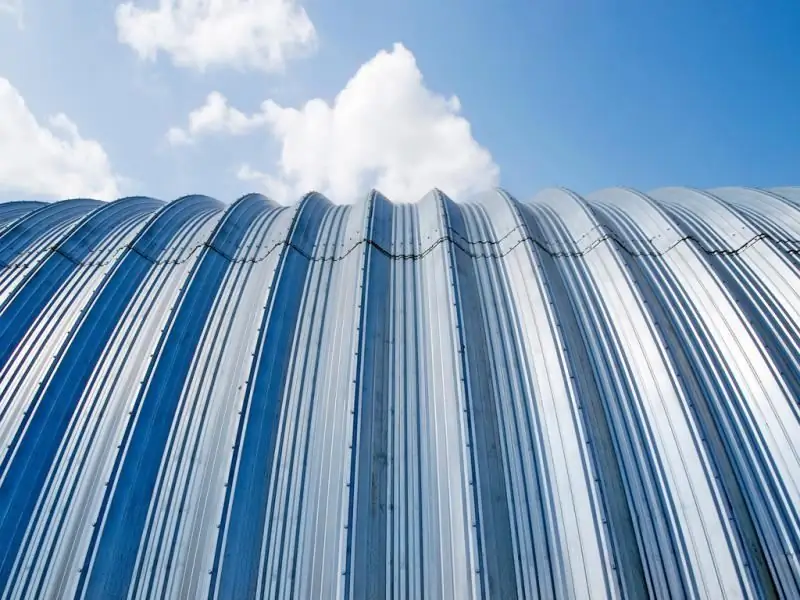
Table of contents:
2025 Author: Bailey Albertson | [email protected]. Last modified: 2025-06-01 07:32
Hangar roof: from material selection to finished roof maintenance
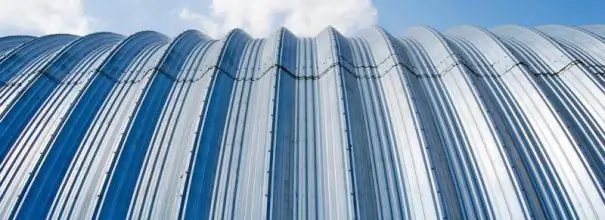
Frame hangars have proven to be the most efficient and cost-effective structures in many areas of life, from sporting events to storing grain crops. But the correct construction of a hangar is associated with many nuances, most of which are related to the roof. It is a poorly made roof that most often causes the destruction of the hangar and financial losses of its owner. Therefore, information on the correct roof structure will be useful both to those who are going to build / buy a hangar and to those who wish to check the quality of the existing structure.
Content
-
1 Types of roofs in hangars
- 1.1 Hangars with a pitched roof
- 1.2 Hangars with a gable roof
- 1.3 Hangars with polygonal roof
- 1.4 Hangars with arched roof
-
2 Insulation of hangars
-
2.1 Insulation of the roof of the hangar PPU
2.1.1 Table: comparison of thermal conductivity indicators of different types of insulation
- 2.2 Insulation of the hangar roof with cotton wool
- 2.3 The roof of the hangar made of sandwich panels
-
- 3 Hangar roof device
-
4 How to make a roof for a hangar with your own hands
- 4.1 What material to choose for the roof of the hangar
-
4.2 Building a roof for a hangar step by step
4.2.1 Video: construction of a metal frame for a small hangar
-
4.3 Sheathing of the arched roof of the hangar with corrugated board
4.3.1 Video: sheathing of the arched roof of the hangar with profiled sheet
-
4.4 Installation of a pitched roof of a hangar made of sandwich panels
4.4.1 Video: how to cut sandwich panels
-
5 Hangar roof repair
- 5.1 Leaking roof
- 5.2 Deformation of trusses
Types of roofs in hangars
Depending on the features of using the hangar, the roof is made for it:
- single-slope;
- gable;
- polygonal (gable broken);
- flat;
- arched.
The choice of the roof structure is also influenced by such factors as the material consumption of the product (and, accordingly, the price), the climatic conditions of the region and the location of the structure (permanent or mobile).
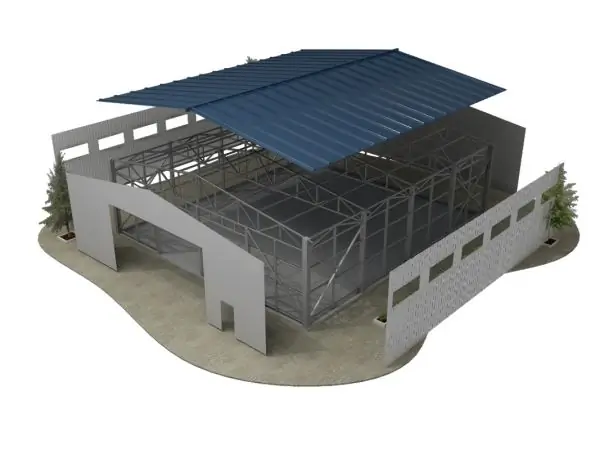
Gable roofs are often installed over large hangars
Hangars with a pitched roof
Hangars with a pitched roof are the least material-intensive budget option. In addition, they are being built much faster than analogues. Straight-walled structures can be supplied with standard metal-plastic windows and doors, therefore they are universal in use. In such a building, both a tire repair shop and a warehouse, a production line, a trade pavilion can be located. The pitched roof is quite resistant to strong wind gusts, therefore it is suitable for regions with strong wind loads.
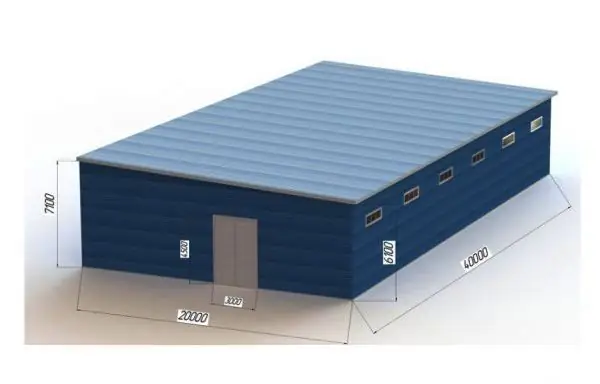
With a span of 20 m, at least one longitudinal row of supports must be installed under the roof structure
This roof structure requires the construction of additional supports along the central axis of the building, and with a large width - even in several rows. Therefore, hangars with pitched roofs are not suitable for storing large equipment.
Hangars with a gable roof
Structures with a standard gable roof are considered the most reliable. They are able to effectively withstand strong winds and are not afraid of a large layer of snow on the roof. The angle of the slope on both sides of the roof is most often the same (the roof is symmetrical) and ranges from 15 to 27 o. To improve aerodynamics and accelerate the snow melting process, in some hangars, the corner is rounded on the ridge and when passing from the roof to the walls.
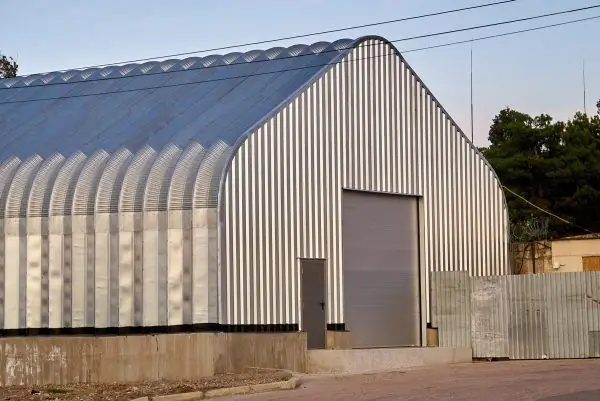
Hangar with rounded corners better withstands wind and snow loads
A gable roof is built on:
-
straight-walled hangars, which are suitable for opening a car wash, trade pavilion, cafe, warehouse, farm, office building;
Hangar with straight walls Straight hangar walls make it possible to use the internal space more efficiently
-
tent hangars with sloping walls used in agriculture for storing products and agricultural machinery.
Hangar with inclined walls In the tent hangar, the sloping walls look like an extension of the roof
The gable roof design is in demand when you need to make a wide (up to 10 m) building without internal support racks. Arched, flat and pitched roofs, even with a reinforced structure, require the construction of supports on wide spans.
Due to the simplicity of the construction, hangars with a gable roof are quickly manufactured and assembled, so they can be made mobile.
Hangars with polygonal roof
Hangars with a broken or polygonal roof are used when the structure has very wide spans (about 30 m). Most often, this is the look of exhibition complexes for large-sized products, workshops with production lines, storage of aviation equipment, sports facilities. For example, it is more expedient to locate an aircraft with a wingspan of 30 m and a height of 3 m in a wide and low building than in a hangar with more familiar proportions.
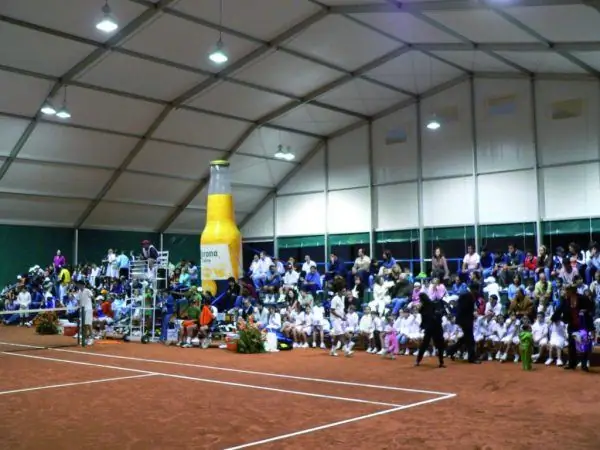
In this hangar with a sloping roof, a tennis court with stands for spectators is very well located
Hangars with polygonal roofs are squat, the width of the building is usually 3-4 times its height. With such a width, a roof of another design would be too high, which would significantly impair its resistance to wind loads. Specialists in the manufacture of hangar frames also emphasize that buildings with a polygonal roof have less material consumption than their counterparts with a gable or arched roof.
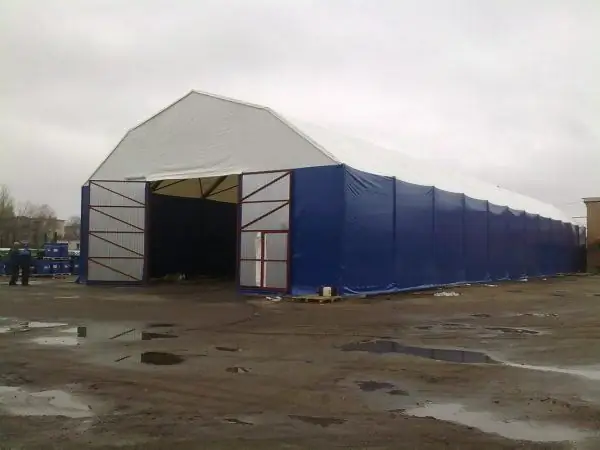
A hangar with a polygonal roof, although it looks squat, allows you to place fairly tall equipment
Hangars with arched roof
Hangars with arched roofs usually have low straight walls, over which a semicircular roof vault is erected. Buildings of this type are most often used on the territory of livestock farms (for keeping cattle) and agricultural complexes (for storing products from the fields).
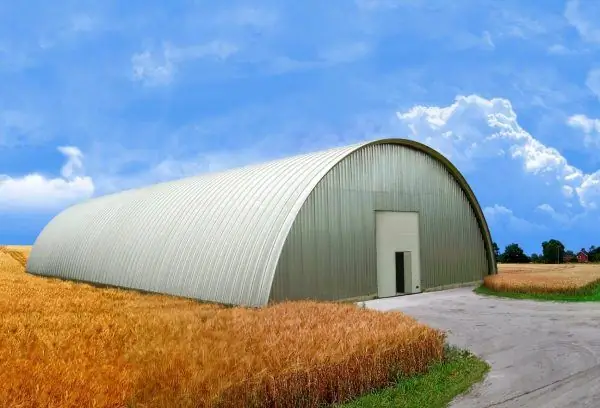
It is convenient to store bulk agricultural products in an arched hangar
In recent years, arched hangars, which look like halves of huge pipes, have been gaining popularity. In such structures, the roof passes into the walls without joints, so they do not need a separate roof structure. But since it is impossible to place racks or equipment right next to the wall in them, hangars with straight walls will remain in demand for a long time.
Warming of hangars
The hangar roof can be insulated or cold. Since most of these buildings do not have a separate roof (there is only a common frame), the roof structure is most often insulated together with the walls.
Cold hangars are either temporary structures (installed for the season or assembled for a specific event), or buildings designed for storing goods or placing equipment with low temperature requirements. Hangars with awning (fabric) sheathing or structures with profiled sheet metal cladding are most often left without insulation.
When insulating hangars, the following methods are used:
- spraying with polyurethane foam on the finished structure;
- cladding with stone / slag wool from the inside / outside;
- use in the construction of sandwich panels made of cotton wool and metal sheets.
Insulation of the roof of the hangar PPU
Spraying polyurethane foam is one of the most demanded methods of thermal insulation of hangars, which are operated in the cold season. Its main advantage is the ability to work on surfaces of any shape; it equally effectively insulates both arched and pitched roofs. In addition, the material is not afraid of rodents and fungi, which makes it the best option for agricultural warehouses.
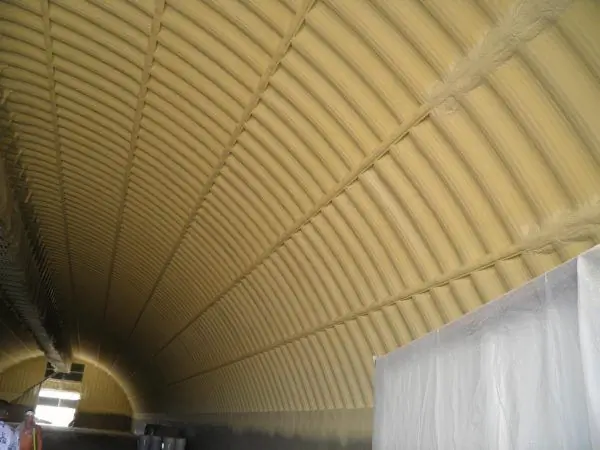
A layer of polyurethane foam tightly overlaps the frame elements, preventing the appearance of cold bridges
Table: comparison of thermal conductivity indicators of different types of insulation
Material | Thermal conductivity coefficient, W / (m ∙ o K) |
Required layer thickness (versus polyurethane foam) |
Service life, years |
Minvata | 0.06 | 3X | five |
Styrofoam | 0.04 | 2X | ten |
Extruded polystyrene foam | 0.03 | 1,5X | 20 |
Polyurethane foam | 0.02 | 1X | thirty |
The data shown in the table indicate that polyurethane foam is three times more effective than mineral or stone wool. In addition, the spraying technology allows you to create a uniform layer without joints, cracks, cold bridges and the need for an additional vapor, moisture and windproof membrane. As a result, the insulation is carried out quickly and as efficiently as possible, which has a positive effect on the payback period of the hangar. Since the spraying method can be used on metal structures of any age (the material adheres well to the base and does not overload the structure), PPU is actively used to improve and repurpose old hangars.
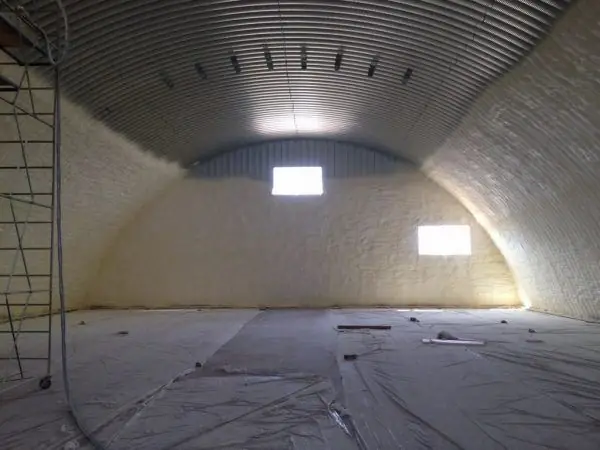
When insulating PPU, it is simply not required to specially arrange the transition between the insulation and the window / door frame
The only disadvantage of PPU is the need for interior decoration of the room, since the material is soft and does not withstand either mechanical stress or ultraviolet radiation. But only sandwich panels surpass it in this indicator. Mineral wool and polystyrene also need protection.
Insulation of the hangar roof with cotton wool
Slag and stone wool are produced in rolls, so it is easy to work with them even at high heights, especially when the arched structures are insulated outside. These materials do not emit harmful binders when heated, so they can be safely used for thermal insulation of grain warehouses with metal sheathing (even if the region has a harsh continental climate with cold winters and hot summers).
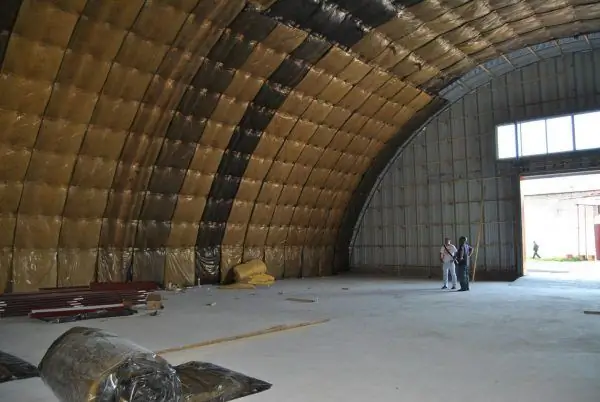
When insulating an arched hangar with rolled mineral wool, the insulation does not even have to be cut
Since the thermal conductivity of stone wool is 0.077-0.12 W / (m ∙ o K), and for slag wool it can reach 0.48 W / (m ∙ o K), these materials need insulation with a foil material (reflective film, foil with foamed layer). Such a tandem will enhance the heat-insulating properties of cotton wool and protect it from water vapor. When insulating the frame from the outside, the foil can be placed “facing inward” and thus save on decorative filing of the hangar roof. On the walls, you usually have to make a crate and cover the soft material of OSB, plywood, chipboard. A properly equipped cake made of cotton wool and hydro / vapor barriers can save up to 95% of heat.
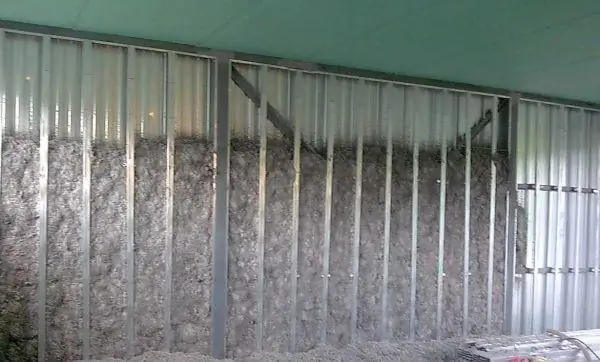
When applied wet, ecowool adheres well to profiled sheets and without the inner lining of the hangar
Ecowool (cellulose wool) is often used in food hangars - a safer analogue of stone wool. Its thermal conductivity is 0.037-0.042 W / (m ∙ o K), which is comparable to extruded polystyrene foam. Due to the borax content in cotton wool, it is fireproof and can be used in hangars with an increased risk of fire. But ecowool, like mineral wool, should be protected from moisture by equipping membranes on the walls and ceiling.
Depending on the form of production, ecowool can be rolled out in rolls, sprayed with separate fibers (like polyurethane foam) and covered with flakes. In the third case, a cavity is left between the outer and inner cladding of the hangar, which is stuffed with insulation flakes. Since for this, the inner sheathing is assembled in stages and its installation takes a lot of time, this technique is rarely used to insulate hangars. Spraying in such buildings is more appropriate.
Hangar roof made of sandwich panels
Sandwich panels are multi-layer blocks that allow you to assemble insulated hangars as a constructor. They usually consist of:
- outer layer - decorative cladding made of profiled metal sheet;
- insulation (expanded polystyrene, mineral wool, ecowool);
-
interior decoration of the hangar from OSB sheets, moisture-resistant plywood, smooth metal sheets.
Roof sandwich panel Sandwich panels are used not only for the construction of the supporting frame, but also for the roof of the hangar
Since all layers are glued with a polyurethane compound, the insulation used in the panels does not need additional moisture insulation. The dimensions of the sandwiches can be matched to the building frame (or vice versa - select panels and calculate the metal frame for them), which makes building assembly as simple and quick as possible. Moreover, construction can be carried out at any temperature, even in winter. Walls, roofs and ceilings made of this material are perfectly flat due to the ideal geometry of each product and the careful adjustment of the fragments to each other.
On the other hand, SIP (structural insulating panels) require particularly careful sealing of the joints, because frost will pass through any gap right into the hangar. In addition, they can only be used for hangars with a strict geometric shape.
Hangar roof device
The roof of a standard metal hangar consists of trusses and girders connecting them. These structures form the roof on which the roofing and insulation material lies. When it is necessary to reduce the distance between the girders, to save or provide a gap between the frame and the roof, wooden girders are used, which are attached to the trusses with connector brackets.
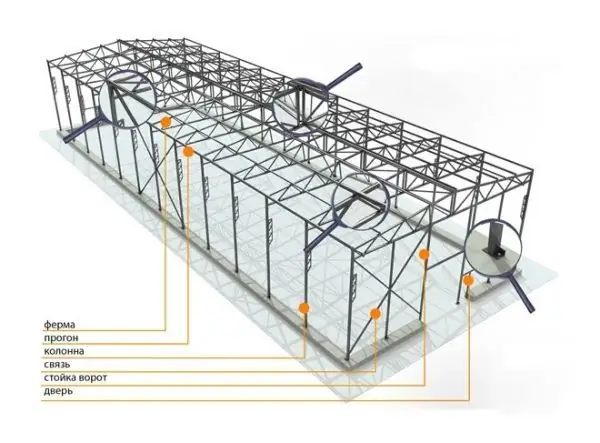
The hangar frame consists of several transverse trusses connected by longitudinal girders
If the hangar remains cold, the corrugated sheets are mounted on the frame face up. For an insulated roof, you will need to create a roofing cake from:
- face down corrugated board (interior decoration and at the same time the basis for insulation);
- heat insulating material (in rolls, plates or sprayed on);
- corrugated board face up (decorative roof trim).
If mineral wool is used as insulation, it must be protected on both sides with waterproof / vapor barrier membranes. During installation, it is important to prevent the formation of cracks and cold bridges.
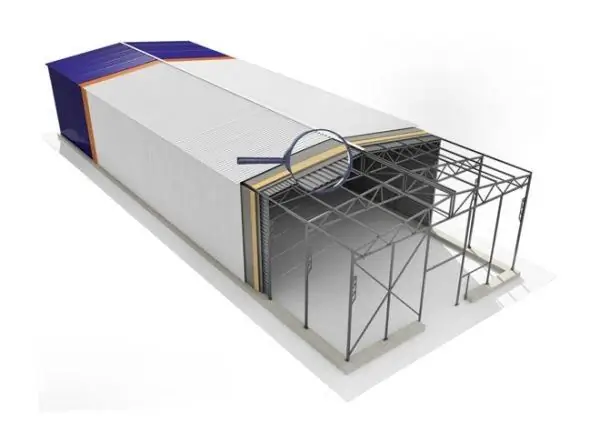
For cladding the walls and roof of the insulated hangar, an insulation structure is used, protected by a profiled sheet on both sides
How to make a roof for a hangar with your own hands
Building a hangar is much easier than building a house or even a bathhouse. Therefore, if you have similar experience, hangar roof cladding will not be a problem. But there are some nuances when choosing materials and implementing an idea.
What material to choose for the roof of the hangar
For cladding the roof of the hangar are used:
-
sandwich panels. We have already talked about the advantages and disadvantages of these products in the section on insulation. They are chosen mainly when it is necessary to equip a warm roof in a short time, as well as to facilitate the work during construction with your own hands. But if there is even the slightest doubt about the correct geometry of the foundation and frame, it is worth abandoning the sandwich panels. There are cases when the roof let water through due to the loose junction of the panels, because the height of the support pillars of the foundation differed by 1-2 mm;
Long sandwich panels By using such long sandwich panels, the number of joints can be minimized
-
awnings made of PVC fabric. They are used only for non-insulated temporary hangars. The main advantage of the sheathing in the form of a cover is quick installation, which allows the hangar to be maximally mobile. If you need a hangar that will be erected for 1-2 weeks during harvest or for 1-2 days for sports matches, you should choose an awning. Due to its low weight, it can be placed on a lightweight frame, which will significantly save money when buying. In addition, with occasional use, PVC fabric will serve for many years;
PVC hangar PVC awning can be used for sheathing and walls and roof of a temporary hangar
-
profiled metal sheets (corrugated board). When you need a permanent insulated hangar, choose corrugated board. The service life of this material is 50 years or more, in addition, it provides additional structural rigidity (due to the undulating bends of the sheet). Since the weight of the sheets is small, when building a small hangar with your own hands, the crate for corrugated board can be made wooden and thus save on expensive metal pipes. Profiled sheets can be combined with all types of heat insulators, so you won't have any problems with roof insulation.
Hangar from galvanized corrugated board Any curved structure can be sheathed with flexible corrugated board
More expensive and heavy materials for arranging the roof of a hangar are not used, since this inevitably leads to an increase in the cost of the frame and the entire structure as a whole. Practice has confirmed that corrugated board and awning fabric are the best and economically viable options for hangar cladding.
Hangar roof construction step by step
Let's consider the process using the example of a hangar with a gable roof. Keep in mind that they begin to work with the roof after installing all the supporting columns, their vertical ties and struts (purlins). A roof is mounted from ready-made trusses, which are welded and painted in advance (in production or at home with your own hands). It is very important that the trusses are exactly the same, otherwise small differences will cause difficulties in the installation and joining of the sheathing sheets.
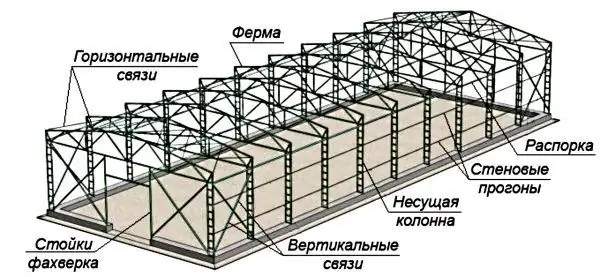
Installation of the roof can be started only after all the necessary frame elements have been assembled
-
Raise the truss over the base of the hangar and orient it so that when lowering the lower part of the truss lies exactly on the support heel of the supporting column.
Installing farms Such wide trusses are installed on four support columns at once.
-
Check the correct position of the laid truss with a building level. If necessary, ask the crane operator to lift the structure and correct its position.
Magnetic building level To work with metal structures, it is worth purchasing a magnetic level
-
Grab the truss to the heels with a welding machine or fasten with bolts (preferably on both sides at the same time). Make sure the metal is not skewed and the truss maintains the correct horizontal and vertical orientation. Make an even seam.
Steel structure seam In order for the connection to be strong and reliable, it is necessary to make an even weld
-
Place the rest of the trusses on each of the structural columns.
Assembling hangar trusses For light construction, trusses can be used without reinforcement
-
Connect the trusses to each other with girders made of pipes of the same profile that were used for the frame. Make sure that the run in the ridge area is exactly along the long center axis of the hangar.
Hangar roof welding After installing all the trusses, they must be tied with horizontal runs
-
After welding, remove any slag that has formed on the seams and apply a rustproof paint.
Rust paint To cover the frame, you must use paint designed for outdoor use.
In the same way, polygonal, arched and pitched roofs are mounted on metal hangars.
Video: construction of a metal frame for a small hangar
Sheathing with corrugated board of the arched roof of the hangar
Required tools and materials:
- cordless screwdriver with spare battery;
- self-tapping screws with rubber / polyurethane sealing washers;
- building level for checking contours, verticals and angles;
- electric or ordinary scissors for metal for cutting corrugated board / sandwich panels (do not use a grinder, the material is afraid of overheating).
To complete the task:
-
Fasten a sheet of metal to the metal frame with the front side inward.
Sheathing the frame with a profile Fastening of the corrugated board is made with special roofing screws with sealed rubber washers
-
Put a wind and vapor barrier on top of the metal, carefully glue the seams with tape.
Roof vapor barrier The diaphragm connections are, if possible, secured with staples
-
Place sheets of mineral wool in the prepared cells in two layers with an offset of half the length of the block.
Laying mineral wool The displacement of the mineral wool blocks allows for high-quality insulation of the seams
-
Cover the insulation with a waterproofing membrane and seal the seams. Attach wooden beams over the metal sheathing to provide a ventilation gap.
Superdiffusion membrane For waterproofing the roof, you can use a superdiffusion membrane that will allow steam to pass from the side of the insulation
-
Sew up the roof with corrugated board face up.
Arched hangars from corrugated board For the external cladding of the hangar, you can use corrugated board of any color
Video: sheathing of the arched roof of the hangar with profiled sheet
Installation of a pitched roof of a hangar made of sandwich panels
Preparation for installation:
- Read the technical documentation and recommendations of the panel manufacturer and strictly adhere to the described rules. Please note that for the installation of standard panels, the lathing step should be 0.8 m, and the distance from the edge should be 0.6 m;
- Check the slope of the roof, it should be 5-7 degrees depending on the presence of skylights and dormers. If necessary, correct the slope by placing wooden wedges of the required length on top of the trusses;
- Check the horizontal and vertical elements of the frame, the absence of corrosion on the metal, the operability of the tools used.
Let's get to work:
-
Lift the panel to the roof with a crane so as not to damage the locks. If using long panels, make several support belts from slings. Remove the protective film from the panel, make sure there are no fragments of the film on the panel.
Preparing the sandwich panel for installation Before installation, it is necessary to remove the protective film from all surfaces of the sandwich panel
-
Install the panel in place and fix it to the crate with special screws. Correct the tightening torque so that the sealing washer fits snugly against the casing, but does not deform. The minimum distance from the screw to the edge of the panel is 5 cm.
Self-tapping screws for sandwich panels It is advisable to choose a self-tapping screw head to match the facing profiled sheet
-
Dock the following panels with those already installed precisely along the lock, avoiding cracks and distortions. Fix the outer panels to the purlins through the ribs protruding on the panels.
Sequential installation of panels Sandwich panels are connected to each other using special locks, which require care during installation work
-
Install the inner ridge strip.
Ridge bar The special shape of the strip allows you to dock the panels on the ridge without gaps
-
Perform the longitudinal connection of the panels using self-tapping screws screwed in at a distance of 0.4-0.5 m from each other.
Longitudinal panel connection For longitudinal connection of sandwiches, use the longest self-tapping screws
-
Fill the joints between the panels with polyurethane foam from a spray can or a special silicone sealant that does not contain acid (the usual one deteriorates from the sun and turns black from the fungus).
Sandwich Panel Sealant Sandwich panel sealant is a one-component polyurethane based adhesive
-
After the foam has set, remove the protruding fragments and close the joints with polyurethane gaskets with the profile.
Profiled tape for panels The profiled tape must reliably cover all joints of the panels
-
Place the ridge strip on top of the spacers and fix it on the protruding ridges of the panel.
Roof ridge strip The metal ridge is mounted with medium-length self-tapping screws
- Fit the ridge strip - the finishing part of the roof.
If, during assembly, all the gaps are thoroughly foamed and the sandwich panels are not skewed, the roof will last at least 25 years.
Video: how to cut sandwich panels
Hangar roof repair
As already mentioned, the roof is one of the most vulnerable parts of the hangar, so it is precisely this that has to be repaired most often. Let's consider the most common roof problems.
Leaking in the roof
The ingress of water into the roofing cake not only leads to damage to the materials or equipment stored inside, but also destroys the roof itself. Metal parts begin to rust, and when wet, cotton wool loses its heat-insulating properties and rots.
If the leak is seen in only one place, spot repairs can be performed. If the seam of the sandwich panel passes water, it should be expanded and the condition of the insulation and corrugated board should be assessed. In cases where they did not have time to suffer, the joint is repaired using the technology described above and sealed with a polymer tape. If the panel is severely damaged, a fragment is cut out of it or the sandwich is completely replaced. After that, the joints are also sealed. If the roof is damaged from corrugated board with insulation, you can also build a patch according to the described algorithm.
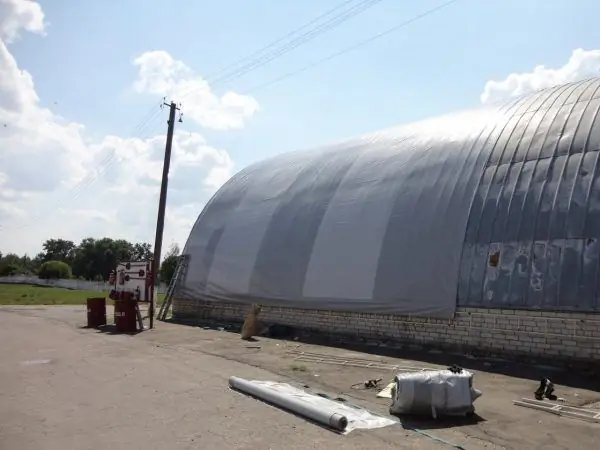
Thanks to the PVC awning, the hangar not only does not leak, but also looks more aesthetically pleasing
If there are a lot of leaks, they can be eliminated by covering the hangar with an awning made of PVC fabric. Thanks to the welded seams, it keeps water out, even in the worst weather. Since the awning does not allow air to pass through, during installation, a sealed joint should be ensured between the fabric and the elements of the ventilation system protruding from the roof. This technology is best suited for non-insulated hangars, as well as structures insulated with a waterproof thermal insulator. If stone or glass wool was used when arranging the hangar, after eliminating the leak, you will need to disassemble the inner lining and replace the insulation (the ecowool can simply be dried).
Truss deformation
The load-bearing elements of the frame begin to bend after heavy snow loads if:
- for cladding, a heavier material was used than originally planned;
- low-quality metal or thin-walled rolled metal was used;
- weld spots were poorly processed, due to which the metal quickly rusted;
- deformation has occurred due to metal fatigue.
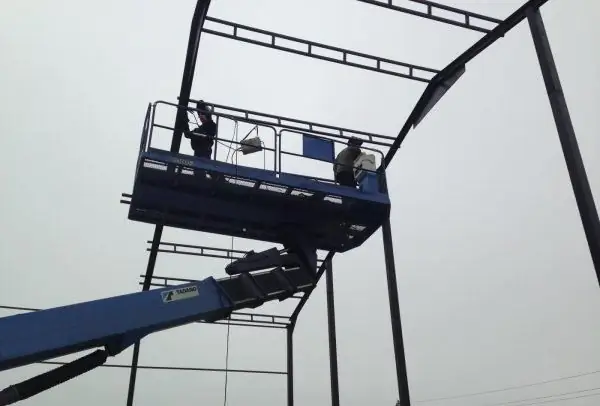
High-quality repair of hangar trusses can only be carried out using lifting equipment
To fix this problem, you will need to strengthen the frame, remove all damaged fragments, carry out welding and painting work. This is a task for a team of specialists who are able to carry out architectural calculations, measure the level of metal fatigue, and perform high-quality repairs. In difficult cases, it may be necessary to dismantle and completely replace some trusses and purlins. You should not do this yourself, because without the proper buildings and equipment, you will not be able to ensure not only the durability of the corrected frame, but also your own safety.
We hope that the information provided will help you adequately assess your capabilities and skills and prevent mistakes when arranging the hangar roof. If you have doubts about your own abilities, order a hangar from professionals, because now you can control the quality of their work.
Recommended:
How To Make A Roof For A Bathhouse, Including With Your Own Hands, As Well As The Features Of Its Design And Installation
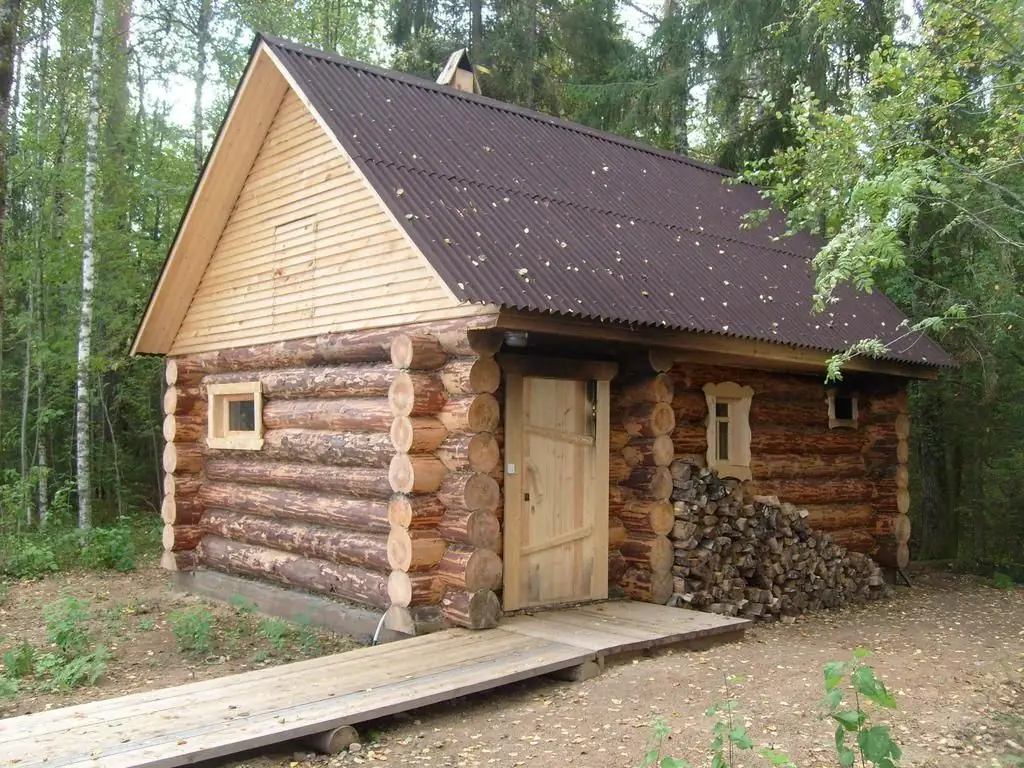
Types of roofs in baths and features of their design. The choice of materials for this design. Roof construction for a bath. Bath roofing repair
Shed Roof For A Garage, How To Do It Right, Including With Your Own Hands, As Well As The Features Of Its Device And Installation
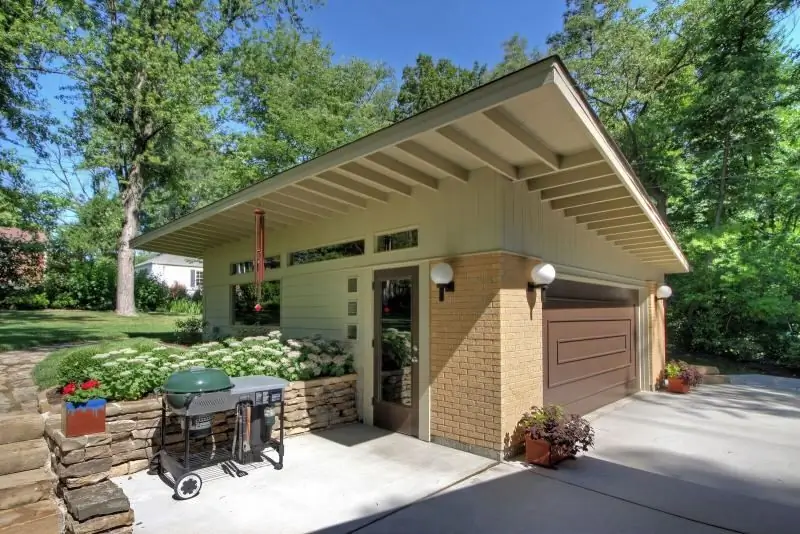
Existing types of pitched roofs. Features of creating and maintaining such a structure in their own hands. What tools and materials you need to have
How To Make A Roof For A Summer Residence, Including With Your Own Hands, As Well As The Features Of Its Design And Installation
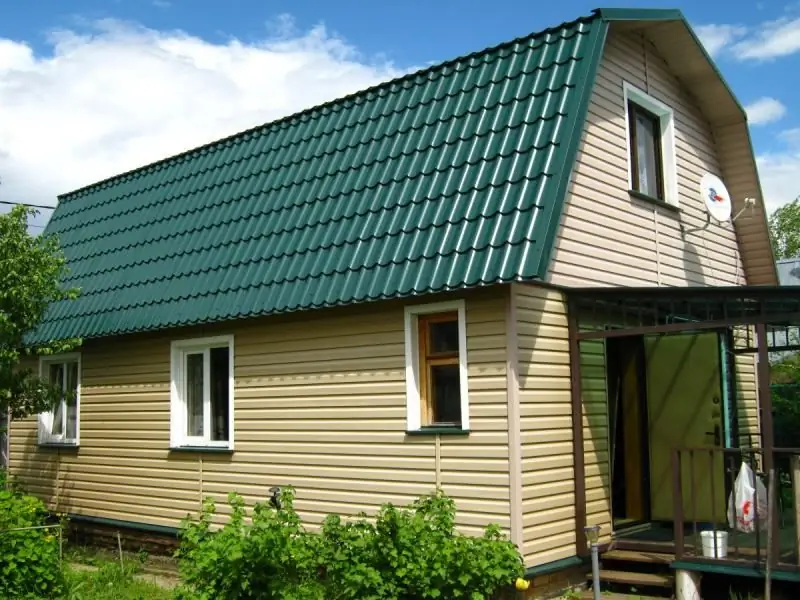
Types of roofs for summer cottages. Calculation and selection of materials. DIY installation and insulation, Dacha roof repair with replacement of materials
Waterproofing The Roof Of The Garage, How To Do It Right, Including With Your Own Hands, As Well As The Features Of Its Device And Installation
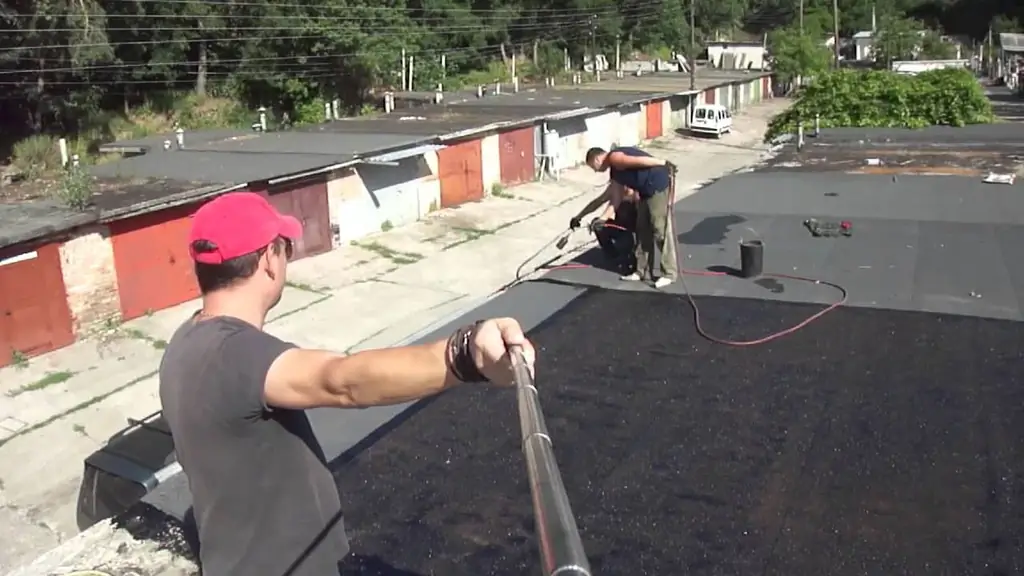
Materials that protect the garage roof from moisture. Waterproofing tools. Laying material on different types of roofs. Replacing the waterproofer
Installation Of Roof Windows, Including With Your Own Hands, As Well As Installation Features In An Already Finished Roof
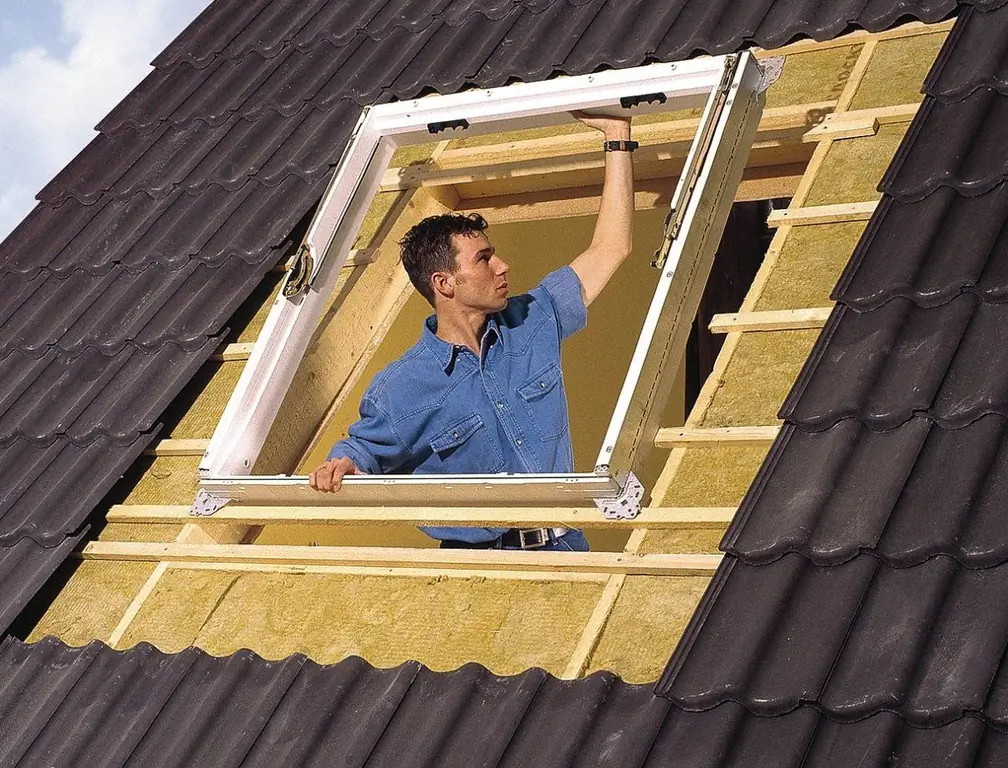
Step by step instructions for installing a roof window. Features of technology and nuances of installation in various types of roofing