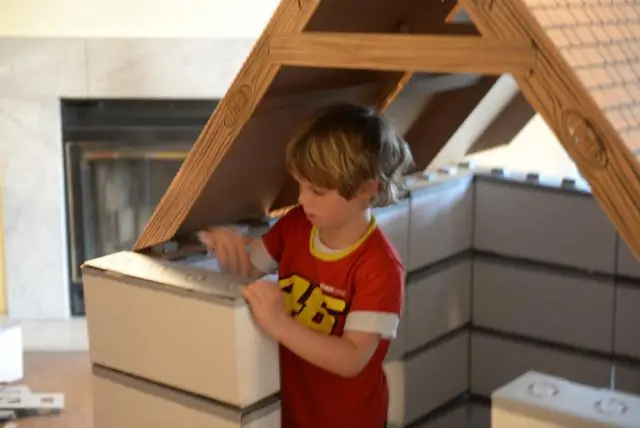
Table of contents:
2025 Author: Bailey Albertson | [email protected]. Last modified: 2025-06-01 07:32
Self-construction of a foam block shed from scratch
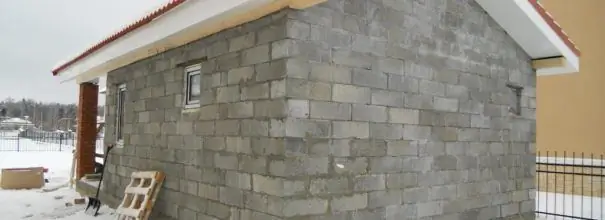
In a private household, outbuildings are always needed. It is convenient to store numerous tools, garden tools, building materials and old, but necessary things in a barn. This building is often used as a workshop or as a home for pets. In order for the barn room to keep warm and a stable internal atmosphere, it is necessary to build it from a suitable material. For this outbuilding, it is better to use foam blocks.
Content
- 1 Advantages and disadvantages of using
-
2 Preparation: barn designs, drawings, approximate dimensions
- 2.1 Material calculation. The choice of foundation and insulation
- 2.2 Required tools
- 3 Step-by-step instructions for making a barn with your own hands
- 4 Video: How to build a shed from foam blocks yourself
Advantages and disadvantages of using
Foam blocks have all the qualities necessary for the construction of low structures and have significant advantages:
- Their use will provide the building with excellent thermal insulation performance. The foam block has the same thermal conductivity as natural wood. In comparison with ceramic or silicate bricks, it loses heat almost three times less. This effect is achieved due to the porous structure of the foam block. 4/5 foam block consists of small closed cavities. These air pockets are well insulated from each other. As a result, the temperature changes slowly. A building made of this material acquires the properties of a thermos.
- This material has good frost resistance. The porous composition of the block allows water to migrate when freezing. Thanks to this, the foam block retains its structure and integrity.
- The presence of small cavities inside the unit provides excellent sound insulation.
- Possession of high hygroscopic properties contributes to normal air exchange. This advantage makes it possible to remove water vapor and prevent dampness and mold in the room.
- Foam blocks do not burn and do not support the flame. This material can withstand open fire for 8 hours and will not collapse.
- Ease of use. The foam block is much larger than ordinary brick. Its dimensions are 200x300x600 mm. It is convenient to build with such blocks, since the construction of walls is faster.
- A clear advantage is the weight of the foam block. On average, it is about 11 kg. This provides less stress on the foundation and walls.
- The total cost of this material is much less than the purchase of bricks for such a structure.
- Foam blocks are an environmentally friendly material, as they consist of cement, sand and a foaming agent. A protein base is used as a foaming agent.
- The porous base of the blocks is flexible for sawing.
The disadvantages of foam blocks include the following criteria:
- The limited strength does not make it possible to erect buildings higher than ten meters.
- The same disadvantage affects the transportation of foam blocks.
- The unattractive appearance of the blocks requires additional cladding, which significantly affects the cost of the building.
- Without additional protection, at low temperatures, foam blocks are destroyed.
Preparation: barn designs, drawings, approximate dimensions
At the preparatory stage of building a shed from foam blocks, it is necessary to choose a place for its construction. An important point is its convenient location on the site of home ownership. As a rule, two entrances are made in the barn, one of which should be wide and unobstructed. It is convenient when furniture and bulky items are brought in, for example, when renovating a house. Depending on the functional purpose, the shed is placed close to a residential building or built away from prying eyes. It is necessary to pay special attention to the layout of the barn, the overall dimensions and its functional areas. With good design, in the future there will be no need to erect additional extensions to it. The most convenient for household needs, it has dimensions of 6x3 m (divided into two rooms 2x3 m and 4x3 m). Such a project of an outbuilding will make it possible to use it for different purposes. This layout of the barn will allow you to place not only a workshop, but also a dwelling for pets.
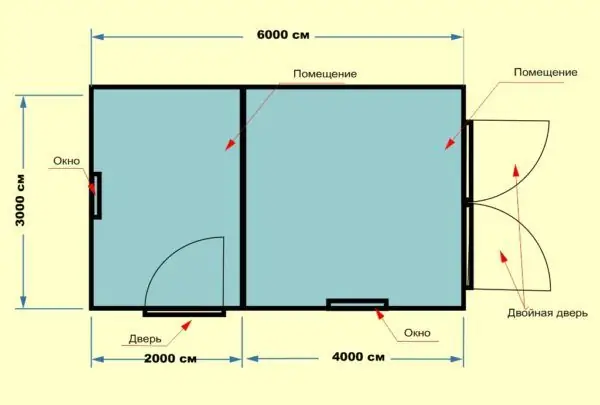
The presence of two functional areas of the barn create convenience when using it
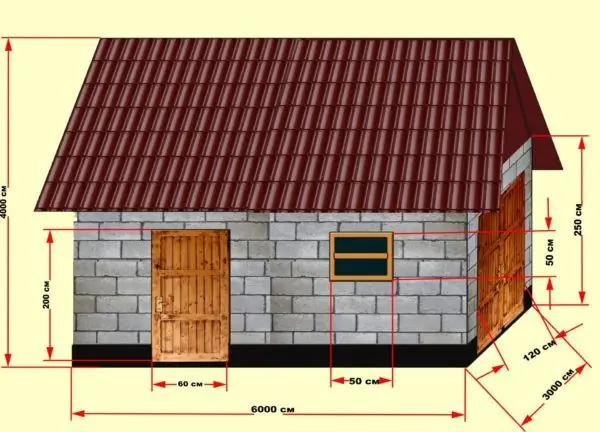
Optimal building dimensions
The rafter system of the gable roof forms a floor that can be conveniently equipped for storing fruits or crops. The height of the roof is selected depending on the purpose of use. If necessary, you can build a rafter system with roof slope angles that will allow the arrangement of the second floor. In our case, a roof with a slope of 53º was used.
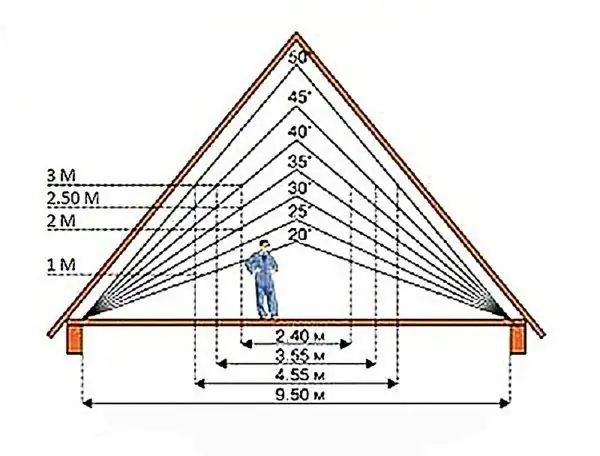
Dependence of the usable attic area on the angle of inclination of the roof
Calculation of the material. The choice of foundation and insulation
It is possible to calculate the number of foam blocks required to build a shed without involving estimates. Through simple mathematical calculations, you can get accurate information about the amount of material required. To do this, you need to know the parameters of the foam block used, the height and perimeter of the future shed. In our case, the shed will be built from foam blocks measuring 200x300x600 mm. With a building length of 6 m, a height of 2.5 m, you need (6 + 3) 2 = 18 / 0.6 = 30 pieces of foam blocks, where 18 is the perimeter of the shed, and 0.6 is the length of one foam block. As a result, one row will contain 30 blocks. Now you need to find out how many strips of masonry are required. To do this, divide the height of the building by the height of the block 2.5 · 0.30 = 8.3 rows. In total, 8.3 strips are required to build a barn, 30 foam blocks in each row. To calculate how many blocks will take in total, you need 8.3 30 = 249 foam blocks.
In some cases, another method of masonry is used, in which the block height will be 20 cm and the width 30 cm. In this case, not 8.3 strips, but 12.5 strips are needed to build the walls of the shed. We get this value as follows: 2.5: 0.20 = 12.5, where 2.5 is the wall height, 0.20 is the block height. Therefore, the total number of foam blocks for laying walls in this way will be 12.5 · 30 = 375 foam blocks.
When calculating the number of foam blocks, it is necessary to take into account door and window openings. To do this, subtract from the total number of blocks as many windows and doors will take. The calculation is done by masonry at a block height of 30 cm. According to our drawing, the shed provides two identical windows with dimensions of 50x50 cm and a pair of doors (one of them is double), dimensions of 0.6x2.0 m and 1.2x2.0 m. For one the window opening will need (0.5 2): 0.6 = 1.6 blocks in length and (0.5 2): 0.3 = 3.3 blocks in height.
Since we have two windows, we add the obtained dimensions of the length and height of the blocks 1.6 + 3.3 = 4.9 blocks. Now we know how much needs to be subtracted from the total number of foam blocks to accommodate two windows. It is necessary to round the figure 4.9 to 5 foam blocks.
The calculation of foam blocks for doors is done in the same way. To open one (smaller) door, you need 0.6: 0.6 = 1 foam block in length and 2.0: 0.3 = 6.66 or 2.0: 0.2 = 10 in height. The second (double door) requires 1.2: 0.6 = 2 foam blocks in length and 2.0: 0.3 = 6.66 or 2.0: 0.2 = 10 in height.
Total 1 6.66 = 6.66 and 1 10 = 10 blocks, as well as 2 6.66 = 13.32 and 210 = 20 foam blocks, 6.66 + 10 + 13.32 + 20 = 49, 98 blocks, round up to 50 foam blocks.
Then you need to calculate how many blocks will occupy the openings of doors and windows. For this, 50 + 5 = 55 blocks. Now you need to subtract the extra blocks from the total number of all blocks. For this, 249-55 = 194 foam blocks are needed to build a shed with doors and windows.
Now you need to determine the amount of material for the roof. This requires wooden beams and boards for the gable roof truss system, as well as roofing material. A red metal tile will be used as this material.
The length of the front, rear and side overhangs should be 50 cm longer than the width and length of the base. This is necessary to avoid the ingress of snow and moisture on the walls of the barn. For the construction of a gable roof you will need:
- Wooden beams (for the manufacture of rafters) with a section of 100x50 mm and a length of 300 cm in an amount of 20 pieces. The angle of inclination of the roof with this length of the rafter beams will be 53 degrees.
- Boards (for lathing) with a section of 100x25 mm, 6 meters long, 17 pieces.
- Bars (for floor beams) 100x50 mm 400 cm long - 20 pieces.
- Mauerlat (bars) with a section of 150x50 mm and a length of 700 cm - 2 pieces.
- Board (for crossbars of rafters) with a section of 100x25 mm, 300 cm long - 1 piece.
- Insulation material in the amount of 3 rolls.
- Metal corners for attaching rafters to floor beams.
- Nails and screws.
Depending on the material from which the shed will be built, the type of base is selected. For this building, the following types of foundations are used:
- Columnar. The use of this foundation contributes to savings in building material and installation speed. Usually it is used for light frame-panel buildings.
- Screw and plate. These species are irreplaceable on soft ground, heaving and marshy soils, as well as on sand. The screw foundation can be installed at any time of the year.
- Monolithic tape. This look is ideal for brick, stone and concrete block buildings.
- Blocky. This foundation combines the advantages of other types of foundations.
An important point will be to study the characteristics of the soil, since certain problems in construction can arise from them:
- Soil, which contains a lot of sand, can move after melting snow or heavy rains. When building on such soil, it is recommended to install a slab, pile (screw pile) or strip foundation.
- The content of a large amount of clay and sandy loam contributes to deep freezing of the soil and the formation of quicksand, which makes the soil unstable.
- The soil, consisting of gravel, does not freeze to a considerable depth and does not shift under the influence of moisture. This soil is well suited for building a barn on a columnar foundation.
- Rocky or solid stone soil is suitable for the installation of any (except for screw pile) foundation.
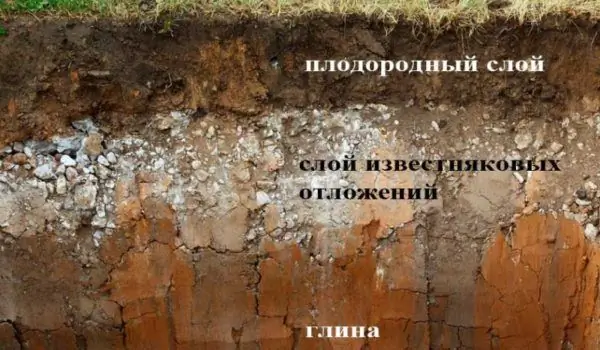
Visual determination of the quality of layers
A shed made of foam blocks has the ability to keep a constant temperature inside the room well, but it still needs additional insulation work. This will exclude the possibility of freezing of walls and destruction of foam blocks. In cases of low temperatures for a long time, it makes sense to insulate not only external, but also internal walls, floors and ceiling of the barn. Today there are several ways to insulate walls:
- Mineral wool.
- Styrofoam or styrofoam.
- Cork plate.
- Penofol.
- Polyurethane foam.
- Expanded clay (for the floor).
Insulating the exterior walls of a barn with mineral wool is a relatively inexpensive method with good thermal insulation properties. Due to its vapor permeability, this material perfectly ventilates not only the blocks, but also the interior of the barn. Mineral wool is fire resistant and durable to use.
There are disadvantages to using mineral wool:
- the properties of this material are preserved only if it is isolated from moisture, otherwise, being saturated with water, cotton wool will significantly reduce its thermal insulation qualities;
- work with this material should be carried out in respirators;
- if installed incorrectly, mineral wool will create additional shrinkage, which can also affect thermal insulation.
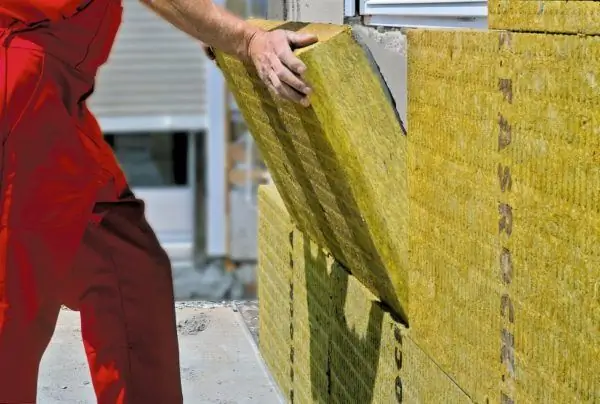
Mineral wool is one of the ways to insulate walls
Insulation of the outer walls with expanded polystyrene or foam is very convenient during installation. Quite often, these materials are referred to as single foam. In fact, these materials have a common basis, but differ significantly in their characteristics.
- the density of the foam is much lower (10 kg per m³) than the indicators of expanded polystyrene (40 kg per m³);
- unlike foam, polystyrene foam does not absorb moisture and steam;
- in appearance these materials differ markedly. Styrofoam has internal granules, and expanded polystyrene has a more uniform structure;
- prices for polystyrene are lower, which is convenient when purchasing it in large quantities for insulation of outer walls;
- expanded polystyrene has a relative strength to mechanical damage.
Unlike mineral wool, this material is cheaper, has excellent frost resistance and is able to isolate sounds well. As thermal insulation, the performance of expanded polystyrene is significantly higher than that of mineral wool.
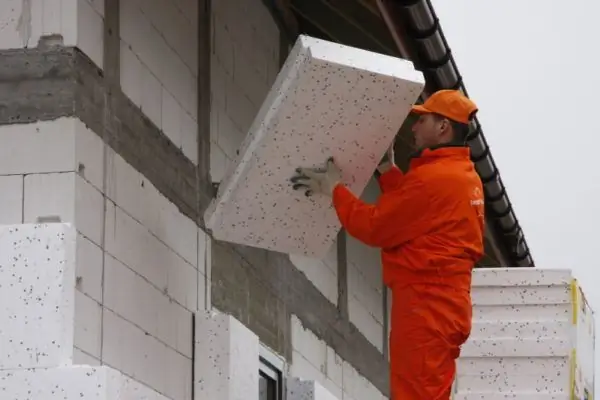
A reliable and cheaper way is insulation with expanded polystyrene
Insulating inner walls with cork has a number of advantages:
- this material adheres perfectly to the adhesive layer;
- the cork structure has very good thermal insulation properties;
- walls covered with cork are excellent at isolating sounds;
- does not require additional finishing, it is often used as a finishing layer.
For insulation with cork, it is not necessary to smoothly plaster the walls.
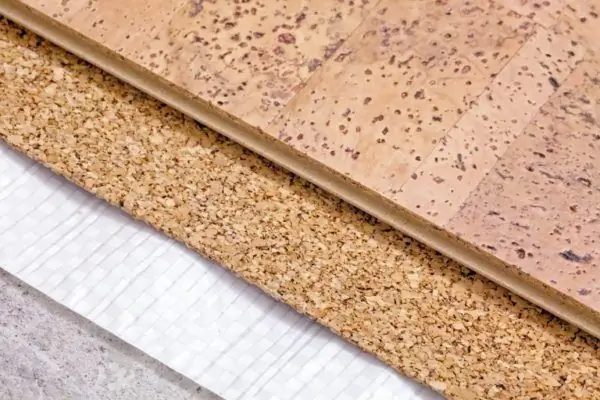
The material is easy to install
The heat-insulating layer of foamed polyethylene (penofol) allows you to keep heat in the room by 97%. This material is used to insulate the interior walls of the barn. When installing it on a wall of foam blocks, small section bars (10x10 mm) are attached. Penofol plates are laid between the beams. The joints are glued with aluminum tape.
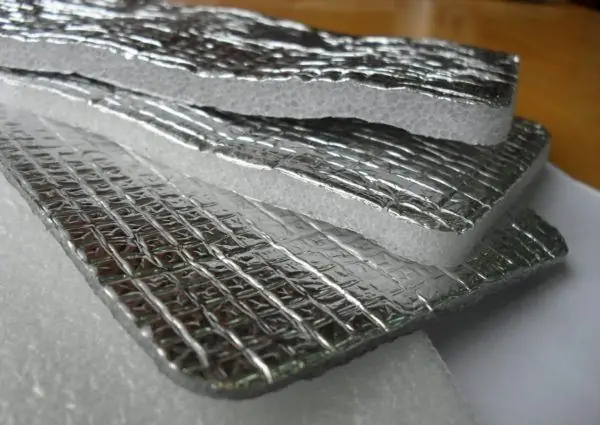
The material is water-repellent
Insulation with polyurethane foam is used for both roofs, external walls and interior decoration. The technology of applying polyurethane foam by spraying greatly facilitates the work of insulating the walls of the shed. Thanks to this property, there is no need to use adhesive solutions. The sprayable polyurethane foam is firmly attached to the wall surface and hardens immediately. This material has found its widespread use due to its advantages:
- when spraying, a heat-insulating layer is formed without seams;
- this material has low thermal conductivity;
- due to its low weight, it can be applied without the use of lags and barriers;
- the cellular structure of polyurethane foam creates tensile-compressive strength;
- the material has a durability (up to 50 years of service, provided that the surface does not succumb to mechanical damage);
- relative resistance to open fire;
- polyurethane foam has a sealed and dense structure, thanks to which there is no need to install a vapor barrier layer;
- insulates well from the wind;
- the material does not rot, is not covered with mold and is unsuitable for the life of rodents and insects;
- has a low degree of moisture absorption;
- reliably isolates from noise and extraneous sounds;
- has a high degree of environmental friendliness when used, since there are no toxic substances in the material;
- relatively inexpensive material.
If we compare the thermal insulation properties of polyurethane foam with other popular materials, then its 50 mm layer has the same qualities as an 80 mm foam layer or 150 mm mineral wool. With its resistance to fire, polyurethane foam surpasses all the previously mentioned materials. It ignites only in close contact with an open fire, and the material does not ignite.
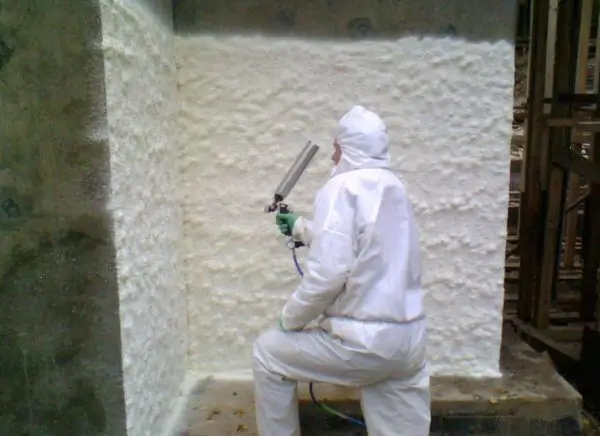
The material is quickly applied to the surface
Insulation of the barn floor with expanded clay gives a good thermal insulation layer. To use this material, a concrete floor is required, on which a lathing of wooden beams with a section of 15x10 cm is installed with a step of 40 to 60 cm. It should be noted that the expanded clay layer should not be less than 10 cm, since a smaller coating thickness with this material loses its thermal insulation properties … Granular expanded clay is poured between the beams of the crate. Then expanded clay granules are leveled so that it does not rise above the wooden structure of the crate. A vapor barrier layer is spread on top, which is covered with a sub-floor made of plywood or OSB boards.
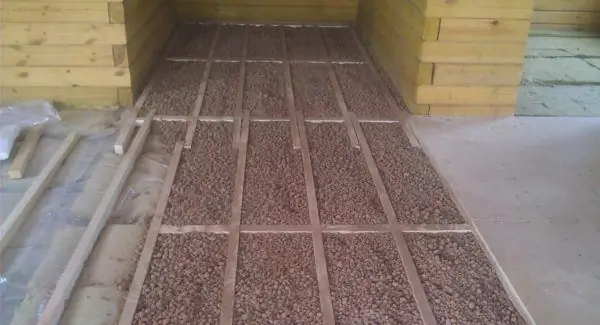
This material reliably protects floors
Required tools
To build a shed from foam blocks you will need:
- Measuring tools - tape measure, building level, square and ruler.
- Tools for the manufacture of adhesive mortar - a concrete mixer or a drill with a special mixer nozzle, a container for cement mortar, bayonet shovels for digging trenches and shovels for supplying mortar.
- Large watering can.
- Pump and flexible hose supplying solution.
- Ladders.
- A hammer.
- Putty knife.
- Self-tapping screws and nails.
Step-by-step instructions for making a barn with your own hands
When all the tools are ready, and the necessary materials are purchased, you can proceed to the direct construction. A strip foundation was chosen for a foam block shed. To install it you need:
-
First of all, you need to level the place for the future building. When the site has a flat surface, you need to make markings according to the dimensions of the future shed. This is done with a cord and pegs.
marking a plot for building a barn It is more convenient to do this with a cord
-
Dig a trench around the perimeter of the future barn. It is desirable that its depth be below freezing point. Usually it is from 30 to 50 cm, and in some soils (for example, with a high clay content) up to 100 cm. The width of the trench should be 30 cm.
troning under the strip foundation It is advisable to make the depth below the freezing point
-
Then pour sand into it, which must be tamped to obtain a uniform layer, 10 cm thick. A layer of crushed stone 10 cm thick must be poured onto the sand pillow. A waterproofing layer should be laid on the sand layer with crushed stone along the entire perimeter of the trench. This is necessary to prevent liquid concrete from absorbing into the lower layers. Waterproofing should cover not only the top of the rubble, but also the earthen walls of the trench.
the bottom of the trench for the strip foundation Compacted wet sand covered with gravel
-
Make a formwork structure for pouring concrete. It is usually made from wood planks or metal. The height of the formwork should be above ground level and reach the height of the base of the future shed. To create a strong formwork structure, it is fixed with spacers and clamps, and the upper part is fixed with props. Lay a metal frame or reinforcing mesh on the waterproofing layer along the entire perimeter of the trench. This requires metal rods with a thickness of 10 to 12 mm.
wooden formwork Reinforcement cage firmly holds the wire
-
Pour the reinforcement frame with M200-250 grade concrete. The entire perimeter must be filled in one go. To avoid cracking of the concrete, it is not recommended to pour it in rainy weather or in extreme heat. Concrete hardens under normal conditions for about 4 weeks. This is the time when it can withstand the design loads. These setting times are called control times.
strip foundation under the barn The monolithic foundation structure will become a reliable support for the building
- When the concrete base has hardened, it is necessary to prepare its surface for further construction. Concrete should be cleaned of dirt and dust. If there are any defects in the base (sharp protrusions), they must be processed. Before laying the first row of foam blocks, it is necessary to cover the top of the concrete base with a waterproofing material. As it is used waterproofing or roofing material.
- For foam blocks, prepare an adhesive mortar of sand and cement in a 1: 3 ratio.
-
Start laying the first row of foam blocks. It must be produced from the corners of the future building and continue along the entire perimeter. The thickness of the seam when laying foam blocks should not exceed 30 mm. After laying the first row, check the wall for evenness. For the strength of the walls, reinforcing rods with a diameter of 0.8 cm are used. They are laid on top before laying every fourth row of foam blocks.
laying foam blocks The reinforcement will give the walls additional strength
-
When the walls are erected, and the adhesive mortar of the joints has hardened, proceed to the installation of the roof. To the upper row of the wall masonry, on metal studs, attach beams with a section of 50x150 mm, which will serve as a mauerlat. The distance between the studs should not exceed 120 cm. Under the Mauerlat, a waterproofing layer must be laid, which should be used as a double layer of roofing felt or waterproofing.
top of the wall with mauelat A layer of waterproofing will protect wood and blocks from destruction
-
Install the outer trusses that form the gables. They can be leveled and reinforced with temporary stops. The structures of the outer trusses must be temporarily reinforced with a board nailed to the wall of the house. This is done provided the wall is perfectly flat. For convenience, you need to make a template with all cuts and corners. All rafters are best assembled on the ground, and then lifted for installation. Twine is pulled between the installed trusses, at the level of the ridge board and on both sides (at the end of the rafter legs).
installation of the rafter system The cord is required for accurate installation
-
The exposed extreme farms are fixed to the Mauerlat. The following trusses are placed according to the taut twine. For convenience, it is necessary to make marks on the Mauerlat, and only then lift and install them. For better rigidity of the fasteners, it is better to use metal fasteners and overlays. Over time, the wooden parts will dry out, and the nails will not provide the necessary rigidity of the fasteners.
strengthening the structure of the rafters Metal fasteners will create additional rigidity
-
Cover the installed rafter system with a layer of waterproofing membrane, on top of which the lathing is installed. It is better to make one layer of beams with a section of 50x60 mm under the metal tile. Install roofing material.
installation of metal tiles The light weight of this material does not create a significant load on the rafter system
- Proceed with the insulation of the outer walls of the barn. In our case, polystyrene is chosen as a heater. Clean the wall surface from dust and dirt. If the wall has defects in the form of protruding particles, it is necessary to level the surface.
- Apply a primer to the wall (eg polymin-AC5).
-
Attach the plinth strips with anchors and dowels, which will serve as a support for the first row of slabs and anchoring for corners.
preparation for installing the heater The aluminum strip will reinforce the foam slabs
- Prepare an adhesive mass for foam boards (for example, polymin-P22). Pour only cold water and mix with a drill with a mixer nozzle. Leave the solution for 5 minutes.
-
Apply glue around the entire perimeter to the foam plates, at a distance of 3 cm from the edge. It is imperative to make gaps in the glue for air to escape. In the middle of the slab, apply the glue in patches of about 10 cm in diameter.
applying adhesive to the foam board For the wall to "breathe" it is necessary to leave gaps in the glue
-
Place the slab against the wall and press firmly. Do not allow glue to get into butt joints. Reinforce the slabs glued to the wall with plastic dowels with special expansion elements.
reinforcement of foam plates with special dowels Expansion on the dowel will additionally secure the slab to the wall
- The slopes of doors and windows are reinforced with perforated aluminum squares.
-
Cover the entire surface of the foam boards with a layer of 3 to 4 mm of adhesive. From above, using a wide spatula, spread the reinforcing mesh. It must be evenly drowned in the glue applied to the wall. Leave for a couple of days to dry.
reinforcing mesh covering Its use will level the surface of the wall for the topcoat
- Cover the surface with plaster or paint.
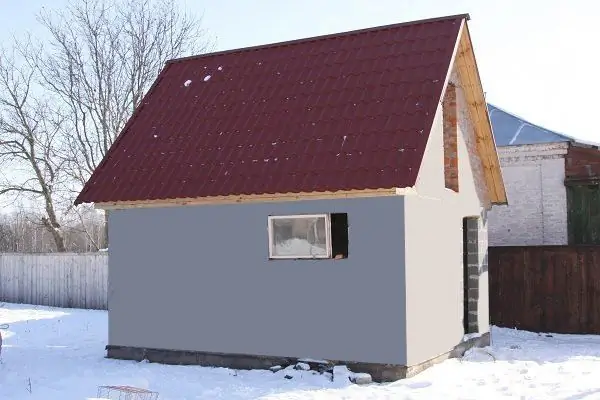
With painted walls and metal tiles, the barn looks more attractive
Video: How to build a shed from foam blocks yourself
From all that has been said, we can conclude that building a shed from foam blocks is not such a difficult business. You just need to be able to use tools, have a great desire to create and own some building skills. Your efforts will be rewarded. As a result, you will build a high-quality and necessary building that will last more than one year. It will become doubly pleasant to realize that you did this work yourself and did not spend extra money on planners, estimators, builders and other specialists. Moreover, now you have a wonderful experience, which will certainly come in handy in the future, and will give you the opportunity to share it with your loved ones.
Recommended:
How To Make A Bar Stool With Your Own Hands From Wood, Metal And Other Materials + Drawings, Photos And Videos
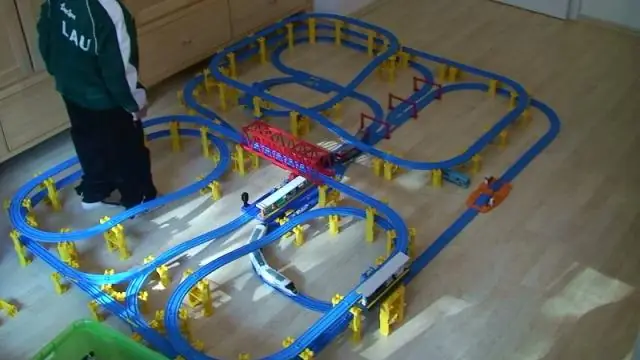
Bar stools manufacturing options. Required tools, materials used. Step-by-step description of the manufacturing process with a photo
How To Make And How To Paint A Concrete Fence With Your Own Hands - A Step-by-step Guide With Photos And Videos
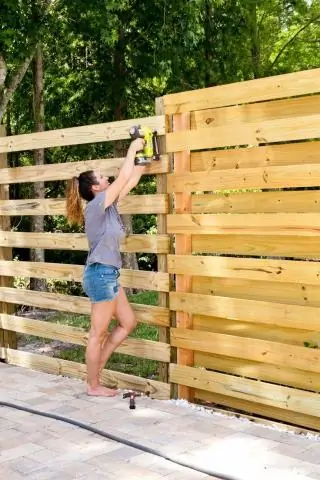
Advantages and disadvantages of concrete barriers. Instructions and tips on how to make a concrete fence with your own hands
How To Make A Kite With Your Own Hands At Home: Options With Drawings And Sizes + Photos And Videos
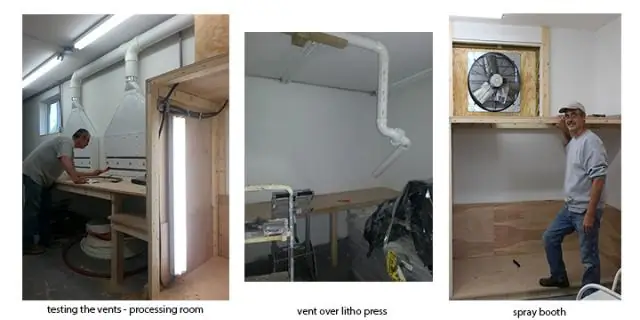
DIY kite: the necessary materials, diagrams, drawings, manufacturing steps. How to make a kite of different shapes. Secrets of a Successful Launch
How To Make A Slime At Home With Your Own Hands - Without Sodium Tetraborate And Glue, From Hand Cream, Shaving Foam And Other Ingredients, Recipes With Photos And Videos
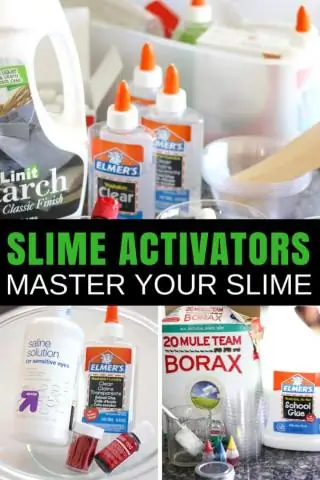
Is it possible to make a slime at home. Types of slimes and recipes for their manufacture, depending on the desired properties. Toy care features
Shed Roof For A Garage, How To Do It Right, Including With Your Own Hands, As Well As The Features Of Its Device And Installation
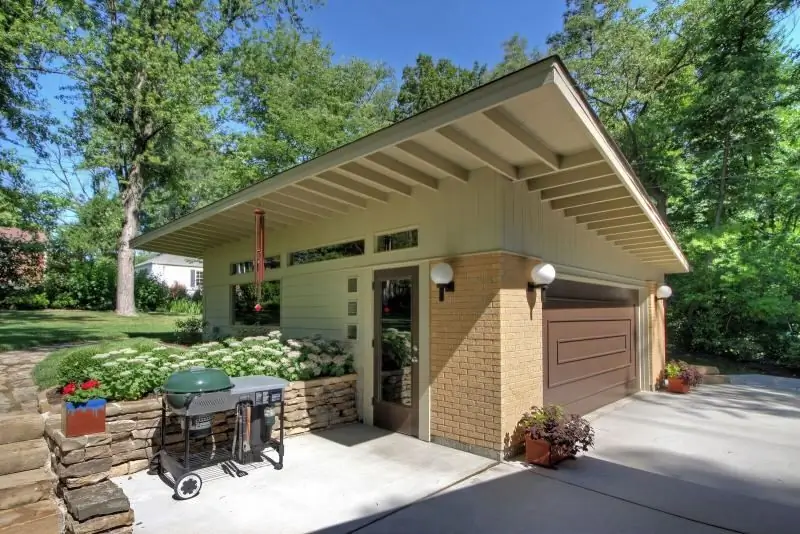
Existing types of pitched roofs. Features of creating and maintaining such a structure in their own hands. What tools and materials you need to have