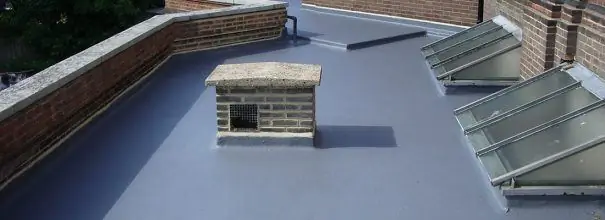
It is no secret that the roof is one of the most significant building structures, to which strict requirements are imposed. Roofing materials must be reliable and resistant to atmospheric precipitation. Liquid self-leveling roofing has recently become firmly entrenched in the market and has established itself as a high-quality and wear-resistant product for roofs of residential, industrial and utility structures of various sizes and configurations. Roofing mastic has a number of advantages over other materials. It provides a lower total cost of the coating, does not lend itself to deformation and mechanical stress. Such coatings are created not only on new roofs, but are also used during restoration work.
Content
-
1 Materials used for the production of liquid bulk roof
- 1.1 Video: testing of samples of liquid roofing "Elastometric"
- 1.2 Basic elements and the device of a self-leveling roof
-
2 Installation of bulk roof
- 2.1 Preparation of the base
-
2.2 Application of roofing material
2.2.1 Video: spraying liquid rubber on the roof
-
3 Features of the operation of a liquid bulk roof
-
3.1 Quick repair of liquid roof
3.1.1 Video: Liquid Roof - Quick Repair
-
- 4 Safety of a building with a liquid bulk roof
Materials used for the production of liquid bulk roofing
Liquid roofing, which is also called liquid rubber, can have a single-component or multi-component composition:
- one-component roofing mastics are made on the basis of a polyurethane composition;
- multicomponent mastics are made from modified bitumen components such as synthetic rubber (styrene-butadiene-styrene compound) and synthetic plastic (atactic polypropylene).
In addition, various antiseptics and herbicides can be used as processing aids to impart improved properties to the liquid mastic. Mineral materials are used as a filler. A self-leveling roof may also contain solvents, but some manufacturers have brought products to the market without them and boldly declare their environmental friendliness.
Polymer-bitumen mastic is a homogeneous mass of neutral color. The colors of the bulk roof are usually standard: gray, brown, red or black. Manufacturers do not have a variety of shades, but usually there are no problems with the selection of the desired color. If a non-standard and rare color scheme is required, then the surface of the liquid roof, after drying, is covered with paint for outdoor use.
Coatings with a bitumen-polymer base have the following properties:
- elasticity;
- heat resistance;
- waterproofness;
- high and stable adhesion over the entire coating area;
- maintainability;
- self-tightening of minor defects (punctures or cuts).
Video: testing of samples of liquid roofing "Elastometric"
The main elements and the device of the bulk roof
The main element of a liquid bulk roof is roofing mastic. It is packaged in sealed cans, buckets or barrels, depending on the volume.
Since the device of a self-leveling roof can be performed in two ways - without reinforcement or with partial reinforcement - the reinforcing material is also an element of the self-leveling roofing system.
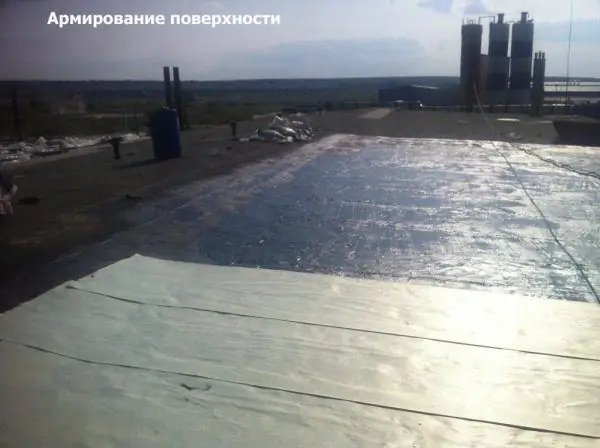
Reinforcement over the entire roof area is performed on particularly critical buildings and structures
Reinforcement is arranged mainly in the places of abutments and junctions, on the roofs of critical structures subject to high operational loads. Reinforcement is performed with various materials: fiberglass, fiberglass or geotextile. In some cases, roll roofing materials can be used for this purpose.
Some manufacturers insist on using an additional primer coat. As a rule, if the instructions say about the need for preliminary priming of the base, the manufacturer has both products in the assortment that are fully compatible with each other. Therefore, before buying a roofing material, it is worthwhile to study the instructions for use in detail and stock up on the necessary components. Roofing soil (primer) is applied manually or mechanically on a prepared and cleaned base. Today the market offers a wide range of self-priming mastics that do not require surface pretreatment.
Reinforce the surface as follows:
- Roofing mastic is applied to the base by hand, evenly distributing it over the surface with a roller.
- Lay out the reinforcing material evenly and roll it to the base with a roller, preventing the formation of air spaces, bubbles, bends or displacements relative to the area to be reinforced.
-
If necessary, apply another layer of mastic so that the armoet is completely closed.
Reinforcement junction processing Reinforcement of the water intake funnel with fiberglass is performed in a small area of 50 × 50 cm
After covering the roof with the main layer of mastic and gaining mechanical strength to increase the service life and protect the roof from ultraviolet radiation, some manufacturers suggest using an aluminum-based topcoat.
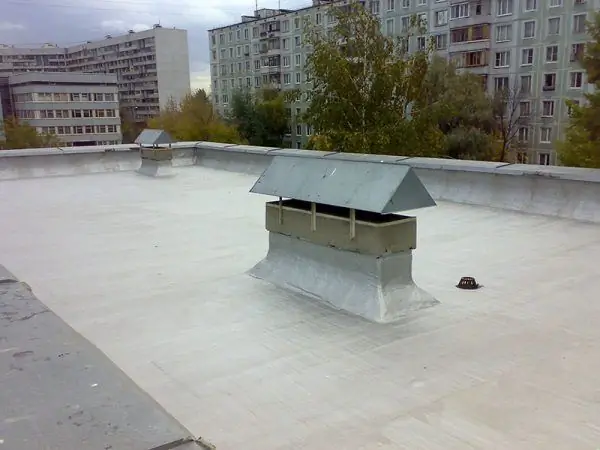
The surface of the roof after coating with an aluminum-based finishing compound becomes silvery
Thus, the list of all elements of a liquid bulk roof in the order of their sequence from the base to the topcoat is as follows:
- Priming layer.
- Reinforcing materials.
- The main coating is roofing mastic.
- Protective layer based on aluminum.
Installation of bulk roof
The physicochemical properties of a liquid roofing coating allow it to be laid on any solid base:
- reinforced concrete slabs;
- cement screed;
- asphalt or asphalt concrete screed;
- bases made of asbestos-cement sheets;
- wooden bases;
- old mastic or roll roofs when carrying out repair work.
Installation of a liquid roof is greatly simplified in contrast to the installation of a roof made of other materials.
Ease of installation is achieved due to:
- mechanized application;
- cold styling;
- seamlessness;
- light weight;
- simplicity of the arrangement of adjacencies;
- short drying and hardening time;
- independence from the complex configuration of the roof;
- no need for additional structural elements.
Before starting work on the installation of a mastic roof, it is necessary to assess the weather conditions: the air temperature should be in the range from +5 to +40 o C. In rainy weather, installation is not recommended. In addition, it is necessary to prevent direct sunlight on the material, therefore, in hot climatic regions, it is preferable to choose the morning or evening time for work.
Roofing works are divided into two main stages:
- Preparation of the base.
- Application of roofing material.
Foundation preparation
When installing a new or renovating an old roof, the base surface must be flat, clean and dry.
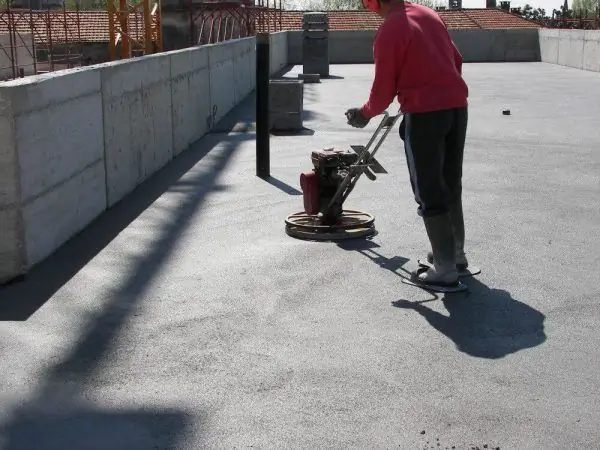
Before starting roofing work, the surface of the roof base must be thoroughly cleaned of dirt and debris
The prepared substrate must be free of dirt, dust, grease, oils and solvents. If the roof already has a mastic or roll coating, then peeling, swollen and damaged areas should be removed. All junctions must have a smooth transition.
Cleaning of surfaces is done manually or using various mechanisms if the volume of work is large. The accumulated water is pumped out by vacuum pumps or air-gas burners. The dust is removed by compressor units, industrial vacuum cleaners or washed off by high pressure washers.
Preparatory work also includes the installation of the building's drainage system, the device of inputs and outputs of technological equipment, the installation of vapor barrier and thermal insulation, if required. If a decision is made to build a primer or reinforcing layer, then these works are also performed at the preparation stage.
Roofing material application
The procedure for installing a liquid bulk roof consists of the following stages:
-
Before starting work, the quality of the roofing material is checked. Liquid mastic in consistency should resemble a homogeneous rubber mass without foreign inclusions and delamination. On the surface, the formation of a thin dense crust of mastic is allowed. The crust must be removed and the mass thoroughly mixed - it is prohibited to mix the material together with the crust. Roofing material should be prepared outdoors or in a well-ventilated area. Bitumen-polymer mastics freeze at negative temperatures, therefore the optimum temperature for preparatory work is at least +10 o C. The advantage of one-component polymer mastics is that they do not lose their properties at temperatures from -20 to +30 oC. Opened containers with roofing mastic should be stored tightly closed in a place protected from direct sunlight.
Bitumen-polymer roofing mastic Work can be started only if the mastic has a homogeneous structure and does not contain foreign inclusions
-
With the manual method of application, the mastic is poured in small portions onto the surface of the roof and distributed in an even layer with a roller, brush or spatula. The instructions for the roofing material must indicate the recommended tools for its application. If the mastic is applied with a roller or brush, then they do it in two layers. The second layer begins to fill only after the first has dried. The thickness of the common layer of the liquid roof should be in the range from 2 to 10 mm. A more precise value can be found in the instructions.
Manual method of applying roofing mastic When leveling the mastic with a spatula, you need to carefully monitor that each strip has the same thickness
-
With a mechanized method of applying liquid roofing, first of all, it is worth choosing a suitable device. For a perfectly smooth and even surface, it is best to use a high pressure spray unit. Low-pressure installations are unlikely to give a good result - the probability of smudges, bumps and unevenness of the layer is very high. Two-component mastics are applied using a two-channel gun: a bitumen-latex mass is fed from one channel, and a liquid catalyst is supplied from the other. The mixing ratio must strictly comply with the manufacturer's instructions. The components are simultaneously fed from the pistol and mixed already on the surface. The distance from the gun to the base of the roof should be within 50-60 cm. The roofing mastic should be applied in even strips about 1 m wide along the entire length. The adjacent strip should overlap the previous one by at least 20 cm. One-component mastics are applied according to the same principle, only a single-channel gun is used.
Mechanized method of applying mastic Two-component mastics are applied with high pressure units with two nozzles
-
An important stage in the construction of a liquid roof is a set of mechanical strength by the material. This period usually takes 3 to 7 days. The coating begins to harden approximately on the second day. During this period, it is imperative to ensure the safety of the coating from any mechanical stress.
Liquid rubber on the roof After curing, liquid rubber becomes viscous and pliable
Video: spraying liquid rubber on the roof
Features of the operation of a liquid bulk roof
When using a self-leveling roof, it should be protected from significant mechanical stress. It is not intended for the constant movement of people, goods, etc. But you should not be afraid of small cuts and microcracks, since liquid rubber has the property of self-tightening. The bulk roof is not damaged from the impact of various atmospheric precipitations and loads from them. A big plus of this coating is that it is completely maintainable.
Quick repair of liquid roofing
The need to repair a liquid roof, unfortunately, is sometimes revealed not only after a significant period of operation, but also almost immediately after application. Various defects may appear due to insufficient preparation of the base or violation of the technological process of work.
- If blisters or bubbles filled with air or water are visible on the surface, the damaged area is pierced with a needle and the contents are released. Then the coating is carefully rolled with a roller to the base, while the hole from the needle is tightened almost immediately.
- During operation, areas may appear that have an insufficient thickness of the roofing in comparison with the required one. In this case, the mastic is applied in a second layer to the cleaned and dried defective area so that the total thickness of the coating meets the necessary requirements.
-
If significant damage to the coating appears on the roof: wide cuts to the base of the roof, ruptures due to partial destruction of the base or mechanical damage in large areas, then the repair technology should completely repeat the process of installing a new roof, only work is carried out not over the entire area, but locally … In this case, the base must be completely repaired, cleaned and primed. If the coating was previously applied by spraying, then the repair will be easier to carry out manually, which will greatly facilitate the task, reduce the cost of work and take less time.
Manual liquid roofing Restoration of damaged liquid roofing is easier and cheaper to do manually
In addition, it is worth noting the widespread use of liquid roofing during restoration work, when a significant part of the roof remains made of a different material, and the damaged areas are covered with liquid rubber.
Video: liquid roof - quick repair
youtube.com/watch?v=nqwYgYN_0NE
Building safety with liquid self-leveling roof
The safety and durability of any residential and industrial building directly depends on the quality of the roof structure. We list the properties of a liquid roof that ensure the safety of structures:
- the material is slightly flammable, therefore it does not pose a threat from the point of view of the spread of fire;
- the coating is applied in a cold way, therefore, accidental ignition, which is potentially possible when using welded roll materials, is completely excluded;
- in the composition of the mastic there are no volatile compounds that can harm people or the environment;
- the liquid roof has, though small, vapor permeability sufficient for operation without additional aerators.
The use of a liquid roof will provide the owner and tenants with a comfortable and hassle-free operation for many years. Reliable roofing material creates normal microclimate in the premises and excludes the penetration of moisture into them from the side of the floors. Liquid roofing is easy to install, so the work does not require special training and even a non-professional can handle them. As a result, its overall cost is often lower than with other technologies. The compact size of the container allows you to easily deliver the mastic to objects and lift them to the roof without using any mechanisms or even outside help. Liquid roofing is a reliable protection for multi-storey residential and industrial buildings, private houses, loggias, balconies, garages, terraces and various auxiliary buildings.
Recommended:
Inverted Roof, Its Structure And Main Elements, As Well As Features Of Installation And Operation
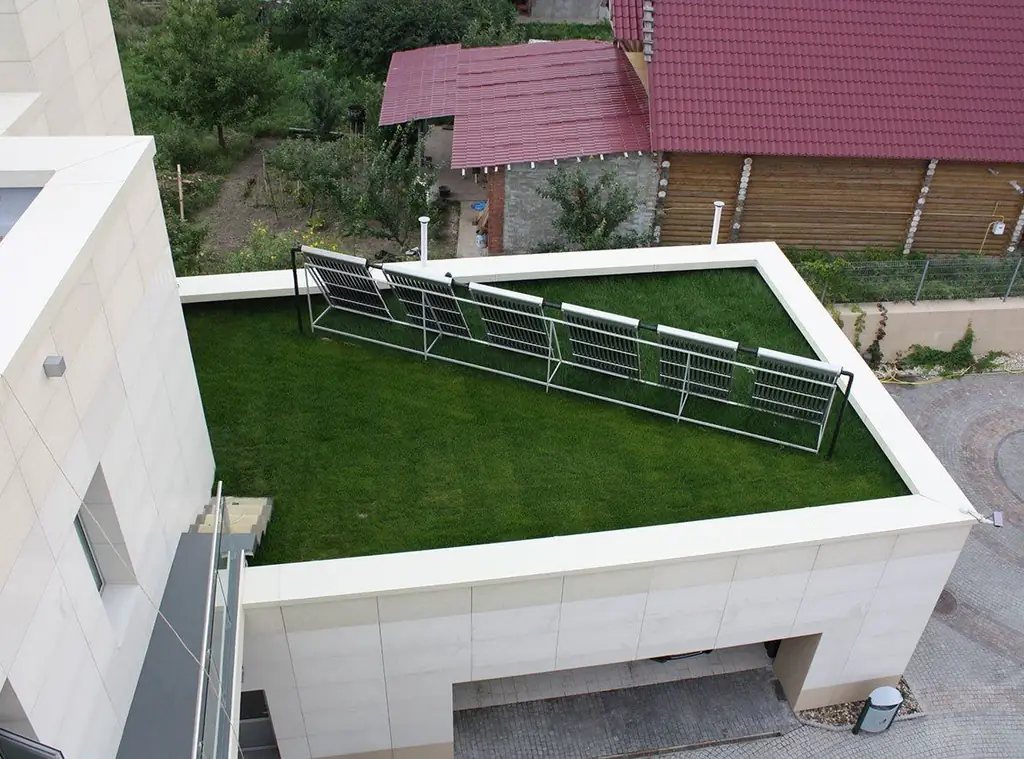
What is an inversion roof. Inverted roof types. What materials can be used. DIY installation of an inverted roof. Operating rules
Copper Roof, Its Structure And Main Elements, As Well As Features Of Installation And Operation
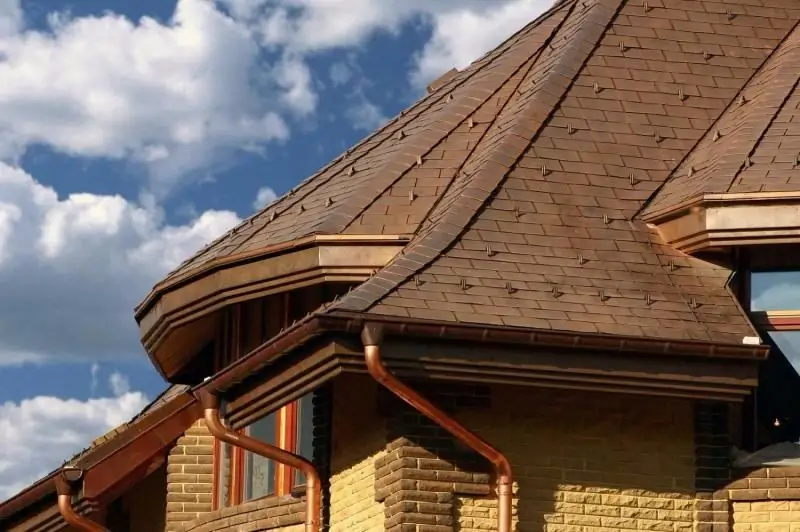
Copper roof, its types and advantages. Installation of roll and tiled copper roofs and features of their installation. Copper roof maintenance and repair
Wooden Roof, Its Structure And Main Elements, As Well As Features Of Installation And Operation
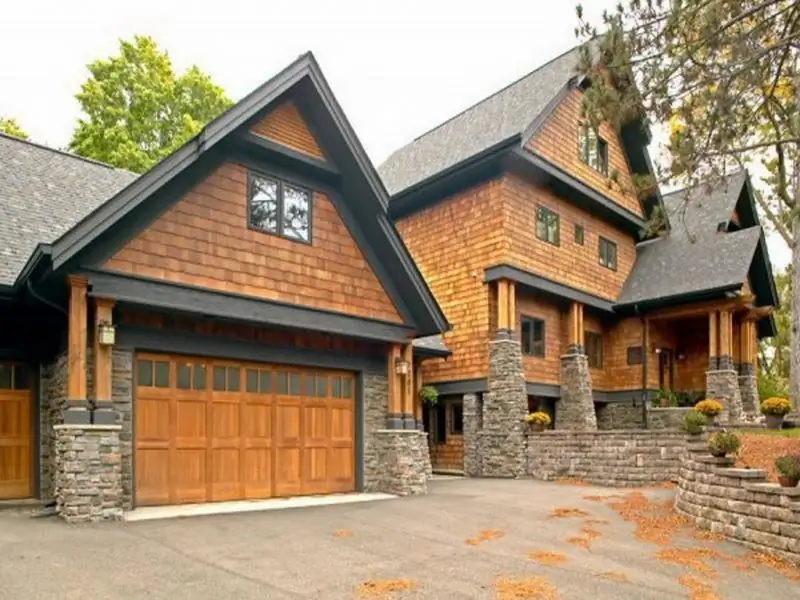
What is a wooden roof. What materials is it made of. Installation of a wooden roof and its features. Safety and operation
Broken Mansard Roof, Its Structure And Main Elements, As Well As Features Of Installation And Operation
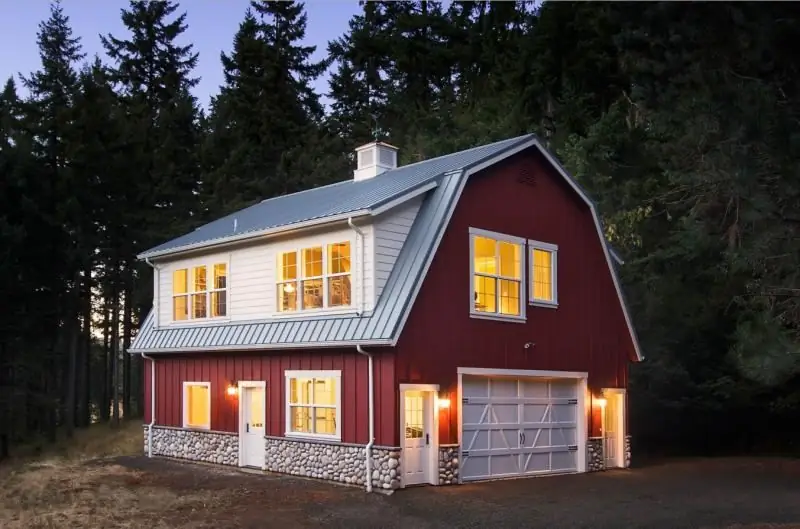
Brief description of the mansard sloping roof. The device of the rafter system. Calculation of the cross-section of the rafters. The procedure for installing a sloping roof and the rules for its operation
Mansard Roof, Its Structure And Main Elements, As Well As Features Of Installation And Operation
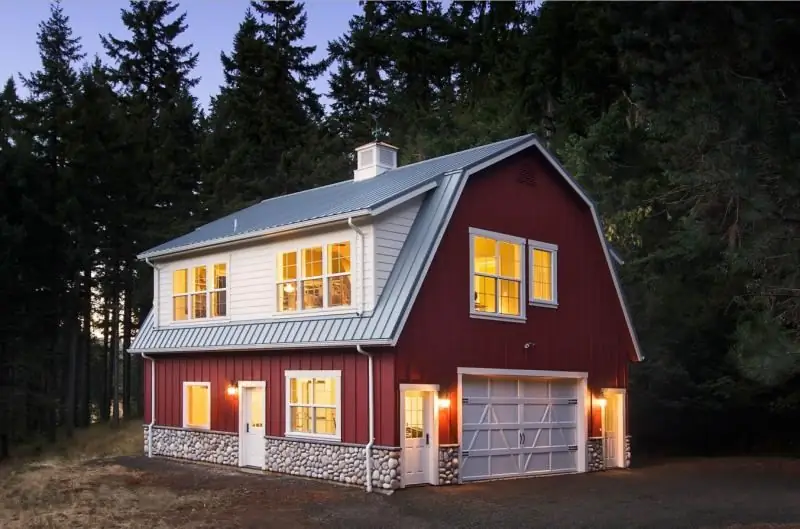
What is a mansard roof. Design, types and features of DIY installation. Calculation of materials, operation and repair of mansard roofs