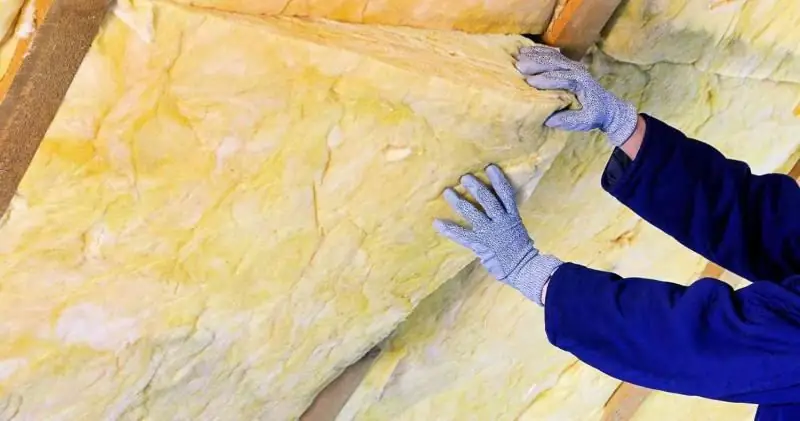
Table of contents:
2025 Author: Bailey Albertson | [email protected]. Last modified: 2025-06-01 07:32
Rules for insulating the roof of a wooden house outside and inside
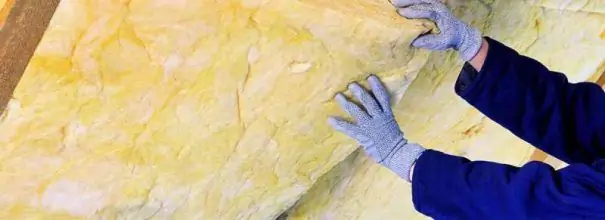
It is a mistake to believe that a wooden house will turn out to be warm by itself, so to speak, by definition. Like any other building, it is advisable to insulate it, especially the roof, through which warm air leaves the premises due to convection. It is the insulation of the roof of a house made of wood that we will discuss in this article.
Content
-
1 What insulation to choose
- 1.1 Mineral wool
- 1.2 Foams
- 1.3 Ecowool
-
2 Do-it-yourself roof insulation of a wooden house
-
2.1 Options for insulating a flat roof
- 2.1.1 External insulation of a flat roof
- 2.1.2 Video: thermal insulation and flat roof sloping
- 2.1.3 Internal insulation
- 2.1.4 Video: ceiling insulation with mineral wool
-
2.2 Insulation of a pitched roof on wooden rafters
2.2.1 Video: Pitched roof insulation
-
-
3 Features of the use of hydro and vapor barrier films
- 3.1 Vapor barrier film
-
3.2 Waterproofing foil
- 3.2.1 Plain Film
- 3.2.2 Vapor permeable membrane
- 3.2.3 Video: Super Diffusion Membrane or Waterproofing Film
What insulation to choose
The main requirement is that the material is as heat-conducting as possible. The ability of a heat insulator to retain heat is evaluated by a physical quantity - the coefficient of thermal conductivity (CT), which has a unit of measurement W / m * 0 С.
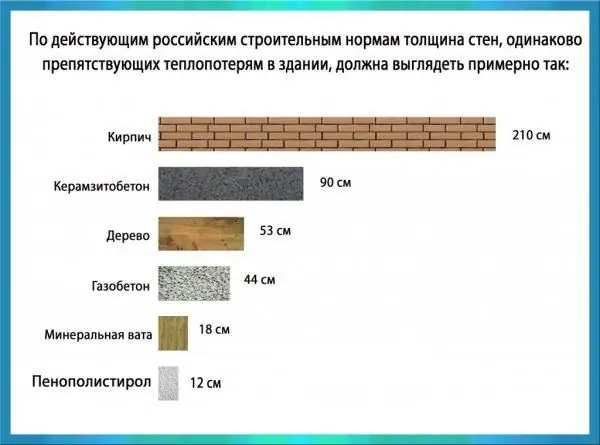
A layer of 18 cm of mineral wool is comparable in thermal conductivity to a brick wall 210 cm thick
The lower it is, the better. Today, the most effective are heat insulators, the CT of which is in the range of 0.034-0.042 W / m * 0 C. These include:
- mineral wool;
- foams;
- ecowool.
Quite important for insulation is such a characteristic as vapor permeability, the unit of measurement of which is mg / m * h * Pa. As the name implies, it reflects the ability of the material to pass water vapor, that is, in fact, it is about air permeability. Those materials that have high vapor permeability are popularly called "breathable". In general, "breathing" enclosing structures, if they let in steam in moderation, is good, because part of the warm and humid air available in the room will be removed through them, and this will reduce the ventilation rate.
Accordingly, the heat loss will be lower. For example, in houses built according to Soviet standards - with vapor-permeable walls, with a single hourly air exchange, the share of heat loss due to ventilation is 40%. In Europe, where walls are usually sheathed with a vapor barrier film, the required air exchange rate per hour is 2, and the proportion of heat loss through ventilation increases to 60%.
But in the case of the roof, the vapor permeability of the insulation does not play a special role, and they usually refrain from the device of a "breathing" roofing cake. After all, steam due to convection enters here in the largest quantities and the probability that it condenses on the outside of the insulation or even inside it is quite large. And condensate, that is, water, is a completely different story: there is rotting, and the destruction of material during freezing, and a significant increase in thermal conductivity.
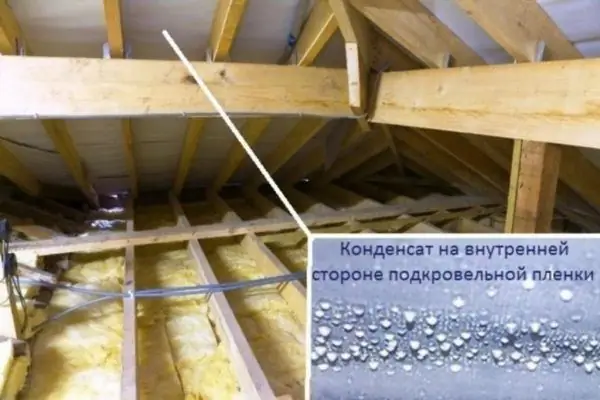
With improper insulation on the roof, condensation forms, which quickly destroys the rafter system and the materials of the roofing pie
Now it is worth taking a closer look at thermal insulators that provide the most effective protection.
Mineral wool
Mineral wool threads are made of molten natural stone (basalt wool), glass or slag, so it:
- does not burn;
- not of interest to the biological environment (fungi, mold, rodents);
- not afraid of high temperatures;
- absorbs sound well (due to its soft structure);
- has a high vapor permeability;
-
does not emit harmful substances when heated.
Mineral wool Mineral wool is not subject to decay, is not afraid of high temperatures and has high sound insulation performance
The last point can be considered conditional. The fact is that mineral fibers are short and they have to be glued together using compounds based on phenol-formaldehyde resin. It is believed that, subject to the production technology, the emission (release) of toxic substances by mineral wool is scanty, but today there are very often cheap varieties on sale, most often of Chinese production, which may well turn out to be unsafe.
In order not to worry about this, you can purchase mineral wool with an acrylic binder - it is considered absolutely safe
Mineral wool has features that it is useful for a potential buyer to know about in advance:
- the material is relatively expensive;
- it absorbs water well (hygroscopicity), while completely losing its ability to retain heat;
- during installation, it emits dangerous stinging dust, from which you have to protect yourself with a respirator, glasses and gloves (clothes are thrown away after installation).
Today, thanks to the well-thought-out and well-funded "promotion" of basalt wool, there is an opinion in society that it is the most advanced and modern variety of mineral wool. Glass wool is presented as an outdated material, moreover, terribly prickly and inconvenient. Such PR allows you to sell basalt wool at exorbitant prices, but you shouldn't believe it.
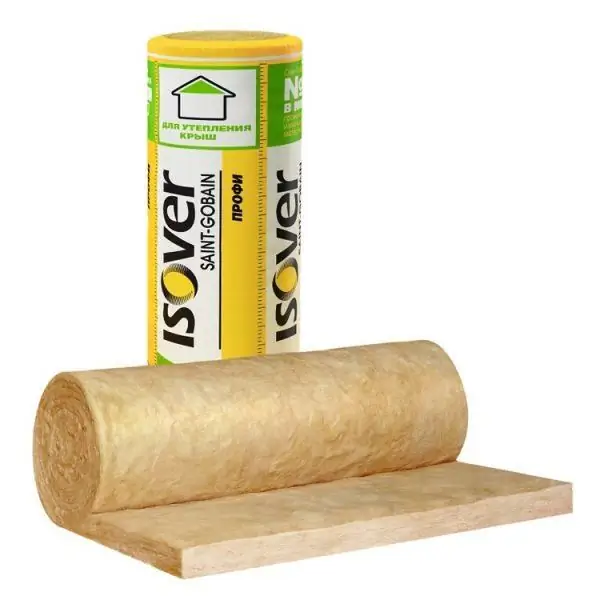
Izover is made on the basis of the highest quality glass fibers and practically does not emit any harmful components during installation
Modern glass fibers are made very thin, so that they no longer prick hands, thus, glass wool is in no way inferior to basalt wool. Many well-known manufacturers, such as Isover, make their products out of it, just because of the powerful anti-advertising it is not advertised.
It should be noted that the density of mineral wool varies over a very wide range - from 35 to 450 kg / m 3. Accordingly, the load on the roof when insulated with mineral wool of different types can be very different.
Styrofoam
This term refers to all materials obtained by foaming polymers. For example, what we used to call polystyrene in everyday life is granular polystyrene foam (PPS).

Foam is made by foaming polymer materials, so it contains a lot of air and weighs very little
There are also polyurethane foam (PPU), polyvinyl chloride foam (PVC), polyethylene foam (PPE) and much more difficult to wear materials such as polyisocyanurate (used in sandwich panels). The structure of foams is not fibrous, like mineral wool, but porous. Therefore they:
- moisture resistant;
- have low vapor permeability.
All of this applies to most foams, but there are exceptions. The most famous is foam rubber, which is a kind of polyurethane foam: it, as you know, absorbs moisture and passes air with steam very well.
The widespread use of foams is due to two important advantages:
- low cost;
- the absence of a pronounced harmful effect (mineral wool, we recall, is very dusty).
In everyday life, the following types are usually used:
- For insulation of flat surfaces - expanded polystyrene. Along with granular PPP, in which, for example, household appliances are packed, extruded is produced. Its structure is not divided into granules, but is a solid porous polymer. Extruded PPP is much more expensive than granular, but it is capable of withstanding significant loads - up to 50 t / m 2, which makes it possible to use it for thermal insulation of operating roofs and floors.
-
Curved surfaces - with polyethylene foam. It can be produced under various trade marks, for example, "Penoplex". PPE, unlike PPP, is a soft, flexible material and is supplied in rolls. Having such a structure, it also absorbs sounds very well, while PPS and other rigid polymeric foams do not have this ability.
Polyethylene foam It is convenient to insulate curved roof sections with polyethylene foam
-
Hard-to-reach places (cracks, seams, cracks, cavities) - with polyurethane foam. This material exists not only in foam rubber, but also in the well-known polyurethane foam - it is it that is used to fill all of the above. Foam made of polyurethane foam could also be used to insulate flat surfaces, as it forms a seamless coating, but it is expensive.
Insulation with polyurethane foam Polyurethane foam is nothing more than the well-known polyurethane foam
Polymeric heaters also have disadvantages, and they are quite serious:
- Even at relatively low temperatures (for PPS - starting from +80 o С), the processes of thermal decomposition begin in materials, leading to the release of gases harmful to health. This must be taken into account by the owners of houses with roofs made of corrugated board or metal tiles - in the summer, such roofs get very hot.
- All polymers are flammable, and during combustion they emit highly toxic smoke in large quantities. By introducing fire retardants into the composition, it is possible to lower the flammability group to G1, but under conditions of a high temperature characteristic of a fire, such materials still smoke strongly. True, smoke on the roof of a private house is not so dangerous, this problem is relevant for high-rise buildings that cannot be insulated with foam in any case (smoke can poison residents of the upper floors).
Foam plastics attract rodents, who enjoy eating them with pleasure. This problem is relevant just for residents of private houses
Ecowool
Ecowool is one of the most effective insulation materials, but at the same time it is extremely cheap. In essence, it is shredded paper impregnated with an antiseptic and flame retardant.
There are two ways to use this material:
-
Dry. It is blown out by a special installation or manually filled into a closed cavity, for example, behind a wall cladding.
Warming with dry ecowool Dry ecowool is blown out behind the pre-assembled skin
-
With moisture. Feeding with humidification can only be carried out using special equipment. When wet, the lignin that is part of the paper exhibits adhesive properties (papier-mâché effect), as a result of which the ecowool sticks to the surface (even to the ceiling) and forms a hard, seamless coating.
Application of wet ecowool The lignin contained in ecowool, under the influence of water, turns into an adhesive and gives the coating the necessary strength
In everyday life, ecowool has not received widespread use, since:
- the fire retardants and antiseptics used for its impregnation are moderately toxic;
- the material is flammable: flammability group G2 (moderately flammable materials), according to flammability characteristics - B1 (highly flammable).
In addition to those indicated, when insulating the roof, bulk heaters can be used - expanded clay, sawdust, slag. They are less effective, for example, in expanded clay, depending on the density of the CT, it ranges from 0.1 to 0.18 W / m * 0 С, but they are very cheap.
Do-it-yourself roof insulation of a wooden house
The work technique depends on the type of roof.
Flat roof insulation options
Flat roofs are erected on small buildings in the southern regions where rainfall is minimal. There are two types of insulation:
- outdoor;
- internal.
It is imperative to start with the outside, and only if it turns out to be insufficiently effective, they also perform internal insulation.
External insulation of a flat roof
You need to act in the following sequence:
- The roof is covered with a vapor barrier film, which can be fixed with glue.
-
Next, a heater is laid out on the roof - mineral wool plates, expanded polystyrene or expanded clay. Mineral wool slabs should be chosen rigid enough to carry the load. For the same reason, only extruded polystyrene foam should be used. These materials can be glued with special mastic, or they can be screwed to the ceiling with dowels. The first option is preferable, because the dowels act as a cold bridge.
External insulation of a flat roof Thermal insulation boards are laid along the waterproofing layer and fixed to mastic or dowels
-
On the upper edge of the insulation, a slope of 7 degrees is formed, which is necessary for water to drain. If expanded clay is used, it must be properly leveled. In the case of PPP or mineral wool, special plates made of these materials are used, one face of which has a corresponding slope. These slabs must be laid so that they overlap the joints in the main insulation layer.
Flat roof slope To form a slope along which water will flow, use special insulation plates with a beveled surface
- When laying the second layer, it is very likely that the first one can be damaged, therefore, in order to distribute the weight of the installer, it is highly desirable to lay boards on the insulation (you should only walk on them).
- In the next step, foam plastic or mineral wool slabs are screwed with dowels or self-tapping screws to the ceiling, if they were not glued with mastic. Special fasteners should be used - the so-called disc-shaped, characterized by large caps (so as not to push through the insulation).
Metal fasteners contribute to heat loss, and to a very significant extent: it is calculated that a metal cold bridge with an area of only 10% of the area of the insulated section reduces the efficiency of the heat insulator by 90%, that is, it works by only one tenth
Next, a waterproof coating is laid. Previously, roofing material was used in this capacity, but today it is considered outdated: frost resistance is too low for this material, it also does not tolerate ultraviolet (UV) radiation and temperature changes. UV rays deprive plasticity and mastic, which are used for gluing roofing material, so that as a result, the service life of the roof is reduced to only 5-7 years.
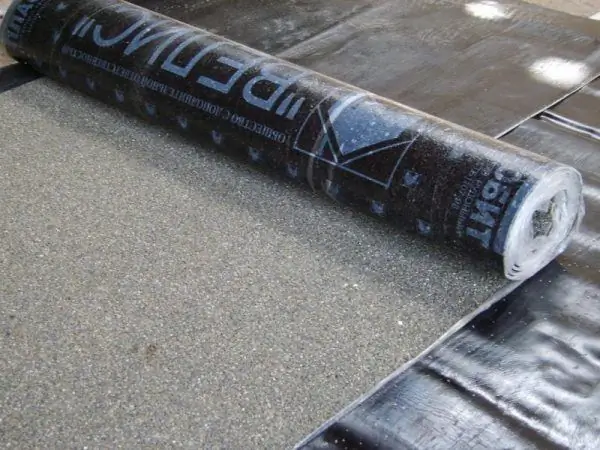
Modern roll materials last 15-20 years
More durable (last 15-20 years) are modern materials:
- bituminous - folgoizol and metalloizol (foil was used instead of cardboard);
- bitumen-polymer - hydrostekloizol, rubemast, glass-melt, bikrost, etc. (thanks to polymer additives they are more plastic).
There are also such rolled roofing materials that fit in just 1 layer:
- Kromel;
- Rukril;
- Firestone.
Instead of bitumen, rubber is used in them, the service life is 25 years. Finally, you can make a seamless self-leveling coating of polymer or bitumen-polymer mastic:
- "Polikrov M-120";
- "Polikrov M-140";
- "Polikrov-L" (serve up to 25 years);
- Blam-20 (20 years old).
It should be borne in mind that with a small thickness of the insulation in winter, moisture can condense under the vapor barrier film, coming from the room through the ceiling. Before insulating the roof, you need to perform a calculation using one of the heat engineering calculators posted on many sites. If the calculation shows that during the cold period the temperature under the insulation will be below the dew point, the vapor barrier film will need to be laid on the ceiling inside the room.
Video: insulation and flat roof sloping
Internal insulation
If it was not possible to achieve the desired effect by external insulation, the heat insulator is also placed on the inner side of the ceiling. This is done in the following order:
- The protruding irregularities are eliminated on the ceiling.
- Next, a frame made of wooden blocks is attached. The distance in the light between them should be equal to the width of the insulation slab (we use mineral wool or PPP slabs).
-
Insulation is placed between the bars. Ideally, it should be held in place with a slight spacing force. If the slabs fall out of the frame, they can be temporarily fixed with a stretched cord.
Ceiling insulation Insulation plates should be kept inside the frame by installing a rasp
- The insulation is covered with a vapor barrier film, which must be shot to the frame with a stapler (construction stapler).
- The frame is sheathed with some kind of sheet material - drywall, gypsum fiber sheets, plastic panels or just plywood, and then the finishing is done.
Video: insulation of the ceiling with mineral wool
Insulation of a pitched roof on wooden rafters
The vast majority of private houses, including wooden ones, are equipped with pitched roofs. The latter can be divided into two types:
- Constructed from laminated veneer lumber. The boards from which such a bar is made are pre-dried, so such houses do not shrink. Thus, insulation work can be carried out during the construction phase.
- Constructed from logs or beams of natural moisture. For some time, such structures change their geometry somewhat due to shrinkage. For this reason, even the rafters are installed on them according to a special scheme - on sliding supports. It is advisable to take up the insulation of the slopes after shrinkage (usually it takes 0.5-1 year), and before that time you can temporarily insulate the attic floor by laying the insulation directly on it.
At the moment, the following version of the device of the insulated pitched roof is being practiced:
-
A waterproofing film is laid on top of the rafters. It is distinguished by increased strength; it is impossible to use a vapor barrier film as such. Waterproofing, regardless of its type, is laid with a sagging of 2-4 cm. If it is drawn from separate strips, they must be laid with an overlap of 10-15 cm, carefully gluing.
Laying waterproofing The waterproofing film is laid with a slight slack and is fixed with counter-lattice bars
- The film is fixed with a counter-lattice - boards 3-5 cm thick, which are packed over the rafters along them. The boards should be the same width as the rafters.
-
A crate is stuffed onto the counter-lattice (across the rafters), and a roof covering is placed on it. Thus, a so-called ventilation gap is formed between the waterproofing film and the roofing, which, due to the presence of holes in the cornice and ridge, will be blown out. The movement of air will carry out the steam that enters here from the living room, preventing it from condensing on the roofing.
Lathing The main lathing on which the finishing coating will be laid is spaced from the waterproofing coating by the thickness of the counter-lattice bar, which is quite enough for ventilation of the under-roof space
- Next, a heater is mounted - plates of foam or mineral wool. Ideally, the width of the slabs should be equal to the gap between the rafters. Recall that for such purposes, mineral wool slabs with an elastic edge are produced, which can be held between the rafters or any other surfaces due to the thrust force.
-
If the insulation is completed at this stage, the rafters will act as a cold bridge. Of course, the thermal conductivity of wood is lower than that of metals, but in comparison with the thermal conductivity of a heater, it is quite high - 0.15 versus 0.004 W / m * C. Therefore, it is highly desirable to lay another heat-insulating layer from below. It is better to use soft material: if mineral wool slabs are laid between the rafters, then we use mats from the same material; when using PPS - foamed polyethylene coated with foil (it should face the room). If the rafters are completely hidden, their position must be somehow indicated, for example, with a stretched nylon thread. In the future, they will be needed to fasten the crate.
Pitched roof insulation Air circulation in the under-roof space is carried out due to the flow of air into the ventilation gap under the crate and its output through the cold triangle of the ventilated ridge
The second layer of insulation can be grabbed with staples to the rafters or temporary fastening in the form of a stretched cord can be applied. In the future, it will be fixed with a crate.
- A vapor barrier film is laid on top of the insulation, which can be immediately pressed with lathing bars (located perpendicular to the rafters). The bars are screwed to the rafters with self-tapping screws. In the attachment area, the second layer of insulation will be compressed, allowing the crate to be screwed on tightly enough. The bars must be used in such a height that a small gap remains between the casing and the vapor barrier film (in case of condensation on the film).
- At the end, sheathing material is screwed to the crate - drywall, lining, etc.
Video: insulation of a pitched roof
Features of the use of hydro and vapor barrier films
When insulating a roof, the result is greatly influenced by the correct selection of materials used to protect the insulation from moisture and vapors.
Vapor barrier film
Instead of polyethylene, you can use a polypropylene film. It is distinguished by the presence of an absorbent layer, which absorbs moisture during steam condensation, and then, when the humidity in the room returns to normal, evaporates it.
If the insulation was carried out using mineral wool, which has a high vapor permeability, you can try to use a membrane instead of a vapor barrier film.
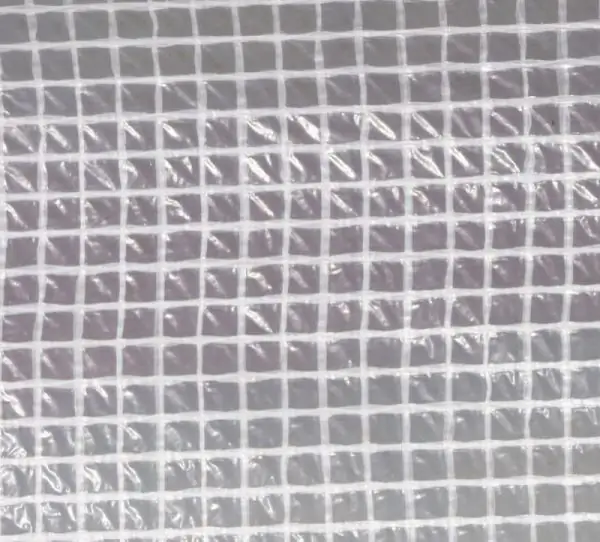
The vapor barrier layer should exclude vapor condensation on the insulation
The vapor permeability of the latter should be such that the vapor penetrating into the mineral wool does not condense in its outer layers and has time to weather out
To clearly determine this value, you need to order a calculation from a civil engineer or heating engineer.
You can also use one of the aforementioned heat engineering calculators. As you can see, using a membrane instead of a dull vapor barrier, you have to go along a more complicated path, but the roofing cake turns out to be "breathing", which means that the heat loss for ventilation will be lower.
Waterproofing film
There are two types of waterproofing film:
- Vapor tight. The simplest and most inexpensive option, made of polyethylene or polypropylene.
- Vapor permeable. Such films are usually called membranes. The material is impervious to water, but has microscopic perforations through which steam can penetrate. Membranes are produced under various trade marks; for example, Yutavek and Yutafol films are quite well-known. Such material is somewhat more expensive than the usual vapor-proof material, but, as will be shown below, it is more practical.
The method of placing the insulation depends on what was installed as waterproofing.
Plain film
In this case, the insulation must be positioned so that it is separated from the film at some distance. Thus, a second ventilated gap is formed, due to which steam seeping through the insulation will be removed to the outside. If you place the heat insulator close to the film, then the steam will condense on it, causing the insulation to get wet (the mineral wool loses its thermal insulation qualities) and rafters (leads to decay).
The distance in question should be at least 2 cm. That is, when the waterproofing film sags by 3 cm, the insulation does not need to be brought up to the upper edge of the rafters by 5 cm. You can hammer in carnations as stops. The inner edge of the insulation slab should not protrude beyond the lower edge of the rafters. If the height of the cross-section of the rafters is not enough to accommodate the insulation of the required thickness, bars or boards must be nailed to them from below.
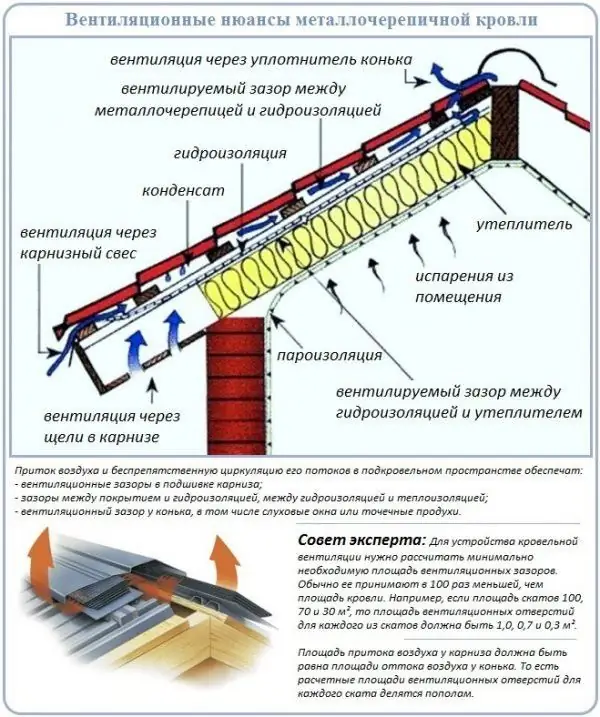
The first ventilation gap is formed between the waterproofing and the topcoat, the second between the insulation and the vapor barrier
If a mineral wool of a particularly low density (which is well blown through) is used as a heater, it makes sense to wrap it on top with a vapor-permeable windproof film
Vapor permeable membrane
In the case of using a vapor-tight membrane, the insulation must be laid close to it.
For mineral wool, this option is more preferable, since the film will simultaneously play the role of wind protection.
It is important that the insulation fits snugly enough to the rafters. If the width of the slabs is not enough for this, the gaps between them and the rafters must be filled with scraps of mineral wool mats (when using mineral wool slabs) or polyurethane foam (when using PPS boards).
To prevent the insulation from falling out, it can be temporarily fixed with a stretched nylon cord
Video: Super Diffusion Membrane or Waterproofing Film
According to the laws of physics, the air heated in a dwelling rises upwards, therefore, special attention should be paid to the issue of roof insulation. It should be borne in mind that warm air carries with it a large amount of water vapor, and the roof covering, by definition, is vapor-tight. Therefore, such structural elements as a ventilation gap, membrane and / or vapor barrier must be present in the roofing cake.
Recommended:
Insulation Of The Roof From The Inside With Foam: Description And Characteristics Of The Material, Installation Stages + Video And Reviews
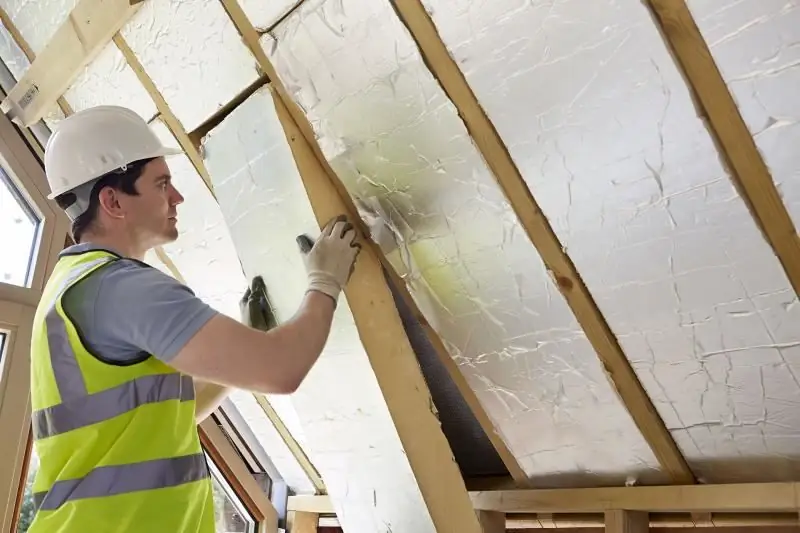
How to choose foam for roof insulation. How to properly form a roofing cake. Styrofoam stacking and cutting methods
Ceiling Insulation In A House With A Cold Roof, How To Do It Right
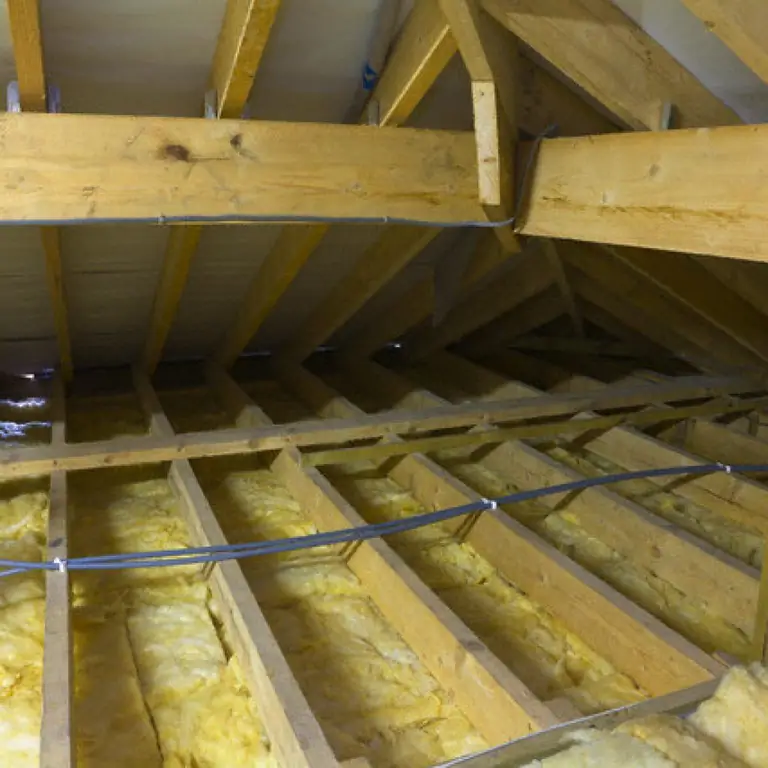
Do I need to insulate the ceiling in a house with a cold roof? Types and methods of insulation. Materials and technologies used for thermal insulation of the ceiling
The Structure Of The Roof Of A Wooden House, Including The Main Nodes Of The Roof, As Well As What Material Is Better To Use
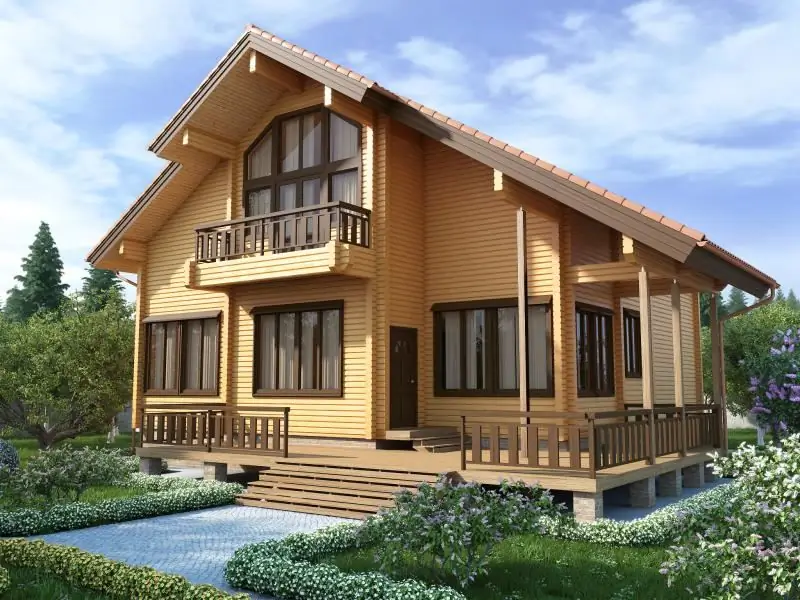
Roof device of a wooden house. The main units, elements and types of roofing. Insulation, decoration, repair and replacement of the roof of a wooden house
Waterproofing The Roof With Liquid Rubber, How To Do It Right, Including Preparing The Roof For Work
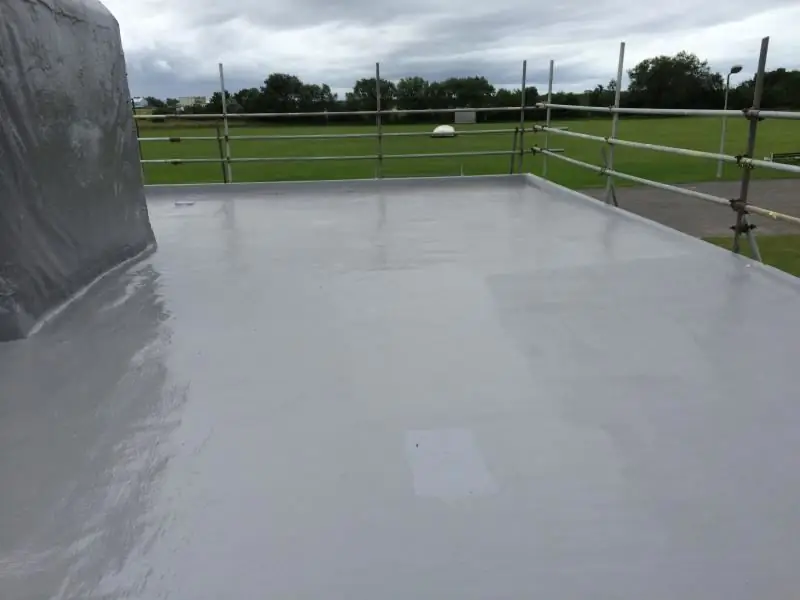
Liquid rubber: properties and characteristics. Calculation of the material. Technology and methods of application. Step by step instructions for work
Installation Of Roof Vapor Barrier, How To Do It Right, Including Which Side To Put On The Roof
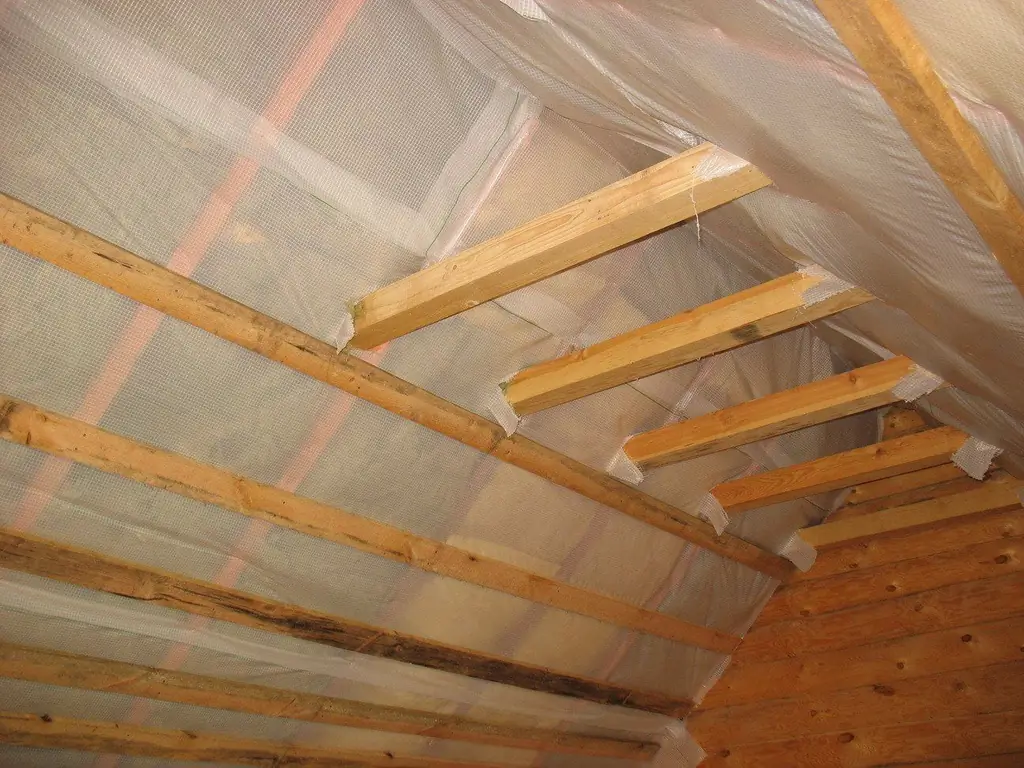
Why do you need a vapor barrier and what materials can be used. Rules for arranging a roof vapor barrier: how to avoid mistakes. Photo and video